Information injection-pump assembly
BOSCH
9 400 611 462
9400611462
ZEXEL
106673-7960
1066737960
MITSUBISHI
ME158505
me158505
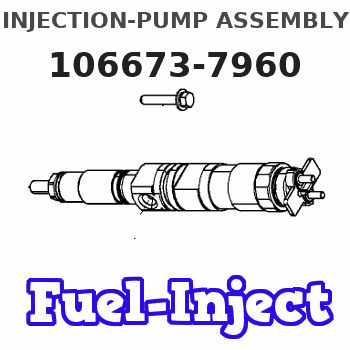
Rating:
Service parts 106673-7960 INJECTION-PUMP ASSEMBLY:
1.
_
7.
COUPLING PLATE
8.
_
9.
_
11.
Nozzle and Holder
ME158200
12.
Open Pre:MPa(Kqf/cm2)
17.7{180}/21.6{220}
14.
NOZZLE
Include in #1:
106673-7960
as INJECTION-PUMP ASSEMBLY
Cross reference number
BOSCH
9 400 611 462
9400611462
ZEXEL
106673-7960
1066737960
MITSUBISHI
ME158505
me158505
Zexel num
Bosch num
Firm num
Name
9 400 611 462
ME158505 MITSUBISHI
INJECTION-PUMP ASSEMBLY
6D24 * K 14CA PE6P,6PD PE
6D24 * K 14CA PE6P,6PD PE
Calibration Data:
Adjustment conditions
Test oil
1404 Test oil ISO4113 or {SAEJ967d}
1404 Test oil ISO4113 or {SAEJ967d}
Test oil temperature
degC
40
40
45
Nozzle and nozzle holder
105780-8140
Bosch type code
EF8511/9A
Nozzle
105780-0000
Bosch type code
DN12SD12T
Nozzle holder
105780-2080
Bosch type code
EF8511/9
Opening pressure
MPa
17.2
Opening pressure
kgf/cm2
175
Injection pipe
Outer diameter - inner diameter - length (mm) mm 8-3-600
Outer diameter - inner diameter - length (mm) mm 8-3-600
Overflow valve
131424-4620
Overflow valve opening pressure
kPa
225
225
225
Overflow valve opening pressure
kgf/cm2
2.6
2.6
2.6
Tester oil delivery pressure
kPa
157
157
157
Tester oil delivery pressure
kgf/cm2
1.6
1.6
1.6
Direction of rotation (viewed from drive side)
Right R
Right R
Injection timing adjustment
Direction of rotation (viewed from drive side)
Right R
Right R
Injection order
1-5-3-6-
2-4
Pre-stroke
mm
4.8
4.75
4.85
Beginning of injection position
Governor side NO.1
Governor side NO.1
Difference between angles 1
Cal 1-5 deg. 60 59.5 60.5
Cal 1-5 deg. 60 59.5 60.5
Difference between angles 2
Cal 1-3 deg. 120 119.5 120.5
Cal 1-3 deg. 120 119.5 120.5
Difference between angles 3
Cal 1-6 deg. 180 179.5 180.5
Cal 1-6 deg. 180 179.5 180.5
Difference between angles 4
Cyl.1-2 deg. 240 239.5 240.5
Cyl.1-2 deg. 240 239.5 240.5
Difference between angles 5
Cal 1-4 deg. 300 299.5 300.5
Cal 1-4 deg. 300 299.5 300.5
Injection quantity adjustment
Adjusting point
A
Rack position
8.8
Pump speed
r/min
750
750
750
Average injection quantity
mm3/st.
94.5
91.5
97.5
Max. variation between cylinders
%
0
-3
3
Basic
*
Fixing the lever
*
Injection quantity adjustment_02
Adjusting point
B
Rack position
8.5
Pump speed
r/min
750
750
750
Average injection quantity
mm3/st.
84.5
81.5
87.5
Fixing the rack
*
Injection quantity adjustment_03
Adjusting point
C
Rack position
5.5+-0.5
Pump speed
r/min
300
300
300
Average injection quantity
mm3/st.
9.5
6.9
12.1
Fixing the rack
*
Remarks
Check
Check
Injection quantity adjustment_04
Adjusting point
D
Rack position
4.8
Pump speed
r/min
500
500
500
Average injection quantity
mm3/st.
8.5
5.9
11.1
Max. variation between cylinders
%
0
-15
15
Fixing the rack
*
Injection quantity adjustment_05
Adjusting point
E
Rack position
-
Pump speed
r/min
100
100
100
Average injection quantity
mm3/st.
100
90
110
Fixing the lever
*
Rack limit
*
Timer adjustment
Pump speed
r/min
(900)
Advance angle
deg.
0.5
Timer adjustment_02
Pump speed
r/min
-
Advance angle
deg.
2
2
2
Remarks
Measure the actual speed, stop
Measure the actual speed, stop
Test data Ex:
Governor adjustment
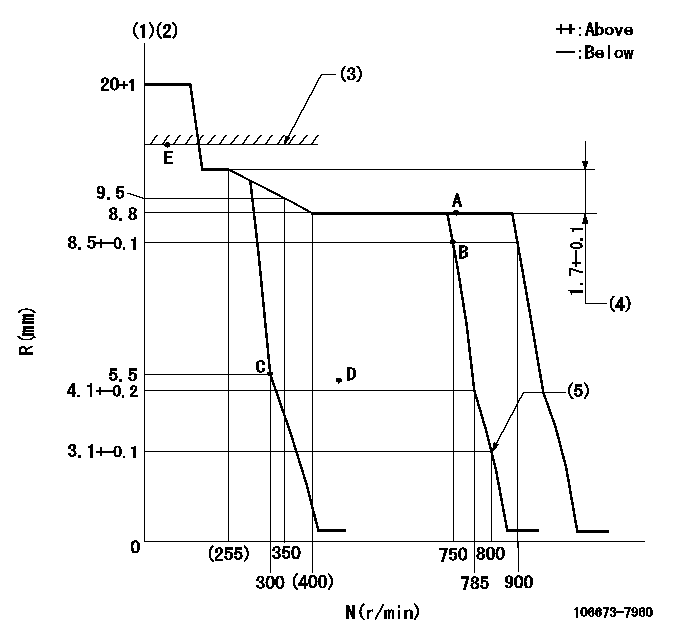
N:Pump speed
R:Rack position (mm)
(1)Target notch: K
(2)Tolerance for racks not indicated: +-0.05mm.
(3)RACK LIMIT
(4)Rack difference between N = N1 and N = N2
(5)Set idle sub-spring
----------
K=8 N1=750r/min N2=220r/min
----------
----------
K=8 N1=750r/min N2=220r/min
----------
Speed control lever angle
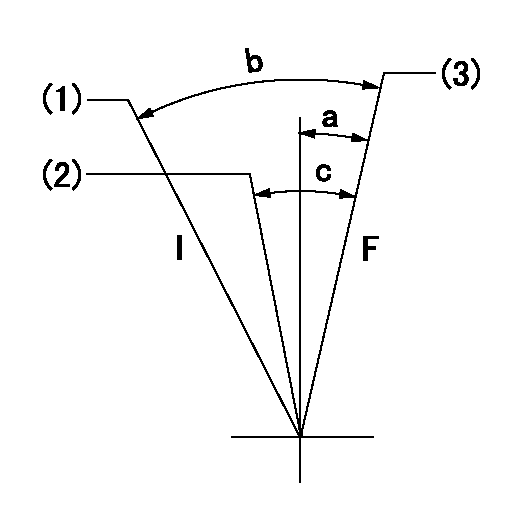
F:Full speed
I:Idle
(1)Stopper bolt setting
(2)Set the pump speed at aa
(3)Set the pump speed at bb (at delivery)
----------
aa=750r/min bb=900r/min
----------
a=3deg+-5deg b=24deg+-5deg c=6deg+-5deg
----------
aa=750r/min bb=900r/min
----------
a=3deg+-5deg b=24deg+-5deg c=6deg+-5deg
Stop lever angle

N:Pump normal
S:Stop the pump.
----------
----------
a=43.5deg+-5deg b=53deg+-5deg
----------
----------
a=43.5deg+-5deg b=53deg+-5deg
Timing setting

(1)Pump vertical direction
(2)Coupling's key groove position at No 1 cylinder's beginning of injection
(3)-
(4)-
----------
----------
a=(7deg)
----------
----------
a=(7deg)
Information:
ACTION REQUIRED
After Failure:
1 - Update Engine Software, refer to UENR0611 Troubleshooting ? ECM Software ? Install, ensure to follow the steps to save the Engine Configuration data. Refer to the table in Image 1 to determine the correct engine software file to apply.
2 - Service CCB Filter and replace with new filter, refer to SEBU8727 Operation and Maintenance Manual ? Engine Crankcase Breather element ? Replace.
3 - Remove Diesel Particulate Filter, Refer to UENR0621 Disassembly and Assembly - Diesel Particulate Filter - Remove - Wall Flow Diesel Particulate Filter.
4 - Move the Diesel Particulate Filter Assembly to a suitable work surface.
5 - Refer to UENR0619 Specifications - Diesel Particulate Filter (Wall Flow Diesel Particulate Filter(DPF)), remove V Band Clamps (1)&(4), carefully split assembly and remove DPF Canister element.
6 - Using new DPF Kit Filter, reassemble the Diesel Particulate Filter Assembly noting the alignment marks previously made in Step 3, refer to UENR0619 Specifications - Diesel Particulate Filter (Wall Flow Diesel Particulate Filter(DPF)).
7 - Reinstall the Diesel Particulate Filter assembly, Refer to UENR0621 Disassembly and Assembly - Diesel Particulate Filter - Install - Wall Flow Diesel Particulate Filter.
8 - As the DPF has been replaced, ensure the ?DPF Replacement Reset? procedure is performed using CAT ET, refer to UENR0611 Troubleshooting - Service Tool Features - Components Replacement Resets.
Image1
SERVICE CLAIM ALLOWANCES
Product smu/age whichever comes first Caterpillar Dealer Suggested Customer Suggested
Parts % Labor Hrs% Parts % Labor Hrs% Parts % Labor Hrs%
*******Group 1*******
0-3000 hrs,
0-60 mo 100.0% 100.0% 0.0% 0.0% 0.0% 0.0%
This is a 6.0-hour job for Group 1
Product smu/age whichever comes first Caterpillar Dealer Suggested Customer Suggested
Parts % Labor Hrs% Parts % Labor Hrs% Parts % Labor Hrs%
*******Group 2*******
0-3000 hrs,
0-60 mo 100.0% 100.0% 0.0% 0.0% 0.0% 0.0%
This is a 6.0-hour job for Group 2
PARTS DISPOSITION
Handle the parts in accordance with your Warranty Bulletin on warranty parts handling.