Information injection-pump assembly
ZEXEL
106675-4352
1066754352
KOMATSU
6152711450
6152711450
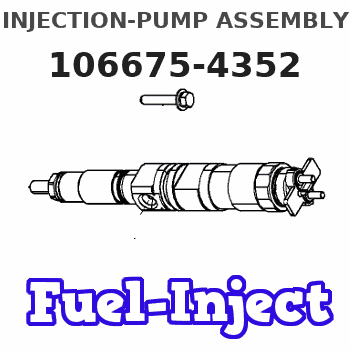
Rating:
Service parts 106675-4352 INJECTION-PUMP ASSEMBLY:
1.
_
5.
AUTOM. ADVANCE MECHANIS
8.
_
9.
_
11.
Nozzle and Holder
6152-11-3100
12.
Open Pre:MPa(Kqf/cm2)
24.5{250}
15.
NOZZLE SET
Include in #1:
106675-4352
as INJECTION-PUMP ASSEMBLY
Cross reference number
ZEXEL
106675-4352
1066754352
KOMATSU
6152711450
6152711450
Zexel num
Bosch num
Firm num
Name
Calibration Data:
Adjustment conditions
Test oil
1404 Test oil ISO4113 or {SAEJ967d}
1404 Test oil ISO4113 or {SAEJ967d}
Test oil temperature
degC
40
40
45
Nozzle and nozzle holder
105780-8140
Bosch type code
EF8511/9A
Nozzle
105780-0000
Bosch type code
DN12SD12T
Nozzle holder
105780-2080
Bosch type code
EF8511/9
Opening pressure
MPa
17.2
Opening pressure
kgf/cm2
175
Injection pipe
Outer diameter - inner diameter - length (mm) mm 8-3-600
Outer diameter - inner diameter - length (mm) mm 8-3-600
Overflow valve
131424-1520
Overflow valve opening pressure
kPa
157
123
191
Overflow valve opening pressure
kgf/cm2
1.6
1.25
1.95
Tester oil delivery pressure
kPa
157
157
157
Tester oil delivery pressure
kgf/cm2
1.6
1.6
1.6
Direction of rotation (viewed from drive side)
Left L
Left L
Injection timing adjustment
Direction of rotation (viewed from drive side)
Left L
Left L
Injection order
1-5-3-6-
2-4
Pre-stroke
mm
3.8
3.75
3.85
Beginning of injection position
Drive side NO.1
Drive side NO.1
Difference between angles 1
Cal 1-5 deg. 60 59.5 60.5
Cal 1-5 deg. 60 59.5 60.5
Difference between angles 2
Cal 1-3 deg. 120 119.5 120.5
Cal 1-3 deg. 120 119.5 120.5
Difference between angles 3
Cal 1-6 deg. 180 179.5 180.5
Cal 1-6 deg. 180 179.5 180.5
Difference between angles 4
Cyl.1-2 deg. 240 239.5 240.5
Cyl.1-2 deg. 240 239.5 240.5
Difference between angles 5
Cal 1-4 deg. 300 299.5 300.5
Cal 1-4 deg. 300 299.5 300.5
Injection quantity adjustment
Adjusting point
A
Rack position
10.7
Pump speed
r/min
1050
1050
1050
Average injection quantity
mm3/st.
184
182
186
Max. variation between cylinders
%
0
-3
3
Basic
*
Fixing the lever
*
Injection quantity adjustment_02
Adjusting point
C
Rack position
5.4+-0.5
Pump speed
r/min
400
400
400
Average injection quantity
mm3/st.
12.5
11
14
Max. variation between cylinders
%
0
-15
15
Fixing the rack
*
Test data Ex:
Governor adjustment
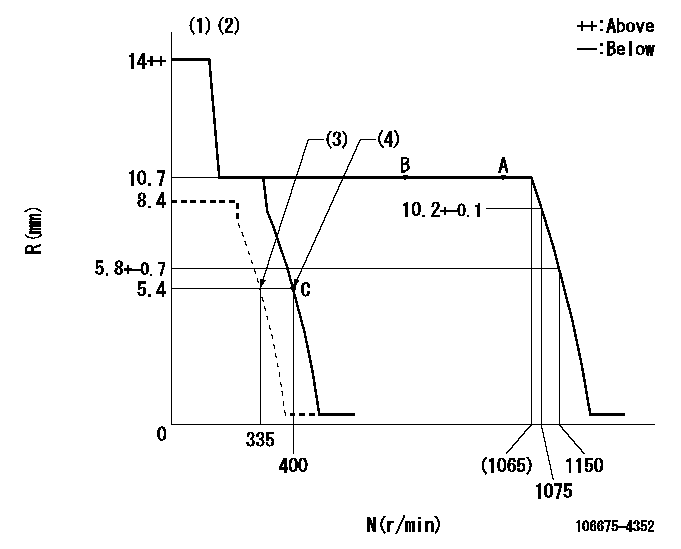
N:Pump speed
R:Rack position (mm)
(1)Target notch: K
(2)Tolerance for racks not indicated: +-0.05mm.
(3)Set idle sub-spring
(4)Main spring setting
----------
K=7
----------
----------
K=7
----------
Speed control lever angle
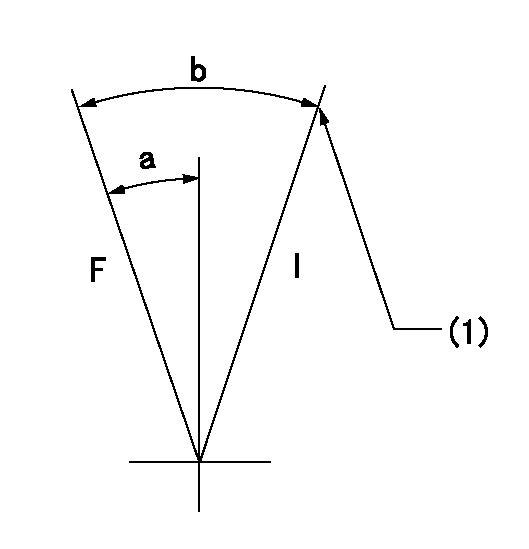
F:Full speed
I:Idle
(1)Stopper bolt setting
----------
----------
a=7deg+-5deg b=28deg+-5deg
----------
----------
a=7deg+-5deg b=28deg+-5deg
Stop lever angle

N:Pump normal
S:Stop the pump.
----------
----------
a=53deg+-5deg b=66.5deg+-5deg
----------
----------
a=53deg+-5deg b=66.5deg+-5deg
Timing setting

(1)Pump vertical direction
(2)Coupling's key groove position at No 1 cylinder's beginning of injection
(3)-
(4)-
----------
----------
a=(150deg)
----------
----------
a=(150deg)
Information:
Introduction
Do not perform any procedure in this Special Instruction until you have read the information and you understand the information.There have been isolated occurrences of excessive fuel leakage past the electronic unit injectors on some engines.Accelerated wear on the delivery valve results in an increased leak rate. The high pressure pump cannot generate enough fuel flow or volume to compensate for the leakoff rates above the critical value 38 mL (1.3 oz) per 30 seconds of cranking for six cylinder engines at a speed of 150 rpm. The high pressure pump cannot generate enough fuel flow or volume to compensate for the leakoff rates above the critical value 25 mL (0.85 oz) per 30 seconds of cranking for four cylinder engines at a speed of 150 rpm.If the engine turns over but the engine does not start, refer to Troubleshooting, "Engine Cranks but Will Not Start".Test Procedure
Before begining any work on the fuel system, refer to Operation and Maintenance Manual, "General Hazard Information and High Pressure Fuel Lines" for safety information.Refer to Systems Operation, Testing and Adjusting, "Cleanliness of Fuel System Components" for detailed information on the standards of cleanliness that must be observed during ALL work on the fuel system.
Table 1
Required Tools    
Tool     Part Number     Part Description     Qty    
A     334-3221     Fuel Leakoff Kit     1    
Ensure that the engine is shut down.
Illustration 1 g02103090
Injector harness
Disconnect the injector harness (1) from the front of the engine.
Illustration 2 g02103093
Typical exampleNote: Direct any leaking fuel into a suitable container.
Remove the bolt (2) from the "fuel relief block" and save the bolt for reinstallation.
Illustration 3 g02103095
Fuel leakoff kit (A) Tooling (3) Clear plastic hose
Install tooling (A) to the "fuel relief block".
Slide the tooling through the banjo bolt in order to replace the bolt that was removed in the previous step.
Thread the tooling into the "fuel relief block" and slightly tighten the tooling.
Connect a plastic hose (3) onto the tooling. Place the opposite end of the plastic hose into a suitable container that is clean.
Crank the engine with the starting motor for 30 seconds.
Record the amount of fuel that has been collected. Conduct the test three times. Calculate the average of the three values.
For six cylinder engines, if more than 38 mL (1.3 oz) of fuel has been collected during the 30 second crank test, then there is high leakoff of the electronic unit injectors. For four cylinder engines, if more than 25 mL (0.85 oz) of fuel has been collected during the 30 second crank test, then there is high leakoff of the electronic unit injectors. If this is the case, replace the electronic unit injectors and the fuel injection lines. Return the original electronic unit injectors and the fuel injection lines to the parts return center.
For six cylinder
Do not perform any procedure in this Special Instruction until you have read the information and you understand the information.There have been isolated occurrences of excessive fuel leakage past the electronic unit injectors on some engines.Accelerated wear on the delivery valve results in an increased leak rate. The high pressure pump cannot generate enough fuel flow or volume to compensate for the leakoff rates above the critical value 38 mL (1.3 oz) per 30 seconds of cranking for six cylinder engines at a speed of 150 rpm. The high pressure pump cannot generate enough fuel flow or volume to compensate for the leakoff rates above the critical value 25 mL (0.85 oz) per 30 seconds of cranking for four cylinder engines at a speed of 150 rpm.If the engine turns over but the engine does not start, refer to Troubleshooting, "Engine Cranks but Will Not Start".Test Procedure
Before begining any work on the fuel system, refer to Operation and Maintenance Manual, "General Hazard Information and High Pressure Fuel Lines" for safety information.Refer to Systems Operation, Testing and Adjusting, "Cleanliness of Fuel System Components" for detailed information on the standards of cleanliness that must be observed during ALL work on the fuel system.
Table 1
Required Tools    
Tool     Part Number     Part Description     Qty    
A     334-3221     Fuel Leakoff Kit     1    
Ensure that the engine is shut down.
Illustration 1 g02103090
Injector harness
Disconnect the injector harness (1) from the front of the engine.
Illustration 2 g02103093
Typical exampleNote: Direct any leaking fuel into a suitable container.
Remove the bolt (2) from the "fuel relief block" and save the bolt for reinstallation.
Illustration 3 g02103095
Fuel leakoff kit (A) Tooling (3) Clear plastic hose
Install tooling (A) to the "fuel relief block".
Slide the tooling through the banjo bolt in order to replace the bolt that was removed in the previous step.
Thread the tooling into the "fuel relief block" and slightly tighten the tooling.
Connect a plastic hose (3) onto the tooling. Place the opposite end of the plastic hose into a suitable container that is clean.
Crank the engine with the starting motor for 30 seconds.
Record the amount of fuel that has been collected. Conduct the test three times. Calculate the average of the three values.
For six cylinder engines, if more than 38 mL (1.3 oz) of fuel has been collected during the 30 second crank test, then there is high leakoff of the electronic unit injectors. For four cylinder engines, if more than 25 mL (0.85 oz) of fuel has been collected during the 30 second crank test, then there is high leakoff of the electronic unit injectors. If this is the case, replace the electronic unit injectors and the fuel injection lines. Return the original electronic unit injectors and the fuel injection lines to the parts return center.
For six cylinder