Information injection-pump assembly
ZEXEL
106681-4360
1066814360
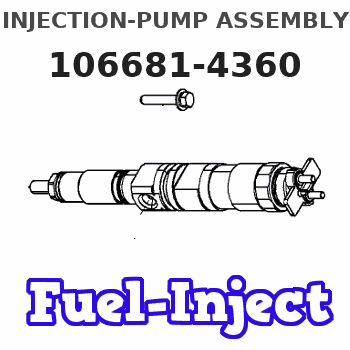
Rating:
Cross reference number
ZEXEL
106681-4360
1066814360
Zexel num
Bosch num
Firm num
Name
106681-4360
INJECTION-PUMP ASSEMBLY
Calibration Data:
Adjustment conditions
Test oil
1404 Test oil ISO4113 or {SAEJ967d}
1404 Test oil ISO4113 or {SAEJ967d}
Test oil temperature
degC
40
40
45
Nozzle and nozzle holder
105780-8130
Bosch type code
EFEP215A
Nozzle
105780-0050
Bosch type code
DN6TD119NP1T
Nozzle holder
105780-2090
Bosch type code
EFEP215
Opening pressure
MPa
17.2
Opening pressure
kgf/cm2
175
Injection pipe
Outer diameter - inner diameter - length (mm) mm 8-4-1000
Outer diameter - inner diameter - length (mm) mm 8-4-1000
Overflow valve
131424-3420
Overflow valve opening pressure
kPa
255
221
289
Overflow valve opening pressure
kgf/cm2
2.6
2.25
2.95
Tester oil delivery pressure
kPa
157
157
157
Tester oil delivery pressure
kgf/cm2
1.6
1.6
1.6
Direction of rotation (viewed from drive side)
Left L
Left L
Injection timing adjustment
Direction of rotation (viewed from drive side)
Left L
Left L
Injection order
1-5-3-6-
2-4
Pre-stroke
mm
2.8
2.75
2.85
Rack position
Point A R=A
Point A R=A
Beginning of injection position
Governor side NO.1
Governor side NO.1
Difference between angles 1
Cal 1-5 deg. 60 59.5 60.5
Cal 1-5 deg. 60 59.5 60.5
Difference between angles 2
Cal 1-3 deg. 120 119.5 120.5
Cal 1-3 deg. 120 119.5 120.5
Difference between angles 3
Cal 1-6 deg. 180 179.5 180.5
Cal 1-6 deg. 180 179.5 180.5
Difference between angles 4
Cyl.1-2 deg. 240 239.5 240.5
Cyl.1-2 deg. 240 239.5 240.5
Difference between angles 5
Cal 1-4 deg. 300 299.5 300.5
Cal 1-4 deg. 300 299.5 300.5
Injection quantity adjustment
Adjusting point
A
Rack position
14.2
Pump speed
r/min
980
980
980
Average injection quantity
mm3/st.
456
447
465
Max. variation between cylinders
%
0
-3
3
Basic
*
Fixing the lever
*
Boost pressure
kPa
127
127
Boost pressure
mmHg
950
950
Injection quantity adjustment_02
Adjusting point
B
Rack position
6.9+-0.5
Pump speed
r/min
250
250
250
Average injection quantity
mm3/st.
23.5
20.5
26.5
Max. variation between cylinders
%
0
-10
10
Fixing the rack
*
Boost pressure
kPa
0
0
0
Boost pressure
mmHg
0
0
0
Boost compensator adjustment
Pump speed
r/min
600
600
600
Rack position
R1-1.5
Boost pressure
kPa
73.3
70.6
76
Boost pressure
mmHg
550
530
570
Boost compensator adjustment_02
Pump speed
r/min
600
600
600
Rack position
R1(14.2)
Boost pressure
kPa
113
106.3
119.7
Boost pressure
mmHg
850
800
900
Timer adjustment
Pump speed
r/min
450--
Advance angle
deg.
0
0
0
Remarks
Start
Start
Timer adjustment_02
Pump speed
r/min
400
Advance angle
deg.
0.5
Timer adjustment_03
Pump speed
r/min
700
Advance angle
deg.
4
3.5
4.5
Remarks
Finish
Finish
Test data Ex:
Governor adjustment

N:Pump speed
R:Rack position (mm)
(1)Notch fixed: K
(2)Tolerance for racks not indicated: +-0.05mm.
(3)Boost compensator stroke: BCL
----------
K=14 BCL=1.5+-0.1mm
----------
----------
K=14 BCL=1.5+-0.1mm
----------
Speed control lever angle

F:Full speed
I:Idle
(1)Stopper bolt setting
----------
----------
a=17deg+-5deg b=36deg+-5deg
----------
----------
a=17deg+-5deg b=36deg+-5deg
Stop lever angle

N:Pump normal
S:Stop the pump.
(1)Pump speed aa, rack position bb
(2)Normal
----------
aa=0r/min bb=1-0.5mm
----------
a=33deg+-5deg b=(73deg)
----------
aa=0r/min bb=1-0.5mm
----------
a=33deg+-5deg b=(73deg)
Timing setting

(1)Pump vertical direction
(2)Coupling's key groove position at No 1 cylinder's beginning of injection
(3)-
(4)-
----------
----------
a=(110deg)
----------
----------
a=(110deg)
Information:
BRAKESAVER CONTROL VALVE IN FLOW CONTROL POSITION
1. Passage to oil filter. 2. Oil cooler. 3. Air line. 4. Oil inlet passage. 5. Valve spool. 6. Control valve body. 7. Differential pressure valve. 8. Poppet valve. 9. BrakeSaver. 10. BrakeSaver inlet pressure. 11. BrakeSaver outlet pressure.BrakeSaver Operator Controls
Two types of controls are available for the BrakeSaver: a manual control and an automatic control. Supply air goes into the circuit through pressure reducing valve (17). The pressure reducing valve keeps a maximum pressure in the control circuit of 40 psi (280 kPa).This pressure air is available at manual control lever (2) in the operator's compartment and at the solenoid valve (8). When ignition switch (5) is turned ON, the electrical circuit to manual-automatic switch (3) has current available. [Switch (3) is shown in the MANUAL position.] In the MANUAL position, switch (3) opens the circuit. The automatic section of switch (3) is in the OFF position and the BrakeSaver can only be operated manually. Maximum supply air pressure from the air compressor (not shown) is 125 psi (860 kPa).
BRAKESAVER CONTROL CIRCUIT SCHEMATIC
1. Pressure reducing valve. 2. Manual control lever. 3. Manual-automatic selector switch. 4. Control valve. 5. Ignition switch. 6. Double check valve. 7. Accelerator switch. 8. Solenoid valve. 9. Clutch switch.Manual Control
When the BrakeSaver manual-automatic selector switch (3) is in the MANUAL position, the BrakeSaver can only be turned on by the operator by moving manual control lever (2). With control lever (2) in the BrakeSaver ON position, air goes through manual control lever (2) and double check valve (6) to control valve (4). A valve spool moves and the BrakeSaver gets oil. It holds this oil until manual control lever (2) is moved to the BrakeSaver OFF position. Air can go from control valve (4) to the atmosphere through manual control lever (2).The farther control lever (2) is moved toward the ON position, the higher the pressure of the air sent to the control valve. An increase in air pressure in the control valve causes an increase in the oil pressure in the BrakeSaver. An increase in the oil pressure in the BrakeSaver causes an increase in the braking force in the BrakeSaver. The operator can give modulation to the braking force in the BrakeSaver through the movement of control lever (2).An air pressure gauge gives the operator a relative indication of the air pressure being sent to the control valve. Through the use of the indication on the air pressure gauge in relation to engine rpm, the operator can get approximately the same braking effect from the BrakeSaver time after time. This lets the operator more easily control the desired wheel speed of the vehicle.An oil temperature gauge gives the operator an indication of the ability of the engine cooling system to control the heat in the BrakeSaver during its operation. If the gauge reads too HOT, move control lever (2) to the OFF position and use the service brakes to control the wheel speed of the
Have questions with 106681-4360?
Group cross 106681-4360 ZEXEL
Mitsubishi-Heav
Niigata-Urawa
Mitsubishi-Heav
Yanmar
Yanmar
Mitsubishi-Heav
Komatsu
106681-4360
INJECTION-PUMP ASSEMBLY