Information injection-pump assembly
BOSCH
F 01G 09U 0JB
f01g09u0jb
ZEXEL
106682-1120
1066821120
ISUZU
1156035140
1156035140
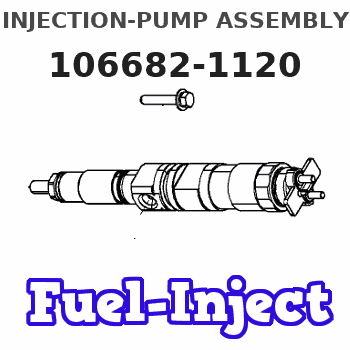
Rating:
Service parts 106682-1120 INJECTION-PUMP ASSEMBLY:
1.
_
5.
AUTOM. ADVANCE MECHANIS
7.
COUPLING PLATE
8.
_
11.
Nozzle and Holder
1-15300-438-0
12.
Open Pre:MPa(Kqf/cm2)
15.
NOZZLE SET
Include in #1:
106682-1120
as INJECTION-PUMP ASSEMBLY
Cross reference number
BOSCH
F 01G 09U 0JB
f01g09u0jb
ZEXEL
106682-1120
1066821120
ISUZU
1156035140
1156035140
Zexel num
Bosch num
Firm num
Name
F 01G 09U 0JB
1156035140 ISUZU
INJECTION-PUMP ASSEMBLY
6WF1-TMC * K 14CA INJECTION PUMP ASSY PE6P,6PD PE
6WF1-TMC * K 14CA INJECTION PUMP ASSY PE6P,6PD PE
Calibration Data:
Adjustment conditions
Test oil
1404 Test oil ISO4113 or {SAEJ967d}
1404 Test oil ISO4113 or {SAEJ967d}
Test oil temperature
degC
40
40
45
Nozzle and nozzle holder
105780-8130
Bosch type code
EFEP215A
Nozzle
105780-0050
Bosch type code
DN6TD119NP1T
Nozzle holder
105780-2090
Bosch type code
EFEP215
Opening pressure
MPa
17.2
Opening pressure
kgf/cm2
175
Injection pipe
Outer diameter - inner diameter - length (mm) mm 8-4-1000
Outer diameter - inner diameter - length (mm) mm 8-4-1000
Overflow valve
134424-4320
Overflow valve opening pressure
kPa
255
221
289
Overflow valve opening pressure
kgf/cm2
2.6
2.25
2.95
Tester oil delivery pressure
kPa
255
255
255
Tester oil delivery pressure
kgf/cm2
2.6
2.6
2.6
Direction of rotation (viewed from drive side)
Right R
Right R
Injection timing adjustment
Direction of rotation (viewed from drive side)
Right R
Right R
Injection order
1-5-3-6-
2-4
Pre-stroke
mm
2.8
2.75
2.85
Beginning of injection position
Drive side NO.1
Drive side NO.1
Difference between angles 1
Cal 1-5 deg. 60 59.5 60.5
Cal 1-5 deg. 60 59.5 60.5
Difference between angles 2
Cal 1-3 deg. 120 119.5 120.5
Cal 1-3 deg. 120 119.5 120.5
Difference between angles 3
Cal 1-6 deg. 180 179.5 180.5
Cal 1-6 deg. 180 179.5 180.5
Difference between angles 4
Cyl.1-2 deg. 240 239.5 240.5
Cyl.1-2 deg. 240 239.5 240.5
Difference between angles 5
Cal 1-4 deg. 300 299.5 300.5
Cal 1-4 deg. 300 299.5 300.5
Injection quantity adjustment
Adjusting point
A
Rack position
11.3
Pump speed
r/min
1115
1115
1115
Average injection quantity
mm3/st.
417
413
421
Max. variation between cylinders
%
0
-3
3
Basic
*
Fixing the lever
*
Boost pressure
kPa
169
169
Boost pressure
mmHg
1270
1270
Injection quantity adjustment_02
Adjusting point
B
Rack position
4.4+-0.5
Pump speed
r/min
290
290
290
Average injection quantity
mm3/st.
18
14.8
21.2
Max. variation between cylinders
%
0
-15
15
Fixing the rack
*
Boost pressure
kPa
0
0
0
Boost pressure
mmHg
0
0
0
Boost compensator adjustment
Pump speed
r/min
550
550
550
Rack position
R1-4
Boost pressure
kPa
70
66
74
Boost pressure
mmHg
525
495
555
Boost compensator adjustment_02
Pump speed
r/min
550
550
550
Rack position
R1(11.3)
Boost pressure
kPa
156
149.3
162.7
Boost pressure
mmHg
1170
1120
1220
Test data Ex:
Governor adjustment
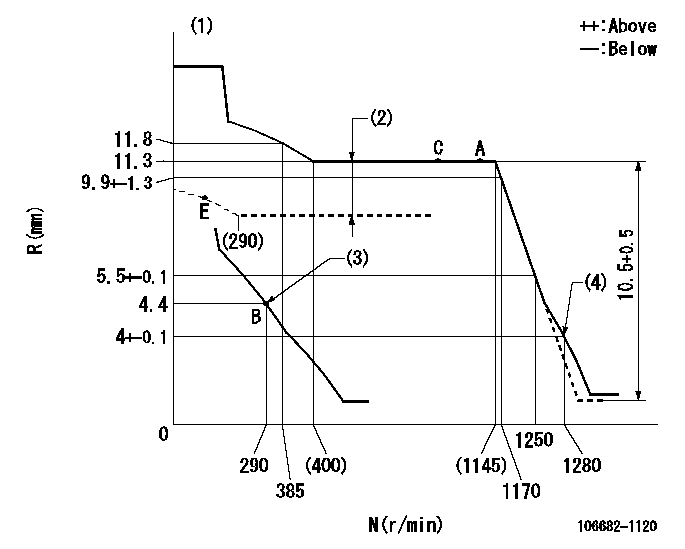
N:Pump speed
R:Rack position (mm)
(1)Tolerance for racks not indicated: +-0.05mm.
(2)Boost compensator stroke: BCL
(3)Main spring setting
(4)Set idle sub-spring
----------
BCL=4+-0.1mm
----------
----------
BCL=4+-0.1mm
----------
Speed control lever angle
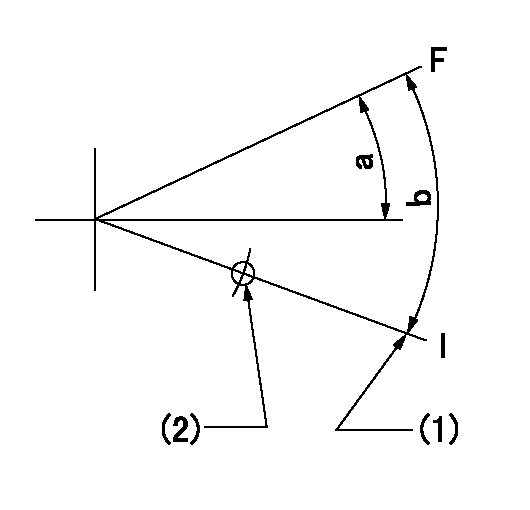
F:Full speed
I:Idle
(1)Stopper bolt setting
(2)Use the hole at R = aa
----------
aa=135mm
----------
a=(4deg)+-5deg b=(14deg)+-5deg
----------
aa=135mm
----------
a=(4deg)+-5deg b=(14deg)+-5deg
0000000901
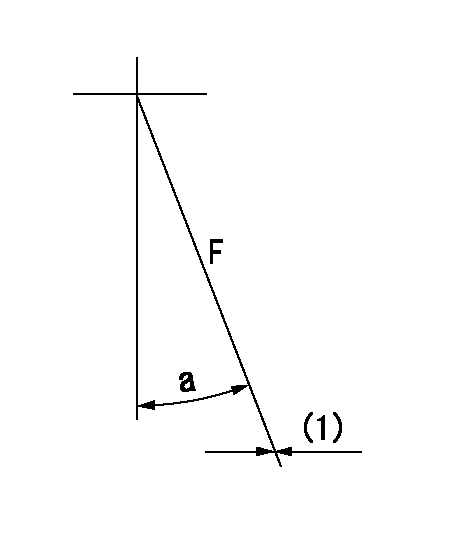
F:Full load
(1)Fix using the stopper bolt.
----------
----------
a=15deg+-5deg
----------
----------
a=15deg+-5deg
Stop lever angle
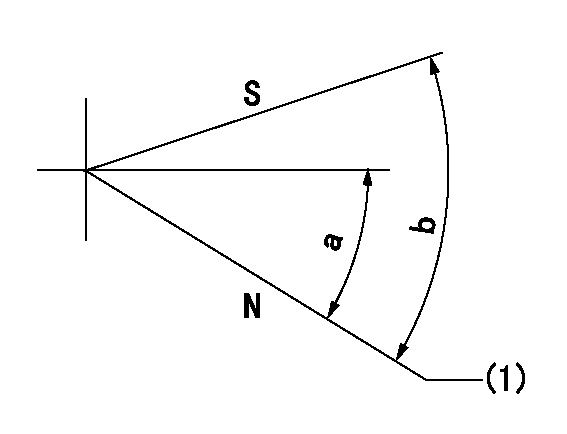
N:Pump normal
S:Stop the pump.
(1)Normal
----------
----------
a=27deg+-5deg b=71deg+-5deg
----------
----------
a=27deg+-5deg b=71deg+-5deg
Timing setting

(1)Pump vertical direction
(2)Position of coupling's threaded hole at No 1 cylinder's beginning of injection
(3)B.T.D.C.: aa
(4)-
----------
aa=18deg
----------
a=(30deg)
----------
aa=18deg
----------
a=(30deg)
Information:
Bolts And Bolt Torque
A bolt which is too long may "bottom" before the head is tight against the part it is to hold. The threads can be damaged when a "long" bolt is removed.If a bolt is too short, there may not be enough threads engaged to hold the part securely.Apply proper torque values to all bolts and nuts when assembling Caterpillar equipment. When a specific torque value is required, the value is listed in the SPECIFICATIONS section of the Service Manual. Tighten all other bolts and nuts for general usage, hydraulic valve bodies, or taperlock studs to the torque values given in the torque charts.T-T-T Procedure
A torque-turn-tighten (T-T-T) procedure is used in many specifications and instructions. 1. Clean the bolt and nut threads.2. Put lubricant on the threads and the seat face of the bolt and the nut.3. Turn the bolt or the nut tight according to the torque specification.4. Put a location mark on the part and on the bolt or the nut.5. Turn the bolt or the nut tighter the amount of degrees according to the specifications. The side of a nut or bolt head can be used for reference if a mark can not be put on. Torque Wrench Extension
When a torque wrench extension is used with a torque wrench, the torque indication on the torque wrench will be less than the real torque.
TORQUE WRENCH WITH TORQUE WRENCH EXTENSION
E: Torque wrench drive axis-to-torque wrench extension drive axis. W: Mark on handle-to-torque wrench drive axis.1. Put a mark on the handle. Measure the handle from the mark to the axis of the torque wrench drive (W).2. Measure the torque wrench extension from the torque wrench drive to the axis of the torque wrench extension drive (E).3. To get correct torque indication (TI) when the real torque (RT) is known: Example: W = 12 in. (304.8 mm); E = 2.56 in. (65.0 mm); RT (from specifications) = 125 lb. ft. (170 N m). 4. Hold the torque wrench handle with the longest finger of the hand over the mark on the handle to get the real torque (RT) with low torque indication (TI) on the torque wrench.Locks
Flat metal locks must be installed properly to be effective. Bend one end of the lock around the edge of the part. Bend the other end against one flat surface of the nut or bolt head.Always install new locks in compartments which house moving parts.If lockwashers are installed on housing made of aluminum, use a flat washer between the lockwasher and the housing. Lines And Wires
When removing or disconnecting a group of lines or wires, tag each one to assure proper assembly.Lubrication
Where applicable, fill the compartments of the components serviced with the amount, type and grade of lubricant recommended in the Lubrication and Maintenance Guide.Rust Preventive Compound
Clean the rust preventive compound from all machined surfaces of new parts before installing them.Shims
When shims are removed, tie them together and identify them as to location. Keep shims clean and flat until they
A bolt which is too long may "bottom" before the head is tight against the part it is to hold. The threads can be damaged when a "long" bolt is removed.If a bolt is too short, there may not be enough threads engaged to hold the part securely.Apply proper torque values to all bolts and nuts when assembling Caterpillar equipment. When a specific torque value is required, the value is listed in the SPECIFICATIONS section of the Service Manual. Tighten all other bolts and nuts for general usage, hydraulic valve bodies, or taperlock studs to the torque values given in the torque charts.T-T-T Procedure
A torque-turn-tighten (T-T-T) procedure is used in many specifications and instructions. 1. Clean the bolt and nut threads.2. Put lubricant on the threads and the seat face of the bolt and the nut.3. Turn the bolt or the nut tight according to the torque specification.4. Put a location mark on the part and on the bolt or the nut.5. Turn the bolt or the nut tighter the amount of degrees according to the specifications. The side of a nut or bolt head can be used for reference if a mark can not be put on. Torque Wrench Extension
When a torque wrench extension is used with a torque wrench, the torque indication on the torque wrench will be less than the real torque.
TORQUE WRENCH WITH TORQUE WRENCH EXTENSION
E: Torque wrench drive axis-to-torque wrench extension drive axis. W: Mark on handle-to-torque wrench drive axis.1. Put a mark on the handle. Measure the handle from the mark to the axis of the torque wrench drive (W).2. Measure the torque wrench extension from the torque wrench drive to the axis of the torque wrench extension drive (E).3. To get correct torque indication (TI) when the real torque (RT) is known: Example: W = 12 in. (304.8 mm); E = 2.56 in. (65.0 mm); RT (from specifications) = 125 lb. ft. (170 N m). 4. Hold the torque wrench handle with the longest finger of the hand over the mark on the handle to get the real torque (RT) with low torque indication (TI) on the torque wrench.Locks
Flat metal locks must be installed properly to be effective. Bend one end of the lock around the edge of the part. Bend the other end against one flat surface of the nut or bolt head.Always install new locks in compartments which house moving parts.If lockwashers are installed on housing made of aluminum, use a flat washer between the lockwasher and the housing. Lines And Wires
When removing or disconnecting a group of lines or wires, tag each one to assure proper assembly.Lubrication
Where applicable, fill the compartments of the components serviced with the amount, type and grade of lubricant recommended in the Lubrication and Maintenance Guide.Rust Preventive Compound
Clean the rust preventive compound from all machined surfaces of new parts before installing them.Shims
When shims are removed, tie them together and identify them as to location. Keep shims clean and flat until they