Information injection-pump assembly
ZEXEL
106681-4200
1066814200
MITSUBISHI-HEAV
35A6500280
35a6500280
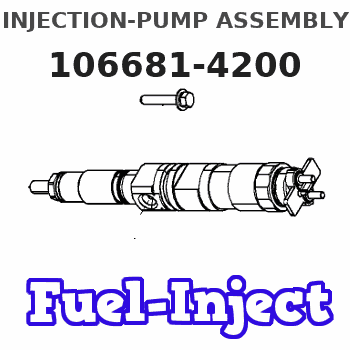
Rating:
Service parts 106681-4200 INJECTION-PUMP ASSEMBLY:
1.
_
8.
_
9.
_
11.
Nozzle and Holder
35A61-00010
12.
Open Pre:MPa(Kqf/cm2)
21.6{220}
15.
NOZZLE SET
Include in #1:
106681-4200
as INJECTION-PUMP ASSEMBLY
Cross reference number
ZEXEL
106681-4200
1066814200
MITSUBISHI-HEAV
35A6500280
35a6500280
Zexel num
Bosch num
Firm num
Name
35A6500280 MITSUBISHI-HEAV
INJECTION-PUMP ASSEMBLY
S6A3 * K 14CA PE6P,6PD PE
S6A3 * K 14CA PE6P,6PD PE
Calibration Data:
Adjustment conditions
Test oil
1404 Test oil ISO4113 or {SAEJ967d}
1404 Test oil ISO4113 or {SAEJ967d}
Test oil temperature
degC
40
40
45
Nozzle and nozzle holder
105780-8130
Bosch type code
EFEP215A
Nozzle
105780-0050
Bosch type code
DN6TD119NP1T
Nozzle holder
105780-2090
Bosch type code
EFEP215
Opening pressure
MPa
17.2
Opening pressure
kgf/cm2
175
Injection pipe
Outer diameter - inner diameter - length (mm) mm 8-4-1000
Outer diameter - inner diameter - length (mm) mm 8-4-1000
Overflow valve
131424-3420
Overflow valve opening pressure
kPa
255
221
289
Overflow valve opening pressure
kgf/cm2
2.6
2.25
2.95
Tester oil delivery pressure
kPa
157
157
157
Tester oil delivery pressure
kgf/cm2
1.6
1.6
1.6
Direction of rotation (viewed from drive side)
Left L
Left L
Injection timing adjustment
Direction of rotation (viewed from drive side)
Left L
Left L
Injection order
1-5-3-6-
2-4
Pre-stroke
mm
2.8
2.75
2.85
Beginning of injection position
Governor side N0.1
Governor side N0.1
Difference between angles 1
Cal 1-5 deg. 60 59.5 60.5
Cal 1-5 deg. 60 59.5 60.5
Difference between angles 2
Cal 1-3 deg. 120 119.5 120.5
Cal 1-3 deg. 120 119.5 120.5
Difference between angles 3
Cal 1-6 deg. 180 179.5 180.5
Cal 1-6 deg. 180 179.5 180.5
Difference between angles 4
Cyl.1-2 deg. 240 239.5 240.5
Cyl.1-2 deg. 240 239.5 240.5
Difference between angles 5
Cal 1-4 deg. 300 299.5 300.5
Cal 1-4 deg. 300 299.5 300.5
Injection quantity adjustment
Adjusting point
A
Rack position
13.9
Pump speed
r/min
900
900
900
Average injection quantity
mm3/st.
503
494
512
Max. variation between cylinders
%
0
-3
3
Basic
*
Fixing the lever
*
Injection quantity adjustment_02
Adjusting point
C
Rack position
5.6+-0.5
Pump speed
r/min
300
300
300
Average injection quantity
mm3/st.
29.5
26.5
32.5
Max. variation between cylinders
%
0
-10
10
Fixing the rack
*
Timer adjustment
Pump speed
r/min
450--
Advance angle
deg.
0
0
0
Remarks
Start
Start
Timer adjustment_02
Pump speed
r/min
400
Advance angle
deg.
0.5
Timer adjustment_03
Pump speed
r/min
700
Advance angle
deg.
4
3.5
4.5
Remarks
Finish
Finish
Test data Ex:
Governor adjustment
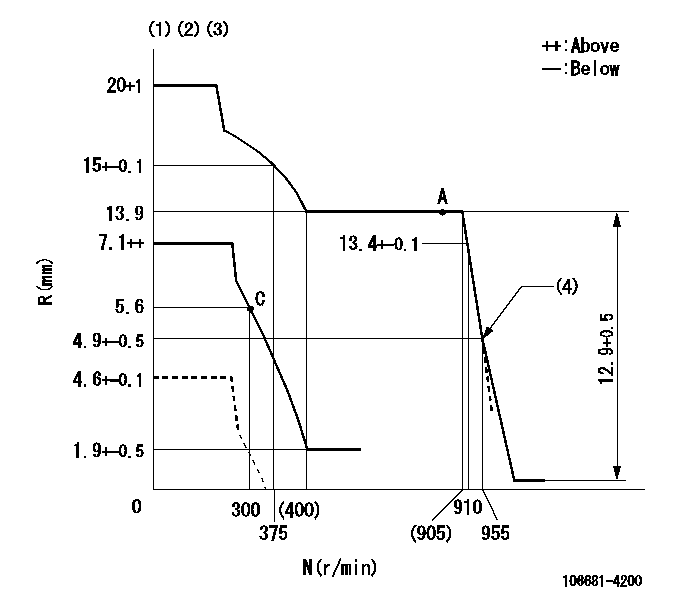
N:Pump speed
R:Rack position (mm)
(1)Maximum - minimum speed specification (using speed lever at adjustment)
(2)Target notch: K
(3)Tolerance for racks not indicated: +-0.05mm.
(4)Idle sub-spring setting: L1
----------
K=13 L1=4.9-0.5mm
----------
----------
K=13 L1=4.9-0.5mm
----------
Speed control lever angle

F:Full speed
S:Stop
(1)At the center of the lever key groove
----------
----------
a=15deg+-5deg b=32deg+-3deg
----------
----------
a=15deg+-5deg b=32deg+-3deg
0000000901
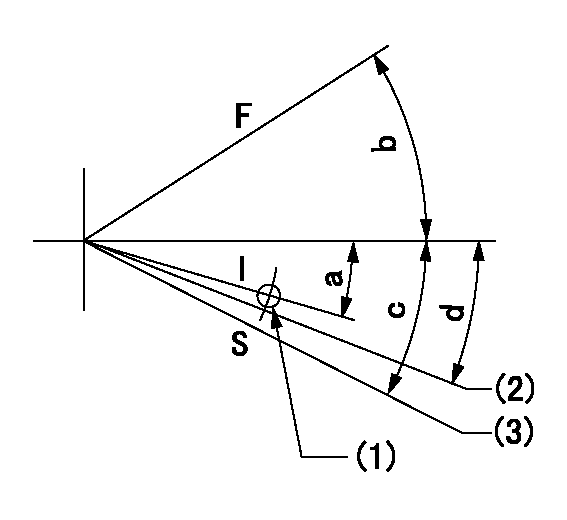
F:Full load
I:Idle
S:Stop
(1)Use the hole at R = aa
(2)Speed = bb, rack position = cc
(3)Stop side boss position
----------
aa=60mm bb=0r/min cc=4.6+-0.1mm
----------
a=8deg+-5deg b=17deg+-5deg c=34deg+-5deg d=(28deg)+-5deg
----------
aa=60mm bb=0r/min cc=4.6+-0.1mm
----------
a=8deg+-5deg b=17deg+-5deg c=34deg+-5deg d=(28deg)+-5deg
Timing setting

(1)Pump vertical direction
(2)Coupling's key groove position at No 1 cylinder's beginning of injection
(3)-
(4)-
----------
----------
a=(20deg)
----------
----------
a=(20deg)
Information:
start by: a) remove valve cover The following steps can be used for the direct injection and precombustion engines except the direct injection engines do not have glow plugs and wires. 1. Remove clip (2) for glow plug wire and fuel injection line (1). Use tool (A) to remove the fuel injection line from the fuel injection valve. 2. Remove fuel line adapters (4) and the spacers from valve cover base (3). Remove the O-ring seal from the adapter.3. Remove bolts (5) and washers (6) that hold rocker shaft assembly (7).4. Remove the rocker shaft assembly. All push rods except those at each end can be removed without removal of the rocker shaft.5. Remove the push rods from the cylinder head.6. Remove intake bridge (9) and exhaust bridge (8) from the bridge dowels. Put identification on the parts to prevent a mix at installation.Install Rocker Shaft Assembly And Push Rods
1. Put clean SAE 30 oil on the bridge dowel and install exhaust bridge (3) and intake bridge (2) in their correct locations.2. Put finger pressure on top of the bridge and turn the adjusting screw clockwise until it makes contact with the valve stem. Turn the adjusting screw 20° to 30° more. Hold the adjusting screw in this position and tighten the locknut to a torque of 22 3 lb.ft. (28 4 N m).3. Put clean SAE 30 oil on top of the pad on the bridge.4. Install push rods (1) and the rocker shaft assembly. Put clean SAE 30 oil on the threads of the bolts that hold the rocker shaft in position. Install the bolts and washers. 5. Tighten the bolts that hold rocker shaft assembly (8) as follows: a) Tighten the bolts in number sequence to a torque of 200 20 lb.ft. (270 25 N m).b) Tighten the bolts again in number sequence to a torque of 330 15 lb.ft. (447 20 N m).c) Tighten the bolts again in number sequence to a torque of 330 15 lb.ft. (447 20 N m).6. Make an adjustment of the correct valve clearances. The clearance must be .015 in. (0.38 mm) for intake and .030 in. (0.76 mm) for exhaust. See VALVE CLEARANCE SETTING in TESTING AND ADJUSTING. 7. Put clean SAE 30 oil on the O-ring seal and install O-ring seal (9) on adapter (10). Install the adapter in valve cover base (11). Install the locks, spacers and nuts that hold it.8. Install the fuel injection line on the adapter and the fuel injection valve. Tighten the nut on the fuel injection valve with tool (A) to a torque of 55 5 lb.ft. (75 7 N m). Tighten the nut on the adapter with tool (A) to a torque of 30 5 lb.ft. (40 7 N m).9. Connect the wire to the glow plug. Connect the clip for the glow plug to the fuel injection line with the wire on the same side as the
1. Put clean SAE 30 oil on the bridge dowel and install exhaust bridge (3) and intake bridge (2) in their correct locations.2. Put finger pressure on top of the bridge and turn the adjusting screw clockwise until it makes contact with the valve stem. Turn the adjusting screw 20° to 30° more. Hold the adjusting screw in this position and tighten the locknut to a torque of 22 3 lb.ft. (28 4 N m).3. Put clean SAE 30 oil on top of the pad on the bridge.4. Install push rods (1) and the rocker shaft assembly. Put clean SAE 30 oil on the threads of the bolts that hold the rocker shaft in position. Install the bolts and washers. 5. Tighten the bolts that hold rocker shaft assembly (8) as follows: a) Tighten the bolts in number sequence to a torque of 200 20 lb.ft. (270 25 N m).b) Tighten the bolts again in number sequence to a torque of 330 15 lb.ft. (447 20 N m).c) Tighten the bolts again in number sequence to a torque of 330 15 lb.ft. (447 20 N m).6. Make an adjustment of the correct valve clearances. The clearance must be .015 in. (0.38 mm) for intake and .030 in. (0.76 mm) for exhaust. See VALVE CLEARANCE SETTING in TESTING AND ADJUSTING. 7. Put clean SAE 30 oil on the O-ring seal and install O-ring seal (9) on adapter (10). Install the adapter in valve cover base (11). Install the locks, spacers and nuts that hold it.8. Install the fuel injection line on the adapter and the fuel injection valve. Tighten the nut on the fuel injection valve with tool (A) to a torque of 55 5 lb.ft. (75 7 N m). Tighten the nut on the adapter with tool (A) to a torque of 30 5 lb.ft. (40 7 N m).9. Connect the wire to the glow plug. Connect the clip for the glow plug to the fuel injection line with the wire on the same side as the