Information injection-pump assembly
ZEXEL
106673-7281
1066737281
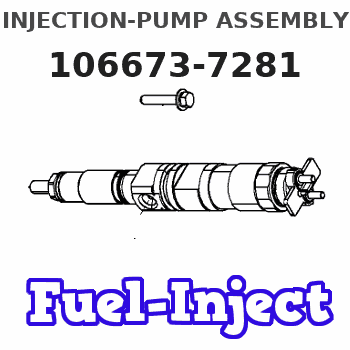
Rating:
Service parts 106673-7281 INJECTION-PUMP ASSEMBLY:
1.
_
7.
COUPLING PLATE
8.
_
9.
_
11.
Nozzle and Holder
ME150945
12.
Open Pre:MPa(Kqf/cm2)
17.7{180}/24.5{250}
14.
NOZZLE
Include in #1:
106673-7281
as INJECTION-PUMP ASSEMBLY
Cross reference number
ZEXEL
106673-7281
1066737281
Zexel num
Bosch num
Firm num
Name
106673-7281
INJECTION-PUMP ASSEMBLY
Calibration Data:
Adjustment conditions
Test oil
1404 Test oil ISO4113 or {SAEJ967d}
1404 Test oil ISO4113 or {SAEJ967d}
Test oil temperature
degC
40
40
45
Nozzle and nozzle holder
105780-8250
Bosch type code
1 688 901 101
Nozzle
105780-0120
Bosch type code
1 688 901 990
Nozzle holder
105780-2190
Opening pressure
MPa
20.7
Opening pressure
kgf/cm2
211
Injection pipe
Outer diameter - inner diameter - length (mm) mm 8-3-600
Outer diameter - inner diameter - length (mm) mm 8-3-600
Overflow valve
131425-0220
Overflow valve opening pressure
kPa
157
123
191
Overflow valve opening pressure
kgf/cm2
1.6
1.25
1.95
Tester oil delivery pressure
kPa
255
255
255
Tester oil delivery pressure
kgf/cm2
2.6
2.6
2.6
Direction of rotation (viewed from drive side)
Right R
Right R
Injection timing adjustment
Direction of rotation (viewed from drive side)
Right R
Right R
Injection order
1-5-3-6-
2-4
Pre-stroke
mm
3.9
3.85
3.95
Beginning of injection position
Governor side NO.1
Governor side NO.1
Difference between angles 1
Cal 1-5 deg. 60 59.5 60.5
Cal 1-5 deg. 60 59.5 60.5
Difference between angles 2
Cal 1-3 deg. 120 119.5 120.5
Cal 1-3 deg. 120 119.5 120.5
Difference between angles 3
Cal 1-6 deg. 180 179.5 180.5
Cal 1-6 deg. 180 179.5 180.5
Difference between angles 4
Cyl.1-2 deg. 240 239.5 240.5
Cyl.1-2 deg. 240 239.5 240.5
Difference between angles 5
Cal 1-4 deg. 300 299.5 300.5
Cal 1-4 deg. 300 299.5 300.5
Injection quantity adjustment
Adjusting point
-
Rack position
13.2
Pump speed
r/min
650
650
650
Each cylinder's injection qty
mm3/st.
153.5
149.7
157.3
Basic
*
Fixing the rack
*
Standard for adjustment of the maximum variation between cylinders
*
Injection quantity adjustment_02
Adjusting point
Z
Rack position
8.6+-0.5
Pump speed
r/min
360
360
360
Each cylinder's injection qty
mm3/st.
15.8
13.4
18.2
Fixing the rack
*
Standard for adjustment of the maximum variation between cylinders
*
Injection quantity adjustment_03
Adjusting point
A
Rack position
R1(13.2)
Pump speed
r/min
650
650
650
Average injection quantity
mm3/st.
153.5
152.5
154.5
Basic
*
Fixing the lever
*
Boost pressure
kPa
24
24
Boost pressure
mmHg
180
180
Injection quantity adjustment_04
Adjusting point
B
Rack position
R1+1.4
Pump speed
r/min
1100
1100
1100
Average injection quantity
mm3/st.
151.5
147.5
155.5
Fixing the lever
*
Boost pressure
kPa
24
24
Boost pressure
mmHg
180
180
Injection quantity adjustment_05
Adjusting point
D
Rack position
R3-1.2
Pump speed
r/min
300
300
300
Average injection quantity
mm3/st.
92.5
88.5
96.5
Fixing the lever
*
Boost pressure
kPa
0
0
0
Boost pressure
mmHg
0
0
0
Boost compensator adjustment
Pump speed
r/min
300
300
300
Rack position
R3-1.2
Boost pressure
kPa
4
3.3
4.7
Boost pressure
mmHg
30
25
35
Boost compensator adjustment_02
Pump speed
r/min
300
300
300
Rack position
R3(R1-1.
3)
Boost pressure
kPa
10.7
10.7
10.7
Boost pressure
mmHg
80
80
80
Timer adjustment
Pump speed
r/min
750--
Advance angle
deg.
0
0
0
Remarks
Start
Start
Timer adjustment_02
Pump speed
r/min
700
Advance angle
deg.
0.5
Timer adjustment_03
Pump speed
r/min
1100
Advance angle
deg.
4
3.5
4.5
Remarks
Finish
Finish
Test data Ex:
Governor adjustment
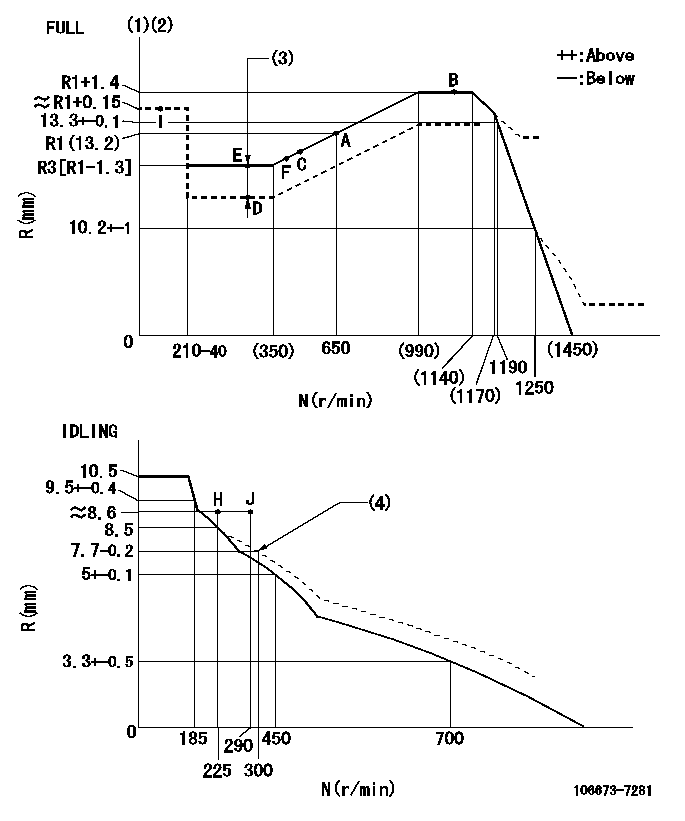
N:Pump speed
R:Rack position (mm)
(1)Torque cam stamping: T1
(2)Tolerance for racks not indicated: +-0.05mm.
(3)Boost compensator stroke: BCL
(4)Damper spring setting
----------
T1=AD44 BCL=1.2+-0.1mm
----------
----------
T1=AD44 BCL=1.2+-0.1mm
----------
Speed control lever angle
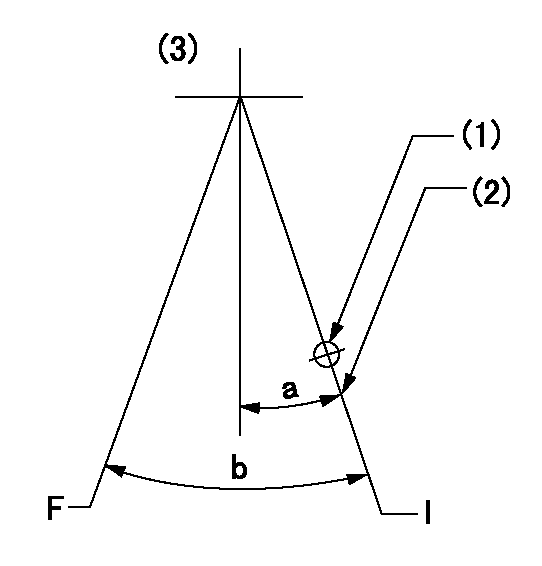
F:Full speed
I:Idle
(1)Use the hole at R = aa
(2)Stopper bolt set position 'H'
(3)Viewed from feed pump side.
----------
aa=37.5mm
----------
a=0.5deg+-5deg b=39deg+-3deg
----------
aa=37.5mm
----------
a=0.5deg+-5deg b=39deg+-3deg
Stop lever angle
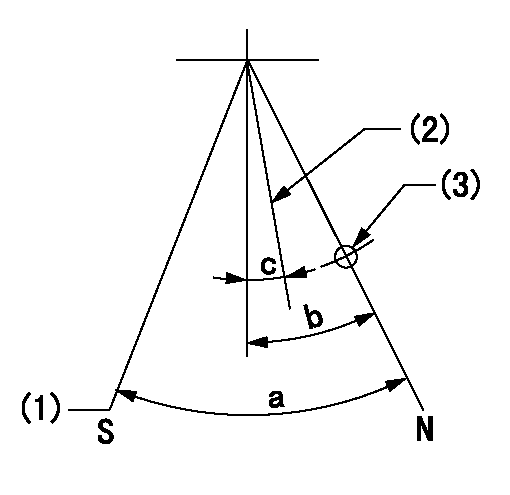
N:Pump normal
S:Stop the pump.
(1)At pump speed aa and rack position bb, set the stopper bolt. (Confirm non-injection.)
(2)Normal engine position (equivalent to R = cc).
(3)Use the hole above R = dd
----------
aa=1100r/min bb=3.5+-0.3mm cc=18mm dd=54mm
----------
a=41deg+-5deg b=29.5deg+-5deg c=(16.5deg)
----------
aa=1100r/min bb=3.5+-0.3mm cc=18mm dd=54mm
----------
a=41deg+-5deg b=29.5deg+-5deg c=(16.5deg)
0000001501 MICRO SWITCH
Adjustment of the micro-switch
Adjust the bolt to obtain the following lever position when the micro-switch is ON.
(1)Speed N1
(2)Rack position Ra
----------
N1=325r/min Ra=8.1+-0.1mm
----------
----------
N1=325r/min Ra=8.1+-0.1mm
----------
Timing setting

(1)Pump vertical direction
(2)Coupling's key groove position at No 1 cylinder's beginning of injection
(3)B.T.D.C.: aa
(4)-
----------
aa=8deg
----------
a=(2deg)
----------
aa=8deg
----------
a=(2deg)
Information:
Transmission Oil Cooler
The machine is equipped with a power shift transmission. A transmission oil cooler is installed in the outlet section of the radiator. The radiator coolant flows around the tubes of the cooler and cools the transmission oil as it flows through the cooler. The transmission oil then returns to the transmission inlet.Lubrication System
Oil Pump
(1) Strainer. (2) Oil pump relief valve. (3) Oil pump. (4) Idler gear. (5) Crankshaft gear.The lubrication system is the pressure type and the flow of oil goes from the oil pan through strainer (1) into oil pump (3). Oil pump (3) is driven by crankshaft gear (5) through the idler gear (4). The oil pump is connected to the front main bearing cap. Relief valve (2) which is spring loaded controls the maximum oil pressure. An oil pressure sending unit is connected to the main oil gallery.Oil under pressure goes from the oil pump through the relief valve, oil filter and into the main oil gallery that is a drilled passage the length of the crankcase. From the gallery the oil flows through drilled passages to the main bearing bores and then through the crankshaft passages to the big end (rod) bearings. The small end (rod) bearings, cylinder liners and pistons get splash lubrication from the big end (rod) bearings.The camshaft front bearing and journals are lubricated from numbers 1, 3 and 5 main bearings. The camshaft center journal supplies a controlled amount of oil to the rocker shaft assembly. Oil from the rocker shaft drains through a bleed hole in each rocker lever to lubricate the valves, guides, tappets (valve lifters) and cam lobes.
Timing Gears
(6) Idler gear. (7) Idler gear retainer plate.Oil also goes from the gallery through the rear of idler gear (6) hub, then through passages to lubricate the idler gear bearing and gear retainer plate (7). On engines equipped with hydraulic governed fuel injection pumps, the fuel pump adapter plate is also lubricated from the main oil gallery. The timing gears are splash lubricated from the idler gear hub.
Oil Lubrication SchematicAir Inlet And Exhaust System
Air Inlet Components
(1) Intake manifold. (2) Exhaust manifold.
Air Inlet Components
(3) Air cleaner.The air inlet and exhaust system components are: air cleaner (3), intake manifold (1), an air inlet hose, an air indicator, the cylinder head valves and valve mechanism components, exhaust manifold (2), pipe and muffler.Air is pulled in the air inlet system by the intake stroke of the piston. The air flows in air cleaner (3), through air inlet hose that directs the volume of air to intake manifold (1). The air flows through intake manifold (1) which directs even distribution of the air to each cylinder where the air is mixed with fuel from the injectors. The sequence and action of the engines' four cylinders and four strokes, (compression, power, exhaust and intake) give constant air flow to the intake system for engine operation.An air indicator located on the air inlet hose shows a red indication when too much air restriction (dirt)
The machine is equipped with a power shift transmission. A transmission oil cooler is installed in the outlet section of the radiator. The radiator coolant flows around the tubes of the cooler and cools the transmission oil as it flows through the cooler. The transmission oil then returns to the transmission inlet.Lubrication System
Oil Pump
(1) Strainer. (2) Oil pump relief valve. (3) Oil pump. (4) Idler gear. (5) Crankshaft gear.The lubrication system is the pressure type and the flow of oil goes from the oil pan through strainer (1) into oil pump (3). Oil pump (3) is driven by crankshaft gear (5) through the idler gear (4). The oil pump is connected to the front main bearing cap. Relief valve (2) which is spring loaded controls the maximum oil pressure. An oil pressure sending unit is connected to the main oil gallery.Oil under pressure goes from the oil pump through the relief valve, oil filter and into the main oil gallery that is a drilled passage the length of the crankcase. From the gallery the oil flows through drilled passages to the main bearing bores and then through the crankshaft passages to the big end (rod) bearings. The small end (rod) bearings, cylinder liners and pistons get splash lubrication from the big end (rod) bearings.The camshaft front bearing and journals are lubricated from numbers 1, 3 and 5 main bearings. The camshaft center journal supplies a controlled amount of oil to the rocker shaft assembly. Oil from the rocker shaft drains through a bleed hole in each rocker lever to lubricate the valves, guides, tappets (valve lifters) and cam lobes.
Timing Gears
(6) Idler gear. (7) Idler gear retainer plate.Oil also goes from the gallery through the rear of idler gear (6) hub, then through passages to lubricate the idler gear bearing and gear retainer plate (7). On engines equipped with hydraulic governed fuel injection pumps, the fuel pump adapter plate is also lubricated from the main oil gallery. The timing gears are splash lubricated from the idler gear hub.
Oil Lubrication SchematicAir Inlet And Exhaust System
Air Inlet Components
(1) Intake manifold. (2) Exhaust manifold.
Air Inlet Components
(3) Air cleaner.The air inlet and exhaust system components are: air cleaner (3), intake manifold (1), an air inlet hose, an air indicator, the cylinder head valves and valve mechanism components, exhaust manifold (2), pipe and muffler.Air is pulled in the air inlet system by the intake stroke of the piston. The air flows in air cleaner (3), through air inlet hose that directs the volume of air to intake manifold (1). The air flows through intake manifold (1) which directs even distribution of the air to each cylinder where the air is mixed with fuel from the injectors. The sequence and action of the engines' four cylinders and four strokes, (compression, power, exhaust and intake) give constant air flow to the intake system for engine operation.An air indicator located on the air inlet hose shows a red indication when too much air restriction (dirt)
Have questions with 106673-7281?
Group cross 106673-7281 ZEXEL
Mitsubishi
Mitsubishi
Mitsubishi
Mitsubishi
Mitsubishi
Mitsubishi
Mitsubishi
106673-7281
INJECTION-PUMP ASSEMBLY