Information injection-pump assembly
BOSCH
F 019 Z10 427
f019z10427
ZEXEL
106682-3000
1066823000
HINO
220204210A
220204210a
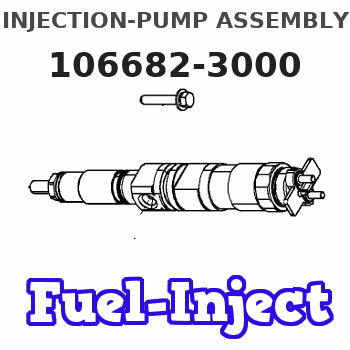
Rating:
Service parts 106682-3000 INJECTION-PUMP ASSEMBLY:
1.
_
5.
AUTOM. ADVANCE MECHANIS
8.
_
9.
_
11.
Nozzle and Holder
23600-2590A
12.
Open Pre:MPa(Kqf/cm2)
21.1{215}
15.
NOZZLE SET
Include in #1:
106682-3000
as INJECTION-PUMP ASSEMBLY
Cross reference number
BOSCH
F 019 Z10 427
f019z10427
ZEXEL
106682-3000
1066823000
HINO
220204210A
220204210a
Zexel num
Bosch num
Firm num
Name
Calibration Data:
Adjustment conditions
Test oil
1404 Test oil ISO4113 or {SAEJ967d}
1404 Test oil ISO4113 or {SAEJ967d}
Test oil temperature
degC
40
40
45
Nozzle and nozzle holder
105780-8130
Bosch type code
EFEP215A
Nozzle
105780-0050
Bosch type code
DN6TD119NP1T
Nozzle holder
105780-2090
Bosch type code
EFEP215
Opening pressure
MPa
17.2
Opening pressure
kgf/cm2
175
Injection pipe
Outer diameter - inner diameter - length (mm) mm 8-4-1000
Outer diameter - inner diameter - length (mm) mm 8-4-1000
Overflow valve (drive side)
134424-0820
Overflow valve opening pressure (drive side)
kPa
127
107
147
Overflow valve opening pressure (drive side)
kgf/cm2
1.3
1.1
1.5
Overflow valve (governor side)
134424-0820
Overflow valve opening pressure (governor side)
kPa
127
107
147
Overflow valve opening pressure (governor side)
kgf/cm2
1.3
1.1
1.5
Tester oil delivery pressure
kPa
157
157
157
Tester oil delivery pressure
kgf/cm2
1.6
1.6
1.6
Direction of rotation (viewed from drive side)
Left L
Left L
Injection timing adjustment
Direction of rotation (viewed from drive side)
Left L
Left L
Injection order
1-4-2-6-
3-5
Pre-stroke
mm
3.3
3.27
3.33
Beginning of injection position
Drive side NO.1
Drive side NO.1
Difference between angles 1
Cal 1-4 deg. 60 59.75 60.25
Cal 1-4 deg. 60 59.75 60.25
Difference between angles 2
Cyl.1-2 deg. 120 119.75 120.25
Cyl.1-2 deg. 120 119.75 120.25
Difference between angles 3
Cal 1-6 deg. 180 179.75 180.25
Cal 1-6 deg. 180 179.75 180.25
Difference between angles 4
Cal 1-3 deg. 240 239.75 240.25
Cal 1-3 deg. 240 239.75 240.25
Difference between angles 5
Cal 1-5 deg. 300 299.75 300.25
Cal 1-5 deg. 300 299.75 300.25
Injection quantity adjustment
Adjusting point
A
Rack position
14.4
Pump speed
r/min
1110
1110
1110
Average injection quantity
mm3/st.
427
424
430
Max. variation between cylinders
%
0
-3
3
Basic
*
Fixing the lever
*
Boost pressure
kPa
58.7
58.7
Boost pressure
mmHg
440
440
Injection quantity adjustment_02
Adjusting point
B
Rack position
5+-0.5
Pump speed
r/min
265
265
265
Average injection quantity
mm3/st.
14
11
17
Max. variation between cylinders
%
0
-15
15
Fixing the rack
*
Boost pressure
kPa
0
0
0
Boost pressure
mmHg
0
0
0
Boost compensator adjustment
Pump speed
r/min
500
500
500
Rack position
R1-3.9
Boost pressure
kPa
21.3
18.6
24
Boost pressure
mmHg
160
140
180
Boost compensator adjustment_02
Pump speed
r/min
500
500
500
Rack position
R1(14.4)
Boost pressure
kPa
45.3
45.3
45.3
Boost pressure
mmHg
340
340
340
Test data Ex:
Governor adjustment
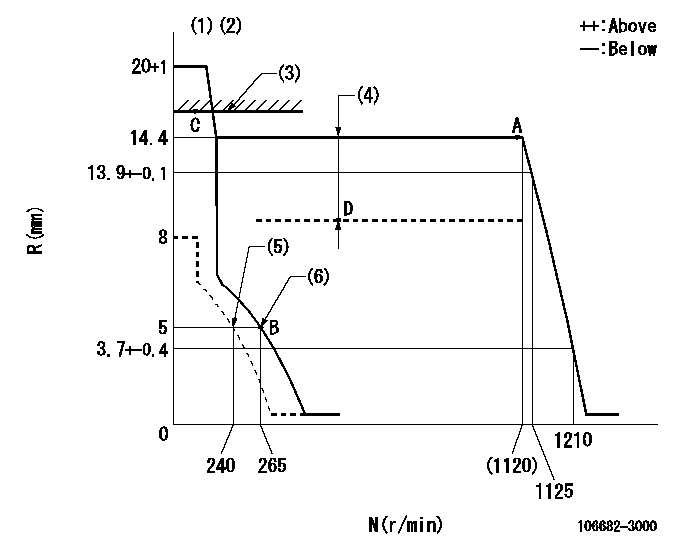
N:Pump speed
R:Rack position (mm)
(1)Target notch: K
(2)Tolerance for racks not indicated: +-0.05mm.
(3)Boost compensator excessive fuel lever at operation: L1 (at 0 boost pressure)
(4)Boost compensator stroke: BCL
(5)Set idle sub-spring
(6)Main spring setting
----------
K=6 L1=15.4+0.2mm BCL=3.9+-0.1mm
----------
----------
K=6 L1=15.4+0.2mm BCL=3.9+-0.1mm
----------
Speed control lever angle
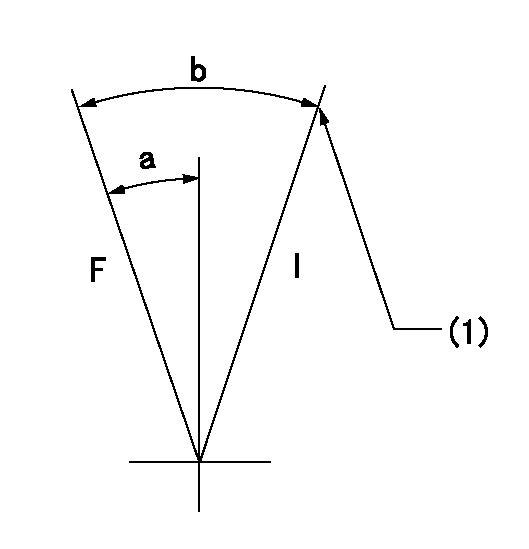
F:Full speed
I:Idle
(1)Stopper bolt setting
----------
----------
a=9deg+-5deg b=38deg+-5deg
----------
----------
a=9deg+-5deg b=38deg+-5deg
Stop lever angle
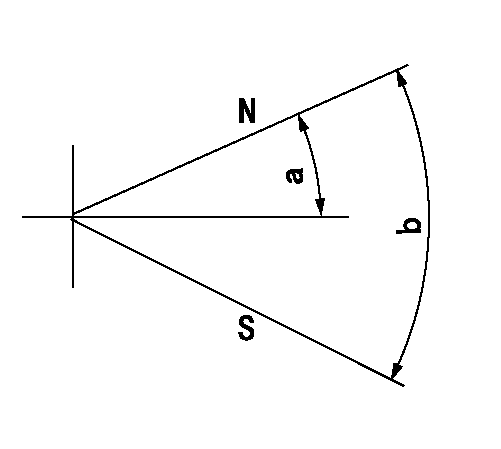
N:Pump normal
S:Stop the pump.
----------
----------
a=27deg+-5deg b=53deg+-5deg
----------
----------
a=27deg+-5deg b=53deg+-5deg
0000001101
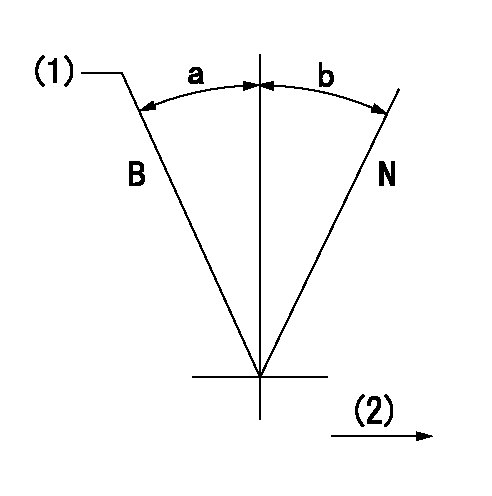
N:Normal
B:When boosted
(1)Rack position = aa at boost pressure 0.
(2)Drive side
----------
aa=15.4+0.2mm
----------
a=(18deg) b=(15deg)
----------
aa=15.4+0.2mm
----------
a=(18deg) b=(15deg)
0000001501 Q ADJUSTMENT PIPING
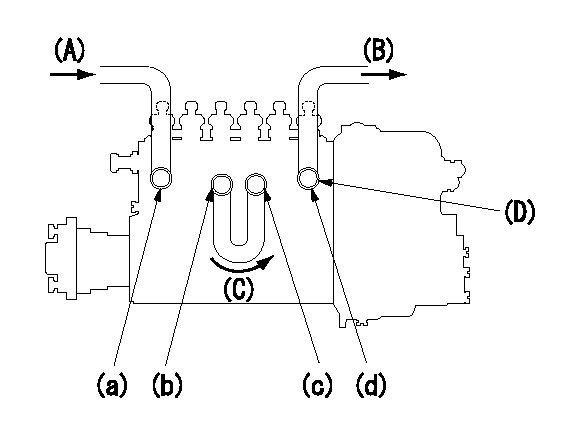
Fuel hose adjusting procedure
Fuel inlet hose A
Fuel inlet hose B
Fuel hose C ( (for bypass)
(D) Overflow valve
1. Because the pump gallery is divided into two, be careful of the fuel piping.
(1)Connect the fuel inlet hose to port (a).
(2)Connect the fuel hose (for bypass) to ports (b) and (c).
(3)Assemble the overflow valve (D) to the fuel outlet hose and connect to port (d).
----------
----------
----------
----------
Timing setting

(1)Pump vertical direction
(2)Coupling's key groove position at No 1 cylinder's beginning of injection
(3)-
(4)-
----------
----------
a=(2deg)
----------
----------
a=(2deg)
Information:
start by:a) remove air compressor 1. Remove elbow (1) and adapter. Remove the gasket, screen and gasket from behind the flange.2. Remove air compressor governor (2).3. Put a mark on the head assembly and block for correct assembly. 4. Remove six bolts (3). Remove head assembly (4). 5. Remove inlet valve springs (5) from the head assembly.6. Remove discharge valve seats (6). 7. Remove discharge valves (7). Remove springs from behind the valves. Check the discharge valve stops for wear or damage. If the discharge valve travel exceeds .057 in. (1.45 mm), make a replacement of the head assembly. 8. Remove inlet valves (8) from guides. Remove guides (9) from around the inlet valve seats. 9. Remove unloader spring (10), spring seat and spring saddle (12).10. Remove unloader plungers (11) and guides. 11. To remove unloader pistons (13) from the bore, put a cover over the inlet port, then blow air pressure in the governor mounting pad unloader port (14). 12. Check inlet valve seats (15) and unloader bore bushings (16) for damage or wear. If necessary, make a replacement. 13. Remove bolts (17). Remove cover (18) and gasket from the crankcase assembly.14. Put marks on the rod bearing caps and rods for correct assembly. 15. Remove bolts (19) and locks. Remove rod bearing caps (20). Push the pistons and rods through the top of the crankcase assembly. 16. Remove rod pin (21) from the piston. Remove rod (23).17. Remove bearings (22) from the rods and caps. 18. Use tooling (A) to remove bushing (24) from the rod. 19. Remove buttons (25) from each end of the rod pins. 20. Remove piston rings (26) from piston (27) with an approved ring expander. 21. Remove O-ring seal (29) from the crankshaft.22. Remove bolts (28). Remove adapter (30) from the crankcase assembly. 23. Remove three O-ring seals (32) from the adapter.24. Remove thrust bearing (31). 25. Use tooling (A) and a press to remove the bearing from the adapter.
Do not cause damage to the bearing surfaces of the crankshaft when it is removed from the crankcase assembly.
26. Remove crankshaft (33) from the crankcase assembly. 27. Remove bolts (34). Remove cover (35). Remove two O-ring seals from the crankcase assembly. 28. Remove O-ring seal (37) from the cover.29. Remove thrust bearing (36). 30. Remove bearing (38) from the cover.Assemble Air Compressor
1. Check all parts for damage or wear. If necessary, make a replacement with a new part.2. Make sure all parts are clean and free of dirt and foreign material. 3. Use tool (A) and a press to install the bearing in cover (1). 4. Install O-ring seal (3) on the cover.5. Install thrust bearing (2). 6. Install O-ring seals (4) in the crankcase assembly.7. Put a small amount of SAE 30 oil on the O-ring seal and install the cover on crankcase assembly (5). Tighten the bolts to a torque of 25 to 35 lb.ft. (35 to 45 N m). 8. Put crankshaft (6) in position in the crankcase assembly.
Do not cause damage to the bearing surfaces of the crankshaft when it is removed from the crankcase assembly.
26. Remove crankshaft (33) from the crankcase assembly. 27. Remove bolts (34). Remove cover (35). Remove two O-ring seals from the crankcase assembly. 28. Remove O-ring seal (37) from the cover.29. Remove thrust bearing (36). 30. Remove bearing (38) from the cover.Assemble Air Compressor
1. Check all parts for damage or wear. If necessary, make a replacement with a new part.2. Make sure all parts are clean and free of dirt and foreign material. 3. Use tool (A) and a press to install the bearing in cover (1). 4. Install O-ring seal (3) on the cover.5. Install thrust bearing (2). 6. Install O-ring seals (4) in the crankcase assembly.7. Put a small amount of SAE 30 oil on the O-ring seal and install the cover on crankcase assembly (5). Tighten the bolts to a torque of 25 to 35 lb.ft. (35 to 45 N m). 8. Put crankshaft (6) in position in the crankcase assembly.