Information injection-pump assembly
BOSCH
9 400 612 668
9400612668
ZEXEL
106681-4101
1066814101
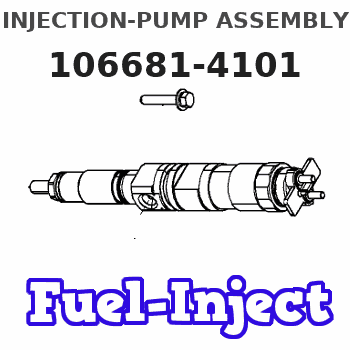
Rating:
Service parts 106681-4101 INJECTION-PUMP ASSEMBLY:
1.
_
7.
COUPLING PLATE
8.
_
9.
_
10.
NOZZLE AND HOLDER ASSY
11.
Nozzle and Holder
12.
Open Pre:MPa(Kqf/cm2)
13.
NOZZLE-HOLDER
14.
NOZZLE
15.
NOZZLE SET
Include in #1:
106681-4101
as INJECTION-PUMP ASSEMBLY
Cross reference number
BOSCH
9 400 612 668
9400612668
ZEXEL
106681-4101
1066814101
Zexel num
Bosch num
Firm num
Name
Calibration Data:
Adjustment conditions
Test oil
1404 Test oil ISO4113 or {SAEJ967d}
1404 Test oil ISO4113 or {SAEJ967d}
Test oil temperature
degC
40
40
45
Nozzle and nozzle holder
105780-8130
Bosch type code
EFEP215A
Nozzle
105780-0050
Bosch type code
DN6TD119NP1T
Nozzle holder
105780-2090
Bosch type code
EFEP215
Opening pressure
MPa
17.2
Opening pressure
kgf/cm2
175
Injection pipe
Outer diameter - inner diameter - length (mm) mm 8-4-1000
Outer diameter - inner diameter - length (mm) mm 8-4-1000
Overflow valve
131424-7120
Overflow valve opening pressure
kPa
255
221
289
Overflow valve opening pressure
kgf/cm2
2.6
2.25
2.95
Tester oil delivery pressure
kPa
157
157
157
Tester oil delivery pressure
kgf/cm2
1.6
1.6
1.6
Direction of rotation (viewed from drive side)
Right R
Right R
Injection timing adjustment
Direction of rotation (viewed from drive side)
Right R
Right R
Injection order
1-4-2-6-
3-5
Pre-stroke
mm
4.1
4.05
4.15
Beginning of injection position
Drive side NO.1
Drive side NO.1
Difference between angles 1
Cal 1-4 deg. 60 59.5 60.5
Cal 1-4 deg. 60 59.5 60.5
Difference between angles 2
Cyl.1-2 deg. 120 119.5 120.5
Cyl.1-2 deg. 120 119.5 120.5
Difference between angles 3
Cal 1-6 deg. 180 179.5 180.5
Cal 1-6 deg. 180 179.5 180.5
Difference between angles 4
Cal 1-3 deg. 240 239.5 240.5
Cal 1-3 deg. 240 239.5 240.5
Difference between angles 5
Cal 1-5 deg. 300 299.5 300.5
Cal 1-5 deg. 300 299.5 300.5
Injection quantity adjustment
Adjusting point
A
Rack position
12.8
Pump speed
r/min
1150
1150
1150
Each cylinder's injection qty
mm3/st.
329
319.1
338.9
Basic
*
Fixing the lever
*
Boost pressure
kPa
93.3
93.3
Boost pressure
mmHg
700
700
Injection quantity adjustment_02
Adjusting point
B
Rack position
5.8+-0.5
Pump speed
r/min
250
250
250
Each cylinder's injection qty
mm3/st.
28.5
25.6
31.4
Fixing the rack
*
Boost pressure
kPa
0
0
0
Boost pressure
mmHg
0
0
0
Injection quantity adjustment_03
Adjusting point
C
Rack position
13.3+0.2
Pump speed
r/min
100
100
100
Average injection quantity
mm3/st.
275
275
335
Fixing the lever
*
Boost pressure
kPa
0
0
0
Boost pressure
mmHg
0
0
0
Rack limit
*
Boost compensator adjustment
Pump speed
r/min
500
500
500
Rack position
R1-1.7
Boost pressure
kPa
40
37.3
42.7
Boost pressure
mmHg
300
280
320
Boost compensator adjustment_02
Pump speed
r/min
500
500
500
Rack position
R1(12.8)
Boost pressure
kPa
80
80
80
Boost pressure
mmHg
600
600
600
Timer adjustment
Pump speed
r/min
400--
Advance angle
deg.
0
0
0
Remarks
Start
Start
Timer adjustment_02
Pump speed
r/min
350
Advance angle
deg.
0.5
Timer adjustment_03
Pump speed
r/min
520
Advance angle
deg.
1
0.7
1.3
Remarks
Finish
Finish
Test data Ex:
Governor adjustment
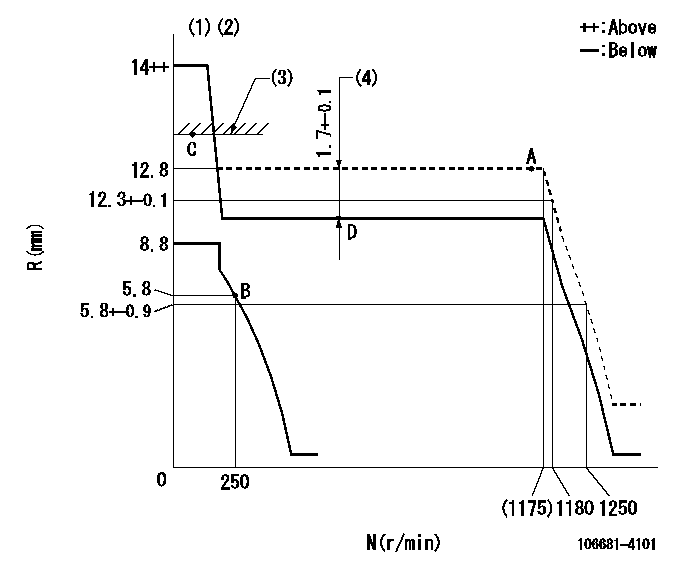
N:Pump speed
R:Rack position (mm)
(1)Target notch: K
(2)Tolerance for racks not indicated: +-0.05mm.
(3)RACK LIMIT: RAL
(4)Boost compensator stroke (at N = N1)
----------
K=6 RAL=13.3+0.2mm N1=500r/min
----------
----------
K=6 RAL=13.3+0.2mm N1=500r/min
----------
Speed control lever angle
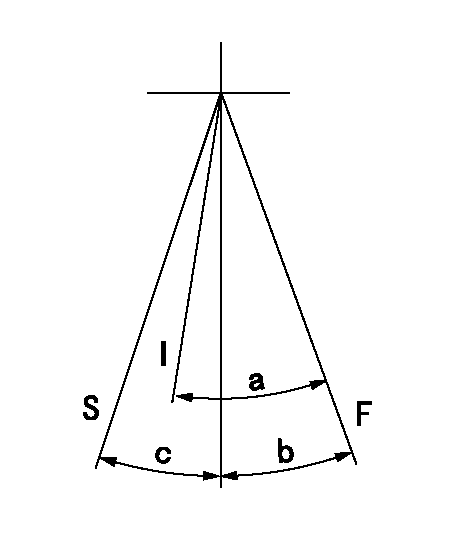
F:Full speed
I:Idle
S:Stop
----------
----------
a=34deg+-5deg b=8deg+-5deg c=35deg+-3deg
----------
----------
a=34deg+-5deg b=8deg+-5deg c=35deg+-3deg
Stop lever angle

N:Pump normal
S:Stop the pump.
(1)Pump speed aa and rack position bb (to be sealed at delivery)
----------
aa=0r/min bb=1-0.2mm
----------
a=25deg+-5deg b=70deg+-5deg
----------
aa=0r/min bb=1-0.2mm
----------
a=25deg+-5deg b=70deg+-5deg
Timing setting
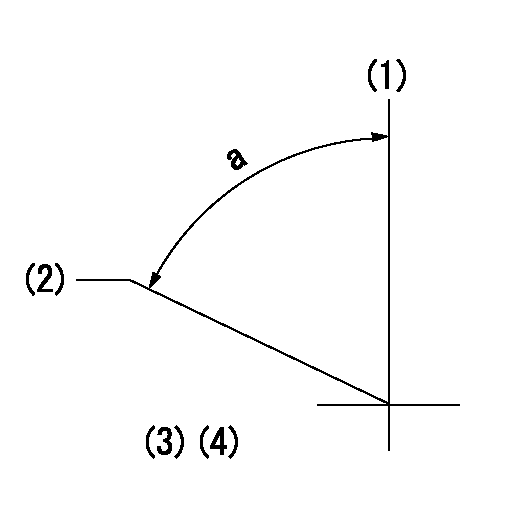
(1)Pump vertical direction
(2)Coupling's key groove position at No 1 cylinder's beginning of injection
(3)-
(4)-
----------
----------
a=(60deg)
----------
----------
a=(60deg)
Information:
(1) Bore in connecting rod for piston pin bearing ... 55.436 0.013 mm (2.1825 .0005 in.)Tight fit between connecting rod eye and piston pin bearing ... 0.05 to 0.10 mm (.002 to .004 in.) Connecting rod must be heated for installation of piston pin bearing. Do not use a torch.Heat connecting rod for piston pin bearing installation to a temperature of ... 177 to 260° C (350 to 500° F)Position of pin bearing:
Positioning Pin Bearing (Type A)Type A (Narrow Taper) - Bearing junction and locating hole are 180° apart (directly across from each other). Bearing junction and locating hole must be assembled within either area "A" (90 10° from centerline through the connecting rod bores) as shown.
Positioning Pin Bearing (Type B)Type B (Wide Taper) - Bearing junction and locating hole are 155° apart (not directly across from each other). Bearing junction and locating holes must be assembled in the top half of connecting rod eye area "A" (12.5 1° above the horizontal centerline) as shown.Make reference to Special Instruction Form No. SMHS7295 for use of pin bearing removal and installation tools and procedures.(2) Bore in connecting rod for bearing with nuts tight to specifications (6) ... 103.500 0.013 mm (4.0748 .0005 in.)(3) Distance between center of bearings ... 261.62 0.05 mm (10.300 .002 in.)(4) Bore in bearing for piston pin (new) ... 50.830 0.008 mm (2.0012 .0003 in.)Diameter of piston pin (new) ... 50.795 0.005 mm (1.9998 .0002 in.)Maximum permissible clearance between bearing and piston pin (worn) ... 0.08 mm (.003 in.)(5) Bore in bearing for crankshaft ... 97.119 to 97.175 mm (3.8236 to 3.8258 in.)Clearance between bearing and crankshaft (new) ... 0.071 to 0.168 mm (.0028 to .0066 in.)Maximum permissible clearance between bearing and crankshaft (worn) ... 0.25 mm (.010 in.) Bearings are available in 0.63 mm (.025 in.) and 1.27 mm (.050 in.) smaller than original size.
Marks For Tightening Connecting Rod Bolts(6) Tightening procedure for connecting rod bolts:a. Put 2P2506 Thread Lubricant on bolt threads and contact surfaces of nut and cap.b. Tighten both nuts to ... 80 8 N m (60 6 lb.ft.)c. Put a mark on each nut and end of bolt as shown.d. Tighten each nut from mark ... 120 5° The connecting rod must be installed so the chamfer on the edge of bore (5) is near the corner on the crankshaft. The side opposite the chamfered edge must be against the other connecting rod on the same crankshaft pin.Side clearance between two connecting rods on the same crankshaft pin (new) ... 0.28 to 0.84 mm (.011 to .033 in.)Make reference to Special Instruction Form Nos. GMG02394 & SMHS7366 for information to check and recondition connecting rods. Also see, Guideline For Reusable Parts; Salvage Of Non-Serrated Connecting Rods, Form No. SEBF8064.
Positioning Pin Bearing (Type A)Type A (Narrow Taper) - Bearing junction and locating hole are 180° apart (directly across from each other). Bearing junction and locating hole must be assembled within either area "A" (90 10° from centerline through the connecting rod bores) as shown.
Positioning Pin Bearing (Type B)Type B (Wide Taper) - Bearing junction and locating hole are 155° apart (not directly across from each other). Bearing junction and locating holes must be assembled in the top half of connecting rod eye area "A" (12.5 1° above the horizontal centerline) as shown.Make reference to Special Instruction Form No. SMHS7295 for use of pin bearing removal and installation tools and procedures.(2) Bore in connecting rod for bearing with nuts tight to specifications (6) ... 103.500 0.013 mm (4.0748 .0005 in.)(3) Distance between center of bearings ... 261.62 0.05 mm (10.300 .002 in.)(4) Bore in bearing for piston pin (new) ... 50.830 0.008 mm (2.0012 .0003 in.)Diameter of piston pin (new) ... 50.795 0.005 mm (1.9998 .0002 in.)Maximum permissible clearance between bearing and piston pin (worn) ... 0.08 mm (.003 in.)(5) Bore in bearing for crankshaft ... 97.119 to 97.175 mm (3.8236 to 3.8258 in.)Clearance between bearing and crankshaft (new) ... 0.071 to 0.168 mm (.0028 to .0066 in.)Maximum permissible clearance between bearing and crankshaft (worn) ... 0.25 mm (.010 in.) Bearings are available in 0.63 mm (.025 in.) and 1.27 mm (.050 in.) smaller than original size.
Marks For Tightening Connecting Rod Bolts(6) Tightening procedure for connecting rod bolts:a. Put 2P2506 Thread Lubricant on bolt threads and contact surfaces of nut and cap.b. Tighten both nuts to ... 80 8 N m (60 6 lb.ft.)c. Put a mark on each nut and end of bolt as shown.d. Tighten each nut from mark ... 120 5° The connecting rod must be installed so the chamfer on the edge of bore (5) is near the corner on the crankshaft. The side opposite the chamfered edge must be against the other connecting rod on the same crankshaft pin.Side clearance between two connecting rods on the same crankshaft pin (new) ... 0.28 to 0.84 mm (.011 to .033 in.)Make reference to Special Instruction Form Nos. GMG02394 & SMHS7366 for information to check and recondition connecting rods. Also see, Guideline For Reusable Parts; Salvage Of Non-Serrated Connecting Rods, Form No. SEBF8064.