Information injection-pump assembly
ZEXEL
106676-2321
1066762321
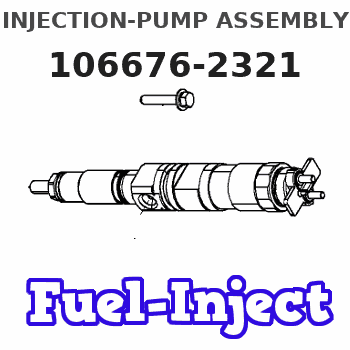
Rating:
Service parts 106676-2321 INJECTION-PUMP ASSEMBLY:
1.
_
7.
COUPLING PLATE
8.
_
9.
_
11.
Nozzle and Holder
ME158263
12.
Open Pre:MPa(Kqf/cm2)
17.7{180}/21.6{220}
14.
NOZZLE
Include in #1:
106676-2321
as INJECTION-PUMP ASSEMBLY
Cross reference number
ZEXEL
106676-2321
1066762321
Zexel num
Bosch num
Firm num
Name
106676-2321
INJECTION-PUMP ASSEMBLY
Calibration Data:
Adjustment conditions
Test oil
1404 Test oil ISO4113 or {SAEJ967d}
1404 Test oil ISO4113 or {SAEJ967d}
Test oil temperature
degC
40
40
45
Nozzle and nozzle holder
105780-8140
Bosch type code
EF8511/9A
Nozzle
105780-0000
Bosch type code
DN12SD12T
Nozzle holder
105780-2080
Bosch type code
EF8511/9
Opening pressure
MPa
17.2
Opening pressure
kgf/cm2
175
Injection pipe
Outer diameter - inner diameter - length (mm) mm 8-3-600
Outer diameter - inner diameter - length (mm) mm 8-3-600
Overflow valve
131424-4620
Overflow valve opening pressure
kPa
255
221
289
Overflow valve opening pressure
kgf/cm2
2.6
2.25
2.95
Tester oil delivery pressure
kPa
157
157
157
Tester oil delivery pressure
kgf/cm2
1.6
1.6
1.6
Direction of rotation (viewed from drive side)
Right R
Right R
Injection timing adjustment
Direction of rotation (viewed from drive side)
Right R
Right R
Injection order
1-5-3-6-
2-4
Pre-stroke
mm
4.8
4.75
4.85
Beginning of injection position
Governor side NO.1
Governor side NO.1
Difference between angles 1
Cal 1-5 deg. 60 59.5 60.5
Cal 1-5 deg. 60 59.5 60.5
Difference between angles 2
Cal 1-3 deg. 120 119.5 120.5
Cal 1-3 deg. 120 119.5 120.5
Difference between angles 3
Cal 1-6 deg. 180 179.5 180.5
Cal 1-6 deg. 180 179.5 180.5
Difference between angles 4
Cyl.1-2 deg. 240 239.5 240.5
Cyl.1-2 deg. 240 239.5 240.5
Difference between angles 5
Cal 1-4 deg. 300 299.5 300.5
Cal 1-4 deg. 300 299.5 300.5
Injection quantity adjustment
Adjusting point
A
Rack position
8.9
Pump speed
r/min
1000
1000
1000
Average injection quantity
mm3/st.
123
120
126
Max. variation between cylinders
%
0
-3
3
Basic
*
Fixing the lever
*
Boost pressure
kPa
30.7
30.7
Boost pressure
mmHg
230
230
Injection quantity adjustment_02
Adjusting point
B
Rack position
4.4+-0.5
Pump speed
r/min
425
425
425
Average injection quantity
mm3/st.
9.5
6.9
12.1
Max. variation between cylinders
%
0
-15
15
Fixing the rack
*
Boost pressure
kPa
0
0
0
Boost pressure
mmHg
0
0
0
Injection quantity adjustment_03
Adjusting point
D
Rack position
-
Pump speed
r/min
100
100
100
Average injection quantity
mm3/st.
145
125
165
Fixing the lever
*
Boost pressure
kPa
0
0
0
Boost pressure
mmHg
0
0
0
Rack limit
*
Boost compensator adjustment
Pump speed
r/min
700
700
700
Rack position
R1-1.25
Boost pressure
kPa
4
2.7
5.3
Boost pressure
mmHg
30
20
40
Boost compensator adjustment_02
Pump speed
r/min
700
700
700
Rack position
R1(8.9)
Boost pressure
kPa
17.3
10.6
24
Boost pressure
mmHg
130
80
180
Timer adjustment
Pump speed
r/min
0
Advance angle
deg.
2.5
2
3
Timer adjustment_02
Pump speed
r/min
300
Advance angle
deg.
2.5
2
3
Remarks
Start
Start
Timer adjustment_03
Pump speed
r/min
-
Advance angle
deg.
0
0
0
Remarks
Measure the actual speed, stop
Measure the actual speed, stop
Test data Ex:
Governor adjustment
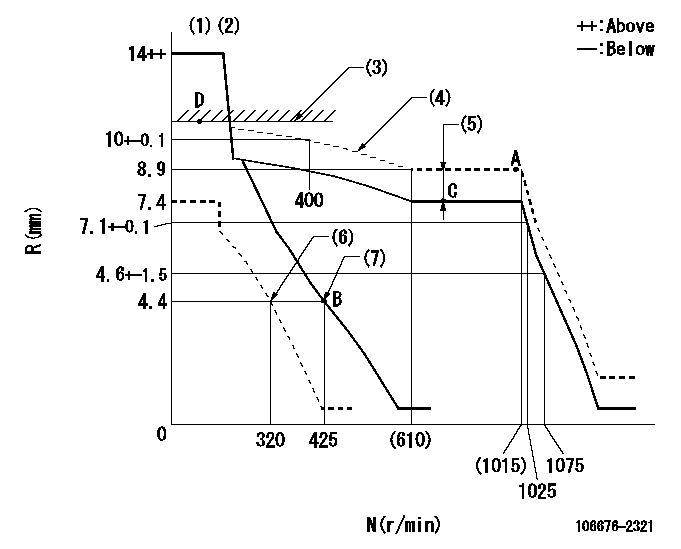
N:Pump speed
R:Rack position (mm)
(1)Notch fixed: K
(2)Tolerance for racks not indicated: +-0.05mm.
(3)RACK LIMIT
(4)The torque control spring must does not have a set force.
(5)Boost compensator stroke: BCL
(6)Set idle sub-spring
(7)Main spring setting
----------
K=8 BCL=1.25+-0.1mm
----------
----------
K=8 BCL=1.25+-0.1mm
----------
Speed control lever angle

F:Full speed
I:Idle
(1)Stopper bolt setting
----------
----------
a=(21deg)+-5deg b=(0deg)+-5deg
----------
----------
a=(21deg)+-5deg b=(0deg)+-5deg
Stop lever angle

N:Pump normal
S:Stop the pump.
(1)Normal
(2)Pump speed = aa and rack position = bb, set the stopper bolt (to be sealed at delivery).
----------
aa=0r/min bb=1-0.5mm
----------
a=35deg+-5deg b=70deg+-5deg
----------
aa=0r/min bb=1-0.5mm
----------
a=35deg+-5deg b=70deg+-5deg
0000001501 TAMPER PROOF

Tamperproofing-equipped boost compensator cover installation procedure
(A) After adjusting the boost compensator, tighten the bolts to remove the heads.
(1)Before adjusting the governor and the boost compensator, tighten the screw to the specified torque.
(Tightening torque T = T1 maximum)
(2)After adjusting the governor and the boost compensator, tighten to the specified torque to break off the bolt heads.
(Tightening torque T = T2)
----------
T1=2.5N-m(0.25kgf-m) T2=2.9~4.4N-m(0.3~0.45kgf-m)
----------
----------
T1=2.5N-m(0.25kgf-m) T2=2.9~4.4N-m(0.3~0.45kgf-m)
----------
Timing setting

(1)Pump vertical direction
(2)Coupling's key groove position at No 1 cylinder's beginning of injection
(3)B.T.D.C.: aa
(4)-
----------
aa=12deg
----------
a=(6deg)
----------
aa=12deg
----------
a=(6deg)
Information:
Image1.1.2
2. Remove existing 215-2705 cap (Image 1.2.1), and replace with new 272-7102 cap, utilizing the existing cap screws (Image 1.2.1). Insure that threads are coated with Thread Lock P/N 9S-3263 or 4C-4030 and torque cap screws to 7(+/-1) Nm.
Image1.2.1
3. Install new 263-2905 switches (Image 1.3.1) into caps insuring that threads are coated with P/N 4C-5598 High temperature Anti-Seize and torque to 16(+/-2) Nm
Image1.3.1
4. Connect new switch to the applicable wiring harness. Install ladder clips as shown (Image 1.4.1), using 0S-1588 Bolts coated with P/N 4C-5598 High Temperature Anti-Seize to replace the top two existing bolts as shown. Torque these bolts to 47 (+/-9) Nm.
Image1.4.1
Image1.4.2
5. IMPORTANT - Tie-wrap new switch wiring to existing solenoid wiring as shown (Images 1.4.1 & 1.4.2), to prevent thermal damage to wiring.
6. Install information films P/N 179-0133 on electrically actuated Air Shut Offs over the existing films on the solenoids as shown in (Image 1.6.1) or install information films for hydraulically actuated Air Shut Offs over the existing films on the valve covers as shown in (Image 1.6.2).
Films in languages other than English are available under the following part numbers:
-Arabic 297-2613
-French 297-2614
-German 297-2615
-Spanish 297-2616
-Portuguese 297-2617
-Russian 297-2618
Image1.6.1
Image1.6.2
Important Notes:
1. If a new switch is to be painted, mask the vent holes around the perimeter of the switch before painting and be sure to remove the masking after the paint dries.
2. Test completed modifications as detailed below for the specific ECM installed on the engine (ADEM 2 or ADEM 3).
OPERATIONAL TEST - ADEM 2 Engine Control Modules ONLY
Note: (For Troubleshooting purposes) The ASO switches are normally closed switches that are in the closed state when the air shutoff valves are latched in the open ("Run") position. If the air shutoff valves are in the closed ("Stop") position, the switch will be in the open state, causing an emergency stop and shutting the engine down. This also prevents the engine from starting.
DO NOT START THE ENGINE! Ensure that the engine control is in the "OFF" position.
1. Ensure that both air shutoff gates are latched in the OPEN position and ensure that both air shutoff switches are connected. Turn on the power to the engine control panel. Both air shutoff gates should remain open. If both air shutoff gates do not remain open, check the wiring for the air shutoff switches.
2. With the power for the engine control panel in the ON position, activate the "EMERGENCY STOP" switch. Both of the air shutoff gates should close. If both air shutoff gates close, proceed to step 3. If both air shutoff gates do not close, check the wiring for the air shutoff switches and check the wiring for the solenoids. Activate the "EMERGENCY STOP" switch again. When both air shutoff gates close, proceed to step 3.
3. Turn the power to the engine control panel to the OFF position. Ensure that the "EMERGENCY STOP" switch is in the RUN position. Latch only the right side air shutoff gate to the OPEN position. Turn the power for the engine control panel to
Have questions with 106676-2321?
Group cross 106676-2321 ZEXEL
Mitsubishi
106676-2321
INJECTION-PUMP ASSEMBLY