Information injection-pump assembly
ZEXEL
106682-4350
1066824350
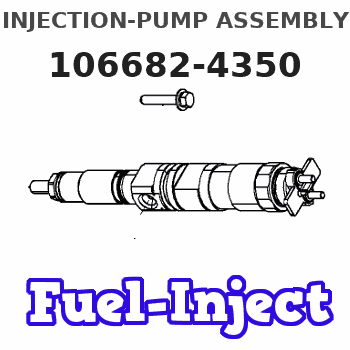
Rating:
Service parts 106682-4350 INJECTION-PUMP ASSEMBLY:
1.
_
3.
GOVERNOR
5.
AUTOM. ADVANCE MECHANIS
7.
COUPLING PLATE
8.
_
9.
_
11.
Nozzle and Holder
6162-13-3702
12.
Open Pre:MPa(Kqf/cm2)
26.0{265}
15.
NOZZLE SET
Include in #1:
106682-4350
as INJECTION-PUMP ASSEMBLY
Cross reference number
ZEXEL
106682-4350
1066824350
Zexel num
Bosch num
Firm num
Name
Calibration Data:
Adjustment conditions
Test oil
1404 Test oil ISO4113 or {SAEJ967d}
1404 Test oil ISO4113 or {SAEJ967d}
Test oil temperature
degC
40
40
45
Nozzle and nozzle holder
105780-8130
Bosch type code
EFEP215A
Nozzle
105780-0050
Bosch type code
DN6TD119NP1T
Nozzle holder
105780-2090
Bosch type code
EFEP215
Opening pressure
MPa
17.2
Opening pressure
kgf/cm2
175
Injection pipe
Outer diameter - inner diameter - length (mm) mm 8-3-600
Outer diameter - inner diameter - length (mm) mm 8-3-600
Overflow valve
131424-6520
Overflow valve opening pressure
kPa
255
221
289
Overflow valve opening pressure
kgf/cm2
2.6
2.25
2.95
Tester oil delivery pressure
kPa
157
157
157
Tester oil delivery pressure
kgf/cm2
1.6
1.6
1.6
Direction of rotation (viewed from drive side)
Left L
Left L
Injection timing adjustment
Direction of rotation (viewed from drive side)
Left L
Left L
Injection order
1-5-3-6-
2-4
Pre-stroke
mm
3.2
3.15
3.25
Beginning of injection position
Drive side NO.1
Drive side NO.1
Difference between angles 1
Cal 1-5 deg. 60 59.5 60.5
Cal 1-5 deg. 60 59.5 60.5
Difference between angles 2
Cal 1-3 deg. 120 119.5 120.5
Cal 1-3 deg. 120 119.5 120.5
Difference between angles 3
Cal 1-6 deg. 180 179.5 180.5
Cal 1-6 deg. 180 179.5 180.5
Difference between angles 4
Cyl.1-2 deg. 240 239.5 240.5
Cyl.1-2 deg. 240 239.5 240.5
Difference between angles 5
Cal 1-4 deg. 300 299.5 300.5
Cal 1-4 deg. 300 299.5 300.5
Injection quantity adjustment
Adjusting point
A
Rack position
14.7
Pump speed
r/min
900
900
900
Average injection quantity
mm3/st.
391
389
393
Max. variation between cylinders
%
0
-3
3
Basic
*
Fixing the lever
*
Boost pressure
kPa
53.3
53.3
Boost pressure
mmHg
400
400
Injection quantity adjustment_02
Adjusting point
C
Rack position
6.6+-0.5
Pump speed
r/min
325
325
325
Average injection quantity
mm3/st.
32.6
27.6
37.6
Max. variation between cylinders
%
0
-15
15
Fixing the rack
*
Boost pressure
kPa
0
0
0
Boost pressure
mmHg
0
0
0
Boost compensator adjustment
Pump speed
r/min
500
500
500
Rack position
13.9
Boost pressure
kPa
9.3
6.6
12
Boost pressure
mmHg
70
50
90
Boost compensator adjustment_02
Pump speed
r/min
500
500
500
Rack position
16.4
Boost pressure
kPa
40
33.3
46.7
Boost pressure
mmHg
300
250
350
Test data Ex:
Governor adjustment
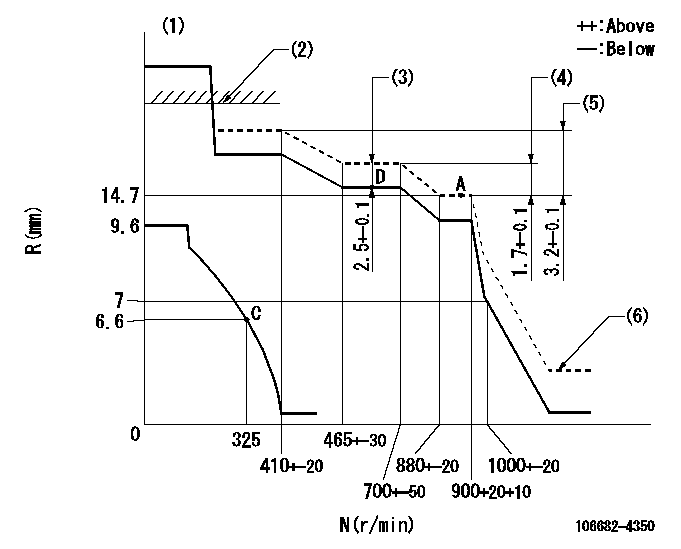
N:Pump speed
R:Rack position (mm)
(1)Target notch: K
(2)RACK LIMIT: RAL
(3)Boost compensator stroke
(4)Rack difference between N = N1 and N = N2
(5)Rack difference between N = N3 and N = N4
(6)Confirm non-injection.
----------
K=(14) RAL=18.4+0.2mm N1=900r/min N2=650r/min N3=900r/min N4=400r/min
----------
----------
K=(14) RAL=18.4+0.2mm N1=900r/min N2=650r/min N3=900r/min N4=400r/min
----------
Speed control lever angle
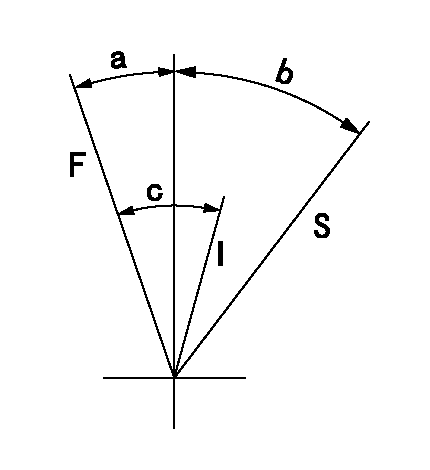
F:Full speed
I:Idle
S:Stop
----------
----------
a=(14deg)+-5deg b=27deg+-3deg c=(26deg)+-5deg
----------
----------
a=(14deg)+-5deg b=27deg+-3deg c=(26deg)+-5deg
0000001501 LEVER
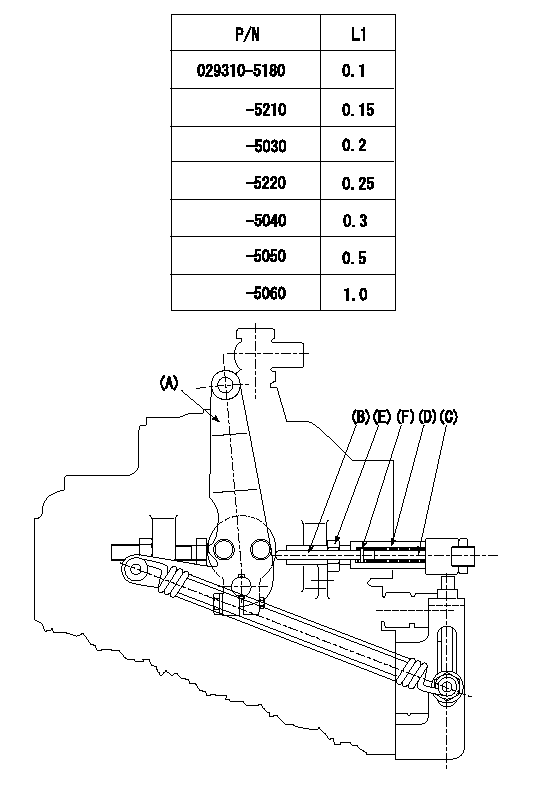
Speed lever adjustment
1. (1) For idling hold the speed lever (a) against the push rod (B).
(2)At this time, confirm that the spring (C) is not bent by the operating torque of the speed lever.
2. (1) To stop, bend the spring (C) using the speed lever.
(2)Position the rack at L2. (Adjustment is performed using the shim (F).)
(3)Set and fix using lock nut (E) so that it contacts the guide screw (D).
3. Confirm that the speed lever returns to the idling position when pulled in the stop direction and then released.
----------
L2=0.2~2mm
----------
----------
L2=0.2~2mm
----------
Timing setting

(1)Pump vertical direction
(2)Coupling's key groove position at No 1 cylinder's beginning of injection
(3)-
(4)-
----------
----------
a=(30deg)
----------
----------
a=(30deg)
Information:
preparatory step: a) remove air compressor1. Disconnect the water pump outlet line (1).2. Disconnect the water temperature regulator water bypass line (2).3. Remove the water pump (3).Install Water Pump
1. Position the water pump on the engine.2. Connect the water temperature regulator bypass line.3. Connect water pump outlet line.concluding step: a) install air compressorDisassemble Water Pump
preparatory step: a) remove water pump 1. Remove the water pump cover (1). 2. Loosen the impeller retaining nut flush with the end of the pump shaft. Install tool setup (A) and separate the impeller from the shaft.3. Remove the tool setup and impeller. 4. Remove the bearing cage retaining nuts (3).5. Remove the bearing cage and shaft assembly (2) from the pump housing.6. Remove the ceramic seal and oil seal from the pump housing.7. Remove the bearing retaining nut and spacer from the shaft assembly. 8. Press the gear and bearings from the shaft.Assemble Water Pump
1. Heat the bearings and gear to 300°F (149°C). 2. Install one bearing and its bearing cage (5) on the shaft. Install the gear (4) on the shaft with the concave side towards the bearing cage.3. Install the remaining bearing (3), spacer (2), lock and retaining nut (1). 4. Install the oil seal in the pump housing using tool setup (A). Install the oil seal (8) as shown. 5. Install the ceramic ring (11) and rubber seal (12) in the pump housing with the polished side of the ceramic ring toward the impeller.6. Position the bearing and shaft assembly in the pump housing. Install the bearing cage retaining nuts (7). Lubricate the oil seal lip lightly with SAE 30 engine oil before installing the shaft assembly.7. Install the carbon portion of the seal and the spring on the shaft.8. Install the impeller (10) and retaining nut (6). Tighten the nut to 30 5 lb. ft. (4,1 0,7 mkg) plus the amount required to align on cotter pin hole. Install the cotter pin and bend the legs of the pin around the nut.9. Install the water pump cover (9).concluding step: a) install water pump
1. Position the water pump on the engine.2. Connect the water temperature regulator bypass line.3. Connect water pump outlet line.concluding step: a) install air compressorDisassemble Water Pump
preparatory step: a) remove water pump 1. Remove the water pump cover (1). 2. Loosen the impeller retaining nut flush with the end of the pump shaft. Install tool setup (A) and separate the impeller from the shaft.3. Remove the tool setup and impeller. 4. Remove the bearing cage retaining nuts (3).5. Remove the bearing cage and shaft assembly (2) from the pump housing.6. Remove the ceramic seal and oil seal from the pump housing.7. Remove the bearing retaining nut and spacer from the shaft assembly. 8. Press the gear and bearings from the shaft.Assemble Water Pump
1. Heat the bearings and gear to 300°F (149°C). 2. Install one bearing and its bearing cage (5) on the shaft. Install the gear (4) on the shaft with the concave side towards the bearing cage.3. Install the remaining bearing (3), spacer (2), lock and retaining nut (1). 4. Install the oil seal in the pump housing using tool setup (A). Install the oil seal (8) as shown. 5. Install the ceramic ring (11) and rubber seal (12) in the pump housing with the polished side of the ceramic ring toward the impeller.6. Position the bearing and shaft assembly in the pump housing. Install the bearing cage retaining nuts (7). Lubricate the oil seal lip lightly with SAE 30 engine oil before installing the shaft assembly.7. Install the carbon portion of the seal and the spring on the shaft.8. Install the impeller (10) and retaining nut (6). Tighten the nut to 30 5 lb. ft. (4,1 0,7 mkg) plus the amount required to align on cotter pin hole. Install the cotter pin and bend the legs of the pin around the nut.9. Install the water pump cover (9).concluding step: a) install water pump