Information injection-pump assembly
BOSCH
9 400 617 241
9400617241
ZEXEL
106673-2500
1066732500
MITSUBISHI
ME056898
me056898
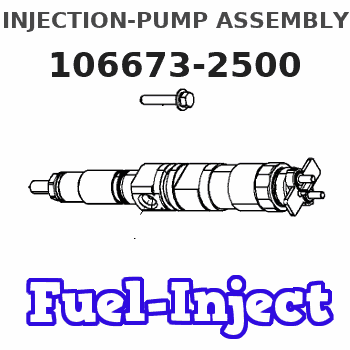
Rating:
Service parts 106673-2500 INJECTION-PUMP ASSEMBLY:
1.
_
7.
COUPLING PLATE
8.
_
9.
_
11.
Nozzle and Holder
ME056473
12.
Open Pre:MPa(Kqf/cm2)
17.7{180}/21.6{220}
15.
NOZZLE SET
Include in #1:
106673-2500
as INJECTION-PUMP ASSEMBLY
Cross reference number
BOSCH
9 400 617 241
9400617241
ZEXEL
106673-2500
1066732500
MITSUBISHI
ME056898
me056898
Zexel num
Bosch num
Firm num
Name
106673-2500
9 400 617 241
ME056898 MITSUBISHI
INJECTION-PUMP ASSEMBLY
6D22T3 * K 14CA INJECTION PUMP ASSY PE6P,6PD PE
6D22T3 * K 14CA INJECTION PUMP ASSY PE6P,6PD PE
Calibration Data:
Adjustment conditions
Test oil
1404 Test oil ISO4113 or {SAEJ967d}
1404 Test oil ISO4113 or {SAEJ967d}
Test oil temperature
degC
40
40
45
Nozzle and nozzle holder
105780-8140
Bosch type code
EF8511/9A
Nozzle
105780-0000
Bosch type code
DN12SD12T
Nozzle holder
105780-2080
Bosch type code
EF8511/9
Opening pressure
MPa
17.2
Opening pressure
kgf/cm2
175
Injection pipe
Outer diameter - inner diameter - length (mm) mm 8-3-600
Outer diameter - inner diameter - length (mm) mm 8-3-600
Overflow valve
131424-4620
Overflow valve opening pressure
kPa
255
221
289
Overflow valve opening pressure
kgf/cm2
2.6
2.25
2.95
Tester oil delivery pressure
kPa
157
157
157
Tester oil delivery pressure
kgf/cm2
1.6
1.6
1.6
Direction of rotation (viewed from drive side)
Right R
Right R
Injection timing adjustment
Direction of rotation (viewed from drive side)
Right R
Right R
Injection order
1-5-3-6-
2-4
Pre-stroke
mm
4.8
4.75
4.85
Beginning of injection position
Governor side NO.1
Governor side NO.1
Difference between angles 1
Cal 1-5 deg. 60 59.5 60.5
Cal 1-5 deg. 60 59.5 60.5
Difference between angles 2
Cal 1-3 deg. 120 119.5 120.5
Cal 1-3 deg. 120 119.5 120.5
Difference between angles 3
Cal 1-6 deg. 180 179.5 180.5
Cal 1-6 deg. 180 179.5 180.5
Difference between angles 4
Cyl.1-2 deg. 240 239.5 240.5
Cyl.1-2 deg. 240 239.5 240.5
Difference between angles 5
Cal 1-4 deg. 300 299.5 300.5
Cal 1-4 deg. 300 299.5 300.5
Injection quantity adjustment
Adjusting point
-
Rack position
10.6
Pump speed
r/min
650
650
650
Each cylinder's injection qty
mm3/st.
174.8
170.4
179.2
Basic
*
Fixing the rack
*
Standard for adjustment of the maximum variation between cylinders
*
Injection quantity adjustment_02
Adjusting point
F
Rack position
4.7+-0.5
Pump speed
r/min
500
500
500
Each cylinder's injection qty
mm3/st.
11
9.7
12.3
Fixing the rack
*
Standard for adjustment of the maximum variation between cylinders
*
Injection quantity adjustment_03
Adjusting point
A
Rack position
R1(10.6)
Pump speed
r/min
650
650
650
Average injection quantity
mm3/st.
174.8
173.8
175.8
Basic
*
Fixing the lever
*
Boost pressure
kPa
45.3
45.3
Boost pressure
mmHg
340
340
Injection quantity adjustment_04
Adjusting point
D
Rack position
R1-2.8
Pump speed
r/min
500
500
500
Average injection quantity
mm3/st.
110
106.2
113.8
Fixing the lever
*
Boost pressure
kPa
0
0
0
Boost pressure
mmHg
0
0
0
Injection quantity adjustment_05
Adjusting point
C
Rack position
5.3+-0.5
Pump speed
r/min
225
225
225
Each cylinder's injection qty
mm3/st.
15
13.2
16.8
Fixing the rack
*
Boost pressure
kPa
0
0
0
Boost pressure
mmHg
0
0
0
Remarks
(check)
(check)
Injection quantity adjustment_06
Adjusting point
E
Rack position
-
Pump speed
r/min
100
100
100
Average injection quantity
mm3/st.
94
54
134
Fixing the lever
*
Boost pressure
kPa
0
0
0
Boost pressure
mmHg
0
0
0
Boost compensator adjustment
Pump speed
r/min
600
600
600
Rack position
R2(R1-2.
8)
Boost pressure
kPa
3.3
3.3
5.3
Boost pressure
mmHg
25
25
40
Boost compensator adjustment_02
Pump speed
r/min
600
600
600
Rack position
R1-0.1
Boost pressure
kPa
21.3
20
22.6
Boost pressure
mmHg
160
150
170
Boost compensator adjustment_03
Pump speed
r/min
600
600
600
Rack position
(10.8)
Boost pressure
kPa
32
32
32
Boost pressure
mmHg
240
240
240
Timer adjustment
Pump speed
r/min
900--
Advance angle
deg.
0
0
0
Remarks
Start
Start
Timer adjustment_02
Pump speed
r/min
850
Advance angle
deg.
0.5
Timer adjustment_03
Pump speed
r/min
1075
Remarks
Measure the actual advance angle.
Measure the actual advance angle.
Timer adjustment_04
Pump speed
r/min
-
Advance angle
deg.
1.5
1
2
Remarks
Measure the actual speed, stop
Measure the actual speed, stop
Test data Ex:
Governor adjustment
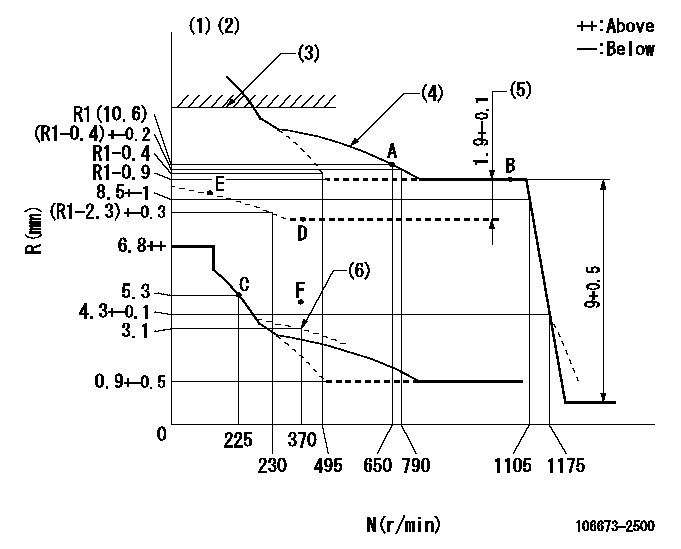
N:Pump speed
R:Rack position (mm)
(1)Tolerance for racks not indicated: +-0.05mm.
(2)Boost compensator cancel stroke: BSL
(3)RACK LIMIT: RAL
(4)The torque control spring must does not have a set force.
(5)Boost compensator stroke (at N = N1)
(6)Damper spring setting
----------
BSL=3.4mm RAL=11.4+-0.1mm N1=1000r/min
----------
----------
BSL=3.4mm RAL=11.4+-0.1mm N1=1000r/min
----------
Speed control lever angle

F:Full speed
----------
----------
a=13deg+-5deg
----------
----------
a=13deg+-5deg
0000000901

F:Full load
I:Idle
(1)Stopper bolt setting
----------
----------
a=28deg+-5deg b=32deg+-3deg
----------
----------
a=28deg+-5deg b=32deg+-3deg
Stop lever angle

N:Engine manufacturer's normal use
S:Stop the pump.
(1)Rack position = aa
(2)Stopper bolt setting
(3)Rack position bb
(4)Free (at shipping)
----------
aa=3-0.5mm bb=13.3mm
----------
a=28.5deg+-5deg b=(38deg) c=1.5deg+7deg-5deg
----------
aa=3-0.5mm bb=13.3mm
----------
a=28.5deg+-5deg b=(38deg) c=1.5deg+7deg-5deg
0000001501 MICRO SWITCH
Adjustment of the micro-switch
Adjust the bolt to obtain the following lever position when the micro-switch is ON.
(1)Speed N1
(2)Rack position Ra
----------
N1=325r/min Ra=5+-0.1mm
----------
----------
N1=325r/min Ra=5+-0.1mm
----------
Timing setting

(1)Pump vertical direction
(2)Coupling's key groove position at No 1 cylinder's beginning of injection
(3)-
(4)-
----------
----------
a=(7deg)
----------
----------
a=(7deg)
Information:
Test
Set up as illustrated and turn the alternator to measure vacuum pump performance. If the measurement is lower than nominal values, disassemble and check for broken vane, traces of interference on housing, rotor and plate surfaces. Replace if defective.Ultimate vacuum Exhaust characteristics after 20 seconds 4.9 Safety Relay
(1) R8T30171 Safety Relay Inspection Measure voltage at each terminal in the sequence shown below to identify faulty parts.(a) On-vehicle Test (b) Component TestThe resistance value between terminals "R" and "L" shall be within specified range.(2) Inspection by RX-Q30 Safety Relay Continuity Tester Check between terminals marked with * applying 15 to 17 V between "K" and "E" terminals.4.10 Preheater
Intake air heater
(1) Removal and installation (Refer to Group 15 Intake and Exhaust.)(2) Inspection Perform the following inspection and check the function of each part or the wiring if necessary.(a) Time required before indicator becomes red-hot: Standard timeNominal value 40 to 60 seconds (ME037260, ME037197:1.83 kW)20 to 30 seconds (ME077014, ME077015:2.86 kW)(b) Check each terminal of the air heater for looseness and the heater element for damage and contact with other parts.Heater relay
Inspection (1) Check to ensure that there is continuity between the terminals "B" and "S" when 2.3 A (24 V type) or 5.2 A (12 V type) exciting current is applied between terminal "SW" in the illustration and body ground.(2) Check also the heater relay fuse and replace if it has been burnt out. When replacing fuses, be sure to use a fuse of specified capacity.4.11 Automatic Stop Device
Energize-to-stop type
(1) Stop solenoid (a) Connect the stop lever and solenoid using the rod and remove the solenoid cover.(b) Push manually the stop lever to the stop position and adjust the rod so that the solenoid pointer gap becomes as specified.(c) Check that the stop lever to external stopper clearance is as specified when the stop lever is on the operation side.(d) In the state of (c) above, apply specified voltage to solenoid "B" terminal and check that the pointer gap and ammeter reading are as specified. (Stop lever stop side)(e) Tighten the lock nut of the rod.(f) Check that the solenoid pointer color has not changed and then install the cover.(2) Solenoid relay Make connections as shown above and perform the following checks.(a) Oil pressure timerSet the snap switch A to ON. Operate a stop watch as soon as the snap switch B is set to ON, and measure the time required before the solenoid is operated.(b) Stop timerSet the snap switch B to OFF 5 seconds after the solenoid has been operated. At the same time, using a stop watch, measure the time required before the solenoid is reset.The snap switch B is set to OFF 5 seconds after operation of the solenoid because if the solenoid is operated, it takes 5 seconds before the alternator voltage disappears.(c) Manual stop timerWhen the push switch C (stop switch) is set to ON, the solenoid is operated. Operate a stop watch as soon as the stop switch C is set to
Set up as illustrated and turn the alternator to measure vacuum pump performance. If the measurement is lower than nominal values, disassemble and check for broken vane, traces of interference on housing, rotor and plate surfaces. Replace if defective.Ultimate vacuum Exhaust characteristics after 20 seconds 4.9 Safety Relay
(1) R8T30171 Safety Relay Inspection Measure voltage at each terminal in the sequence shown below to identify faulty parts.(a) On-vehicle Test (b) Component TestThe resistance value between terminals "R" and "L" shall be within specified range.(2) Inspection by RX-Q30 Safety Relay Continuity Tester Check between terminals marked with * applying 15 to 17 V between "K" and "E" terminals.4.10 Preheater
Intake air heater
(1) Removal and installation (Refer to Group 15 Intake and Exhaust.)(2) Inspection Perform the following inspection and check the function of each part or the wiring if necessary.(a) Time required before indicator becomes red-hot: Standard timeNominal value 40 to 60 seconds (ME037260, ME037197:1.83 kW)20 to 30 seconds (ME077014, ME077015:2.86 kW)(b) Check each terminal of the air heater for looseness and the heater element for damage and contact with other parts.Heater relay
Inspection (1) Check to ensure that there is continuity between the terminals "B" and "S" when 2.3 A (24 V type) or 5.2 A (12 V type) exciting current is applied between terminal "SW" in the illustration and body ground.(2) Check also the heater relay fuse and replace if it has been burnt out. When replacing fuses, be sure to use a fuse of specified capacity.4.11 Automatic Stop Device
Energize-to-stop type
(1) Stop solenoid (a) Connect the stop lever and solenoid using the rod and remove the solenoid cover.(b) Push manually the stop lever to the stop position and adjust the rod so that the solenoid pointer gap becomes as specified.(c) Check that the stop lever to external stopper clearance is as specified when the stop lever is on the operation side.(d) In the state of (c) above, apply specified voltage to solenoid "B" terminal and check that the pointer gap and ammeter reading are as specified. (Stop lever stop side)(e) Tighten the lock nut of the rod.(f) Check that the solenoid pointer color has not changed and then install the cover.(2) Solenoid relay Make connections as shown above and perform the following checks.(a) Oil pressure timerSet the snap switch A to ON. Operate a stop watch as soon as the snap switch B is set to ON, and measure the time required before the solenoid is operated.(b) Stop timerSet the snap switch B to OFF 5 seconds after the solenoid has been operated. At the same time, using a stop watch, measure the time required before the solenoid is reset.The snap switch B is set to OFF 5 seconds after operation of the solenoid because if the solenoid is operated, it takes 5 seconds before the alternator voltage disappears.(c) Manual stop timerWhen the push switch C (stop switch) is set to ON, the solenoid is operated. Operate a stop watch as soon as the stop switch C is set to
Have questions with 106673-2500?
Group cross 106673-2500 ZEXEL
Mitsubishi
106673-2500
9 400 617 241
ME056898
INJECTION-PUMP ASSEMBLY
6D22T3
6D22T3