Information injection-pump assembly
BOSCH
9 400 612 126
9400612126
ZEXEL
106675-4711
1066754711
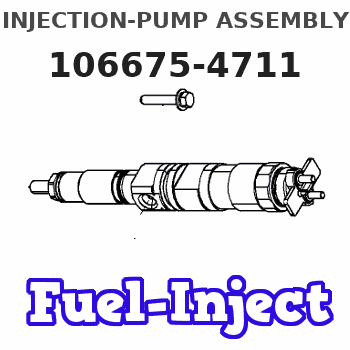
Rating:
Service parts 106675-4711 INJECTION-PUMP ASSEMBLY:
1.
_
5.
AUTOM. ADVANCE MECHANIS
7.
COUPLING PLATE
8.
_
9.
_
11.
Nozzle and Holder
6152-12-3100
12.
Open Pre:MPa(Kqf/cm2)
27.5{280}
15.
NOZZLE SET
Include in #1:
106675-4711
as INJECTION-PUMP ASSEMBLY
Cross reference number
BOSCH
9 400 612 126
9400612126
ZEXEL
106675-4711
1066754711
Zexel num
Bosch num
Firm num
Name
Calibration Data:
Adjustment conditions
Test oil
1404 Test oil ISO4113 or {SAEJ967d}
1404 Test oil ISO4113 or {SAEJ967d}
Test oil temperature
degC
40
40
45
Nozzle and nozzle holder
105780-8130
Bosch type code
EFEP215A
Nozzle
105780-0050
Bosch type code
DN6TD119NP1T
Nozzle holder
105780-2090
Bosch type code
EFEP215
Opening pressure
MPa
17.2
Opening pressure
kgf/cm2
175
Injection pipe
Outer diameter - inner diameter - length (mm) mm 8-3-600
Outer diameter - inner diameter - length (mm) mm 8-3-600
Overflow valve
131425-2120
Overflow valve opening pressure
kPa
157
123
191
Overflow valve opening pressure
kgf/cm2
1.6
1.25
1.95
Tester oil delivery pressure
kPa
157
157
157
Tester oil delivery pressure
kgf/cm2
1.6
1.6
1.6
RED3 control unit part number
407910-3
960
RED3 rack sensor specifications
mm
19
Direction of rotation (viewed from drive side)
Left L
Left L
Injection timing adjustment
Direction of rotation (viewed from drive side)
Left L
Left L
Injection order
1-5-3-6-
2-4
Pre-stroke
mm
3.8
3.75
3.85
Beginning of injection position
Drive side NO.1
Drive side NO.1
Difference between angles 1
Cal 1-5 deg. 60 59.5 60.5
Cal 1-5 deg. 60 59.5 60.5
Difference between angles 2
Cal 1-3 deg. 120 119.5 120.5
Cal 1-3 deg. 120 119.5 120.5
Difference between angles 3
Cal 1-6 deg. 180 179.5 180.5
Cal 1-6 deg. 180 179.5 180.5
Difference between angles 4
Cyl.1-2 deg. 240 239.5 240.5
Cyl.1-2 deg. 240 239.5 240.5
Difference between angles 5
Cal 1-4 deg. 300 299.5 300.5
Cal 1-4 deg. 300 299.5 300.5
Injection quantity adjustment
Rack position
(11.8)
Vist
V
2.08
2.08
2.08
Pump speed
r/min
900
900
900
Average injection quantity
mm3/st.
323
320
326
Max. variation between cylinders
%
0
-3
3
Basic
*
Injection quantity adjustment_02
Rack position
(6.6)
Vist
V
2.9
2.8
3
Pump speed
r/min
375
375
375
Average injection quantity
mm3/st.
16.5
15
18
Max. variation between cylinders
%
0
-15
15
Test data Ex:
Speed control lever angle

N:Pump normal
S:Stop the pump.
(1)Rack position = aa
(2)Rack position bb
----------
aa=20mm bb=1mm
----------
a=27deg+-5deg b=37deg+-5deg
----------
aa=20mm bb=1mm
----------
a=27deg+-5deg b=37deg+-5deg
0000000901
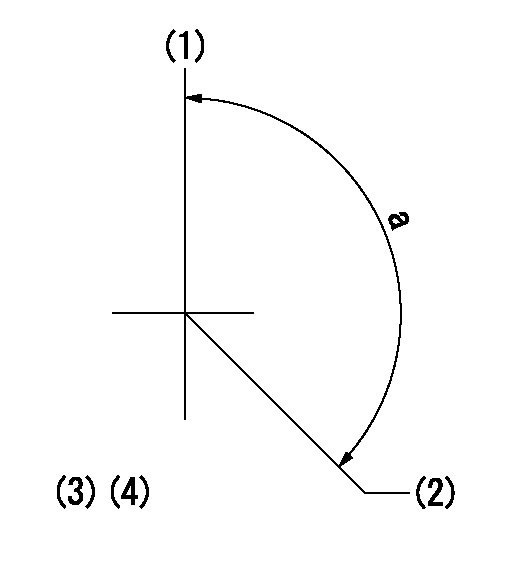
(1)Pump vertical direction
(2)Coupling's key groove position at No 1 cylinder's beginning of injection
(3)-
(4)-
----------
----------
a=(150deg)
----------
----------
a=(150deg)
Stop lever angle
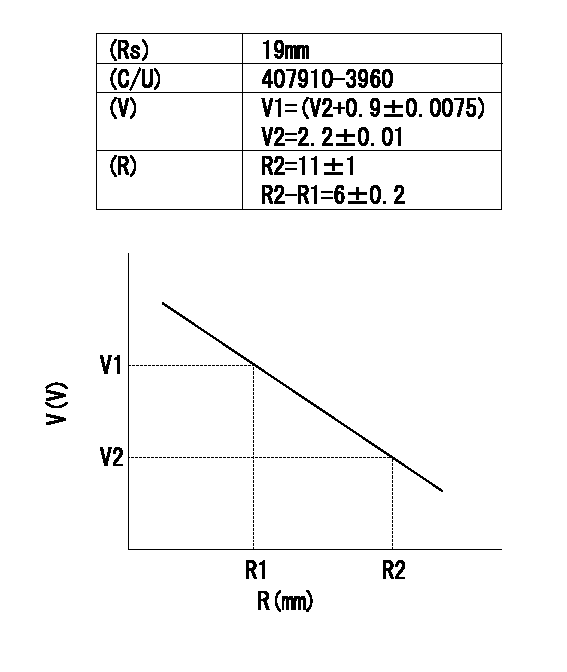
(Rs) rack sensor specifications
(C/U) control unit part number
(V) Rack sensor output voltage
(R) Rack position (mm)
1. Confirming governor output characteristics (rack 19 mm, span 6 mm)
(1)When the output voltages of the rack sensor are V1 and V2, check that the rack positions R1 and R2 in the table above are satisfied.
----------
----------
----------
----------
Information:
Illustration 4 g01341045
(6) Temperature Sensor
(7) Pressure Sensor
Mount the 271-7350 Warning Indicator Module Gp in a place that is easy to view. Ensure that the ambient temperature is below 45 °C (113 °F), and ensure that the Warning Indicator Module is not directly exposed to high pressure steam cleaning, solvents, the battery off gas, or electrical discharge. Note: The LED display panel may be installed in the cab of the vehicle.
Illustration 5 g01341118
(8) LED display panel
(9) ECM Installation for the Wiring Harness
The 274-7578 Monitor Electronic Control Module is provided with a 307-5521 Wire Harness.
Connect the 70 pin AMP to the ECM using a 160-7690 Connector Plug As. Tighten the Connector Screw for the ECM to 6 1 N m (4 0.73 lb ft).
Locate a 12 VDC or 24 VDC power supply that is always available even when the key is turned "OFF".
Connect the power wires from the wiring harness to the power supply. Install a 15 AMP fuse in this circuit. If an additional wire must be spliced, use a 14 gauge wire.
Attach the appropriate connectors to the pressure sensor, the temperature sensor, and the lamp group. Note: The service tool that is used in this installation is Caterpillar Electronic Technician (CAT ET). The service tool connector is a 9 pin Deutsch connector that contains the CDL (Caterpillar Data Link)/ATA, CAN/J1939, and power. A connection from the 274-7578 Monitor Electronic Control Module to the PC requires a Caterpillar Communications adapter, which connects to the PC via a serial port.The service tool (CAT ET) supports the following functions:
Download and review active alarms and logged alarms
Clear active alarms
View the data in real time.
Flash the diagnostic module.
Provide the capability for the user to configure certain parameters.Software Configuration
Refer to Systems Operation, Troubleshooting, Testing and Adjusting, KENR6695 for a description of controllable parameters and operation instructions.Once the 274-7578 Monitor Electronic Control Modulehas power, the 274-7578 Monitor Electronic Control Module will begin monitoring the pressure sensors and the temperature sensors.
Check whether CAT ET is configured with English or Metric units.
Set CAT ET to Metric units if a Metric unit is not already selected. Specifications
Table 3
System Requirements
Requirements for 12VDC or 24VDC System Value Notes
Operating Voltage Minimum +9V Minimum continuous operating voltage without damage to the ECM
Maximum Operating Voltage +32V Maximum continuous operating voltage without damage to the ECM
The voltage is over the maximum voltage that is allowed (two minutes continuous). +80V At 25 °C (77 °F)
Reverse Voltage (one hour) -32V At 85 °C (185 °F)
Power up voltage for the ECM +9V The minimum voltage for the ECM to internally run. Operating the engine at this voltage will cause the damage to the ECM.
The maximum current draw with key switch off 10mA
Maximum current draw with zero engine speed and no loads being driven 500mA
Maximum continuous operating current draw 10A This highly dependent upon the number and type of loads driven by the ECM
Recommended size for the Battery Fuse. 15A
Table 4
Operating Conditions
Thermal Conditions Vibrations Humidity Tolerance Salt Spray Tolerance Moisture Leakage Chemical Splash Immunity Electrostatic Environment
Operating Temperature Range: