Information injection-pump assembly
ZEXEL
106675-4731
1066754731
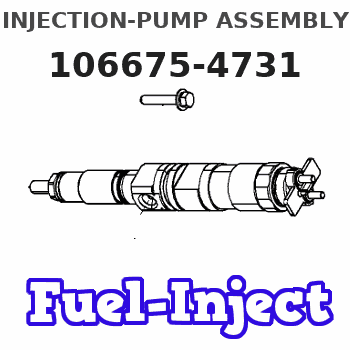
Rating:
Cross reference number
ZEXEL
106675-4731
1066754731
Zexel num
Bosch num
Firm num
Name
106675-4731
INJECTION-PUMP ASSEMBLY
Calibration Data:
Adjustment conditions
Test oil
1404 Test oil ISO4113 or {SAEJ967d}
1404 Test oil ISO4113 or {SAEJ967d}
Test oil temperature
degC
40
40
45
Nozzle and nozzle holder
105780-8130
Bosch type code
EFEP215A
Nozzle
105780-0050
Bosch type code
DN6TD119NP1T
Nozzle holder
105780-2090
Bosch type code
EFEP215
Opening pressure
MPa
17.2
Opening pressure
kgf/cm2
175
Injection pipe
Outer diameter - inner diameter - length (mm) mm 8-3-600
Outer diameter - inner diameter - length (mm) mm 8-3-600
Overflow valve
131425-1620
Overflow valve opening pressure
kPa
255
221
289
Overflow valve opening pressure
kgf/cm2
2.6
2.25
2.95
Tester oil delivery pressure
kPa
157
157
157
Tester oil delivery pressure
kgf/cm2
1.6
1.6
1.6
RED3 control unit part number
407910-3
960
RED3 rack sensor specifications
mm
19
Direction of rotation (viewed from drive side)
Right R
Right R
Injection timing adjustment
Direction of rotation (viewed from drive side)
Right R
Right R
Injection order
1-5-3-6-
2-4
Pre-stroke
mm
3.9
3.85
3.95
Beginning of injection position
Drive side NO.1
Drive side NO.1
Difference between angles 1
Cal 1-5 deg. 60 59.5 60.5
Cal 1-5 deg. 60 59.5 60.5
Difference between angles 2
Cal 1-3 deg. 120 119.5 120.5
Cal 1-3 deg. 120 119.5 120.5
Difference between angles 3
Cal 1-6 deg. 180 179.5 180.5
Cal 1-6 deg. 180 179.5 180.5
Difference between angles 4
Cyl.1-2 deg. 240 239.5 240.5
Cyl.1-2 deg. 240 239.5 240.5
Difference between angles 5
Cal 1-4 deg. 300 299.5 300.5
Cal 1-4 deg. 300 299.5 300.5
Injection quantity adjustment
Rack position
(13.5)
Vist
V
1.82
1.82
1.82
Pump speed
r/min
900
900
900
Average injection quantity
mm3/st.
326
322
330
Max. variation between cylinders
%
0
-3
3
Basic
*
Injection quantity adjustment_02
Rack position
(6.9)
Vist
V
2.8
2.7
2.9
Pump speed
r/min
410
410
410
Average injection quantity
mm3/st.
17
15.5
18.5
Max. variation between cylinders
%
0
-15
15
Test data Ex:
Speed control lever angle

N:Pump normal
S:Stop the pump.
(1)Rack position = aa
(2)Rack position bb
----------
aa=20mm bb=1mm
----------
a=27deg+-5deg b=37deg+-5deg
----------
aa=20mm bb=1mm
----------
a=27deg+-5deg b=37deg+-5deg
0000000901
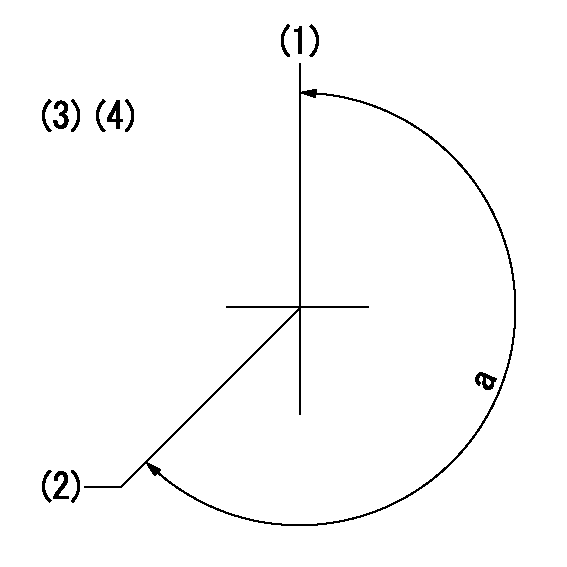
(1)Pump vertical direction
(2)Coupling's key groove position at No 1 cylinder's beginning of injection
(3)-
(4)-
----------
----------
a=(260deg)
----------
----------
a=(260deg)
Stop lever angle
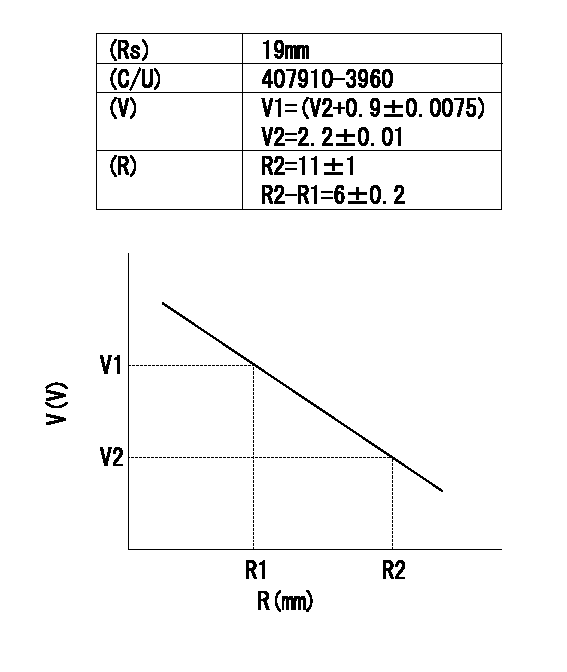
(Rs) rack sensor specifications
(C/U) control unit part number
(V) Rack sensor output voltage
(R) Rack position (mm)
1. Confirming governor output characteristics (rack 19 mm, span 6 mm)
(1)When the output voltages of the rack sensor are V1 and V2, check that the rack positions R1 and R2 in the table above are satisfied.
----------
----------
----------
----------
Information:
PRIMARY FUEL FILTERFINAL FUEL FILTER ELEMENT: The filter element collects and holds contaminants and cannot be washed or otherwise restored. To remove the used filter element, proceed as follows:1. Stop the engine and close the diesel fuel line valve (if equipped).2. Unscrew and remove filter.3. Clean the gasket sealing surface on the filter base.
Do not pour fuel into the new filter elements before installing. Prime the system as instructed in the topic, PRIMING THE FUEL SYSTEM.
4. Lubricate the filter gasket with clean diesel fuel.5. Tighten the filter by hand, only tight enough to prevent leaks. (Do not overtighten.)6. Prime the fuel system. Refer to the topic "PRIMING THE FUEL SYSTEM"
REMOVING FUEL FILTER ELEMENT KEEP A NEW FUEL FILTER ON HAND: An extra filter should be kept on hand for replacement. Always keep the filter wrapped in its original carton to insure against dust and dirt accumulation which will shorten the life of the filter or may cause damage to the fuel injection equipment.PRIMING THE FUEL SYSTEM: Any time the fuel flow is broken and air is allowed to get into the fuel system, the system must be primed. If air is left in the lines, the fuel system may become air bound, resulting in inability to start the engine or the misfiring of one or more cylinders.
PRIMING THE FUEL SYSTEMThe fuel priming pump is mounted on the fuel filter housing as shown. If only the fuel filter is changed follow steps 1 through 5. If the fuel system is completely drained or if the engine has run out of fuel continue with steps through 10.1. Check to see that the fuel line valve is open.2. Open the fuel filter vent valve on the fuel filter housing.3. Loosen the knob of the fuel priming pump.4. Operate the pump plunger in and out until the flow of fuel from the vent valve is continuous and free of air bubbles.5. Close vent valve.6. Move governor control to the shut-off position and loosen fuel line nuts (one at a time) at the pump housing.7. Operate priming pump until clear fuel flows from the fuel pump lines. Tighten fuel line nut.8. Repeat for each fuel pump.9. Lock the knob of the fuel priming pump to its original position.10. Start the engine. If the engine does not run smoothly further bleeding may be necessary. With the engine running, open and close the fuel injection line nuts, one at a time, several times in succession to be sure all the air is bled from the system. Tighten fuel line nuts to 30 lbs.ft. (4,1 mkg). Do not overtighten.Fuel Injection Equipment
When improper fuel injection is affecting engine operation, a systematic check should be made to determine the cause. The most likely cause is dirt or water in the fuel. Drain the sediment from the fuel tank. Check the fuel pressure gauge as mentioned in the topic, FUEL FILTERING SYSTEM. Replace the filter element if necessary. Then prime the fuel system until clean fuel reaches the fuel
Have questions with 106675-4731?
Group cross 106675-4731 ZEXEL
Komatsu
Komatsu
Komatsu
Komatsu
Komatsu
106675-4731
INJECTION-PUMP ASSEMBLY