Information injection-pump assembly
BOSCH
9 400 617 267
9400617267
ZEXEL
106673-2804
1066732804
MITSUBISHI
ME150598
me150598
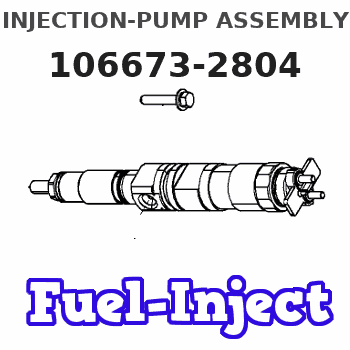
Rating:
Service parts 106673-2804 INJECTION-PUMP ASSEMBLY:
1.
_
7.
COUPLING PLATE
8.
_
9.
_
11.
Nozzle and Holder
ME056804
12.
Open Pre:MPa(Kqf/cm2)
17.7{180}/24.5{250}
15.
NOZZLE SET
Include in #1:
106673-2804
as INJECTION-PUMP ASSEMBLY
Cross reference number
BOSCH
9 400 617 267
9400617267
ZEXEL
106673-2804
1066732804
MITSUBISHI
ME150598
me150598
Zexel num
Bosch num
Firm num
Name
106673-2804
9 400 617 267
ME150598 MITSUBISHI
INJECTION-PUMP ASSEMBLY
6D22T3 * K
6D22T3 * K
Calibration Data:
Adjustment conditions
Test oil
1404 Test oil ISO4113 or {SAEJ967d}
1404 Test oil ISO4113 or {SAEJ967d}
Test oil temperature
degC
40
40
45
Nozzle and nozzle holder
105780-8140
Bosch type code
EF8511/9A
Nozzle
105780-0000
Bosch type code
DN12SD12T
Nozzle holder
105780-2080
Bosch type code
EF8511/9
Opening pressure
MPa
17.2
Opening pressure
kgf/cm2
175
Injection pipe
Outer diameter - inner diameter - length (mm) mm 8-3-600
Outer diameter - inner diameter - length (mm) mm 8-3-600
Overflow valve
131424-4620
Overflow valve opening pressure
kPa
255
221
289
Overflow valve opening pressure
kgf/cm2
2.6
2.25
2.95
Tester oil delivery pressure
kPa
157
157
157
Tester oil delivery pressure
kgf/cm2
1.6
1.6
1.6
Direction of rotation (viewed from drive side)
Right R
Right R
Injection timing adjustment
Direction of rotation (viewed from drive side)
Right R
Right R
Injection order
1-5-3-6-
2-4
Pre-stroke
mm
4.8
4.75
4.85
Beginning of injection position
Governor side NO.1
Governor side NO.1
Difference between angles 1
Cal 1-5 deg. 60 59.5 60.5
Cal 1-5 deg. 60 59.5 60.5
Difference between angles 2
Cal 1-3 deg. 120 119.5 120.5
Cal 1-3 deg. 120 119.5 120.5
Difference between angles 3
Cal 1-6 deg. 180 179.5 180.5
Cal 1-6 deg. 180 179.5 180.5
Difference between angles 4
Cyl.1-2 deg. 240 239.5 240.5
Cyl.1-2 deg. 240 239.5 240.5
Difference between angles 5
Cal 1-4 deg. 300 299.5 300.5
Cal 1-4 deg. 300 299.5 300.5
Injection quantity adjustment
Adjusting point
-
Rack position
9.9
Pump speed
r/min
650
650
650
Each cylinder's injection qty
mm3/st.
163.5
159.4
167.6
Basic
*
Fixing the rack
*
Standard for adjustment of the maximum variation between cylinders
*
Injection quantity adjustment_02
Adjusting point
G
Rack position
4.6+-0.5
Pump speed
r/min
500
500
500
Each cylinder's injection qty
mm3/st.
10
8.8
11.2
Fixing the rack
*
Standard for adjustment of the maximum variation between cylinders
*
Injection quantity adjustment_03
Adjusting point
A
Rack position
R1(9.9)
Pump speed
r/min
650
650
650
Average injection quantity
mm3/st.
163.5
162.5
164.5
Basic
*
Fixing the lever
*
Boost pressure
kPa
42.7
42.7
Boost pressure
mmHg
320
320
Injection quantity adjustment_04
Adjusting point
B
Rack position
R2(R1-1)
Pump speed
r/min
1100
1100
1100
Average injection quantity
mm3/st.
156.5
152.4
160.6
Difference in delivery
mm3/st.
8.2
8.2
8.2
Fixing the lever
*
Boost pressure
kPa
42.7
42.7
Boost pressure
mmHg
320
320
Injection quantity adjustment_05
Adjusting point
D
Rack position
R3(R1-2.
8)
Pump speed
r/min
500
500
500
Average injection quantity
mm3/st.
94
92
96
Fixing the lever
*
Boost pressure
kPa
0
0
0
Boost pressure
mmHg
0
0
0
Injection quantity adjustment_06
Adjusting point
C
Rack position
5.3+-0.5
Pump speed
r/min
225
225
225
Each cylinder's injection qty
mm3/st.
15
13.2
16.8
Fixing the rack
*
Boost pressure
kPa
0
0
0
Boost pressure
mmHg
0
0
0
Remarks
(check)
(check)
Injection quantity adjustment_07
Adjusting point
E
Rack position
-
Pump speed
r/min
100
100
100
Average injection quantity
mm3/st.
65
25
105
Fixing the lever
*
Boost pressure
kPa
0
0
0
Boost pressure
mmHg
0
0
0
Injection quantity adjustment_08
Adjusting point
F
Rack position
-
Pump speed
r/min
250
250
250
Average injection quantity
mm3/st.
175
165
185
Fixing the lever
*
Boost pressure
kPa
101
101
Boost pressure
mmHg
760
760
Rack limit
*
Boost compensator adjustment
Pump speed
r/min
500
500
500
Rack position
R3(R1-2.
8)
Boost pressure
kPa
4
3.3
4.7
Boost pressure
mmHg
30
25
35
Boost compensator adjustment_02
Pump speed
r/min
500
500
500
Rack position
R1+0.1
Boost pressure
kPa
18.7
16
21.4
Boost pressure
mmHg
140
120
160
Boost compensator adjustment_03
Pump speed
r/min
500
500
500
Rack position
(10.3)
Boost pressure
kPa
29.3
29.3
29.3
Boost pressure
mmHg
220
220
220
Timer adjustment
Pump speed
r/min
900--
Advance angle
deg.
0
0
0
Remarks
Start
Start
Timer adjustment_02
Pump speed
r/min
850
Advance angle
deg.
0.5
Timer adjustment_03
Pump speed
r/min
1100
Advance angle
deg.
1.5
1
2
Remarks
Finish
Finish
Test data Ex:
Governor adjustment
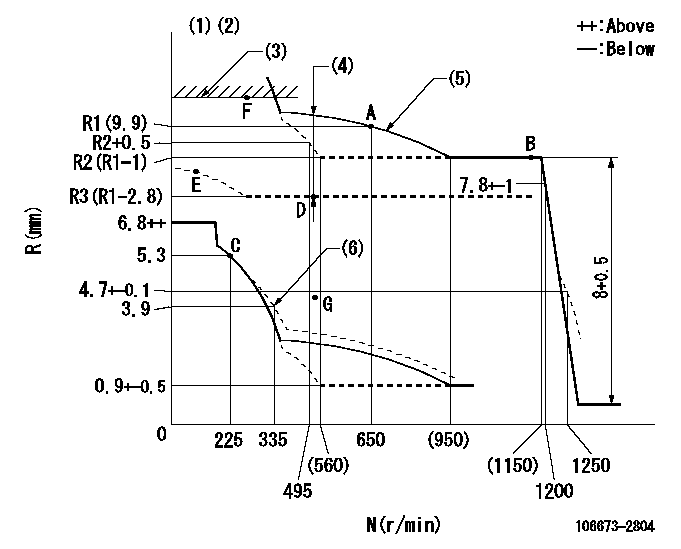
N:Pump speed
R:Rack position (mm)
(1)Tolerance for racks not indicated: +-0.05mm.
(2)Boost compensator cancel stroke: BSL
(3)RACK LIMIT
(4)Boost compensator stroke: BCL
(5)The torque control spring must does not have a set force.
(6)Damper spring setting
----------
BSL=4mm BCL=(3.2)mm
----------
----------
BSL=4mm BCL=(3.2)mm
----------
Speed control lever angle

F:Full speed
----------
----------
a=17.5deg+-5deg
----------
----------
a=17.5deg+-5deg
0000000901

F:Full load
I:Idle
(1)Stopper bolt setting
----------
----------
a=28deg+-5deg b=29.5deg+-3deg
----------
----------
a=28deg+-5deg b=29.5deg+-3deg
Stop lever angle

N:Engine manufacturer's normal use
S:Stop the pump.
(1)Rack position = aa
(2)Set the stopper bolt (seal at shipping).
(3)Rack position bb
(4)Free (at delivery)
----------
aa=3-0.5mm bb=13.3mm
----------
a=28.5deg+-5deg b=(38deg) c=1.5deg+7deg-5deg
----------
aa=3-0.5mm bb=13.3mm
----------
a=28.5deg+-5deg b=(38deg) c=1.5deg+7deg-5deg
0000001501 MICRO SWITCH
Adjustment of the micro-switch
Adjust the bolt to obtain the following lever position when the micro-switch is ON.
(1)Speed N1
(2)Rack position Ra
----------
N1=325r/min Ra=5+-0.1mm
----------
----------
N1=325r/min Ra=5+-0.1mm
----------
Timing setting

(1)Pump vertical direction
(2)Coupling's key groove position at No 1 cylinder's beginning of injection
(3)B.T.D.C.: aa
(4)-
----------
aa=12deg
----------
a=(7deg)
----------
aa=12deg
----------
a=(7deg)
Information:
4. Install a new seal washer (6).Use 6V-4979 Carbon Stop Seal Tool (4) to install new carbon dam (5) on nozzle (2).7000 Series Nozzles
The part number for compression seal (3) is not the same for all nozzles. If the correct seal is not installed, the result will be high emissions. This is NOT acceptable.
Troubleshooting (Pencil-Type Fuel Nozzles Only)
A. To troubleshoot these nozzles, refer to the Troubleshooting Guide For Pencil-Type Fuel Nozzles located in this manual.B. Refer to Special Instruction SEHS8627 "Use of 8S-2245 Nozzle Cleaning Tool Group" for the correct procedure (according to the part number of the nozzle) in order to clean these nozzles. C. If VO is LESS than the specified value for a specific part number, DO NOT use the nozzle.Troubleshooting Guide For Pencil-Type Fuel Nozzles
Troubleshooting Guide For Caterpillar 7000 Series Direct Injection Fuel Nozzles
Engine Nozzle Test Record Form (Sample Copy)
Repair/Calibration Information For 5P-4150 Tester Group
For the repair and/or calibration of the 5P-4150 Tester Group, contact the manufacturer: U.S. Mail:OTC Division
SPX Corporation
655 Eisenhower Drive
Owatonna, Minnesota 55060, U.S.A.
Telephone:(507) 455-7000(800) 533-6127 Fax:(800) 955-8329Test Equipment Calibration
Caterpillar fuel nozzle and unit injector testers feature premium quality, liquid filled gauges for high accuracy and durability.Pressure gauges, in this application must be of high quality in order to provide accurate and consistent test results.To maintain this high degree of accuracy, gauge calibration should be checked at a MINIMUM of once a year. Additional information can be found in NEHS0631 "General Maintenance And Troubleshooting For Fuel Injection Equipment Test Stands (FIETS) And 5P-4150 Nozzle Tester". However, calibration should be checked at any time when the test results have become INCONSISTENT or if the gauge needle does NOT return to the 0 (zero) range when the test pressure is relieved.Calibration
Two methods are available for gauge calibration:* Method 1: Calibration by gauge manufacturer.* Method 2: 5P-8558 Pressure Gauge Calibrating Group. Additional information can be found in NEHS0631 "General Maintenance And Troubleshooting For Fuel Injection Equipment Test Stands (FIETS) And 5P-4150 Nozzle Tester".Calibration By Gauge Manufacturer (Method 1)
Certified calibration services are offered by Carrier - Oehler Company, a Caterpillar certified supplier of premium quality gauges.The Carrier - Oehler Company can promptly check and recalibrate gauges at a low cost.The Carrier - Oehler Company will also repair and recalibrate damaged gauges at a fraction of the cost of a new gauge.When sending gauges to Carrier - Oehler Company, include the following information:* Person or department that gauges and/or correspondence is to be directed to.* List the quantity and a brief description of the gauge(s) problem or the service requested.* Dealer name and address.* Telephone number.* Fax number. The Carrier - Oehler Company will advise you if repair costs exceed 50 percent of a new gauge. Questions on costs, service, and repair time should be directed to the Caterpillar Repair Desk:(800) 321-3241 Shipping:Carrier - Oehler Company
16965 Vincennes Avenue
South Holland, Illinois 60473
U.S. Mail:Carrier - Oehler Company
Post Office Box 40
16965 Vincennes Avenue
South Holland, Illinois 60473
Telephone:(708) 339-8200 Fax:(708) 339-98305P-8558 Pressure Gauge Calibrating Group (Method 2)
(1) 5P-0946 Box Assembly.(2) 1P-2375 Quick
The part number for compression seal (3) is not the same for all nozzles. If the correct seal is not installed, the result will be high emissions. This is NOT acceptable.
Troubleshooting (Pencil-Type Fuel Nozzles Only)
A. To troubleshoot these nozzles, refer to the Troubleshooting Guide For Pencil-Type Fuel Nozzles located in this manual.B. Refer to Special Instruction SEHS8627 "Use of 8S-2245 Nozzle Cleaning Tool Group" for the correct procedure (according to the part number of the nozzle) in order to clean these nozzles. C. If VO is LESS than the specified value for a specific part number, DO NOT use the nozzle.Troubleshooting Guide For Pencil-Type Fuel Nozzles
Troubleshooting Guide For Caterpillar 7000 Series Direct Injection Fuel Nozzles
Engine Nozzle Test Record Form (Sample Copy)
Repair/Calibration Information For 5P-4150 Tester Group
For the repair and/or calibration of the 5P-4150 Tester Group, contact the manufacturer: U.S. Mail:OTC Division
SPX Corporation
655 Eisenhower Drive
Owatonna, Minnesota 55060, U.S.A.
Telephone:(507) 455-7000(800) 533-6127 Fax:(800) 955-8329Test Equipment Calibration
Caterpillar fuel nozzle and unit injector testers feature premium quality, liquid filled gauges for high accuracy and durability.Pressure gauges, in this application must be of high quality in order to provide accurate and consistent test results.To maintain this high degree of accuracy, gauge calibration should be checked at a MINIMUM of once a year. Additional information can be found in NEHS0631 "General Maintenance And Troubleshooting For Fuel Injection Equipment Test Stands (FIETS) And 5P-4150 Nozzle Tester". However, calibration should be checked at any time when the test results have become INCONSISTENT or if the gauge needle does NOT return to the 0 (zero) range when the test pressure is relieved.Calibration
Two methods are available for gauge calibration:* Method 1: Calibration by gauge manufacturer.* Method 2: 5P-8558 Pressure Gauge Calibrating Group. Additional information can be found in NEHS0631 "General Maintenance And Troubleshooting For Fuel Injection Equipment Test Stands (FIETS) And 5P-4150 Nozzle Tester".Calibration By Gauge Manufacturer (Method 1)
Certified calibration services are offered by Carrier - Oehler Company, a Caterpillar certified supplier of premium quality gauges.The Carrier - Oehler Company can promptly check and recalibrate gauges at a low cost.The Carrier - Oehler Company will also repair and recalibrate damaged gauges at a fraction of the cost of a new gauge.When sending gauges to Carrier - Oehler Company, include the following information:* Person or department that gauges and/or correspondence is to be directed to.* List the quantity and a brief description of the gauge(s) problem or the service requested.* Dealer name and address.* Telephone number.* Fax number. The Carrier - Oehler Company will advise you if repair costs exceed 50 percent of a new gauge. Questions on costs, service, and repair time should be directed to the Caterpillar Repair Desk:(800) 321-3241 Shipping:Carrier - Oehler Company
16965 Vincennes Avenue
South Holland, Illinois 60473
U.S. Mail:Carrier - Oehler Company
Post Office Box 40
16965 Vincennes Avenue
South Holland, Illinois 60473
Telephone:(708) 339-8200 Fax:(708) 339-98305P-8558 Pressure Gauge Calibrating Group (Method 2)
(1) 5P-0946 Box Assembly.(2) 1P-2375 Quick
Have questions with 106673-2804?
Group cross 106673-2804 ZEXEL
Mitsubishi
106673-2804
9 400 617 267
ME150598
INJECTION-PUMP ASSEMBLY
6D22T3
6D22T3