Information injection-pump assembly
ZEXEL
106682-9242
1066829242
KOMATSU
6152751262
6152751262
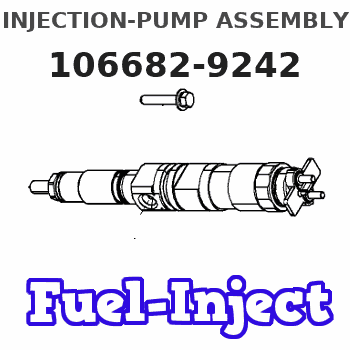
Rating:
Service parts 106682-9242 INJECTION-PUMP ASSEMBLY:
1.
_
5.
AUTOM. ADVANCE MECHANIS
6.
COUPLING PLATE
8.
_
9.
_
10.
NOZZLE AND HOLDER ASSY
11.
Nozzle and Holder
12.
Open Pre:MPa(Kqf/cm2)
26.0{265}
13.
NOZZLE-HOLDER
14.
NOZZLE
15.
NOZZLE SET
Include in #1:
106682-9242
as INJECTION-PUMP ASSEMBLY
Cross reference number
ZEXEL
106682-9242
1066829242
KOMATSU
6152751262
6152751262
Zexel num
Bosch num
Firm num
Name
Calibration Data:
Adjustment conditions
Test oil
1404 Test oil ISO4113 or {SAEJ967d}
1404 Test oil ISO4113 or {SAEJ967d}
Test oil temperature
degC
40
40
45
Nozzle and nozzle holder
105780-8130
Bosch type code
EFEP215A
Nozzle
105780-0050
Bosch type code
DN6TD119NP1T
Nozzle holder
105780-2090
Bosch type code
EFEP215
Opening pressure
MPa
17.2
Opening pressure
kgf/cm2
175
Injection pipe
Outer diameter - inner diameter - length (mm) mm 8-4-1000
Outer diameter - inner diameter - length (mm) mm 8-4-1000
Overflow valve
131425-1620
Overflow valve opening pressure
kPa
255
221
289
Overflow valve opening pressure
kgf/cm2
2.6
2.25
2.95
Tester oil delivery pressure
kPa
157
157
157
Tester oil delivery pressure
kgf/cm2
1.6
1.6
1.6
Direction of rotation (viewed from drive side)
Left L
Left L
Injection timing adjustment
Direction of rotation (viewed from drive side)
Left L
Left L
Injection order
1-5-3-6-
2-4
Pre-stroke
mm
2.8
2.75
2.85
Beginning of injection position
Drive side NO.1
Drive side NO.1
Difference between angles 1
Cal 1-5 deg. 60 59.5 60.5
Cal 1-5 deg. 60 59.5 60.5
Difference between angles 2
Cal 1-3 deg. 120 119.5 120.5
Cal 1-3 deg. 120 119.5 120.5
Difference between angles 3
Cal 1-6 deg. 180 179.5 180.5
Cal 1-6 deg. 180 179.5 180.5
Difference between angles 4
Cyl.1-2 deg. 240 239.5 240.5
Cyl.1-2 deg. 240 239.5 240.5
Difference between angles 5
Cal 1-4 deg. 300 299.5 300.5
Cal 1-4 deg. 300 299.5 300.5
Injection quantity adjustment
Adjusting point
A
Rack position
15.6
Pump speed
r/min
1100
1100
1100
Average injection quantity
mm3/st.
403
400
406
Max. variation between cylinders
%
0
-3
3
Basic
*
Fixing the lever
*
Boost pressure
kPa
49.3
49.3
Boost pressure
mmHg
370
370
Injection quantity adjustment_02
Adjusting point
C
Rack position
7.7+-0.5
Pump speed
r/min
275
275
275
Average injection quantity
mm3/st.
8.5
6.5
10.5
Max. variation between cylinders
%
0
-15
15
Fixing the rack
*
Boost pressure
kPa
0
0
0
Boost pressure
mmHg
0
0
0
Injection quantity adjustment_03
Adjusting point
D
Rack position
-
Pump speed
r/min
100
100
100
Average injection quantity
mm3/st.
340
340
360
Fixing the lever
*
Boost pressure
kPa
0
0
0
Boost pressure
mmHg
0
0
0
Rack limit
*
Boost compensator adjustment
Pump speed
r/min
600
600
600
Rack position
R1-3.1
Boost pressure
kPa
4
2.7
5.3
Boost pressure
mmHg
30
20
40
Boost compensator adjustment_02
Pump speed
r/min
600
600
600
Rack position
R1(15.6)
Boost pressure
kPa
36
29.3
42.7
Boost pressure
mmHg
270
220
320
Test data Ex:
Governor adjustment
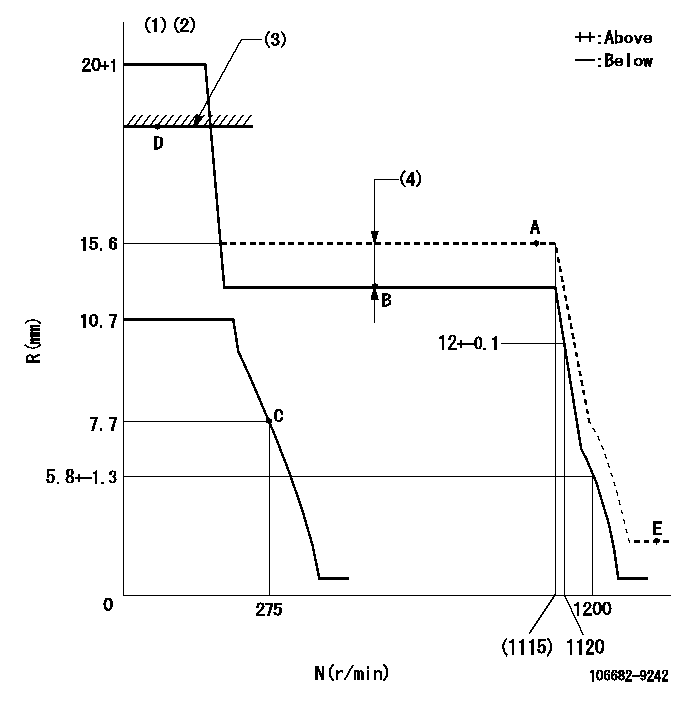
N:Pump speed
R:Rack position (mm)
(1)Target notch: K
(2)Tolerance for racks not indicated: +-0.05mm.
(3)RACK LIMIT
(4)Boost compensator stroke: BCL
----------
K=17 BCL=3.1+-0.1mm
----------
----------
K=17 BCL=3.1+-0.1mm
----------
Speed control lever angle
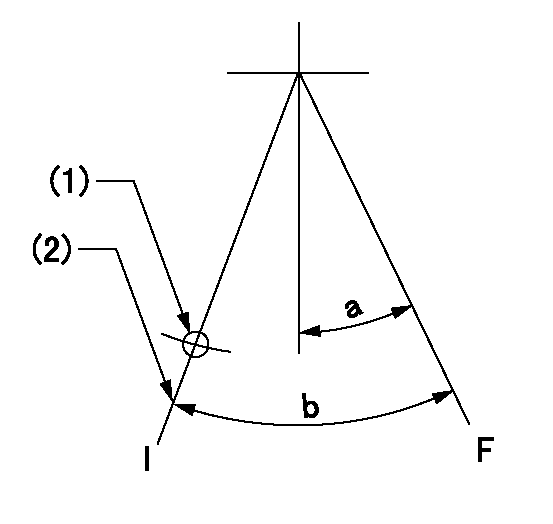
F:Full speed
I:Idle
(1)Use the hole at R = aa
(2)Stopper bolt setting
----------
aa=90mm
----------
a=6deg+-5deg b=36deg+-5deg
----------
aa=90mm
----------
a=6deg+-5deg b=36deg+-5deg
Stop lever angle
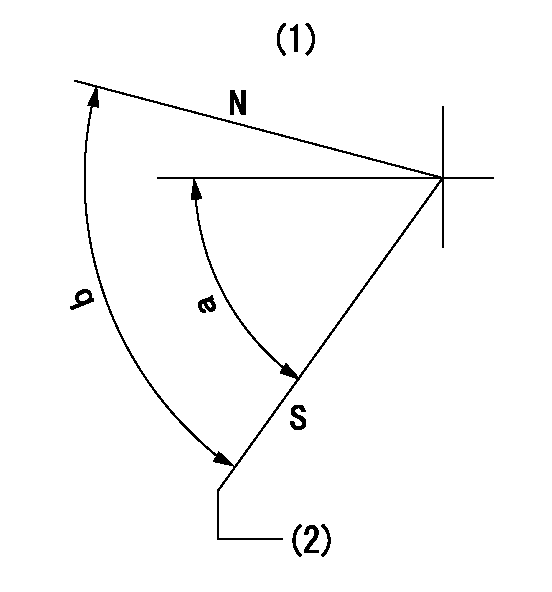
N:Pump normal
S:Stop the pump.
(1)No return spring
(2)Pump speed aa and rack position bb (to be sealed at delivery)
----------
aa=0r/min bb=1-0.5mm
----------
a=63deg+-5deg b=(73deg)
----------
aa=0r/min bb=1-0.5mm
----------
a=63deg+-5deg b=(73deg)
Timing setting

(1)Pump vertical direction
(2)Coupling's key groove position at No 1 cylinder's beginning of injection
(3)-
(4)-
----------
----------
a=(160deg)
----------
----------
a=(160deg)
Information:
Keep all parts clean from contaminants. Contaminants put into the system may cause rapid wear and shortened component life.
1. Loosen hose clamps and slide hose (1) down on the tube assembly. 2. Remove tube assembly (4).3. Disconnect hose assembly (3), loosen two clamps and slide hose (2) on tube assembly. 4. Remove bolts (5). 5. Remove the supply tube (6) and drain tube (7) and the gaskets. 6. Disconnect tube assembly (8) from the aftercooler housing and remove bolts (9).7. Attach a hoist to the cylinder head lift brackets. 8. Remove head bolts (10) and the cylinder head from the engine block. The weight of the cylinder head assembly is 177 kg (390 lb).
Do not set the cylinder head on a flat surface because of possible damage to the fuel injection nozzle tips.
Install Cylinder Head
When the cylinder head is removed, a new spacer plate gasket must be installed. See the topic, Remove And Install Spacer Plate, in this manual. 1. Clean the surfaces of the cylinder head and the cylinder block that make contact with each other. Make sure the surfaces are clean and dry. Install a new dry gasket (2) on the cylinder block.2. Fasten a hoist to the cylinder head (1) and put it on position on the cylinder block.3. Put 6V4876 Molykote Lubricant on all the head bolts and rocker shaft bolts except bolt (25). Install the head bolts and washers that hold the head in place. Do not tighten bolts at this time.4. Loosen the adjusting screws on the rocker arms for valve clearance. This will prevent a bent valve or push rod at installation. 5. Install push rods (4) and rocker shaft assembly (3). Install the bolts and washers that hold the rocker shaft in place. 6. Tighten the bolts as follows:a. Tighten bolts 1 through 26 in number sequence to a torque of 155 N m (115 lb ft).b. Tighten bolts 1 through 26 again in number sequence to a torque of 250 17 N m (185 13 lb ft).c. Tighten bolts 1 through 26 again in number sequence (hand tighten only) to a torque of 250 17 N m (185 13 lb ft).d. Tighten bolts A through G in letter sequence (hand tighten only) to a torque of 43 7 N m (32 5 lb ft). 6. Make an adjustment until the intake valve clearance is 0.38 mm (.015 in) and the exhaust valve clearance is 0.64 mm (.025 in). Tighten the locknuts (5) for the adjusting screws to a torque of 29 7 N m (21 5 lb ft).7. Connect tube assembly (6) and install the bolts to fasten clips (7). 8. Inspect the turbocharger cartridge gaskets and make replacements if necessary. Install gaskets and the turbocharger supply tube assembly (8) and drain tube assembly (9). 9. Make sure the gasket for the water pump bypass elbow is in good condition and install two bolts (11) to fasten elbow (12) to cylinder