Information injection-pump assembly
BOSCH
9 400 617 254
9400617254
ZEXEL
106673-2650
1066732650
MITSUBISHI
ME056939
me056939
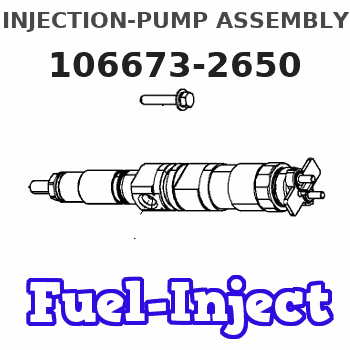
Rating:
Service parts 106673-2650 INJECTION-PUMP ASSEMBLY:
1.
_
7.
COUPLING PLATE
8.
_
9.
_
11.
Nozzle and Holder
ME056804
12.
Open Pre:MPa(Kqf/cm2)
17.7{180}/24.5{250}
15.
NOZZLE SET
Include in #1:
106673-2650
as INJECTION-PUMP ASSEMBLY
Cross reference number
BOSCH
9 400 617 254
9400617254
ZEXEL
106673-2650
1066732650
MITSUBISHI
ME056939
me056939
Zexel num
Bosch num
Firm num
Name
106673-2650
9 400 617 254
ME056939 MITSUBISHI
INJECTION-PUMP ASSEMBLY
6D22T2 * K 14CA INJECTION PUMP ASSY PE6P,6PD PE
6D22T2 * K 14CA INJECTION PUMP ASSY PE6P,6PD PE
Calibration Data:
Adjustment conditions
Test oil
1404 Test oil ISO4113 or {SAEJ967d}
1404 Test oil ISO4113 or {SAEJ967d}
Test oil temperature
degC
40
40
45
Nozzle and nozzle holder
105780-8140
Bosch type code
EF8511/9A
Nozzle
105780-0000
Bosch type code
DN12SD12T
Nozzle holder
105780-2080
Bosch type code
EF8511/9
Opening pressure
MPa
17.2
Opening pressure
kgf/cm2
175
Injection pipe
Outer diameter - inner diameter - length (mm) mm 8-3-600
Outer diameter - inner diameter - length (mm) mm 8-3-600
Overflow valve
131424-4620
Overflow valve opening pressure
kPa
255
221
289
Overflow valve opening pressure
kgf/cm2
2.6
2.25
2.95
Tester oil delivery pressure
kPa
157
157
157
Tester oil delivery pressure
kgf/cm2
1.6
1.6
1.6
Direction of rotation (viewed from drive side)
Right R
Right R
Injection timing adjustment
Direction of rotation (viewed from drive side)
Right R
Right R
Injection order
1-5-3-6-
2-4
Pre-stroke
mm
4.8
4.75
4.85
Beginning of injection position
Governor side NO.1
Governor side NO.1
Difference between angles 1
Cal 1-5 deg. 60 59.5 60.5
Cal 1-5 deg. 60 59.5 60.5
Difference between angles 2
Cal 1-3 deg. 120 119.5 120.5
Cal 1-3 deg. 120 119.5 120.5
Difference between angles 3
Cal 1-6 deg. 180 179.5 180.5
Cal 1-6 deg. 180 179.5 180.5
Difference between angles 4
Cyl.1-2 deg. 240 239.5 240.5
Cyl.1-2 deg. 240 239.5 240.5
Difference between angles 5
Cal 1-4 deg. 300 299.5 300.5
Cal 1-4 deg. 300 299.5 300.5
Injection quantity adjustment
Adjusting point
-
Rack position
9.5
Pump speed
r/min
700
700
700
Each cylinder's injection qty
mm3/st.
146
142.4
149.6
Basic
*
Fixing the rack
*
Standard for adjustment of the maximum variation between cylinders
*
Injection quantity adjustment_02
Adjusting point
F
Rack position
5+-0.5
Pump speed
r/min
500
500
500
Each cylinder's injection qty
mm3/st.
16.5
14
19
Fixing the rack
*
Standard for adjustment of the maximum variation between cylinders
*
Injection quantity adjustment_03
Adjusting point
A
Rack position
R1(9.5)
Pump speed
r/min
700
700
700
Average injection quantity
mm3/st.
146
145
147
Basic
*
Fixing the lever
*
Boost pressure
kPa
44.7
44.7
Boost pressure
mmHg
335
335
Injection quantity adjustment_04
Adjusting point
B
Rack position
R1(9.5)
Pump speed
r/min
1000
1000
1000
Average injection quantity
mm3/st.
154.8
151.6
158
Difference in delivery
mm3/st.
6.4
6.4
6.4
Fixing the lever
*
Boost pressure
kPa
44.7
44.7
Boost pressure
mmHg
335
335
Injection quantity adjustment_05
Adjusting point
D
Rack position
9.3
Pump speed
r/min
500
500
500
Average injection quantity
mm3/st.
139.5
135.5
143.5
Fixing the lever
*
Boost pressure
kPa
28
28
28
Boost pressure
mmHg
210
210
210
Injection quantity adjustment_06
Adjusting point
C
Rack position
5.7+-0.5
Pump speed
r/min
225
225
225
Each cylinder's injection qty
mm3/st.
16.5
14
19
Fixing the rack
*
Boost pressure
kPa
0
0
0
Boost pressure
mmHg
0
0
0
Remarks
(check)
(check)
Injection quantity adjustment_07
Adjusting point
E
Rack position
-
Pump speed
r/min
100
100
100
Average injection quantity
mm3/st.
125
105
145
Fixing the lever
*
Boost pressure
kPa
0
0
0
Boost pressure
mmHg
0
0
0
Boost compensator adjustment
Pump speed
r/min
600
600
600
Rack position
R2(R1-1.
6)
Boost pressure
kPa
3.3
3.3
3.3
Boost pressure
mmHg
25
25
25
Boost compensator adjustment_02
Pump speed
r/min
600
600
600
Rack position
8.55
Boost pressure
kPa
14.7
8
21.4
Boost pressure
mmHg
110
60
160
Boost compensator adjustment_03
Pump speed
r/min
600
600
600
Rack position
9.3
Boost pressure
kPa
28
26.7
29.3
Boost pressure
mmHg
210
200
220
Boost compensator adjustment_04
Pump speed
r/min
600
600
600
Rack position
R1(9.5)
Boost pressure
kPa
31.3
31.3
31.3
Boost pressure
mmHg
235
235
235
Timer adjustment
Pump speed
r/min
450--
Advance angle
deg.
0
0
0
Remarks
Start
Start
Timer adjustment_02
Pump speed
r/min
400
Advance angle
deg.
0.5
Timer adjustment_03
Pump speed
r/min
800
Advance angle
deg.
3
2.5
3.5
Remarks
Finish
Finish
Test data Ex:
Governor adjustment
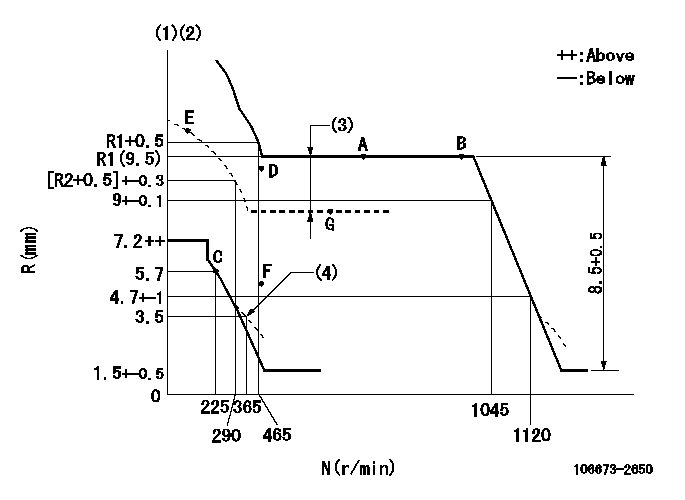
N:Pump speed
R:Rack position (mm)
(1)Tolerance for racks not indicated: +-0.05mm.
(2)Boost compensator cancel stroke: BSL
(3)Boost compensator stroke: BCL
(4)Damper spring setting
----------
BSL=2.2mm BCL=1.6+-0.1mm
----------
----------
BSL=2.2mm BCL=1.6+-0.1mm
----------
Speed control lever angle

F:Full speed
----------
----------
a=(12.5deg)+-5deg
----------
----------
a=(12.5deg)+-5deg
0000000901

F:Full load
I:Idle
(1)Stopper bolt setting
----------
----------
a=28deg+-5deg b=29.5deg+-3deg
----------
----------
a=28deg+-5deg b=29.5deg+-3deg
Stop lever angle

N:Engine manufacturer's normal use
S:Stop the pump.
(1)Rack position = aa
(2)Stopper bolt setting
(3)Rack position bb
(4)Free (at delivery)
----------
aa=4.1-0.5mm bb=13.3mm
----------
a=26deg+-5deg b=(38deg) c=0deg+7deg-5deg
----------
aa=4.1-0.5mm bb=13.3mm
----------
a=26deg+-5deg b=(38deg) c=0deg+7deg-5deg
0000001501 MICRO SWITCH
Adjustment of the micro-switch
Adjust the bolt to obtain the following lever position when the micro-switch is ON.
(1)Speed N1
(2)Rack position Ra
----------
N1=325r/min Ra=5.4+-0.1mm
----------
----------
N1=325r/min Ra=5.4+-0.1mm
----------
Timing setting

(1)Pump vertical direction
(2)Coupling's key groove position at No 1 cylinder's beginning of injection
(3)-
(4)-
----------
----------
a=(7deg)
----------
----------
a=(7deg)
Information:
Caterpillar Diesel Engines can operate effectively in cold weather. However, engine operation in cold weather is dependent on the type of fuel used and how well the fuel moves through fuel related components. The purpose of this section is to explain some of the problems and steps that can be taken to minimize fuel problems during cold weather operation, when the engine area is colder than 5°C (40°F).Radiator Restrictions
Caterpillar discourages the use of air flow restriction devices mounted in front of radiators with air-to-air aftercooled engines. Air flow restriction can cause higher exhaust temperatures, power loss, excessive fan usage, and a reduction in fuel economy.If an air flow restriction device must be used, the device should have a permanent opening directly in line with the fan hub. The device must have a minimum opening dimension of at least 770 cm2 (120 in2).A centered opening, directly in line with the fan hub, is specified to provide sensing when viscous fan drives are used and/or to prevent an interrupted air flow on the fan blades. Interrupted air flow on the fan blades could cause a fan failure.Caterpillar recommends that a package include an intake manifold temperature device, such as a light indicator, buzzer, etc., set at 65°C (150°F) and/or installation of an inlet air temperature gauge. For the ATAAC engines, air temperature in the intake manifold should not exceed 65°C (150°F). Temperatures exceeding this limit can cause power loss and potential engine damage.This temperature provides engine protection for full restriction device closure. This temperature can also serve as a diagnostic tool for a malfunction of the charge air cooling system. It is not anticipated that a temperature of 65°C (150°F) will be encountered under normal operating conditions.Fuel and the Effect from Cold Weather
The two types of diesel fuel available for your engine are typically grades No. 1 and No.2. No. 2 diesel fuel is the most commonly used fuel. No. 1 diesel fuel, or a blend of No. 1 and No. 2, is best suited for cold weather operation.Quantities of No. 1 diesel fuel are limited, and generally only available during the winter months in the colder climates. During cold weather operation, if No. 1 fuel is unavailable, it may be necessary to use No. 2 diesel fuel.There are three major differences between No. 1 and No. 2 diesel fuel. No. 1 diesel fuel has:* a lower cloud point* a lower pour point* a lower BTU (kJ) (heat content) rating per unit volume of fuel than the average No. 2 diesel fuel.When using No. 1 diesel fuel, you may notice a drop in power and fuel efficiency. You should not experience any other operating effects.The cloud point is the temperature at which a cloud or haze of wax crystals begins to form in the fuel and cause fuel filters to plug. The pour point is the temperature which diesel fuel begins to thicken and be more resistant to flow through fuel pumps and lines.Be aware of these fuel values when
Caterpillar discourages the use of air flow restriction devices mounted in front of radiators with air-to-air aftercooled engines. Air flow restriction can cause higher exhaust temperatures, power loss, excessive fan usage, and a reduction in fuel economy.If an air flow restriction device must be used, the device should have a permanent opening directly in line with the fan hub. The device must have a minimum opening dimension of at least 770 cm2 (120 in2).A centered opening, directly in line with the fan hub, is specified to provide sensing when viscous fan drives are used and/or to prevent an interrupted air flow on the fan blades. Interrupted air flow on the fan blades could cause a fan failure.Caterpillar recommends that a package include an intake manifold temperature device, such as a light indicator, buzzer, etc., set at 65°C (150°F) and/or installation of an inlet air temperature gauge. For the ATAAC engines, air temperature in the intake manifold should not exceed 65°C (150°F). Temperatures exceeding this limit can cause power loss and potential engine damage.This temperature provides engine protection for full restriction device closure. This temperature can also serve as a diagnostic tool for a malfunction of the charge air cooling system. It is not anticipated that a temperature of 65°C (150°F) will be encountered under normal operating conditions.Fuel and the Effect from Cold Weather
The two types of diesel fuel available for your engine are typically grades No. 1 and No.2. No. 2 diesel fuel is the most commonly used fuel. No. 1 diesel fuel, or a blend of No. 1 and No. 2, is best suited for cold weather operation.Quantities of No. 1 diesel fuel are limited, and generally only available during the winter months in the colder climates. During cold weather operation, if No. 1 fuel is unavailable, it may be necessary to use No. 2 diesel fuel.There are three major differences between No. 1 and No. 2 diesel fuel. No. 1 diesel fuel has:* a lower cloud point* a lower pour point* a lower BTU (kJ) (heat content) rating per unit volume of fuel than the average No. 2 diesel fuel.When using No. 1 diesel fuel, you may notice a drop in power and fuel efficiency. You should not experience any other operating effects.The cloud point is the temperature at which a cloud or haze of wax crystals begins to form in the fuel and cause fuel filters to plug. The pour point is the temperature which diesel fuel begins to thicken and be more resistant to flow through fuel pumps and lines.Be aware of these fuel values when
Have questions with 106673-2650?
Group cross 106673-2650 ZEXEL
Mitsubishi
Mitsubishi
Mitsubishi
Mitsubishi
106673-2650
9 400 617 254
ME056939
INJECTION-PUMP ASSEMBLY
6D22T2
6D22T2