Information injection-pump assembly
BOSCH
9 400 617 606
9400617606
ZEXEL
106682-9212
1066829212
KOMATSU
6215711650
6215711650
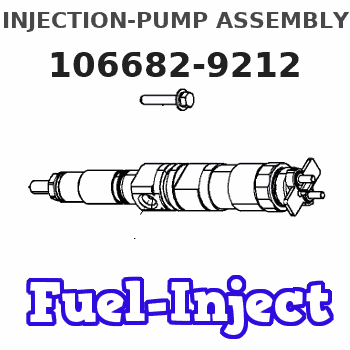
Rating:
Service parts 106682-9212 INJECTION-PUMP ASSEMBLY:
1.
_
5.
AUTOM. ADVANCE MECHANIS
7.
COUPLING PLATE
8.
_
9.
_
11.
Nozzle and Holder
12.
Open Pre:MPa(Kqf/cm2)
24.5(250)
15.
NOZZLE SET
Include in #1:
106682-9212
as INJECTION-PUMP ASSEMBLY
Cross reference number
BOSCH
9 400 617 606
9400617606
ZEXEL
106682-9212
1066829212
KOMATSU
6215711650
6215711650
Zexel num
Bosch num
Firm num
Name
Calibration Data:
Adjustment conditions
Test oil
1404 Test oil ISO4113 or {SAEJ967d}
1404 Test oil ISO4113 or {SAEJ967d}
Test oil temperature
degC
40
40
45
Nozzle and nozzle holder
105780-8130
Bosch type code
EFEP215A
Nozzle
105780-0050
Bosch type code
DN6TD119NP1T
Nozzle holder
105780-2090
Bosch type code
EFEP215
Opening pressure
MPa
17.2
Opening pressure
kgf/cm2
175
Injection pipe
Outer diameter - inner diameter - length (mm) mm 8-4-1000
Outer diameter - inner diameter - length (mm) mm 8-4-1000
Overflow valve
131425-1620
Overflow valve opening pressure
kPa
255
221
289
Overflow valve opening pressure
kgf/cm2
2.6
2.25
2.95
Tester oil delivery pressure
kPa
157
157
157
Tester oil delivery pressure
kgf/cm2
1.6
1.6
1.6
Direction of rotation (viewed from drive side)
Right R
Right R
Injection timing adjustment
Direction of rotation (viewed from drive side)
Right R
Right R
Injection order
1-5-3-6-
2-4
Pre-stroke
mm
3.5
3.45
3.55
Beginning of injection position
Drive side NO.1
Drive side NO.1
Difference between angles 1
Cal 1-5 deg. 60 59.5 60.5
Cal 1-5 deg. 60 59.5 60.5
Difference between angles 2
Cal 1-3 deg. 120 119.5 120.5
Cal 1-3 deg. 120 119.5 120.5
Difference between angles 3
Cal 1-6 deg. 180 179.5 180.5
Cal 1-6 deg. 180 179.5 180.5
Difference between angles 4
Cyl.1-2 deg. 240 239.5 240.5
Cyl.1-2 deg. 240 239.5 240.5
Difference between angles 5
Cal 1-4 deg. 300 299.5 300.5
Cal 1-4 deg. 300 299.5 300.5
Injection quantity adjustment
Adjusting point
A
Rack position
14.1
Pump speed
r/min
900
900
900
Average injection quantity
mm3/st.
331
328
334
Max. variation between cylinders
%
0
-3
3
Basic
*
Fixing the lever
*
Remarks
Standard point A's rack position same as row R
Standard point A's rack position same as row R
Injection quantity adjustment_02
Adjusting point
B
Rack position
7.7+-0.5
Pump speed
r/min
400
400
400
Average injection quantity
mm3/st.
19
17.5
20.5
Max. variation between cylinders
%
0
-15
15
Fixing the rack
*
Test data Ex:
Governor adjustment
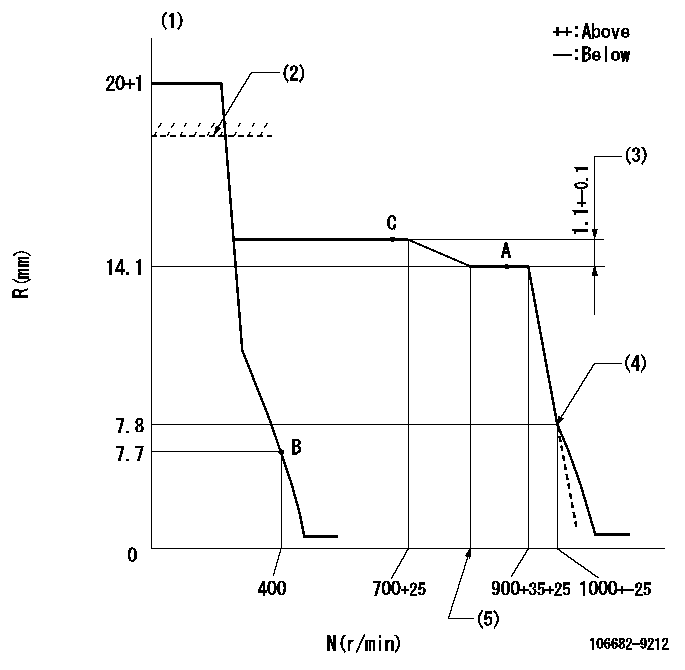
N:Pump speed
R:Rack position (mm)
(1)Target notch: K
(2)Rack limit for 106682-4192
(3)Rack difference between N = N1 and N = N2
(4)Idle sub spring setting: L1.
(5)(Actual measurement)
----------
K=14 N1=900r/min N2=700r/min L1=7.8-0.5mm
----------
----------
K=14 N1=900r/min N2=700r/min L1=7.8-0.5mm
----------
Speed control lever angle
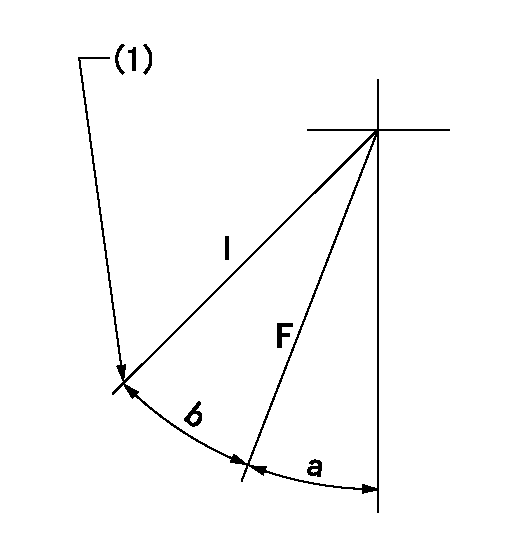
F:Full speed
I:Idle
(1)Stopper bolt setting
----------
----------
a=(21deg)+-5deg b=(21deg)+-5deg
----------
----------
a=(21deg)+-5deg b=(21deg)+-5deg
Stop lever angle
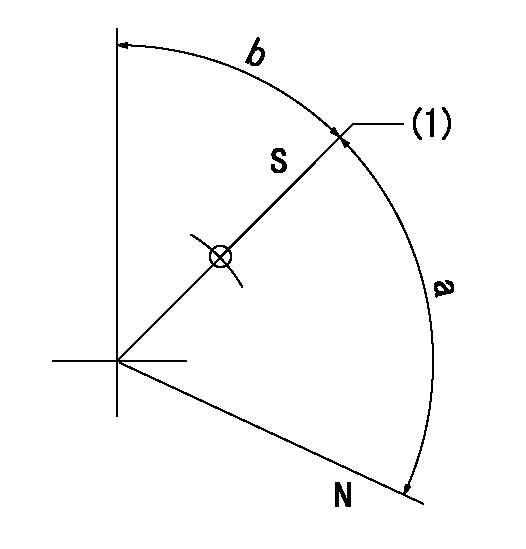
N:Pump normal
S:Stop the pump.
(1)Pump speed aa, rack position bb
----------
aa=0r/min bb=1-0.5mm
----------
a=(73deg) b=43.5deg+-5deg
----------
aa=0r/min bb=1-0.5mm
----------
a=(73deg) b=43.5deg+-5deg
Timing setting

(1)Pump vertical direction
(2)Coupling's key groove position at No 1 cylinder's beginning of injection
(3)-
(4)-
----------
----------
a=(30deg)
----------
----------
a=(30deg)
Information:
Start By:a. remove fuel injection lines
Keep all parts clean from contaminants. Contaminants put into the system may cause rapid wear and shortened component life.
1. Remove bolts (1) and fan guard (2). 2. Loosen bolts (7), (9) and (10). Remove belts (8).3. Remove bolt (4) to clip. Remove grease line (3).4. Remove nuts (6). Remove cover (5) and the gasket. 5. Loosen bolt (12) enough to leave a gap of 3.18 mm (.125 in) between washers (11) and the fuel pump drive gear.6. Install tool (A) as shown. Tighten the stud to pull the fuel pump drive gear loose from the taper on the fuel injection pump camshaft.7. Remove tool (A), bolt (12), and washer (11). 8. Identify and disconnect wires (13).9. Remove tube assemblies (15) and (18).10. Remove two bolts (14), fuel transfer pump (17), and the O-ring seal.11. Remove bolts (16), the filter base, the gasket, and filter (19). 12. Fasten the fuel injection pump housing and governor to a hoist.13. Remove two bolts (22), three nuts (21), and the fuel injection pump housing and governor. The weight of the fuel injection pump housing and governor is 29 kg (64 lb.).14. Remove the two O-ring seals from the bottom of the fuel injection pump housing and governor. 15. Loosen screw (25). Remove two screws (26), control assembly (23) and spacers (24).Install Fuel Injection Pump Housing And Governor
Start By:a. remove fuel injection linesb. remove valve cover Number 1 piston must be set at top dead center (TDC) to perform all timing procedures. The engine is seen from the flywheel end when direction of crankshaft rotation is given. 1. Remove the starter.2. Install tool (B) on flywheel housing as shown.3. To find TDC for No. 1 piston;a. Turn the flywheel clockwise (opposite the direction of engine rotation) approximately 30 degrees. This removes all play from the timing gears. If you go past the bolt hole, you must repeat Step (a).b. Turn the flywheel counterclockwise until a 3/8" - 16 x 2 1/4" NC bolt (27) can be installed in the flywheel through the hole in the flywheel housing. The No. 1 and No. 6 pistons are now at top center position. The No. 1 piston is on the compression stroke when the valves of the No. 1 cylinder are closed. The rocker must be free to move up and down.4. If No. 1 piston is not on the compression stroke, remove the 3/8" - 16 x 2 1/4" NC bolt (27) and turn the flywheel 360° counterclockwise. Install the 3/8" bolt as before. The No. 1 piston is now at TDC.
Typical Example5. Install tooling (C) in the fuel injection pump housing as shown. Push on tooling (C) and turn injection pump camshaft (32). When tooling (C) engages the groove (slot) in the camshaft, the fuel injection pump is in the No. 1 piston TDC position.6. Be sure O-ring seals (28), (29), (30) and (31) are in position on the fuel injection pump housing and governor. Put clean engine oil
Keep all parts clean from contaminants. Contaminants put into the system may cause rapid wear and shortened component life.
1. Remove bolts (1) and fan guard (2). 2. Loosen bolts (7), (9) and (10). Remove belts (8).3. Remove bolt (4) to clip. Remove grease line (3).4. Remove nuts (6). Remove cover (5) and the gasket. 5. Loosen bolt (12) enough to leave a gap of 3.18 mm (.125 in) between washers (11) and the fuel pump drive gear.6. Install tool (A) as shown. Tighten the stud to pull the fuel pump drive gear loose from the taper on the fuel injection pump camshaft.7. Remove tool (A), bolt (12), and washer (11). 8. Identify and disconnect wires (13).9. Remove tube assemblies (15) and (18).10. Remove two bolts (14), fuel transfer pump (17), and the O-ring seal.11. Remove bolts (16), the filter base, the gasket, and filter (19). 12. Fasten the fuel injection pump housing and governor to a hoist.13. Remove two bolts (22), three nuts (21), and the fuel injection pump housing and governor. The weight of the fuel injection pump housing and governor is 29 kg (64 lb.).14. Remove the two O-ring seals from the bottom of the fuel injection pump housing and governor. 15. Loosen screw (25). Remove two screws (26), control assembly (23) and spacers (24).Install Fuel Injection Pump Housing And Governor
Start By:a. remove fuel injection linesb. remove valve cover Number 1 piston must be set at top dead center (TDC) to perform all timing procedures. The engine is seen from the flywheel end when direction of crankshaft rotation is given. 1. Remove the starter.2. Install tool (B) on flywheel housing as shown.3. To find TDC for No. 1 piston;a. Turn the flywheel clockwise (opposite the direction of engine rotation) approximately 30 degrees. This removes all play from the timing gears. If you go past the bolt hole, you must repeat Step (a).b. Turn the flywheel counterclockwise until a 3/8" - 16 x 2 1/4" NC bolt (27) can be installed in the flywheel through the hole in the flywheel housing. The No. 1 and No. 6 pistons are now at top center position. The No. 1 piston is on the compression stroke when the valves of the No. 1 cylinder are closed. The rocker must be free to move up and down.4. If No. 1 piston is not on the compression stroke, remove the 3/8" - 16 x 2 1/4" NC bolt (27) and turn the flywheel 360° counterclockwise. Install the 3/8" bolt as before. The No. 1 piston is now at TDC.
Typical Example5. Install tooling (C) in the fuel injection pump housing as shown. Push on tooling (C) and turn injection pump camshaft (32). When tooling (C) engages the groove (slot) in the camshaft, the fuel injection pump is in the No. 1 piston TDC position.6. Be sure O-ring seals (28), (29), (30) and (31) are in position on the fuel injection pump housing and governor. Put clean engine oil