Information injection-pump assembly
BOSCH
9 400 617 506
9400617506
ZEXEL
106681-4310
1066814310
NIIGATA-URAWA
74W47090A
74w47090a
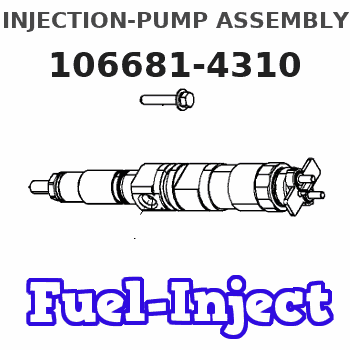
Rating:
Service parts 106681-4310 INJECTION-PUMP ASSEMBLY:
1.
_
7.
COUPLING PLATE
8.
_
9.
_
11.
Nozzle and Holder
74W 3227 1A
12.
Open Pre:MPa(Kqf/cm2)
31.4{320}
15.
NOZZLE SET
Include in #1:
106681-4310
as INJECTION-PUMP ASSEMBLY
Cross reference number
BOSCH
9 400 617 506
9400617506
ZEXEL
106681-4310
1066814310
NIIGATA-URAWA
74W47090A
74w47090a
Zexel num
Bosch num
Firm num
Name
106681-4310
9 400 617 506
74W47090A NIIGATA-URAWA
INJECTION-PUMP ASSEMBLY
6L15CX K
6L15CX K
Calibration Data:
Adjustment conditions
Test oil
1404 Test oil ISO4113 or {SAEJ967d}
1404 Test oil ISO4113 or {SAEJ967d}
Test oil temperature
degC
40
40
45
Nozzle and nozzle holder
105780-8130
Bosch type code
EFEP215A
Nozzle
105780-0050
Bosch type code
DN6TD119NP1T
Nozzle holder
105780-2090
Bosch type code
EFEP215
Opening pressure
MPa
17.2
Opening pressure
kgf/cm2
175
Injection pipe
Outer diameter - inner diameter - length (mm) mm 8-4-1000
Outer diameter - inner diameter - length (mm) mm 8-4-1000
Overflow valve
131425-1620
Overflow valve opening pressure
kPa
255
221
289
Overflow valve opening pressure
kgf/cm2
2.6
2.25
2.95
Tester oil delivery pressure
kPa
157
157
157
Tester oil delivery pressure
kgf/cm2
1.6
1.6
1.6
Direction of rotation (viewed from drive side)
Left L
Left L
Injection timing adjustment
Direction of rotation (viewed from drive side)
Left L
Left L
Injection order
1-4-2-6-
3-5
Pre-stroke
mm
3.5
3.45
3.55
Beginning of injection position
Drive side NO.1
Drive side NO.1
Difference between angles 1
Cal 1-4 deg. 60 59.5 60.5
Cal 1-4 deg. 60 59.5 60.5
Difference between angles 2
Cyl.1-2 deg. 120 119.5 120.5
Cyl.1-2 deg. 120 119.5 120.5
Difference between angles 3
Cal 1-6 deg. 180 179.5 180.5
Cal 1-6 deg. 180 179.5 180.5
Difference between angles 4
Cal 1-3 deg. 240 239.5 240.5
Cal 1-3 deg. 240 239.5 240.5
Difference between angles 5
Cal 1-5 deg. 300 299.5 300.5
Cal 1-5 deg. 300 299.5 300.5
Injection quantity adjustment
Adjusting point
A
Rack position
12.9
Pump speed
r/min
750
750
750
Average injection quantity
mm3/st.
242
237
247
Max. variation between cylinders
%
0
-3
3
Basic
*
Fixing the rack
*
Injection quantity adjustment_02
Adjusting point
B
Rack position
8.8+-0.5
Pump speed
r/min
250
250
250
Average injection quantity
mm3/st.
8
6
10
Max. variation between cylinders
%
0
-10
10
Fixing the rack
*
Injection quantity adjustment_03
Adjusting point
D
Rack position
-
Pump speed
r/min
100
100
100
Average injection quantity
mm3/st.
195
195
215
Fixing the lever
*
Rack limit
*
Timer adjustment
Pump speed
r/min
-
Advance angle
deg.
0
0
0
Remarks
Measure speed (beginning of operation).
Measure speed (beginning of operation).
Timer adjustment_02
Pump speed
r/min
-
Advance angle
deg.
4
3.5
4.5
Remarks
Measure the actual speed, stop
Measure the actual speed, stop
Test data Ex:
Governor adjustment
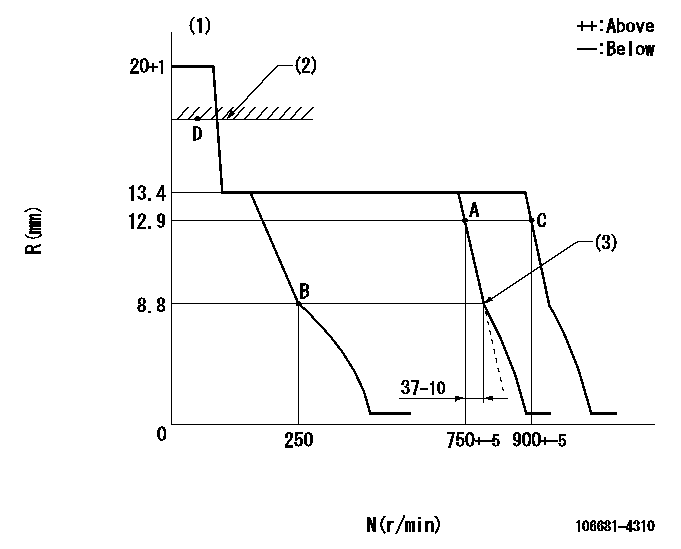
N:Pump speed
R:Rack position (mm)
(1)Target notch: K
(2)RACK LIMIT
(3)Idle sub spring setting: L1.
----------
K=20 L1=8.8-0.5mm
----------
----------
K=20 L1=8.8-0.5mm
----------
Speed control lever angle
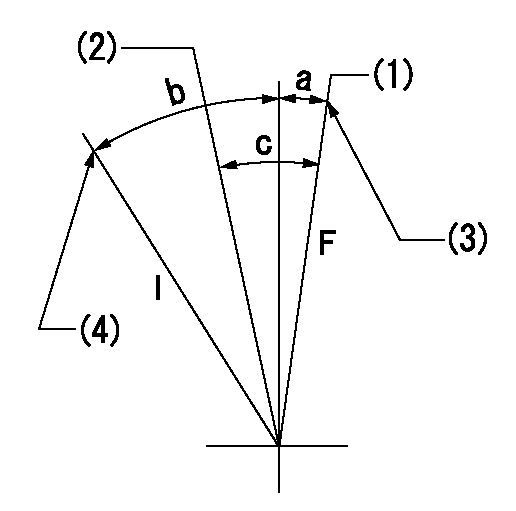
F:Full speed
I:Idle
(1)Set the pump speed at aa
(2)When pump speed set at bb
(3)Stopper bolt setting
(4)Stopper bolt setting
----------
aa=900r/min bb=750r/min
----------
a=2deg+-5deg b=34deg+-5deg c=11deg+-5deg
----------
aa=900r/min bb=750r/min
----------
a=2deg+-5deg b=34deg+-5deg c=11deg+-5deg
Stop lever angle
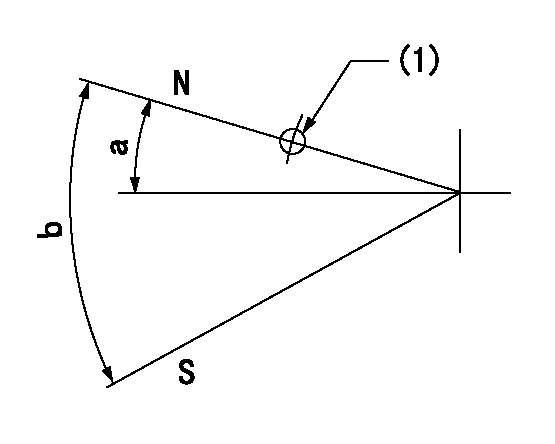
N:Pump normal
S:Stop the pump.
(1)Use the hole at R = aa
----------
aa=17mm
----------
a=27deg+-5deg b=53deg+-5deg
----------
aa=17mm
----------
a=27deg+-5deg b=53deg+-5deg
Timing setting

(1)Pump vertical direction
(2)Coupling's key groove position at No 1 cylinder's beginning of injection
(3)-
(4)-
----------
----------
a=(1deg)
----------
----------
a=(1deg)
Information:
start by:a) remove flywheel 1. Use tool (A) to remove the crankshaft rear seal.2. Install tool (C) in the rear seal bore.
TYPICAL EXAMPLE3. Install tool (B) between tool (C) and the wear sleeve. Turn tool (B) until the ends of the tool make a flat piece (crease) in the wear sleeve. Do this in two or more places until the wear sleeve is loose.4. Remove tool (C) and the wear sleeve by hand.Install Crankshaft Rear Seal And Wear Sleeve
1. Install the crankshaft rear seal and wear sleeve with tooling (A) as follows: a) Put locator (1) in position on the crankshaft and install the three bolts that hold it in place.b) Put clean engine oil on the seal lip of seal (6) and on the outside diameter of wear sleeve (2).c) Install seal (6) on wear sleeve (2) from the end of the wear sleeve that has the bevel on the outside diameter. Make sure the lip of the seal is toward the inside of the engine and the bevel that is on the outside diameter of the wear sleeve is toward the outside of the engine when installed.d) Use 8M8060 Quick Cure Primer to clean the outside diameter of the crankshaft flange (3) and the inside diameter of wear sleeve (2).e) Put 9S3265 Retaining Compound on the outside diameter of crankshaft flange (3) and the inside diameter of wear sleeve (2). Make sure the lip of the seal is toward the inside of the engine and the outside diameter bevel of the wear sleeve is toward the outside of the engine.f) Put wear sleeve (2) with seal (6) on locator (1). Put installer (4) on locator (1) and install nut (5). Put lubrication on the face of the washer and the nut.g) Tighten nut (5) until installer (4) comes in contact with locator (1).h) Remove tooling (A) and check the wear sleeve and seal for correct installation.end by:a) install flywheel
TYPICAL EXAMPLE3. Install tool (B) between tool (C) and the wear sleeve. Turn tool (B) until the ends of the tool make a flat piece (crease) in the wear sleeve. Do this in two or more places until the wear sleeve is loose.4. Remove tool (C) and the wear sleeve by hand.Install Crankshaft Rear Seal And Wear Sleeve
1. Install the crankshaft rear seal and wear sleeve with tooling (A) as follows: a) Put locator (1) in position on the crankshaft and install the three bolts that hold it in place.b) Put clean engine oil on the seal lip of seal (6) and on the outside diameter of wear sleeve (2).c) Install seal (6) on wear sleeve (2) from the end of the wear sleeve that has the bevel on the outside diameter. Make sure the lip of the seal is toward the inside of the engine and the bevel that is on the outside diameter of the wear sleeve is toward the outside of the engine when installed.d) Use 8M8060 Quick Cure Primer to clean the outside diameter of the crankshaft flange (3) and the inside diameter of wear sleeve (2).e) Put 9S3265 Retaining Compound on the outside diameter of crankshaft flange (3) and the inside diameter of wear sleeve (2). Make sure the lip of the seal is toward the inside of the engine and the outside diameter bevel of the wear sleeve is toward the outside of the engine.f) Put wear sleeve (2) with seal (6) on locator (1). Put installer (4) on locator (1) and install nut (5). Put lubrication on the face of the washer and the nut.g) Tighten nut (5) until installer (4) comes in contact with locator (1).h) Remove tooling (A) and check the wear sleeve and seal for correct installation.end by:a) install flywheel
Have questions with 106681-4310?
Group cross 106681-4310 ZEXEL
Mitsubishi-Heav
Niigata-Urawa
106681-4310
9 400 617 506
74W47090A
INJECTION-PUMP ASSEMBLY
6L15CX
6L15CX