Information injection-pump assembly
BOSCH
9 400 613 196
9400613196
ZEXEL
106673-4250
1066734250
KOMATSU
6152721480
6152721480
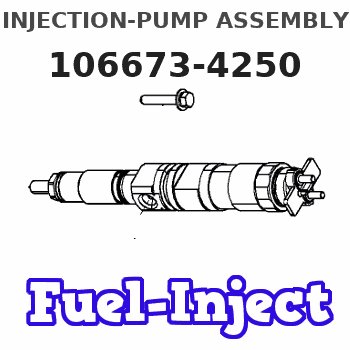
Rating:
Service parts 106673-4250 INJECTION-PUMP ASSEMBLY:
1.
_
7.
COUPLING PLATE
8.
_
9.
_
11.
Nozzle and Holder
12.
Open Pre:MPa(Kqf/cm2)
27.5{280}
15.
NOZZLE SET
Include in #1:
106673-4250
as INJECTION-PUMP ASSEMBLY
Cross reference number
BOSCH
9 400 613 196
9400613196
ZEXEL
106673-4250
1066734250
KOMATSU
6152721480
6152721480
Zexel num
Bosch num
Firm num
Name
106673-4250
9 400 613 196
6152721480 KOMATSU
INJECTION-PUMP ASSEMBLY
SAA6D125 K 14CA INJECTION PUMP ASSY PE6P,6PD PE
SAA6D125 K 14CA INJECTION PUMP ASSY PE6P,6PD PE
Calibration Data:
Adjustment conditions
Test oil
1404 Test oil ISO4113 or {SAEJ967d}
1404 Test oil ISO4113 or {SAEJ967d}
Test oil temperature
degC
40
40
45
Nozzle and nozzle holder
105780-8140
Bosch type code
EF8511/9A
Nozzle
105780-0000
Bosch type code
DN12SD12T
Nozzle holder
105780-2080
Bosch type code
EF8511/9
Opening pressure
MPa
17.2
Opening pressure
kgf/cm2
175
Injection pipe
Outer diameter - inner diameter - length (mm) mm 8-3-600
Outer diameter - inner diameter - length (mm) mm 8-3-600
Overflow valve
131424-1520
Overflow valve opening pressure
kPa
157
123
191
Overflow valve opening pressure
kgf/cm2
1.6
1.25
1.95
Tester oil delivery pressure
kPa
157
157
157
Tester oil delivery pressure
kgf/cm2
1.6
1.6
1.6
Direction of rotation (viewed from drive side)
Left L
Left L
Injection timing adjustment
Direction of rotation (viewed from drive side)
Left L
Left L
Injection order
1-5-3-6-
2-4
Pre-stroke
mm
4.5
4.45
4.55
Rack position
Point A or more. R=A
Point A or more. R=A
Beginning of injection position
Drive side NO.1
Drive side NO.1
Difference between angles 1
Cal 1-5 deg. 60 59.5 60.5
Cal 1-5 deg. 60 59.5 60.5
Difference between angles 2
Cal 1-3 deg. 120 119.5 120.5
Cal 1-3 deg. 120 119.5 120.5
Difference between angles 3
Cal 1-6 deg. 180 179.5 180.5
Cal 1-6 deg. 180 179.5 180.5
Difference between angles 4
Cyl.1-2 deg. 240 239.5 240.5
Cyl.1-2 deg. 240 239.5 240.5
Difference between angles 5
Cal 1-4 deg. 300 299.5 300.5
Cal 1-4 deg. 300 299.5 300.5
Injection quantity adjustment
Adjusting point
A
Rack position
12.9
Pump speed
r/min
1025
1025
1025
Average injection quantity
mm3/st.
191.5
189.5
193.5
Max. variation between cylinders
%
0
-3
3
Basic
*
Fixing the lever
*
Boost pressure
kPa
60
60
Boost pressure
mmHg
450
450
Injection quantity adjustment_02
Adjusting point
C
Rack position
6.6+-0.5
Pump speed
r/min
350
350
350
Average injection quantity
mm3/st.
18
16.5
19.5
Max. variation between cylinders
%
0
-15
15
Fixing the rack
*
Boost pressure
kPa
0
0
0
Boost pressure
mmHg
0
0
0
Injection quantity adjustment_03
Adjusting point
D
Rack position
13.1++
Pump speed
r/min
100
100
100
Average injection quantity
mm3/st.
170
165
175
Fixing the lever
*
Boost pressure
kPa
0
0
0
Boost pressure
mmHg
0
0
0
Rack limit
*
Boost compensator adjustment
Pump speed
r/min
600
600
600
Rack position
R1-2.1
Boost pressure
kPa
9.3
8
10.6
Boost pressure
mmHg
70
60
80
Boost compensator adjustment_02
Pump speed
r/min
600
600
600
Rack position
R1(12.9)
Boost pressure
kPa
46.7
46.7
46.7
Boost pressure
mmHg
350
350
350
Timer adjustment
Pump speed
r/min
825--
Advance angle
deg.
0
0
0
Remarks
Start
Start
Timer adjustment_02
Pump speed
r/min
775
Advance angle
deg.
0.3
Timer adjustment_03
Pump speed
r/min
975
Advance angle
deg.
2
1.7
2.3
Remarks
Finish
Finish
Test data Ex:
Governor adjustment
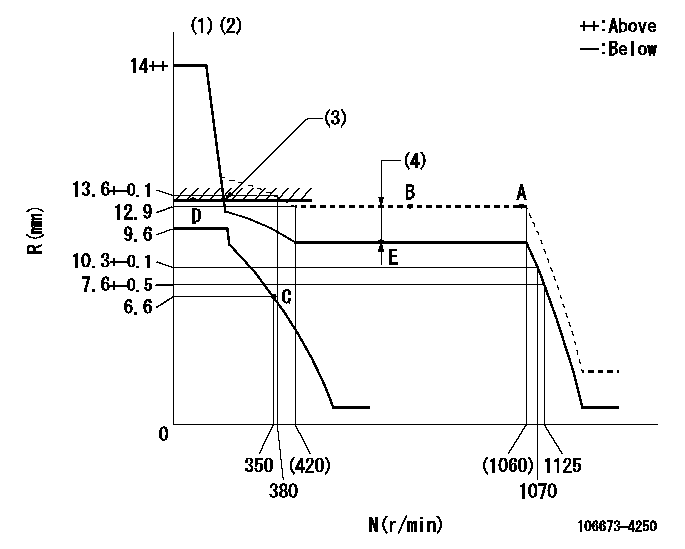
N:Pump speed
R:Rack position (mm)
(1)Target notch: K
(2)Tolerance for racks not indicated: +-0.05mm.
(3)RACK LIMIT
(4)Boost compensator stroke: BCL
----------
K=7 BCL=2.1+-0.1mm
----------
----------
K=7 BCL=2.1+-0.1mm
----------
Speed control lever angle
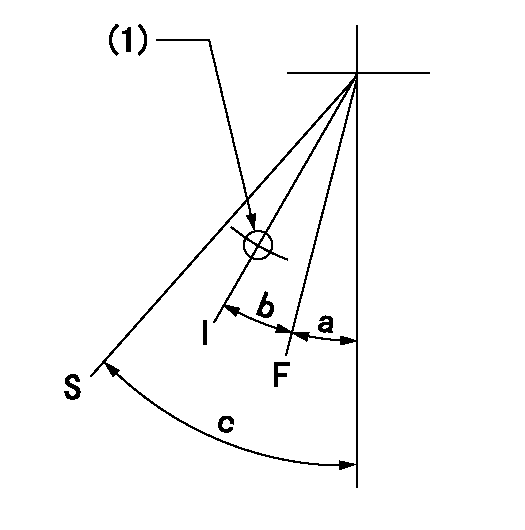
F:Full speed
I:Idle
S:Stop
(1)At hole at R = aa (center)
----------
aa=85mm
----------
a=2deg+-5deg b=24.5deg+-5deg c=35deg+-3deg
----------
aa=85mm
----------
a=2deg+-5deg b=24.5deg+-5deg c=35deg+-3deg
0000001501 TAMPER PROOF

Tamperproofing-equipped boost compensator cover installation procedure
(A) After adjusting the boost compensator, tighten the bolts to remove the heads.
(1)Before adjusting the governor and the boost compensator, tighten the screw to the specified torque.
(Tightening torque T = T1 maximum)
(2)After adjusting the governor and the boost compensator, tighten to the specified torque to break off the bolt heads.
(Tightening torque T = T2)
----------
T1=2.5N-m(0.25kgf-m) T2=2.9~4.4N-m(0.3~0.45kgf-m)
----------
----------
T1=2.5N-m(0.25kgf-m) T2=2.9~4.4N-m(0.3~0.45kgf-m)
----------
Timing setting

(1)Pump vertical direction
(2)Coupling's key groove position at No 1 cylinder's beginning of injection
(3)B.T.D.C.: aa
(4)At rack position = bb or more
----------
aa=8.5deg bb=12.9mm
----------
a=(150deg)
----------
aa=8.5deg bb=12.9mm
----------
a=(150deg)
Information:
Start By:a. remove fuel injection lines 1. Remove bolt (1) and clamp (2) from the fuel injection nozzles to be removed.2. Install Tool (A) with the inside lip of the puller on the lower stepped diameter of the nozzle and the tip of the button in the threaded hole for bolt (1).
Do not exceed a torque of 17 N m (150 lb in) on the screw of Tool (A) during removal of the nozzle. Added force can cause the stem of the nozzle to bend or break off.
3. Tighten the screw of Tool (A) to a maximum torque of 17 N m (150 lb in) to remove fuel injection nozzle (3).4. If the fuel injection nozzle can not be removed with a maximum torque of 17 N m (150 lb in) on the screw of Tool (A), remove Tool (A).
Typical Example5. Remove the protective cap from fuel injection nozzle (3), and install Tool (B) as shown.
Hold Tool (B) so the center line of the tool is in alignment with the centerline of fuel injection nozzle (3). This will prevent distortion of the nozzle which can cause it to bend or break off during removal.
6. Remove the fuel injection nozzle with Tool (B).7. If Tool (B) was used to remove the fuel injection nozzle, replace the nozzle.8. If Tool (A) was used to remove the fuel injection nozzle, remove the carbon dam seal on the end of the nozzle.Install Fuel Injection Nozzle
1. Use Tool (C) to clean the bore for the fuel injection nozzle. Use an open end wrench or tap driver to turn Tool (C).2. Make reference to Special Instruction, Form No. SEHS7292, for the use of Tool (D). Clean the fuel injection nozzle with Tool (D). 3. Install a new seal (4) on fuel injection nozzle (3).4. Put carbon dam seal (5) on the small end of Tool (E). Expand the carbon dam seal by sliding it to the large end. Put Tool (E) against the fuel injection nozzle. Slide carbon dam seal (5) off Tool (E) on to the nozzle. Slide the carbon dam seal into position in the groove on the nozzle as shown. 5. Put fuel injection nozzle (3) in position in the cylinder head. Install clamp (2) and bolt (1) to hold the nozzle in position.End By:a. install fuel injection lines
Do not exceed a torque of 17 N m (150 lb in) on the screw of Tool (A) during removal of the nozzle. Added force can cause the stem of the nozzle to bend or break off.
3. Tighten the screw of Tool (A) to a maximum torque of 17 N m (150 lb in) to remove fuel injection nozzle (3).4. If the fuel injection nozzle can not be removed with a maximum torque of 17 N m (150 lb in) on the screw of Tool (A), remove Tool (A).
Typical Example5. Remove the protective cap from fuel injection nozzle (3), and install Tool (B) as shown.
Hold Tool (B) so the center line of the tool is in alignment with the centerline of fuel injection nozzle (3). This will prevent distortion of the nozzle which can cause it to bend or break off during removal.
6. Remove the fuel injection nozzle with Tool (B).7. If Tool (B) was used to remove the fuel injection nozzle, replace the nozzle.8. If Tool (A) was used to remove the fuel injection nozzle, remove the carbon dam seal on the end of the nozzle.Install Fuel Injection Nozzle
1. Use Tool (C) to clean the bore for the fuel injection nozzle. Use an open end wrench or tap driver to turn Tool (C).2. Make reference to Special Instruction, Form No. SEHS7292, for the use of Tool (D). Clean the fuel injection nozzle with Tool (D). 3. Install a new seal (4) on fuel injection nozzle (3).4. Put carbon dam seal (5) on the small end of Tool (E). Expand the carbon dam seal by sliding it to the large end. Put Tool (E) against the fuel injection nozzle. Slide carbon dam seal (5) off Tool (E) on to the nozzle. Slide the carbon dam seal into position in the groove on the nozzle as shown. 5. Put fuel injection nozzle (3) in position in the cylinder head. Install clamp (2) and bolt (1) to hold the nozzle in position.End By:a. install fuel injection lines
Have questions with 106673-4250?
Group cross 106673-4250 ZEXEL
Daewoo
Komatsu
Komatsu
106673-4250
9 400 613 196
6152721480
INJECTION-PUMP ASSEMBLY
SAA6D125
SAA6D125