Information injection-pump assembly
ZEXEL
106681-4361
1066814361
MITSUBISHI-HEAV
35A6500090
35a6500090
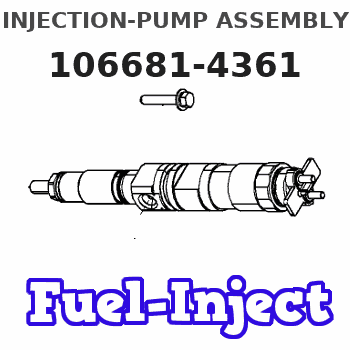
Rating:
Service parts 106681-4361 INJECTION-PUMP ASSEMBLY:
1.
_
7.
COUPLING PLATE
8.
_
9.
_
11.
Nozzle and Holder
35A6100010
12.
Open Pre:MPa(Kqf/cm2)
21.6{220}
15.
NOZZLE SET
Include in #1:
106681-4361
as INJECTION-PUMP ASSEMBLY
Cross reference number
ZEXEL
106681-4361
1066814361
MITSUBISHI-HEAV
35A6500090
35a6500090
Zexel num
Bosch num
Firm num
Name
Calibration Data:
Adjustment conditions
Test oil
1404 Test oil ISO4113 or {SAEJ967d}
1404 Test oil ISO4113 or {SAEJ967d}
Test oil temperature
degC
40
40
45
Nozzle and nozzle holder
105780-8130
Bosch type code
EFEP215A
Nozzle
105780-0050
Bosch type code
DN6TD119NP1T
Nozzle holder
105780-2090
Bosch type code
EFEP215
Opening pressure
MPa
17.2
Opening pressure
kgf/cm2
175
Injection pipe
Outer diameter - inner diameter - length (mm) mm 8-4-1000
Outer diameter - inner diameter - length (mm) mm 8-4-1000
Overflow valve
131424-3420
Overflow valve opening pressure
kPa
255
221
289
Overflow valve opening pressure
kgf/cm2
2.6
2.25
2.95
Tester oil delivery pressure
kPa
157
157
157
Tester oil delivery pressure
kgf/cm2
1.6
1.6
1.6
Direction of rotation (viewed from drive side)
Left L
Left L
Injection timing adjustment
Direction of rotation (viewed from drive side)
Left L
Left L
Injection order
1-5-3-6-
2-4
Pre-stroke
mm
2.8
2.75
2.85
Rack position
Point A R=A
Point A R=A
Beginning of injection position
Governor side NO.1
Governor side NO.1
Difference between angles 1
Cal 1-5 deg. 60 59.5 60.5
Cal 1-5 deg. 60 59.5 60.5
Difference between angles 2
Cal 1-3 deg. 120 119.5 120.5
Cal 1-3 deg. 120 119.5 120.5
Difference between angles 3
Cal 1-6 deg. 180 179.5 180.5
Cal 1-6 deg. 180 179.5 180.5
Difference between angles 4
Cyl.1-2 deg. 240 239.5 240.5
Cyl.1-2 deg. 240 239.5 240.5
Difference between angles 5
Cal 1-4 deg. 300 299.5 300.5
Cal 1-4 deg. 300 299.5 300.5
Injection quantity adjustment
Adjusting point
A
Rack position
14.3
Pump speed
r/min
900
900
900
Average injection quantity
mm3/st.
431
422
440
Max. variation between cylinders
%
0
-3
3
Basic
*
Fixing the lever
*
Boost pressure
kPa
123
123
Boost pressure
mmHg
920
920
Injection quantity adjustment_02
Adjusting point
B
Rack position
6.8+-0.5
Pump speed
r/min
375
375
375
Average injection quantity
mm3/st.
20
17
23
Max. variation between cylinders
%
0
-10
10
Fixing the rack
*
Boost pressure
kPa
0
0
0
Boost pressure
mmHg
0
0
0
Boost compensator adjustment
Pump speed
r/min
600
600
600
Rack position
R1-3.2
Boost pressure
kPa
46.7
44
49.4
Boost pressure
mmHg
350
330
370
Boost compensator adjustment_02
Pump speed
r/min
600
600
600
Rack position
R1(14.3)
Boost pressure
kPa
109
102.3
115.7
Boost pressure
mmHg
820
770
870
Timer adjustment
Pump speed
r/min
(N1+50)-
-
Advance angle
deg.
0
0
0
Remarks
Start
Start
Timer adjustment_02
Pump speed
r/min
N1
Advance angle
deg.
0.5
Remarks
Measure the actual speed.
Measure the actual speed.
Timer adjustment_03
Pump speed
r/min
-
Advance angle
deg.
4
3.5
4.5
Remarks
Measure the actual speed, stop
Measure the actual speed, stop
Test data Ex:
Governor adjustment
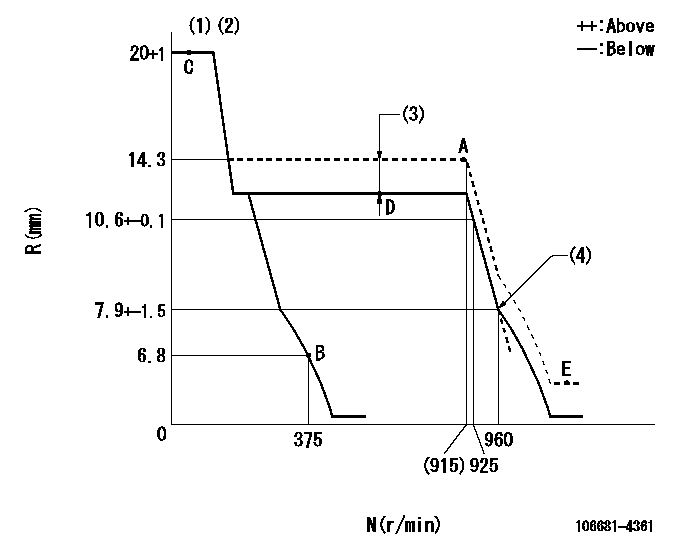
N:Pump speed
R:Rack position (mm)
(1)Notch fixed: K
(2)Tolerance for racks not indicated: +-0.05mm.
(3)Boost compensator stroke: BCL
(4)Idle sub spring setting: L1.
----------
K=22 BCL=3.2+-0.1mm L1=7.9-0.5mm
----------
----------
K=22 BCL=3.2+-0.1mm L1=7.9-0.5mm
----------
Speed control lever angle
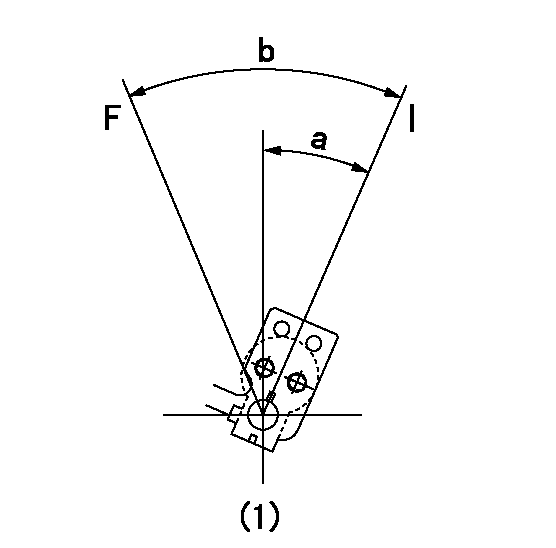
F:Full speed
I:Idle
(1)At the center of the lever key groove
----------
----------
a=(2deg)+-5deg b=(28deg)+-5deg
----------
----------
a=(2deg)+-5deg b=(28deg)+-5deg
Stop lever angle

N:Pump normal
S:Stop the pump.
(1)Pump speed aa, rack position bb
(2)Normal
----------
aa=0r/min bb=1-0.5mm
----------
a=33deg+-5deg b=(73deg)
----------
aa=0r/min bb=1-0.5mm
----------
a=33deg+-5deg b=(73deg)
Timing setting

(1)Pump vertical direction
(2)Coupling's key groove position at No 1 cylinder's beginning of injection
(3)-
(4)-
----------
----------
a=(110deg)
----------
----------
a=(110deg)
Information:
Never disconnect any charging unit circuit or battery circuit cable from battery when the charging unit is charging.
9S1990 BATTERY CHARGER TESTERLoad test a battery that does not hold a charge when in use. To do this, put a test load across the main connections (terminals) of the battery. For a 6, 8, or 12V battery, put a test load of three times the ampere/hour rating, (the maximum test load on any battery is 500 amperes). Let the test load remove the charge (discharge) of the battery for 15 seconds and immediately test the battery voltage. A 6V battery in good condition will show 4.5V; an 8V battery will show 6V; a 12V battery will show 9V. Each cell must show 1.6V on either a 6, 8, or 12V battery.The Special Instruction (GEG00058) with the 9S1990 Battery Charger Tester gives the battery testing procedure.Charging System
5P300 Electrical Tester. Make reference to Special Instruction (GEG02276) and to the instructions inside of the cover of the tester, when testing with the 5P300 Electrical Tester.The condition of charge in the battery at each regular inspection will show if the charging system is operating correctly. An adjustment is necessary when the battery is constantly in a low condition of charge or a large amount of water is needed (more than one ounce of water per cell per week or per every 50 service hours).Make a test of the charging unit and voltage regulator on the engine, when possible, using wiring and components that are a permanent part of the system. Off the engine (bench) testing will give a test of the charging unit and voltage regulator operation. This testing will give an indication of needed repair. After repairs are made, again make a test to give proof that the units are repaired to their original operating condition.Before starting the on engine testing, the charging system and battery must be checked as given in the Steps below.1. Battery must be at least 75% (1.240 Sp. Gr.) full charged and held tightly in place. The battery holder must not put too much stress on the battery.2. Cables between the battery, starter and engine ground must be the correct size. Wires and cables must be free of corrosion and have cable support clamps to prevent stress on battery connections (terminals).3. Leads, junctions, switches and panel instruments that have direct relation to the charging circuit must give correct circuit control.4. Inspect the drive components for the charging unit to be sure they are free of grease and oil and have the ability to operate the charging unit.Alternator Regulator (Delco)
When an alternator is either overcharging or undercharging the battery, the alternator charging rate can be adjusted. Remove the hollow head screw from the cover of the alternator regulator and use a screwdriver to turn the inside adjustment. Turn the adjustment toward the "+" to increase or toward the "-" to decrease the alternator charging rate.
ALTERNATOR REGULATORPulley Nut of Delco-Remy Alternators
Tighten the nut that holds the pulley to a torque