Information injection-pump assembly
ZEXEL
106682-4890
1066824890
KOMATSU
6162731941
6162731941
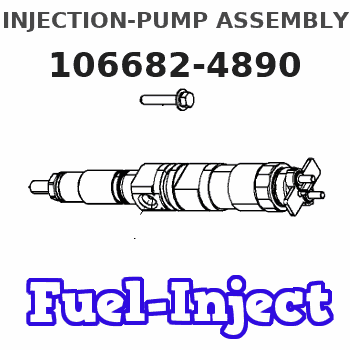
Rating:
Service parts 106682-4890 INJECTION-PUMP ASSEMBLY:
1.
_
5.
AUTOM. ADVANCE MECHANIS
7.
COUPLING PLATE
8.
_
9.
_
11.
Nozzle and Holder
6162-13-7302
12.
Open Pre:MPa(Kqf/cm2)
26.0{265}
15.
NOZZLE SET
Include in #1:
106682-4890
as INJECTION-PUMP ASSEMBLY
Cross reference number
ZEXEL
106682-4890
1066824890
KOMATSU
6162731941
6162731941
Zexel num
Bosch num
Firm num
Name
Calibration Data:
Adjustment conditions
Test oil
1404 Test oil ISO4113 or {SAEJ967d}
1404 Test oil ISO4113 or {SAEJ967d}
Test oil temperature
degC
40
40
45
Nozzle and nozzle holder
105780-8130
Bosch type code
EFEP215A
Nozzle
105780-0050
Bosch type code
DN6TD119NP1T
Nozzle holder
105780-2090
Bosch type code
EFEP215
Opening pressure
MPa
17.2
Opening pressure
kgf/cm2
175
Injection pipe
Outer diameter - inner diameter - length (mm) mm 8-4-1000
Outer diameter - inner diameter - length (mm) mm 8-4-1000
Overflow valve
131424-7120
Overflow valve opening pressure
kPa
255
221
289
Overflow valve opening pressure
kgf/cm2
2.6
2.25
2.95
Tester oil delivery pressure
kPa
157
157
157
Tester oil delivery pressure
kgf/cm2
1.6
1.6
1.6
Direction of rotation (viewed from drive side)
Left L
Left L
Injection timing adjustment
Direction of rotation (viewed from drive side)
Left L
Left L
Injection order
1-5-3-6-
2-4
Pre-stroke
mm
3
2.95
3.05
Beginning of injection position
Drive side NO.1
Drive side NO.1
Difference between angles 1
Cal 1-5 deg. 60 59.5 60.5
Cal 1-5 deg. 60 59.5 60.5
Difference between angles 2
Cal 1-3 deg. 120 119.5 120.5
Cal 1-3 deg. 120 119.5 120.5
Difference between angles 3
Cal 1-6 deg. 180 179.5 180.5
Cal 1-6 deg. 180 179.5 180.5
Difference between angles 4
Cyl.1-2 deg. 240 239.5 240.5
Cyl.1-2 deg. 240 239.5 240.5
Difference between angles 5
Cal 1-4 deg. 300 299.5 300.5
Cal 1-4 deg. 300 299.5 300.5
Injection quantity adjustment
Adjusting point
A
Rack position
14.9
Pump speed
r/min
750
750
750
Average injection quantity
mm3/st.
440
435
445
Max. variation between cylinders
%
0
-3
3
Basic
*
Fixing the rack
*
Injection quantity adjustment_02
Adjusting point
B
Rack position
6.6+-0.5
Pump speed
r/min
400
400
400
Average injection quantity
mm3/st.
34.5
29.5
39.5
Max. variation between cylinders
%
0
-15
15
Fixing the rack
*
Injection quantity adjustment_03
Adjusting point
E
Rack position
18+0.2
Pump speed
r/min
100
100
100
Average injection quantity
mm3/st.
510
510
550
Fixing the lever
*
Rack limit
*
Test data Ex:
Governor adjustment

N:Pump speed
R:Rack position (mm)
(1)Target notch: K
(2)RACK LIMIT: RAL
(3)Idle sub spring setting: L1.
(4)Set at delivery
(5)Dead point position: set at speed N = N1, rack position R = R1
----------
K=9 RAL=18+0.2mm L1=6.2-0.5mm N1=460+-5r/min R1=6.6mm
----------
----------
K=9 RAL=18+0.2mm L1=6.2-0.5mm N1=460+-5r/min R1=6.6mm
----------
Speed control lever angle
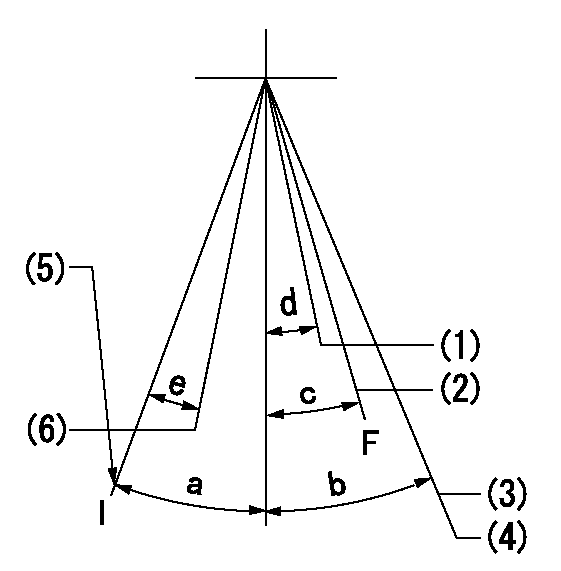
F:Full speed
I:Idle
(1)Set the pump speed at aa
(2)Set the pump speed at bb.
(3)Set the speed at cc (at delivery)
(4)Stopper bolt setting
(5)Stopper bolt setting
(6)Dead point position: Set at speed = dd, rack position = ee
----------
aa=750r/min bb=900r/min cc=965r/min dd=460+-5r/min ee=6.6mm
----------
a=(17deg)+-5deg b=(11deg) c=(10deg)+-5deg d=(4deg)+-5deg e=(4deg)
----------
aa=750r/min bb=900r/min cc=965r/min dd=460+-5r/min ee=6.6mm
----------
a=(17deg)+-5deg b=(11deg) c=(10deg)+-5deg d=(4deg)+-5deg e=(4deg)
Stop lever angle
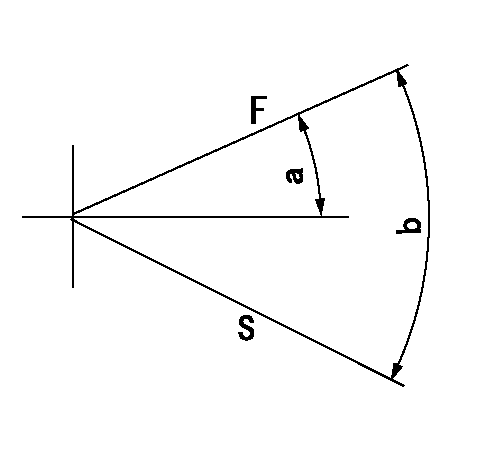
F:Full load
S:Stop the pump.
----------
----------
a=26.5deg+-5deg b=53deg+-5deg
----------
----------
a=26.5deg+-5deg b=53deg+-5deg
0000001501 LEVER
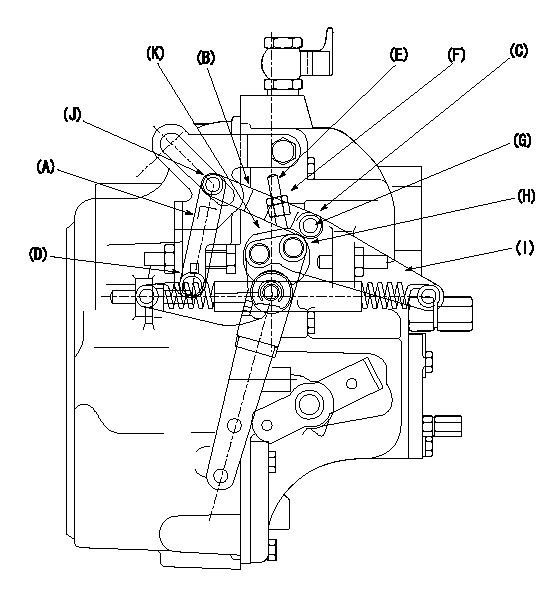
1. (1) Remove the link (A) (B) from (C) and (D).
(2)In this condition, perform normal governor adjustment.
2. (1) Mount the link.
(2)Adjust the umbrella lever.
(3)Adjust the dead point.
Loosen the screw E.
Measure the lever angle when the pump speed is N and the rack position is R.
Temporarily fix the lever with the idle stopper bolt at that angle.
Set the lever (I) with bolts (G) and (H) so that a dead point is obtained.
Check play at the sliding part (J).
Loosen the idle stopper bolt.
Slide the lever.
Re-set the idle stopper bolt at the position of the dead point at that time.
At this time, confirm N, R.
Set so that screw E contacts the lever K.
Fix with the lock nut (F).
3.(1) Set the idle setting.
----------
N=460r/min R=6.6mm
----------
----------
N=460r/min R=6.6mm
----------
Timing setting

(1)Pump vertical direction
(2)Coupling's key groove position at No 1 cylinder's beginning of injection
(3)-
(4)-
----------
----------
a=(30deg)
----------
----------
a=(30deg)
Information:
Exhaust Smoke Can Be Seen While Starting
Possible Causes/Corrections
Cold Outside Temperatures/It can be necessary to use starting aids, or to heat engine oil or coolant at temperatures below -12° C (10° F). Air in Fuel System/With air in the fuel system, the engine will normally be difficult to start, run rough and release a large amount of white smoke. If the engine will not start, loosen a fuel injection line nut and crank the engine until fuel comes out. Tighten the fuel line nut. Start the engine. If the engine still does not run smooth or releases a large amount of white smoke, loosen the fuel line nuts one at a time until the fuel that comes out is free of air. Tighten the fuel line nuts. If the air can not be removed in this way, put 35 kPa (5 psi) of air pressure to the fuel tank.
Do not use more than 55 kPa (8 psi) of air pressure in the fuel tank or damage to the tank may result.
Check for leakage at the connections between the fuel tank and the fuel transfer pump. If leaks are found, tighten the connections or replace the lines. If there are no visual leaks, remove the fuel supply line from the tank and connect it to an outside fuel supply. If this corrects the problem, the suction line (standpipe) inside the fuel tank has a leak. Low Quality Fuel/Remove a small amount of fuel from the tank and check for water in the fuel. If there is water in the fuel, remove fuel from the tank until it is free of water and fill with a good quality fuel. For more information see Special Instruction, Form No. SEHS7067, Fuel Recommendations For Caterpillar Diesel Engines.Change the fuel filter and "prime" (remove the air and/or low quality fuel from the fuel system) the fuel system with the fuel priming pump. If there is no water in the fuel, prime and start the engine by using an outside source of fuel. If engine starts correctly using different fuel, remove all fuel from the tank and fill with good quality fuel. Prime the fuel system if necessary. Low Fuel Pressure/Change the primary and secondary fuel filters and check to make sure the fuel lines are not plugged or damaged. If the filters or lines are not the cause, a repair or replacement of the fuel transfer pump is needed. Fuel Injection Timing Not Correct/Check and make necessary adjustments as in Testing and Adjusting section of this Service Manual. Valve Adjustment Not Correct/Check and make necessary adjustments as in Testing and Adjusting section of this Service Manual. Intake valve clearance is 0.38 mm (.015 in.) and exhaust valve clearance is 0.64 mm (.025 in.). Bad Fuel Nozzle(s)/Remove the fuel nozzles and test as in Testing and Adjusting section of this Service Manual. Low Compression/See Misfiring and Running Rough.Exhaust Smoke Can Not Be Seen While Starting
Possible Causes/Corrections
No Fuel in Tank(s)/Check fuel level visually (do not use the
Possible Causes/Corrections
Cold Outside Temperatures/It can be necessary to use starting aids, or to heat engine oil or coolant at temperatures below -12° C (10° F). Air in Fuel System/With air in the fuel system, the engine will normally be difficult to start, run rough and release a large amount of white smoke. If the engine will not start, loosen a fuel injection line nut and crank the engine until fuel comes out. Tighten the fuel line nut. Start the engine. If the engine still does not run smooth or releases a large amount of white smoke, loosen the fuel line nuts one at a time until the fuel that comes out is free of air. Tighten the fuel line nuts. If the air can not be removed in this way, put 35 kPa (5 psi) of air pressure to the fuel tank.
Do not use more than 55 kPa (8 psi) of air pressure in the fuel tank or damage to the tank may result.
Check for leakage at the connections between the fuel tank and the fuel transfer pump. If leaks are found, tighten the connections or replace the lines. If there are no visual leaks, remove the fuel supply line from the tank and connect it to an outside fuel supply. If this corrects the problem, the suction line (standpipe) inside the fuel tank has a leak. Low Quality Fuel/Remove a small amount of fuel from the tank and check for water in the fuel. If there is water in the fuel, remove fuel from the tank until it is free of water and fill with a good quality fuel. For more information see Special Instruction, Form No. SEHS7067, Fuel Recommendations For Caterpillar Diesel Engines.Change the fuel filter and "prime" (remove the air and/or low quality fuel from the fuel system) the fuel system with the fuel priming pump. If there is no water in the fuel, prime and start the engine by using an outside source of fuel. If engine starts correctly using different fuel, remove all fuel from the tank and fill with good quality fuel. Prime the fuel system if necessary. Low Fuel Pressure/Change the primary and secondary fuel filters and check to make sure the fuel lines are not plugged or damaged. If the filters or lines are not the cause, a repair or replacement of the fuel transfer pump is needed. Fuel Injection Timing Not Correct/Check and make necessary adjustments as in Testing and Adjusting section of this Service Manual. Valve Adjustment Not Correct/Check and make necessary adjustments as in Testing and Adjusting section of this Service Manual. Intake valve clearance is 0.38 mm (.015 in.) and exhaust valve clearance is 0.64 mm (.025 in.). Bad Fuel Nozzle(s)/Remove the fuel nozzles and test as in Testing and Adjusting section of this Service Manual. Low Compression/See Misfiring and Running Rough.Exhaust Smoke Can Not Be Seen While Starting
Possible Causes/Corrections
No Fuel in Tank(s)/Check fuel level visually (do not use the