Information injection-pump assembly
BOSCH
9 400 617 350
9400617350
ZEXEL
106673-7641
1066737641
MITSUBISHI
ME158332
me158332
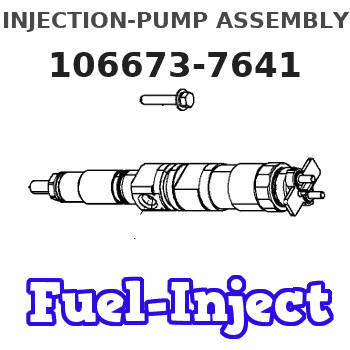
Rating:
Service parts 106673-7641 INJECTION-PUMP ASSEMBLY:
1.
_
7.
COUPLING PLATE
8.
_
9.
_
11.
Nozzle and Holder
ME158263
12.
Open Pre:MPa(Kqf/cm2)
17.7{180}/21.6{220}
14.
NOZZLE
Include in #1:
106673-7641
as INJECTION-PUMP ASSEMBLY
Cross reference number
BOSCH
9 400 617 350
9400617350
ZEXEL
106673-7641
1066737641
MITSUBISHI
ME158332
me158332
Zexel num
Bosch num
Firm num
Name
106673-7641
9 400 617 350
ME158332 MITSUBISHI
INJECTION-PUMP ASSEMBLY
6D24T K 14CA INJECTION PUMP ASSY PE6P,6PD PE
6D24T K 14CA INJECTION PUMP ASSY PE6P,6PD PE
Calibration Data:
Adjustment conditions
Test oil
1404 Test oil ISO4113 or {SAEJ967d}
1404 Test oil ISO4113 or {SAEJ967d}
Test oil temperature
degC
40
40
45
Nozzle and nozzle holder
105780-8140
Bosch type code
EF8511/9A
Nozzle
105780-0000
Bosch type code
DN12SD12T
Nozzle holder
105780-2080
Bosch type code
EF8511/9
Opening pressure
MPa
17.2
Opening pressure
kgf/cm2
175
Injection pipe
Outer diameter - inner diameter - length (mm) mm 8-3-600
Outer diameter - inner diameter - length (mm) mm 8-3-600
Overflow valve
131424-4620
Overflow valve opening pressure
kPa
255
221
289
Overflow valve opening pressure
kgf/cm2
2.6
2.25
2.95
Tester oil delivery pressure
kPa
157
157
157
Tester oil delivery pressure
kgf/cm2
1.6
1.6
1.6
Direction of rotation (viewed from drive side)
Right R
Right R
Injection timing adjustment
Direction of rotation (viewed from drive side)
Right R
Right R
Injection order
1-5-3-6-
2-4
Pre-stroke
mm
4.8
4.75
4.85
Beginning of injection position
Governor side NO.1
Governor side NO.1
Difference between angles 1
Cal 1-5 deg. 60 59.5 60.5
Cal 1-5 deg. 60 59.5 60.5
Difference between angles 2
Cal 1-3 deg. 120 119.5 120.5
Cal 1-3 deg. 120 119.5 120.5
Difference between angles 3
Cal 1-6 deg. 180 179.5 180.5
Cal 1-6 deg. 180 179.5 180.5
Difference between angles 4
Cyl.1-2 deg. 240 239.5 240.5
Cyl.1-2 deg. 240 239.5 240.5
Difference between angles 5
Cal 1-4 deg. 300 299.5 300.5
Cal 1-4 deg. 300 299.5 300.5
Injection quantity adjustment
Adjusting point
A
Rack position
9.3
Pump speed
r/min
1100
1100
1100
Average injection quantity
mm3/st.
116
113
119
Max. variation between cylinders
%
0
-3
3
Basic
*
Fixing the lever
*
Injection quantity adjustment_02
Adjusting point
B
Rack position
5.8+-0.5
Pump speed
r/min
425
425
425
Average injection quantity
mm3/st.
12.5
9.9
15.1
Max. variation between cylinders
%
0
-15
15
Fixing the rack
*
Injection quantity adjustment_03
Adjusting point
C
Rack position
-
Pump speed
r/min
100
100
100
Average injection quantity
mm3/st.
135
125
145
Fixing the lever
*
Rack limit
*
Timer adjustment
Pump speed
r/min
0
Advance angle
deg.
2.5
2
3
Timer adjustment_02
Pump speed
r/min
-
Advance angle
deg.
2.5
2
3
Remarks
Measure speed (beginning of operation).
Measure speed (beginning of operation).
Timer adjustment_03
Pump speed
r/min
-
Advance angle
deg.
0
0
0
Remarks
Measure the actual speed, stop
Measure the actual speed, stop
Test data Ex:
Governor adjustment
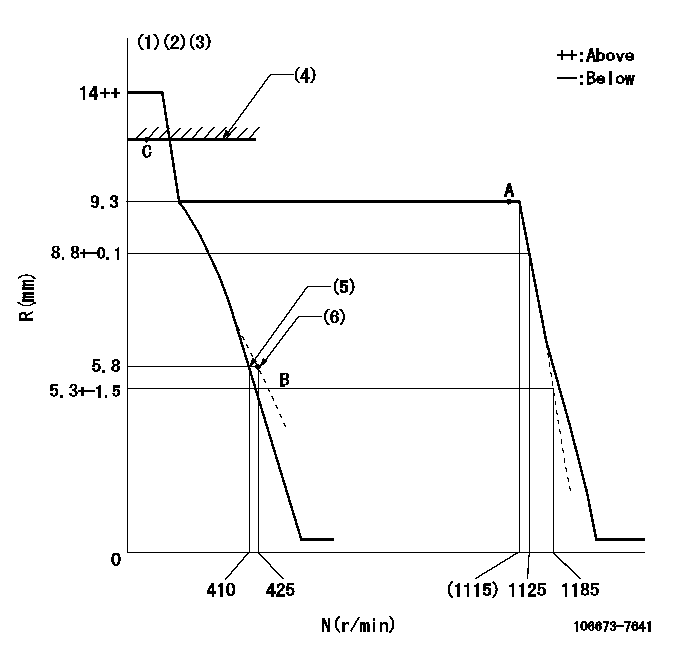
N:Pump speed
R:Rack position (mm)
(1)Notch fixed: K
(2)Tolerance for racks not indicated: +-0.05mm.
(3)Torque spring does not operate.
(4)RACK LIMIT
(5)Main spring setting
(6)Set idle sub-spring
----------
K=10
----------
----------
K=10
----------
Speed control lever angle

F:Full speed
I:Idle
(1)Stopper bolt setting
----------
----------
a=(23deg)+-5deg b=(7deg)+-5deg
----------
----------
a=(23deg)+-5deg b=(7deg)+-5deg
Stop lever angle
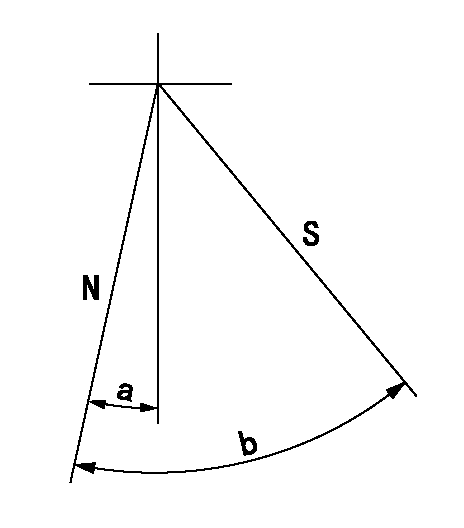
N:Pump normal
S:Stop the pump.
----------
----------
a=19deg+-5deg b=53deg+-5deg
----------
----------
a=19deg+-5deg b=53deg+-5deg
Timing setting

(1)Pump vertical direction
(2)Coupling's key groove position at No 1 cylinder's beginning of injection
(3)B.T.D.C.: aa
(4)-
----------
aa=12deg
----------
a=(6deg)
----------
aa=12deg
----------
a=(6deg)
Information:
(4) VOP (Valve Opening Pressure) Test A. Open the gauge protector valve [0-34500 kPa (0-5000 psi) gauge].B. Increase the pressure until test oil flows from the nozzle tip.C. Write down the VOP. (5) Pressure Loss Test A. Increase the pressure to 690 kPa (100 psi) less than the VOP.B. Close the pump isolator valve (6).C. Use the gauge protector valve (3), [0-34500 kPa (0-5000 psi) gauge] to adjust pressure to 690 kPa (100 psi) less than the VOP.D. After 30 seconds, write down the pressure loss. (6) Adjustment of Valve Opening Pressure If spray characteristics are satisfactory, adjust the valve unseating pressure: Use 7B2591 Cap Wrench (7) to remove the cap. Remove lift screw locknut (8) and loosen lift adjustment screw (9) approximately three turns, so it does not interfere with the pressure adjustment. Loosen pressure adjustment locknut (10).E. Install the nozzle on the 5P4150 Nozzle Tester. F. Use 7B2601 Wrench (11) and adjust the VOP. G. Remove the valve from the nozzle tester and put it in a vise. Install lift adjustment screw locknut (8).H. Use the 6B1655 Wrench to turn lift adjusting screw (9) down lightly against the stem of the fuel valve spring.I. Clamp the needle lift adjustment fixture to the fuel valve body.J. Use a thickness gauge and adjust screw (12) until there is a clearance of 0.43 (.017") between screw (12) and lift adjustment screw (9).K. Hold screw (12) in position with clamping screw (13).L. Remove the thickness gauge and loosen lift adjustment screw (9) until there is 0.3 (.010") clearance between screw (9) and screw (12), after lift screw locknut (8) is tightened with the 7B2587 Wrench. The correct needle lift setting for all valves is 0.177 (.007").Cleaning Needle, Nozzle And Nozzle End Of Flat Seat Valves (Except 1P1795 Master Valves)
(1) Remove cap (1), bonnet (2) or unseating pressure adjusting screw, spring retainer, spring (3) and spring stem (4). Put the correct needle extracting tool (5) through the valve body and tighten over the end of the needle. If the needle is tight, install a new valve service group, or disassemble and clean the valve according to the procedure that follows. (2) If a fuel valve has a chip of scale, metal or foreign material on the seat, this will prevent the needle, from seating on the spray valve nozzle end, and cause the inner surface of the nozzle end and the needle end to become coated with carbon. Put carbon scraper (6) in the needle extracting tool and insert it into the nozzle bore and against the nozzle end; carefully turn the tool one revolution, with a slight pressure to remove the carbon. The cutting surface of scraper (6) has been lapped as perfectly flat and square with the center line of the tool as possible. Unless it remains so, it cannot effectively remove carbon. Handle this tool with care. Two scrapers are provided, so if one becomes marred, the second can be used while another is being obtained.
(1) Remove cap (1), bonnet (2) or unseating pressure adjusting screw, spring retainer, spring (3) and spring stem (4). Put the correct needle extracting tool (5) through the valve body and tighten over the end of the needle. If the needle is tight, install a new valve service group, or disassemble and clean the valve according to the procedure that follows. (2) If a fuel valve has a chip of scale, metal or foreign material on the seat, this will prevent the needle, from seating on the spray valve nozzle end, and cause the inner surface of the nozzle end and the needle end to become coated with carbon. Put carbon scraper (6) in the needle extracting tool and insert it into the nozzle bore and against the nozzle end; carefully turn the tool one revolution, with a slight pressure to remove the carbon. The cutting surface of scraper (6) has been lapped as perfectly flat and square with the center line of the tool as possible. Unless it remains so, it cannot effectively remove carbon. Handle this tool with care. Two scrapers are provided, so if one becomes marred, the second can be used while another is being obtained.
Have questions with 106673-7641?
Group cross 106673-7641 ZEXEL
Mitsubishi
Mitsubishi
Mitsubishi
Mitsubishi
106673-7641
9 400 617 350
ME158332
INJECTION-PUMP ASSEMBLY
6D24T
6D24T