Information injection-pump assembly
ZEXEL
106673-7410
1066737410
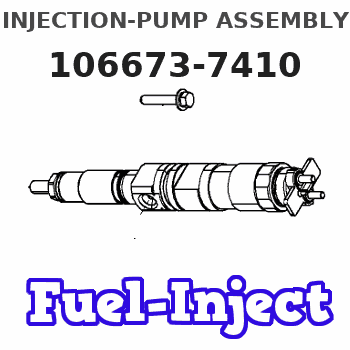
Rating:
Service parts 106673-7410 INJECTION-PUMP ASSEMBLY:
1.
_
7.
COUPLING PLATE
8.
_
9.
_
11.
Nozzle and Holder
ME151161
12.
Open Pre:MPa(Kqf/cm2)
15.7{160}/21.6{220}
14.
NOZZLE
Include in #1:
106673-7410
as INJECTION-PUMP ASSEMBLY
Cross reference number
ZEXEL
106673-7410
1066737410
Zexel num
Bosch num
Firm num
Name
106673-7410
INJECTION-PUMP ASSEMBLY
Calibration Data:
Adjustment conditions
Test oil
1404 Test oil ISO4113 or {SAEJ967d}
1404 Test oil ISO4113 or {SAEJ967d}
Test oil temperature
degC
40
40
45
Nozzle and nozzle holder
105780-8250
Bosch type code
1 688 901 101
Nozzle
105780-0120
Bosch type code
1 688 901 990
Nozzle holder
105780-2190
Opening pressure
MPa
20.7
Opening pressure
kgf/cm2
211
Injection pipe
Outer diameter - inner diameter - length (mm) mm 8-3-600
Outer diameter - inner diameter - length (mm) mm 8-3-600
Overflow valve
131425-0220
Overflow valve opening pressure
kPa
157
123
191
Overflow valve opening pressure
kgf/cm2
1.6
1.25
1.95
Tester oil delivery pressure
kPa
255
255
255
Tester oil delivery pressure
kgf/cm2
2.6
2.6
2.6
Direction of rotation (viewed from drive side)
Right R
Right R
Injection timing adjustment
Direction of rotation (viewed from drive side)
Right R
Right R
Injection order
1-5-3-6-
2-4
Pre-stroke
mm
3.9
3.85
3.95
Beginning of injection position
Governor side NO.1
Governor side NO.1
Difference between angles 1
Cal 1-5 deg. 60 59.5 60.5
Cal 1-5 deg. 60 59.5 60.5
Difference between angles 2
Cal 1-3 deg. 120 119.5 120.5
Cal 1-3 deg. 120 119.5 120.5
Difference between angles 3
Cal 1-6 deg. 180 179.5 180.5
Cal 1-6 deg. 180 179.5 180.5
Difference between angles 4
Cyl.1-2 deg. 240 239.5 240.5
Cyl.1-2 deg. 240 239.5 240.5
Difference between angles 5
Cal 1-4 deg. 300 299.5 300.5
Cal 1-4 deg. 300 299.5 300.5
Injection quantity adjustment
Adjusting point
-
Rack position
12.9
Pump speed
r/min
700
700
700
Each cylinder's injection qty
mm3/st.
147
143.3
150.7
Basic
*
Fixing the rack
*
Standard for adjustment of the maximum variation between cylinders
*
Injection quantity adjustment_02
Adjusting point
Z
Rack position
8+-0.5
Pump speed
r/min
385
385
385
Each cylinder's injection qty
mm3/st.
21
17.8
24.2
Fixing the rack
*
Standard for adjustment of the maximum variation between cylinders
*
Injection quantity adjustment_03
Adjusting point
A
Rack position
R1(12.9)
Pump speed
r/min
700
700
700
Average injection quantity
mm3/st.
147
146
148
Basic
*
Fixing the lever
*
Boost pressure
kPa
23.3
23.3
Boost pressure
mmHg
175
175
Injection quantity adjustment_04
Adjusting point
B
Rack position
R1+1.05
Pump speed
r/min
1100
1100
1100
Average injection quantity
mm3/st.
143.5
139.5
147.5
Fixing the lever
*
Boost pressure
kPa
23.3
23.3
Boost pressure
mmHg
175
175
Injection quantity adjustment_05
Adjusting point
C
Rack position
(R1-0.75
)
Pump speed
r/min
500
500
500
Average injection quantity
mm3/st.
142
136
148
Fixing the lever
*
Boost pressure
kPa
23.3
23.3
Boost pressure
mmHg
175
175
Injection quantity adjustment_06
Adjusting point
D
Rack position
(R2-1.3)
Pump speed
r/min
300
300
300
Average injection quantity
mm3/st.
104.5
102.5
106.5
Fixing the lever
*
Boost pressure
kPa
0
0
0
Boost pressure
mmHg
0
0
0
Boost compensator adjustment
Pump speed
r/min
300
300
300
Rack position
(R2-1.3)
Boost pressure
kPa
4
2.7
5.3
Boost pressure
mmHg
30
20
40
Boost compensator adjustment_02
Pump speed
r/min
300
300
300
Rack position
R2(R1(12
.9)-1)
Boost pressure
kPa
10.7
10.7
10.7
Boost pressure
mmHg
80
80
80
Test data Ex:
Governor adjustment
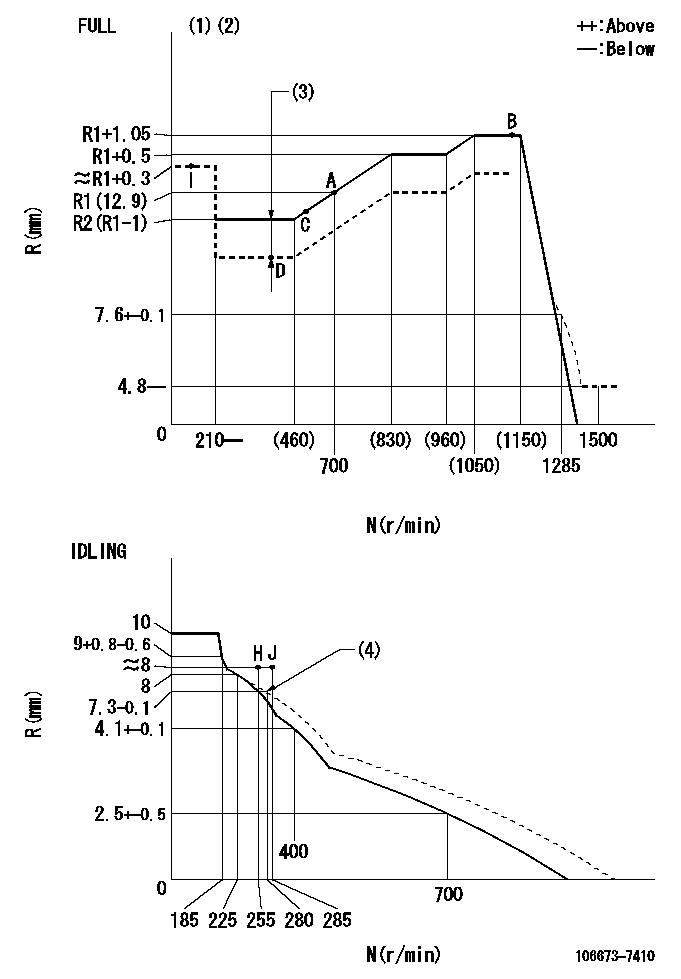
N:Pump speed
R:Rack position (mm)
(1)Torque cam stamping: T1
(2)Tolerance for racks not indicated: +-0.05mm.
(3)Boost compensator stroke: BCL
(4)Damper spring setting
----------
T1=AC25 BCL=(1.3)+-0.1mm
----------
----------
T1=AC25 BCL=(1.3)+-0.1mm
----------
Timer adjustment

(1)Adjusting range
(2)Step response time
(N): Speed of the pump
(L): Load
(theta) Advance angle
(Srd1) Step response time 1
(Srd2) Step response time 2
1. Adjusting conditions for the variable timer
(1)Adjust the clearance between the pickup and the protrusion to L.
----------
L=1-0.2mm N2=800r/min C2=(10deg) t1=2.5--sec. t2=2.5--sec.
----------
N1=750++r/min P1=0kPa(0kgf/cm2) P2=392kPa(4kgf/cm2) C1=10+-0.3deg R01=0/4load R02=4/4load
----------
L=1-0.2mm N2=800r/min C2=(10deg) t1=2.5--sec. t2=2.5--sec.
----------
N1=750++r/min P1=0kPa(0kgf/cm2) P2=392kPa(4kgf/cm2) C1=10+-0.3deg R01=0/4load R02=4/4load
Speed control lever angle
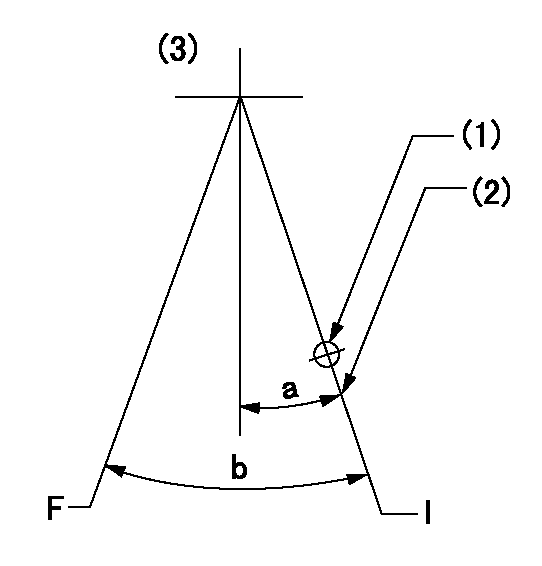
F:Full speed
I:Idle
(1)Use the hole at R = aa
(2)Stopper bolt set position 'H'
(3)Viewed from feed pump side.
----------
aa=37.5mm
----------
a=1deg+-5deg b=(39deg)+-3deg
----------
aa=37.5mm
----------
a=1deg+-5deg b=(39deg)+-3deg
Stop lever angle
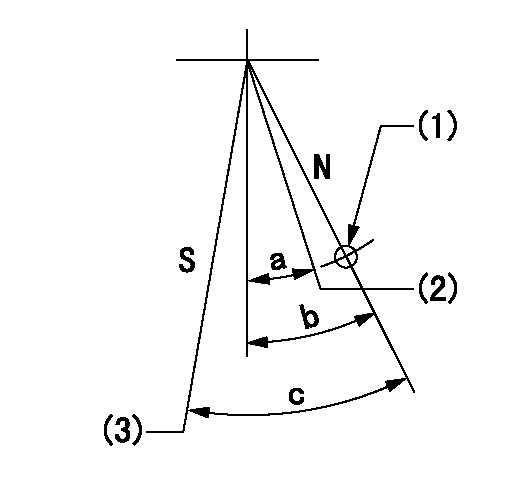
N:Pump normal
S:Stop the pump.
(1)Use the hole at R = aa
(2)Normal engine position (Rack position corresponding to bb)
(3)Set the stopper bolt so that speed = cc and rack position = dd and confirm non-injection.
----------
aa=54mm bb=18mm cc=1100r/min dd=3.5+-0.3mm
----------
a=(20.5deg) b=29.5deg+-5deg c=40deg+-5deg
----------
aa=54mm bb=18mm cc=1100r/min dd=3.5+-0.3mm
----------
a=(20.5deg) b=29.5deg+-5deg c=40deg+-5deg
0000001501 MICRO SWITCH
Adjustment of the micro-switch
Adjust the bolt to obtain the following lever position when the micro-switch is ON.
(1)Speed N1
(2)Rack position Ra
----------
N1=325r/min Ra=7.6+-0.1mm
----------
----------
N1=325r/min Ra=7.6+-0.1mm
----------
0000001601 RACK SENSOR
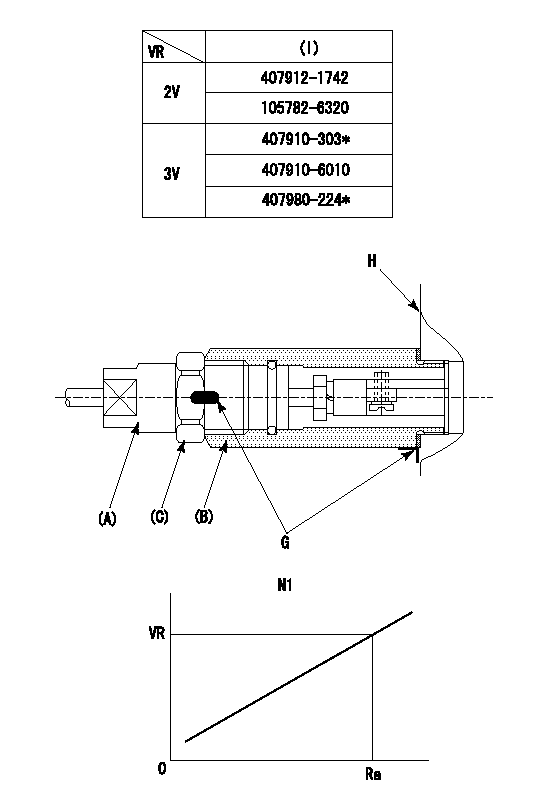
(VR) measurement voltage
(I) Part number of the control unit
(G) Apply red paint.
(H): End surface of the pump
1. Rack sensor adjustment (-0620)
(1)Fix the speed control lever at the full position
(2)Set the speed to N1 r/min.
(If the boost compensator is provided, apply boost pressure.)
(3)Adjust the bobbin (A) so that the rack sensor's output voltage is VR+-0.01.
(4)At that time, rack position must be Ra.
(5)Apply G at two places.
Connecting part between the joint (B) and the nut (F)
Connecting part between the joint (B) and the end surface of the pump (H)
----------
N1=1100r/min Ra=R1(12.9)+1.05mm
----------
----------
N1=1100r/min Ra=R1(12.9)+1.05mm
----------
Timing setting

(1)Pump vertical direction
(2)Coupling's key groove position at No 1 cylinder's beginning of injection
(3)B.T.D.C.: aa
(4)-
----------
aa=5deg
----------
a=(2deg)
----------
aa=5deg
----------
a=(2deg)
Information:
Typical Example2. Remove eight bolts (3) that fasten pipe (1) to the elbow. Remove four bolts (2) that fasten the elbow to the aftercooler cover. Remove elbow (4).
Typical Example3. Remove bracket (5) from the oil filter tube and the oil level gauge group.
Typical Example4. Remove four bolts (7) from the air inlet elbow. Remove plate (6) and elbow (8). 5. Remove two tubes (10) from the air compressor to the aftercooler.6. Remove elbows (9) from the aftercooler housing.
Typical Example
Put identification on bolts (12) because they are 6.4 mm (.25 in) longer than all other bolts. They must be installed in the same location.
7. Remove bolts (11) and (12) from cover, and remove the cover.
Put identification on bolt (14) because it is 12.7 mm (.50 in) shorter than all the other bolts. It must be installed in the same location. Remove four adapters (15). Put plugs in both holes in the aftercooler core assembly. This will keep coolant out of the engine intake manifold.
8. Remove bolts (13) and (14) that hold the core assembly in position.9. Remove the aftercooler core assembly. 10. Remove air line (17) from the fuel ratio control valve.11. Remove eight bolts (16). Remove housing assembly (18).Install Aftercooler
1. Check all seals and gaskets for damage. If damaged, use new parts for replacement.
All foreign material and dirt must be removed from the gasket surface and inside the housing and intake manifold.
2. Install housing (1) and air line (2) to the fuel control valve. 3. Install four new seals (3) on the core assembly. Put clean glycerin on the O-ring seals. 4. Install core assembly (4) inside the housing. Remove plugs in both holes of the aftercooler core assembly. Install the bolts that fasten the core to housing. Install the bolts in their original location. 5. Put clean engine oil in the bores of the adapters. Install adapters (5). 6. Put cover (6) in position on the aftercooler. Install the two bolts in position (7). These bolts are 6.4 mm (.25 in) longer than all other bolts around the housing. Install the remainder of the bolts around the housing. 7. Install elbows (8). 8. Install two tubes (9) between the air compressor and the aftercooler.
Typical Example9. Install elbow (10) and plate (11) on the aftercooler cover. Install the bracket that is a support for the oil filter tube and the oil level gauge group. Install the oil filter tube and the oil level gauge group.
Typical Example10. Install eight bolts (13) that fasten the pipe to elbow (14). Install the elbow in the turbocharger.11. Install the four bolts that fasten the elbow to aftercooler cover (12).12. Fill the engine with coolant to the correct level. See the Operation & Maintenance Manual.
Have questions with 106673-7410?
Group cross 106673-7410 ZEXEL
Mitsubishi
106673-7410
INJECTION-PUMP ASSEMBLY