Information injection-pump assembly
ZEXEL
106676-2800
1066762800
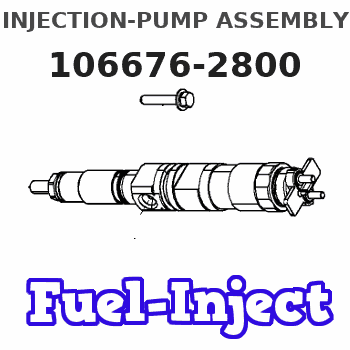
Rating:
Cross reference number
ZEXEL
106676-2800
1066762800
Zexel num
Bosch num
Firm num
Name
106676-2800
INJECTION-PUMP ASSEMBLY
Calibration Data:
Adjustment conditions
Test oil
1404 Test oil ISO4113 or {SAEJ967d}
1404 Test oil ISO4113 or {SAEJ967d}
Test oil temperature
degC
40
40
45
Nozzle and nozzle holder
105780-8140
Bosch type code
EF8511/9A
Nozzle
105780-0000
Bosch type code
DN12SD12T
Nozzle holder
105780-2080
Bosch type code
EF8511/9
Opening pressure
MPa
17.2
Opening pressure
kgf/cm2
175
Injection pipe
Outer diameter - inner diameter - length (mm) mm 8-3-600
Outer diameter - inner diameter - length (mm) mm 8-3-600
Overflow valve
131424-4420
Overflow valve opening pressure
kPa
157
123
191
Overflow valve opening pressure
kgf/cm2
1.6
1.25
1.95
Tester oil delivery pressure
kPa
157
157
157
Tester oil delivery pressure
kgf/cm2
1.6
1.6
1.6
Direction of rotation (viewed from drive side)
Right R
Right R
Injection timing adjustment
Direction of rotation (viewed from drive side)
Right R
Right R
Injection order
1-5-3-6-
2-4
Pre-stroke
mm
3.9
3.85
3.95
Beginning of injection position
Governor side NO.1
Governor side NO.1
Difference between angles 1
Cal 1-5 deg. 60 59.5 60.5
Cal 1-5 deg. 60 59.5 60.5
Difference between angles 2
Cal 1-3 deg. 120 119.5 120.5
Cal 1-3 deg. 120 119.5 120.5
Difference between angles 3
Cal 1-6 deg. 180 179.5 180.5
Cal 1-6 deg. 180 179.5 180.5
Difference between angles 4
Cyl.1-2 deg. 240 239.5 240.5
Cyl.1-2 deg. 240 239.5 240.5
Difference between angles 5
Cal 1-4 deg. 300 299.5 300.5
Cal 1-4 deg. 300 299.5 300.5
Injection quantity adjustment
Adjusting point
A
Rack position
14
Pump speed
r/min
1000
1000
1000
Average injection quantity
mm3/st.
164
161
167
Max. variation between cylinders
%
0
-3
3
Basic
*
Fixing the lever
*
Boost pressure
kPa
30
30
Boost pressure
mmHg
225
225
Injection quantity adjustment_02
Adjusting point
-
Rack position
9.9+-0.5
Pump speed
r/min
400
400
400
Average injection quantity
mm3/st.
16
13.4
18.6
Max. variation between cylinders
%
0
-15
15
Fixing the rack
*
Boost pressure
kPa
0
0
0
Boost pressure
mmHg
0
0
0
Remarks
Adjust only variation between cylinders; adjust governor according to governor specifications.
Adjust only variation between cylinders; adjust governor according to governor specifications.
Boost compensator adjustment
Pump speed
r/min
900
900
900
Rack position
R1-1.2
Boost pressure
kPa
5.3
4
6.6
Boost pressure
mmHg
40
30
50
Boost compensator adjustment_02
Pump speed
r/min
900
900
900
Rack position
R1(14)
Boost pressure
kPa
16.7
10
23.4
Boost pressure
mmHg
125
75
175
Test data Ex:
Governor adjustment
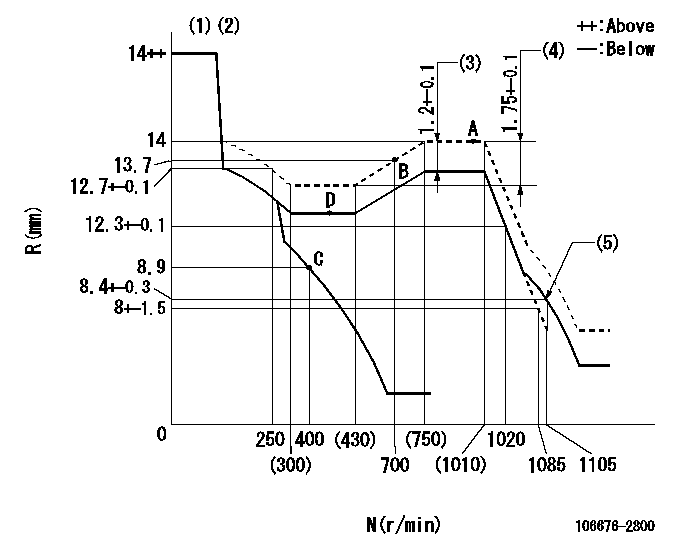
N:Pump speed
R:Rack position (mm)
(1)Notch fixed: K
(2)Tolerance for racks not indicated: +-0.05mm.
(3)Boost compensator stroke
(4)Rack difference between N = N1 and N = N2
(5)Set idle sub-spring
----------
K=10 N1=1000r/min N2=400r/min
----------
----------
K=10 N1=1000r/min N2=400r/min
----------
Timer adjustment

(1)Adjusting range
(2)Step response time
(N): Speed of the pump
(L): Load
(theta) Advance angle
(Srd1) Step response time 1
(Srd2) Step response time 2
1. Adjusting conditions for the variable timer
(1)Adjust the clearance between the pickup and the protrusion to L.
----------
L=1.5-0.2mm N2=800r/min C2=(10deg) t1=2.5--sec. t2=2.5--sec.
----------
N1=750++r/min P1=0kPa(0kgf/cm2) P2=392kPa(4kgf/cm2) C1=10+-0.3deg R01=0/4 load R02=4/4 load
----------
L=1.5-0.2mm N2=800r/min C2=(10deg) t1=2.5--sec. t2=2.5--sec.
----------
N1=750++r/min P1=0kPa(0kgf/cm2) P2=392kPa(4kgf/cm2) C1=10+-0.3deg R01=0/4 load R02=4/4 load
Speed control lever angle
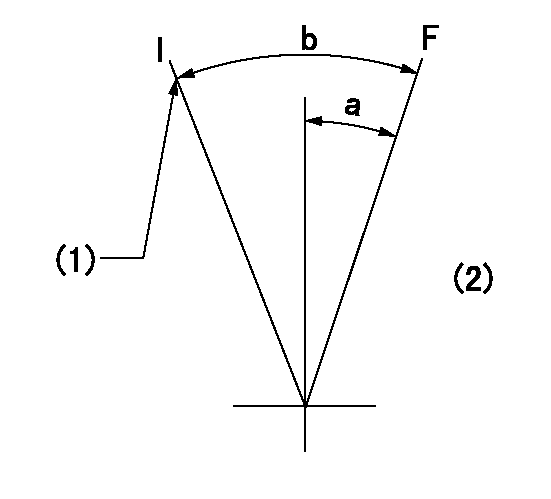
F:Full speed
I:Idle
(1)Stopper bolt setting
(2)Base lever only
----------
----------
a=(1.5deg)+-5deg b=(17deg)+-5deg
----------
----------
a=(1.5deg)+-5deg b=(17deg)+-5deg
Stop lever angle
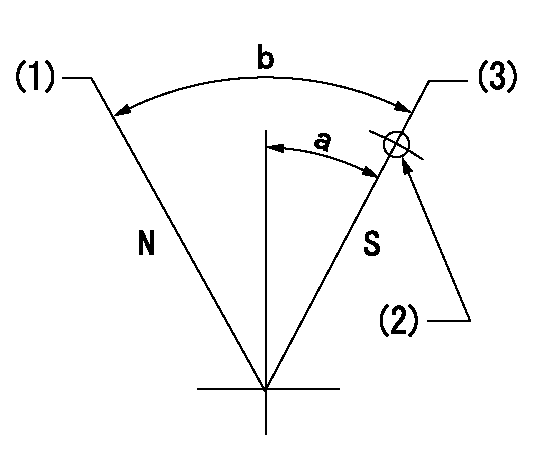
N:Pump normal
S:Stop the pump.
(1)Normal
(2)Use the hole at R = aa
(3)Rack position bb, pump speed cc (seal at delivery)
----------
aa=17mm bb=1-0.5mm cc=0r/min
----------
a=35deg+-5deg b=70deg+-5deg
----------
aa=17mm bb=1-0.5mm cc=0r/min
----------
a=35deg+-5deg b=70deg+-5deg
0000001501 RACK SENSOR
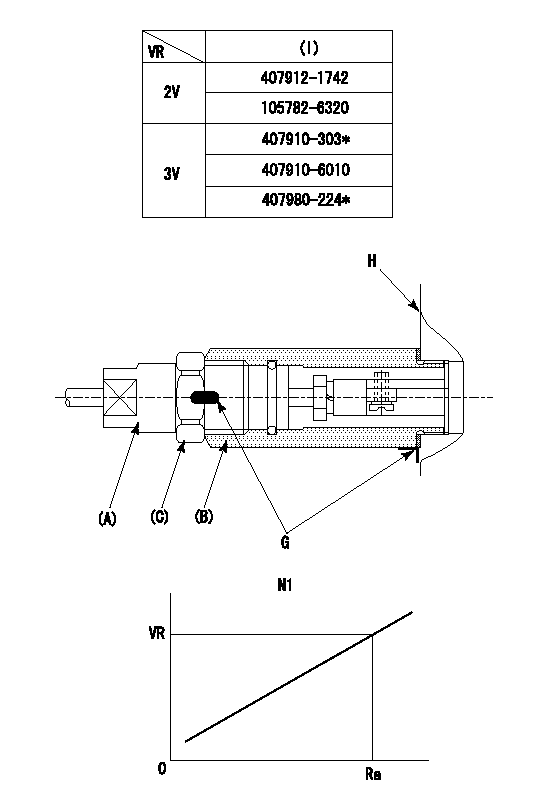
(VR) measurement voltage
(I) Part number of the control unit
(G) Apply red paint.
(H): End surface of the pump
1. Rack sensor adjustment (-0620)
(1)Fix the speed control lever at the full position
(2)Set the speed to N1 r/min.
(If the boost compensator is provided, apply boost pressure.)
(3)Adjust the bobbin (A) so that the rack sensor's output voltage is VR+-0.01.
(4)At that time, rack position must be Ra.
(5)Apply G at two places.
Connecting part between the joint (B) and the nut (F)
Connecting part between the joint (B) and the end surface of the pump (H)
----------
N1=1000r/min Ra=14mm
----------
----------
N1=1000r/min Ra=14mm
----------
0000001601 TAMPER PROOF

Tamperproofing-equipped boost compensator cover installation procedure
(A) After adjusting the boost compensator, tighten the bolts to remove the heads.
(1)Before adjusting the governor and the boost compensator, tighten the screw to the specified torque.
(Tightening torque T = T1 maximum)
(2)After adjusting the governor and the boost compensator, tighten to the specified torque to break off the bolt heads.
(Tightening torque T = T2 maximum)
----------
T1=2.5N-m(0.25kgf-m) T2=2.9~4.4N-m(0.3~0.45kgf-m)
----------
----------
T1=2.5N-m(0.25kgf-m) T2=2.9~4.4N-m(0.3~0.45kgf-m)
----------
Timing setting

(1)Pump vertical direction
(2)Coupling's key groove position at No 1 cylinder's beginning of injection
(3)B.T.D.C.: aa
(4)-
----------
aa=5deg
----------
a=(2deg)
----------
aa=5deg
----------
a=(2deg)
Information:
Introduction
The problem that is identified below does not have a known permanent solution. Until a permanent solution is known, use the solution that is identified below.Problem
Certain F2 series machines installed with Tier II or Tier III engines have reported low power from the engine. After troubleshooting, this low power has been diagnosed as being a faulty fuel injection pump.
Table 1
Required Parts
Part Number Part Name
10R-9707 Fuel Injection Pump Gp
10R-9715 Fuel Injection Pump Gp
20R-4832 Fuel Injection Pump Gp
236-8228 Fuel Injection Pump Gp
237-5213 Fuel Injection Pump Gp
248-2356 Fuel Injection Pump Gp
249-9226 Fuel Injection Pump Gp
266-3712 Fuel Injection Pump Gp
274-4962 Fuel Injection Pump Gp
326-8993 Fuel Injection Pump Gp
326-9147 Fuel Injection Pump Gp
368-5413 Fuel Injection Pump Gp
501-4461 Fuel Priming Pump and Primary Filter Gp Replace failed part with new part for your machine.Solution
Before replacing the fuel injection pump, the following actions can be performed to help ensure that the low-pressure fuel system is in good condition.
There is fuel in the fuel tank
Inspect the fuel filter for excess contamination, if necessary, install a new fuel filter
Check the fuel strainer in the bottom of the fuel tank is not blocked or damaged
Check that the fuel lift pump is delivering fuel to the fuel injection pump.
Check that the fuel tank has been regularly drained of any water contamination, and is clear of any debris that could be restricting the fuel flow. See the Operation and Maintenance Manual for correct maintenance practices.All these issues can cause low fuel pressure problems that could lead to thinking the fuel injection pump is faulty. If the low-pressure fuel system is working correctly, then inspect the fuel injection pump for water damage. Refer to special instruction REHS3767. If the fuel injection pump contains rust, then the root cause of the problem is water in the fuel supply.If necessary, a replacement fuel injection pump may be obtained. Refer to disassembly and assembly, "Fuel Injection Pump - Install" for the correct procedure to install a replacement fuel injection pump.Ensure that the fuel supply is clean and the fuel tank does not contain any water or contamination before installing a new Fuel Injection Pump. Also, replace the fuel filter. If a failure occurs, report the failure to the product group by completing a CPI Feedback Form at the Service Information Management System (SIMSi). Reference CPI 373959 and TIB , M0082583 in the form. The link to SIMSi can be found on the Caterpillar Service Information System (SIS).Note: For machines equipped with 501-4461 Fuel Priming Pump and Primary Filter Gp which has an extra water separation volume. Itis recommended to remove any aftermarket water separator.
The problem that is identified below does not have a known permanent solution. Until a permanent solution is known, use the solution that is identified below.Problem
Certain F2 series machines installed with Tier II or Tier III engines have reported low power from the engine. After troubleshooting, this low power has been diagnosed as being a faulty fuel injection pump.
Table 1
Required Parts
Part Number Part Name
10R-9707 Fuel Injection Pump Gp
10R-9715 Fuel Injection Pump Gp
20R-4832 Fuel Injection Pump Gp
236-8228 Fuel Injection Pump Gp
237-5213 Fuel Injection Pump Gp
248-2356 Fuel Injection Pump Gp
249-9226 Fuel Injection Pump Gp
266-3712 Fuel Injection Pump Gp
274-4962 Fuel Injection Pump Gp
326-8993 Fuel Injection Pump Gp
326-9147 Fuel Injection Pump Gp
368-5413 Fuel Injection Pump Gp
501-4461 Fuel Priming Pump and Primary Filter Gp Replace failed part with new part for your machine.Solution
Before replacing the fuel injection pump, the following actions can be performed to help ensure that the low-pressure fuel system is in good condition.
There is fuel in the fuel tank
Inspect the fuel filter for excess contamination, if necessary, install a new fuel filter
Check the fuel strainer in the bottom of the fuel tank is not blocked or damaged
Check that the fuel lift pump is delivering fuel to the fuel injection pump.
Check that the fuel tank has been regularly drained of any water contamination, and is clear of any debris that could be restricting the fuel flow. See the Operation and Maintenance Manual for correct maintenance practices.All these issues can cause low fuel pressure problems that could lead to thinking the fuel injection pump is faulty. If the low-pressure fuel system is working correctly, then inspect the fuel injection pump for water damage. Refer to special instruction REHS3767. If the fuel injection pump contains rust, then the root cause of the problem is water in the fuel supply.If necessary, a replacement fuel injection pump may be obtained. Refer to disassembly and assembly, "Fuel Injection Pump - Install" for the correct procedure to install a replacement fuel injection pump.Ensure that the fuel supply is clean and the fuel tank does not contain any water or contamination before installing a new Fuel Injection Pump. Also, replace the fuel filter. If a failure occurs, report the failure to the product group by completing a CPI Feedback Form at the Service Information Management System (SIMSi). Reference CPI 373959 and TIB , M0082583 in the form. The link to SIMSi can be found on the Caterpillar Service Information System (SIS).Note: For machines equipped with 501-4461 Fuel Priming Pump and Primary Filter Gp which has an extra water separation volume. Itis recommended to remove any aftermarket water separator.
Have questions with 106676-2800?
Group cross 106676-2800 ZEXEL
106676-2800
INJECTION-PUMP ASSEMBLY