Information injection-pump assembly
BOSCH
9 400 617 303
9400617303
ZEXEL
106673-3341
1066733341
HINO
220206121A
220206121a
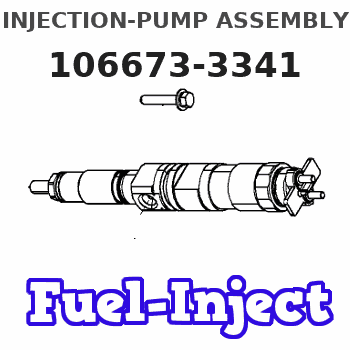
Rating:
Cross reference number
BOSCH
9 400 617 303
9400617303
ZEXEL
106673-3341
1066733341
HINO
220206121A
220206121a
Zexel num
Bosch num
Firm num
Name
9 400 617 303
220206121A HINO
INJECTION-PUMP ASSEMBLY
P09C-T * K 14CA PE6P,6PD PE
P09C-T * K 14CA PE6P,6PD PE
Calibration Data:
Adjustment conditions
Test oil
1404 Test oil ISO4113 or {SAEJ967d}
1404 Test oil ISO4113 or {SAEJ967d}
Test oil temperature
degC
40
40
45
Nozzle and nozzle holder
105780-8140
Bosch type code
EF8511/9A
Nozzle
105780-0000
Bosch type code
DN12SD12T
Nozzle holder
105780-2080
Bosch type code
EF8511/9
Opening pressure
MPa
17.2
Opening pressure
kgf/cm2
175
Injection pipe
Outer diameter - inner diameter - length (mm) mm 8-3-600
Outer diameter - inner diameter - length (mm) mm 8-3-600
Overflow valve
134424-1420
Overflow valve opening pressure
kPa
162
147
177
Overflow valve opening pressure
kgf/cm2
1.65
1.5
1.8
Tester oil delivery pressure
kPa
157
157
157
Tester oil delivery pressure
kgf/cm2
1.6
1.6
1.6
Direction of rotation (viewed from drive side)
Right R
Right R
Injection timing adjustment
Direction of rotation (viewed from drive side)
Right R
Right R
Injection order
1-4-2-6-
3-5
Pre-stroke
mm
3.9
3.8
3.9
Beginning of injection position
Drive side NO.1
Drive side NO.1
Difference between angles 1
Cal 1-4 deg. 60 59.5 60.5
Cal 1-4 deg. 60 59.5 60.5
Difference between angles 2
Cyl.1-2 deg. 120 119.5 120.5
Cyl.1-2 deg. 120 119.5 120.5
Difference between angles 3
Cal 1-6 deg. 180 179.5 180.5
Cal 1-6 deg. 180 179.5 180.5
Difference between angles 4
Cal 1-3 deg. 240 239.5 240.5
Cal 1-3 deg. 240 239.5 240.5
Difference between angles 5
Cal 1-5 deg. 300 299.5 300.5
Cal 1-5 deg. 300 299.5 300.5
Injection quantity adjustment
Adjusting point
A
Rack position
11.3
Pump speed
r/min
700
700
700
Average injection quantity
mm3/st.
151.5
149.5
153.5
Max. variation between cylinders
%
0
-3
3
Basic
*
Fixing the lever
*
Boost pressure
kPa
52
52
Boost pressure
mmHg
390
390
Injection quantity adjustment_02
Adjusting point
C
Rack position
6.5+-0.5
Pump speed
r/min
400
400
400
Average injection quantity
mm3/st.
10
7
13
Max. variation between cylinders
%
0
-15
15
Fixing the rack
*
Boost pressure
kPa
0
0
0
Boost pressure
mmHg
0
0
0
Injection quantity adjustment_03
Adjusting point
E
Rack position
11.5++
Pump speed
r/min
100
100
100
Average injection quantity
mm3/st.
135
130
140
Fixing the lever
*
Boost pressure
kPa
0
0
0
Boost pressure
mmHg
0
0
0
Rack limit
*
Boost compensator adjustment
Pump speed
r/min
600
600
600
Rack position
R1-1.95
Boost pressure
kPa
4
4
6
Boost pressure
mmHg
30
30
45
Boost compensator adjustment_02
Pump speed
r/min
600
600
600
Rack position
R1(11.3)
Boost pressure
kPa
38.7
38.7
38.7
Boost pressure
mmHg
290
290
290
Timer adjustment
Pump speed
r/min
(N1+50)-
-
Advance angle
deg.
0
0
0
Remarks
Start
Start
Timer adjustment_02
Pump speed
r/min
N1
Advance angle
deg.
0.3
Remarks
Measure the actual speed.
Measure the actual speed.
Timer adjustment_03
Pump speed
r/min
-
Advance angle
deg.
1.5
1.2
1.8
Remarks
Measure the actual speed.
Measure the actual speed.
Timer adjustment_04
Pump speed
r/min
(1100)
Advance angle
deg.
2
1.5
2.5
Remarks
Finish
Finish
Test data Ex:
Governor adjustment
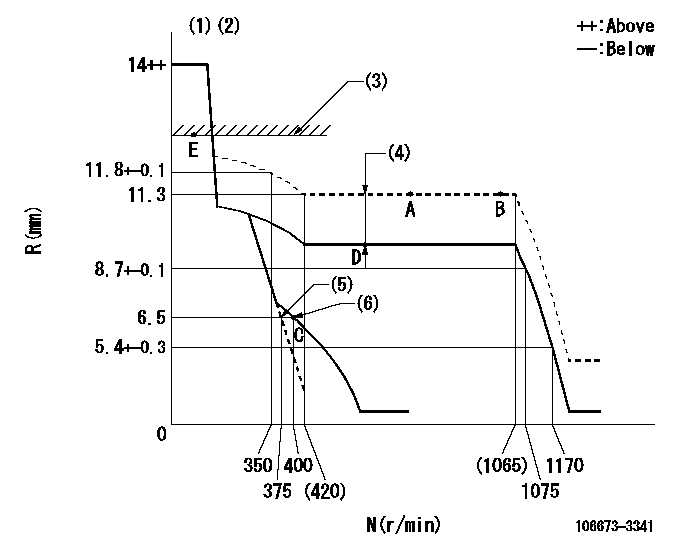
N:Pump speed
R:Rack position (mm)
(1)Target notch: K
(2)Tolerance for racks not indicated: +-0.05mm.
(3)RACK LIMIT
(4)Boost compensator stroke: BCL
(5)Main spring setting
(6)Set idle sub-spring
----------
K=14 BCL=1.95+-0.1mm
----------
----------
K=14 BCL=1.95+-0.1mm
----------
Speed control lever angle
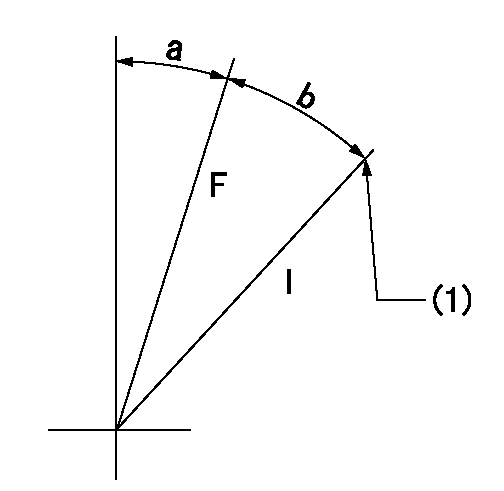
F:Full speed
I:Idle
(1)Stopper bolt setting
----------
----------
a=3deg+-5deg b=13deg+-5deg
----------
----------
a=3deg+-5deg b=13deg+-5deg
Stop lever angle
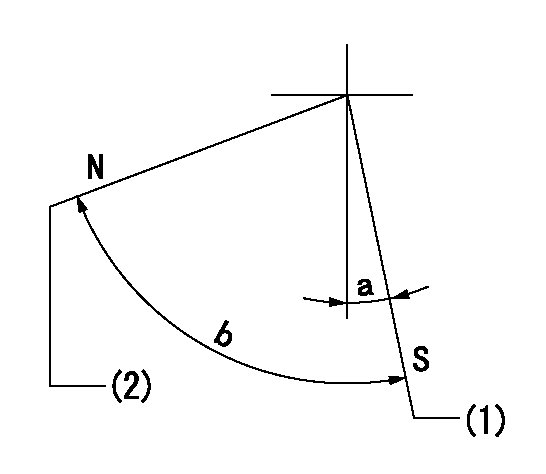
N:Pump normal
S:Stop the pump.
(1)Pump speed aa and rack position bb (to be sealed at delivery)
(2)Normal
----------
aa=0r/min bb=1-0.5mm
----------
a=10deg+-5deg b=70deg+-5deg
----------
aa=0r/min bb=1-0.5mm
----------
a=10deg+-5deg b=70deg+-5deg
0000001501 TAMPER PROOF

Tamperproofing-equipped boost compensator cover installation procedure
(A): After adjusting the boost compensator, assemble then tighten the bolts to remove the heads.
(B): Specified torque
(1)Before adjusting the governor and the boost compensator, tighten the screw to the specified torque.
(Tightening torque T = T1 maximum)
(2)After adjusting the governor and the boost compensator, tighten to the specified torque to break off the bolt heads.
(Tightening torque T = T2)
----------
T1=2.5N-m(0.25kgf-m) T2=2.9~4.4N-m(0.3~0.45kgf-m)
----------
----------
T1=2.5N-m(0.25kgf-m) T2=2.9~4.4N-m(0.3~0.45kgf-m)
----------
Timing setting
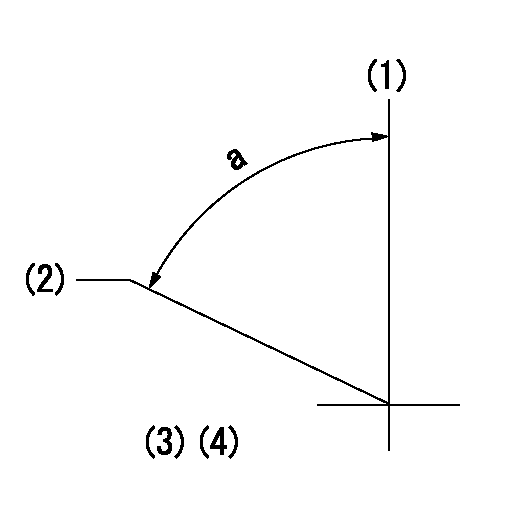
(1)Pump vertical direction
(2)Coupling's key groove position at No 1 cylinder's beginning of injection
(3)-
(4)-
----------
----------
a=(50deg)
----------
----------
a=(50deg)
Information:
3176 Electronic Governor Fuel Injection
The ECM controls the amount of fuel injected, by varying signals to the injectors. The injectors will inject fuel ONLY if the injector solenoid is energized. The ECM sends a 100 volt signal to the solenoid to energize it. By controlling the timing and duration of the 100 volt signal, the ECM can control injection timing and the amount of fuel injected.The ECM sets certain limits on the amount of fuel that can be injected. "FRC Fuel Pos" is a limit based on boost pressure to control the fuel-air ratio, for emissions control purposes. When the ECM senses a higher boost pressure (more air into cylinder), it increases the "FRC Fuel Pos" limit (allows more fuel into cylinder). "Rated Fuel Pos" is a limit based on the horsepower rating of the engine. It is similar to the rack stops and torque spring on a mechanically-governed engine. It provides horsepower and torque curves for a specific engine family and rating. All of these limits are programmed by the factory into the Personality Module and are not programmable in the field.Injection timing depends on engine rpm, load and other operation factors. The ECM knows where top-dead-center of cylinder number one is from the signal provided by the engine Speed/Timing Sensor. It decides when injection should occur relative to top-dead-center and provides the signal to the injector at the desired time.Under certain conditions, the 3176 Engine may intentionally operate on just three cylinders. This feature is called "Three Cylinder Cutout" and occurs when the engine is operated under no load, at high rpm (when signals to the injectors are of very short duration). Under these conditions, the ECM does not inject fuel into cylinders 4, 5 and 6. This allows for more precise fuel metering to cylinders 1, 2 and 3. The accompanying change in feel and sound of the engine should not be misdiagnosed as an engine problem. When more power is needed, all six cylinders will be fueled and full power delivered.Programmable Parameters
Certain parameters that affect 3176 Vehicular Diesel Engine operation may be changed through electronic service tools (either the ECAP or DDT). The parameters are stored in the ECM and passwords are used to prevent unauthorized changes.Password protected parameters are either "System Configuration Parameters" or "Customer Specified Parameters". System Configuration Parameters are set at the factory and affect emissions or horsepower ratings within a family of engines. Factory passwords must be obtained and used to change System Configuration Parameters. Customer Specified Parameters are variable and can be used to affect such things as the rpm/horsepower ratings within the limits set by the factory. Customer Passwords must be used to change Customer Specified Parameters.If the operator has not had adequate training, some parameters may affect engine operation in ways that are not expected. This may lead to power or performance complaints, even though the engine is operating correctly.Passwords
"System Configuration Parameters" are protected by factory passwords. System Configuration Parameters are those that affect horsepower family or
The ECM controls the amount of fuel injected, by varying signals to the injectors. The injectors will inject fuel ONLY if the injector solenoid is energized. The ECM sends a 100 volt signal to the solenoid to energize it. By controlling the timing and duration of the 100 volt signal, the ECM can control injection timing and the amount of fuel injected.The ECM sets certain limits on the amount of fuel that can be injected. "FRC Fuel Pos" is a limit based on boost pressure to control the fuel-air ratio, for emissions control purposes. When the ECM senses a higher boost pressure (more air into cylinder), it increases the "FRC Fuel Pos" limit (allows more fuel into cylinder). "Rated Fuel Pos" is a limit based on the horsepower rating of the engine. It is similar to the rack stops and torque spring on a mechanically-governed engine. It provides horsepower and torque curves for a specific engine family and rating. All of these limits are programmed by the factory into the Personality Module and are not programmable in the field.Injection timing depends on engine rpm, load and other operation factors. The ECM knows where top-dead-center of cylinder number one is from the signal provided by the engine Speed/Timing Sensor. It decides when injection should occur relative to top-dead-center and provides the signal to the injector at the desired time.Under certain conditions, the 3176 Engine may intentionally operate on just three cylinders. This feature is called "Three Cylinder Cutout" and occurs when the engine is operated under no load, at high rpm (when signals to the injectors are of very short duration). Under these conditions, the ECM does not inject fuel into cylinders 4, 5 and 6. This allows for more precise fuel metering to cylinders 1, 2 and 3. The accompanying change in feel and sound of the engine should not be misdiagnosed as an engine problem. When more power is needed, all six cylinders will be fueled and full power delivered.Programmable Parameters
Certain parameters that affect 3176 Vehicular Diesel Engine operation may be changed through electronic service tools (either the ECAP or DDT). The parameters are stored in the ECM and passwords are used to prevent unauthorized changes.Password protected parameters are either "System Configuration Parameters" or "Customer Specified Parameters". System Configuration Parameters are set at the factory and affect emissions or horsepower ratings within a family of engines. Factory passwords must be obtained and used to change System Configuration Parameters. Customer Specified Parameters are variable and can be used to affect such things as the rpm/horsepower ratings within the limits set by the factory. Customer Passwords must be used to change Customer Specified Parameters.If the operator has not had adequate training, some parameters may affect engine operation in ways that are not expected. This may lead to power or performance complaints, even though the engine is operating correctly.Passwords
"System Configuration Parameters" are protected by factory passwords. System Configuration Parameters are those that affect horsepower family or