Information injection-pump assembly
BOSCH
9 400 611 841
9400611841
ZEXEL
106682-4644
1066824644
MITSUBISHI-HEAV
35A6530330
35a6530330
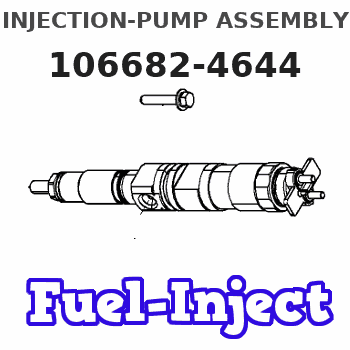
Rating:
Service parts 106682-4644 INJECTION-PUMP ASSEMBLY:
1.
_
5.
AUTOM. ADVANCE MECHANIS
8.
_
9.
_
11.
Nozzle and Holder
35A61-00010
12.
Open Pre:MPa(Kqf/cm2)
21.6{220}
15.
NOZZLE SET
Include in #1:
106682-4644
as INJECTION-PUMP ASSEMBLY
Cross reference number
BOSCH
9 400 611 841
9400611841
ZEXEL
106682-4644
1066824644
MITSUBISHI-HEAV
35A6530330
35a6530330
Zexel num
Bosch num
Firm num
Name
Calibration Data:
Adjustment conditions
Test oil
1404 Test oil ISO4113 or {SAEJ967d}
1404 Test oil ISO4113 or {SAEJ967d}
Test oil temperature
degC
40
40
45
Nozzle and nozzle holder
105780-8130
Bosch type code
EFEP215A
Nozzle
105780-0050
Bosch type code
DN6TD119NP1T
Nozzle holder
105780-2090
Bosch type code
EFEP215
Opening pressure
MPa
17.2
Opening pressure
kgf/cm2
175
Injection pipe
Outer diameter - inner diameter - length (mm) mm 8-4-1000
Outer diameter - inner diameter - length (mm) mm 8-4-1000
Overflow valve
131424-3420
Overflow valve opening pressure
kPa
255
221
289
Overflow valve opening pressure
kgf/cm2
2.6
2.25
2.95
Tester oil delivery pressure
kPa
157
157
157
Tester oil delivery pressure
kgf/cm2
1.6
1.6
1.6
Direction of rotation (viewed from drive side)
Left L
Left L
Injection timing adjustment
Direction of rotation (viewed from drive side)
Left L
Left L
Injection order
1-5-3-6-
2-4
Pre-stroke
mm
2.8
2.75
2.85
Rack position
Point A R=A
Point A R=A
Beginning of injection position
Governor side NO.1
Governor side NO.1
Difference between angles 1
Cal 1-5 deg. 60 59.5 60.5
Cal 1-5 deg. 60 59.5 60.5
Difference between angles 2
Cal 1-3 deg. 120 119.5 120.5
Cal 1-3 deg. 120 119.5 120.5
Difference between angles 3
Cal 1-6 deg. 180 179.5 180.5
Cal 1-6 deg. 180 179.5 180.5
Difference between angles 4
Cyl.1-2 deg. 240 239.5 240.5
Cyl.1-2 deg. 240 239.5 240.5
Difference between angles 5
Cal 1-4 deg. 300 299.5 300.5
Cal 1-4 deg. 300 299.5 300.5
Injection quantity adjustment
Adjusting point
A
Rack position
15.3
Pump speed
r/min
900
900
900
Average injection quantity
mm3/st.
553
544
562
Max. variation between cylinders
%
0
-3
3
Basic
*
Fixing the lever
*
Injection quantity adjustment_02
Adjusting point
B
Rack position
6.6+-0.5
Pump speed
r/min
250
250
250
Average injection quantity
mm3/st.
25
22
28
Max. variation between cylinders
%
0
-10
10
Fixing the rack
*
Test data Ex:
Governor adjustment
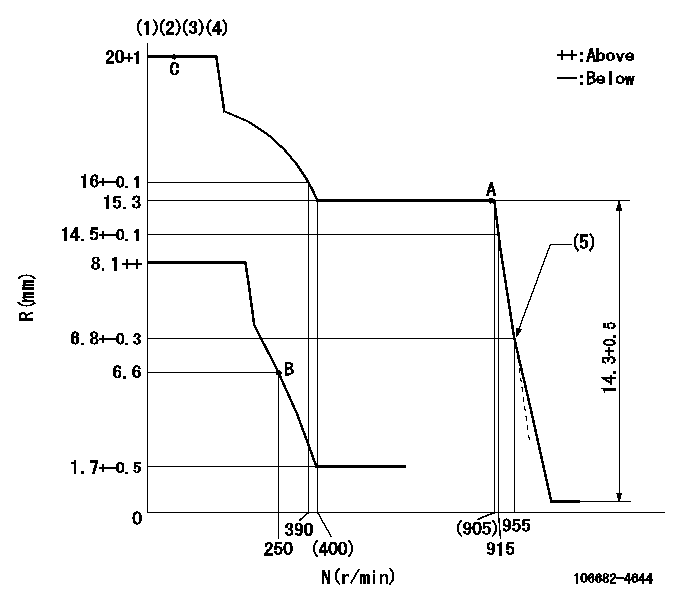
N:Pump speed
R:Rack position (mm)
(1)Minimum - maximum speed specification
(2)Adjust at speed lever's full position.
(3)Target notch: K
(4)Tolerance for racks not indicated: +-0.05mm.
(5)Idle sub spring setting: L1.
----------
K=12 L1=6.8-0.5mm
----------
----------
K=12 L1=6.8-0.5mm
----------
Speed control lever angle

F:Full speed
S:Stop
(1)At the center of the lever key groove
----------
----------
a=17.5deg+-5deg b=33deg+-3deg
----------
----------
a=17.5deg+-5deg b=33deg+-3deg
0000000901
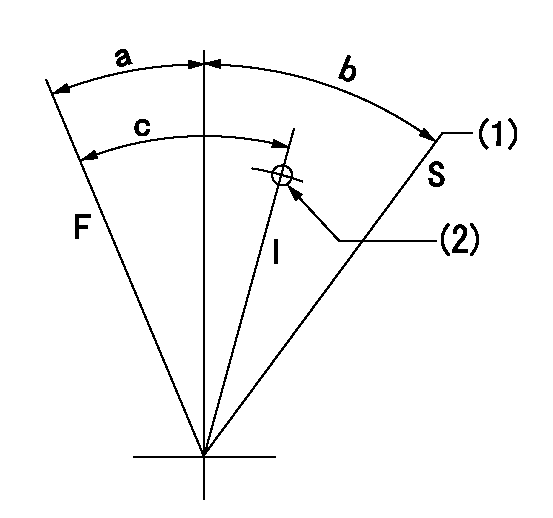
F:Full load
I:Idle
S:Stop
(1)Stop side boss position
(2)Use the screw at R = aa
----------
aa=60mm
----------
a=19deg+-5deg b=30deg+-5deg c=29deg+-5deg
----------
aa=60mm
----------
a=19deg+-5deg b=30deg+-5deg c=29deg+-5deg
Timing setting

(1)Pump vertical direction
(2)Coupling's key groove position at No 1 cylinder's beginning of injection
(3)-
(4)-
----------
----------
a=(110deg)
----------
----------
a=(110deg)
Information:
Loose Belt(s)
Loose fan or water pump belts will cause a reduction in air or water flow. Tighten the belts according to V-Belt Tension Chart that is shown in Specification section of this Service Manual.Bad Hose(s)
Bad hoses with leaks can normally be seen. Hoses that have no visual leaks can "collapse" (pull together) during operation and cause a restriction in the flow of coolant. Hoses become soft and/or get cracks after a period of time. Hoses must be changed after 50,000 miles or a year of use. The inside can become loose, and the loose particles of the hose can cause a restriction in the flow of coolant.Shunt Line Restriction
A restriction of the shunt line from the radiator top tank to the engine front cover, or a shunt line not installed correctly, will cause a reduction in water pump efficiency. The result will be low coolant flow and overheating.Shutters Not Opening Correctly
Check the opening temperature of the shutters. The shutters must be completely closed at a temperature below the fully open temperature of the water temperature regulators. Also, verify that fan control switches or viscous fans are operating correctly.Bad Water Temperature Regulators
A regulator that does not open, or only opens part of the way, can cause above normal heating. To test the thermostats, see the Testing and Adjusting section of this Service Manual.Bad Water Pump
A water pump with a loose impeller does not pump enough coolant for correct engine cooling. A loose impeller can be found by removing the water pump, and by pushing the shaft back and pulling it forward. If the impeller has no damage, check the impeller clearance. The clearance between the impeller and the housing is 0.56 to 1.50 mm (.022 to .059 in).Air in Cooling System
Air can get into the cooling system in different ways. The most common causes are not filling the cooling system correctly, and combustion gas leaking into the system. Combustion gas can get into the system through inside cracks or bad cylinder head gaskets. Air in the cooling system causes a reduction in coolant flow and bubbles in the coolant. Air bubbles hold coolant away from engine parts, preventing heat flow.Air in the cooling system can be found by the Bottle Test. The equipment needed to make this test is a one pint bottle, a bucket of water, and a hose which will fit the end of the overflow pipe of the radiator.Before testing, make sure the cooling system is filled correctly. Use a wire to hold the relief valve in the radiator cap open. Install the radiator cap and tighten it. Put the hose over the end of the overflow pipe.Start the engine and operate it at high idle rpm for a minimum of five minutes after the engine is at normal operating temperature. Use a cover on the radiator core to keep the engine at operating temperature. After five or more minutes at operating temperature, place the loose end of the hose in the bottle filled with water.
Loose fan or water pump belts will cause a reduction in air or water flow. Tighten the belts according to V-Belt Tension Chart that is shown in Specification section of this Service Manual.Bad Hose(s)
Bad hoses with leaks can normally be seen. Hoses that have no visual leaks can "collapse" (pull together) during operation and cause a restriction in the flow of coolant. Hoses become soft and/or get cracks after a period of time. Hoses must be changed after 50,000 miles or a year of use. The inside can become loose, and the loose particles of the hose can cause a restriction in the flow of coolant.Shunt Line Restriction
A restriction of the shunt line from the radiator top tank to the engine front cover, or a shunt line not installed correctly, will cause a reduction in water pump efficiency. The result will be low coolant flow and overheating.Shutters Not Opening Correctly
Check the opening temperature of the shutters. The shutters must be completely closed at a temperature below the fully open temperature of the water temperature regulators. Also, verify that fan control switches or viscous fans are operating correctly.Bad Water Temperature Regulators
A regulator that does not open, or only opens part of the way, can cause above normal heating. To test the thermostats, see the Testing and Adjusting section of this Service Manual.Bad Water Pump
A water pump with a loose impeller does not pump enough coolant for correct engine cooling. A loose impeller can be found by removing the water pump, and by pushing the shaft back and pulling it forward. If the impeller has no damage, check the impeller clearance. The clearance between the impeller and the housing is 0.56 to 1.50 mm (.022 to .059 in).Air in Cooling System
Air can get into the cooling system in different ways. The most common causes are not filling the cooling system correctly, and combustion gas leaking into the system. Combustion gas can get into the system through inside cracks or bad cylinder head gaskets. Air in the cooling system causes a reduction in coolant flow and bubbles in the coolant. Air bubbles hold coolant away from engine parts, preventing heat flow.Air in the cooling system can be found by the Bottle Test. The equipment needed to make this test is a one pint bottle, a bucket of water, and a hose which will fit the end of the overflow pipe of the radiator.Before testing, make sure the cooling system is filled correctly. Use a wire to hold the relief valve in the radiator cap open. Install the radiator cap and tighten it. Put the hose over the end of the overflow pipe.Start the engine and operate it at high idle rpm for a minimum of five minutes after the engine is at normal operating temperature. Use a cover on the radiator core to keep the engine at operating temperature. After five or more minutes at operating temperature, place the loose end of the hose in the bottle filled with water.