Information injection-pump assembly
ZEXEL
106672-9860
1066729860
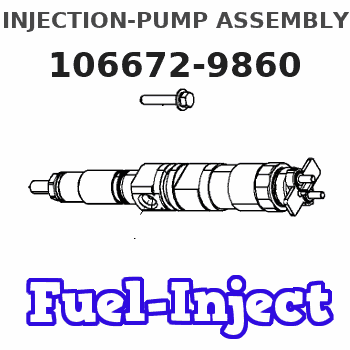
Rating:
Service parts 106672-9860 INJECTION-PUMP ASSEMBLY:
1.
_
5.
AUTOM. ADVANCE MECHANIS
7.
COUPLING PLATE
8.
_
9.
_
11.
Nozzle and Holder
6138-12-3700
12.
Open Pre:MPa(Kqf/cm2)
24.5{250}
15.
NOZZLE SET
Include in #1:
106672-9860
as INJECTION-PUMP ASSEMBLY
Cross reference number
ZEXEL
106672-9860
1066729860
Zexel num
Bosch num
Firm num
Name
106672-9860
INJECTION-PUMP ASSEMBLY
Calibration Data:
Adjustment conditions
Test oil
1404 Test oil ISO4113 or {SAEJ967d}
1404 Test oil ISO4113 or {SAEJ967d}
Test oil temperature
degC
40
40
45
Nozzle and nozzle holder
105780-8140
Bosch type code
EF8511/9A
Nozzle
105780-0000
Bosch type code
DN12SD12T
Nozzle holder
105780-2080
Bosch type code
EF8511/9
Opening pressure
MPa
17.2
Opening pressure
kgf/cm2
175
Injection pipe
Outer diameter - inner diameter - length (mm) mm 8-3-600
Outer diameter - inner diameter - length (mm) mm 8-3-600
Overflow valve (drive side)
131424-1520
Overflow valve opening pressure (drive side)
kPa
157
123
191
Overflow valve opening pressure (drive side)
kgf/cm2
1.6
1.25
1.95
Overflow valve (governor side)
134424-2320
Overflow valve opening pressure (governor side)
kPa
157
123
191
Overflow valve opening pressure (governor side)
kgf/cm2
1.6
1.25
1.95
Tester oil delivery pressure
kPa
294
294
294
Tester oil delivery pressure
kgf/cm2
3
3
3
Direction of rotation (viewed from drive side)
Right R
Right R
Injection timing adjustment
Direction of rotation (viewed from drive side)
Right R
Right R
Injection order
1-5-3-6-
2-4
Pre-stroke
mm
3.3
3.25
3.35
Beginning of injection position
Drive side NO.1
Drive side NO.1
Difference between angles 1
Cal 1-5 deg. 60 59.5 60.5
Cal 1-5 deg. 60 59.5 60.5
Difference between angles 2
Cal 1-3 deg. 120 119.5 120.5
Cal 1-3 deg. 120 119.5 120.5
Difference between angles 3
Cal 1-6 deg. 180 179.5 180.5
Cal 1-6 deg. 180 179.5 180.5
Difference between angles 4
Cyl.1-2 deg. 240 239.5 240.5
Cyl.1-2 deg. 240 239.5 240.5
Difference between angles 5
Cal 1-4 deg. 300 299.5 300.5
Cal 1-4 deg. 300 299.5 300.5
Injection quantity adjustment
Adjusting point
A
Rack position
10.8
Pump speed
r/min
1300
1300
1300
Average injection quantity
mm3/st.
116
114
118
Max. variation between cylinders
%
0
-3
3
Basic
*
Fixing the lever
*
Injection quantity adjustment_02
Adjusting point
B
Rack position
6.1+-0.5
Pump speed
r/min
225
225
225
Average injection quantity
mm3/st.
10.5
9
12
Max. variation between cylinders
%
0
-10
10
Fixing the rack
*
Test data Ex:
Governor adjustment
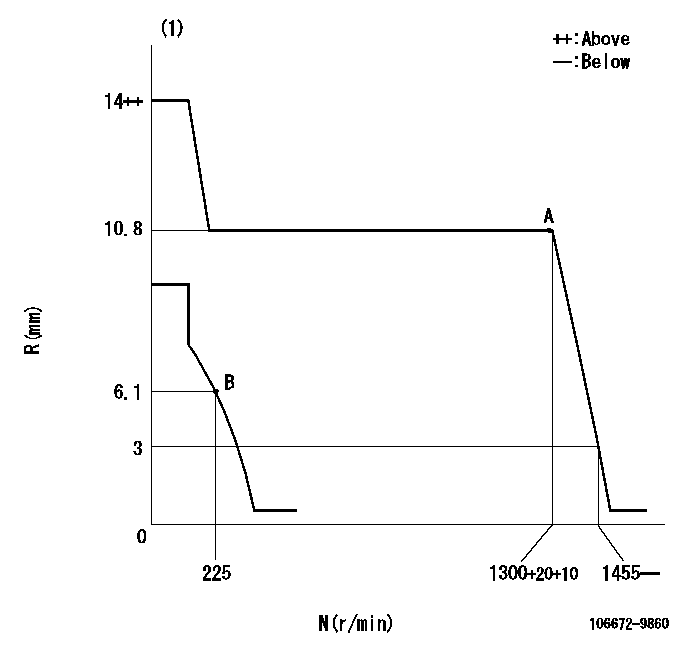
N:Pump speed
R:Rack position (mm)
(1)Target notch: K
----------
K=10
----------
----------
K=10
----------
Speed control lever angle
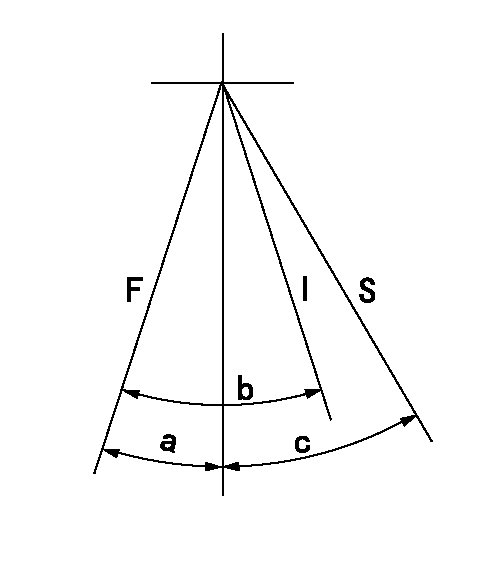
F:Full speed
I:Idle
S:Stop
----------
----------
a=19deg+-5deg b=32deg+-5deg c=25deg+-3deg
----------
----------
a=19deg+-5deg b=32deg+-5deg c=25deg+-3deg
Stop lever angle

N:Pump normal
S:Stop the pump.
----------
----------
a=27deg+-5deg b=53deg+-5deg
----------
----------
a=27deg+-5deg b=53deg+-5deg
0000001501 Q ADJUSTMENT PIPING
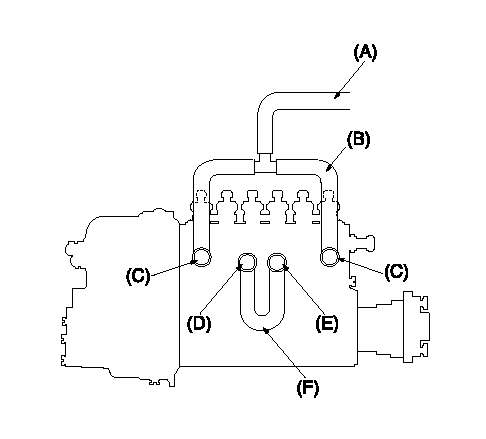
Piping at standard injection quantity adjustment
Tester fuel pipe A
(B) branch piping
Fuel inlet C
(D) With check valve and overflow valve
(E) Without overflow valve
(F) Rubber hose (L = 900mm)
----------
----------
----------
----------
Timing setting

(1)Pump vertical direction
(2)Coupling's key groove position at No 1 cylinder's beginning of injection
(3)-
(4)-
----------
----------
a=(0deg)
----------
----------
a=(0deg)
Information:
Safety is everyone's business and is basically the use of good common sense. A general guide of safety precautions are given below, but each installation has its own peculiarities which cannot always be predicted and covered by established rules. Past experience and common sense are needed for the necessary safety measures. Attention to safety will help avoid serious accidents. Be alert. Watch for hazards. Use preventive measures. Correct deficiencies immediately.The following safety precautions are a general guide to safe operation:1. To prevent personal injury, install guards over all exposed rotating parts.2. To prevent hearing damage, wear ear protective devices if working inside an enclosed engine room with engine running.3. To prevent head injury, wear safety hat when working in the area of overhead equipment.4. Wear safety glasses and shoes as required. 5. Do not wear loose clothing whenever working around engines or machinery.6. Wipe up spilled oil, fuel or coolant.7. Keep batteries in a well ventilated area. Do not smoke around batteries. Hydrogen gas, which is present in the area of the batteries, is highly explosive.8. Provide adequate and safe waste oil disposal.9. Store oily rags in fireproof containers. Don't leave rags on engine.
When using pressure air, wear safety glasses and protective clothing. Maximum air pressure, used for cleaning, must be below 30 PSI (2 kg/cm2).
10. Remove all tools, electrical cords and other loose items from the engine before starting.11. Disconnect and tape the battery ground lead before working on an engine to prevent accidental starting. Be sure an automatic start-stop system cannot operate and start the engine while working on it.12. Do not attempt repairs you do not understand. Follow instructions.13. Stop engine before adjusting or repairing engine or driven equipment.14. Remove radiator cap slowly. Cooling systems can be pressurized and hot fluid will flash to steam as pressure is removed.15. Never start an engine with the governor linkage disconnected.16. Replace or repair broken or damaged equipment. Use proper tools.17. Do not smoke while refueling. Observe NO SMOKING signs.18. Never store flammable liquids near the engine.19. All electrical equipment must be grounded according to local building codes.20. Check all connections periodically for tightness and insulation.21. Insulate all connections and disconnected wires.22. Do not use carbon tetrachloride fire extinguishers. Fumes are toxic and the liquid has a deteriorating effect on insulation. 23. Do not touch the heat sink on the generator regulator when the generator is running. It is electrically "hot".24. Do not work on electrically "hot" equipment.25. Always disconnect the engine starter circuit when working on the generator.26. Hot engine oil can cause burns when drained. Allow the oil to cool below 140°F or provide protection when draining the hot oil.27. Never remove a plug to check pressure with the engine running. Shut down the engine and assure there is no pressure before removing plug.28. When starting an engine after repair, make provisions for shutting off air supply in case there is an overspeed on start up.29. Never look into an open cylinder port and turn over
When using pressure air, wear safety glasses and protective clothing. Maximum air pressure, used for cleaning, must be below 30 PSI (2 kg/cm2).
10. Remove all tools, electrical cords and other loose items from the engine before starting.11. Disconnect and tape the battery ground lead before working on an engine to prevent accidental starting. Be sure an automatic start-stop system cannot operate and start the engine while working on it.12. Do not attempt repairs you do not understand. Follow instructions.13. Stop engine before adjusting or repairing engine or driven equipment.14. Remove radiator cap slowly. Cooling systems can be pressurized and hot fluid will flash to steam as pressure is removed.15. Never start an engine with the governor linkage disconnected.16. Replace or repair broken or damaged equipment. Use proper tools.17. Do not smoke while refueling. Observe NO SMOKING signs.18. Never store flammable liquids near the engine.19. All electrical equipment must be grounded according to local building codes.20. Check all connections periodically for tightness and insulation.21. Insulate all connections and disconnected wires.22. Do not use carbon tetrachloride fire extinguishers. Fumes are toxic and the liquid has a deteriorating effect on insulation. 23. Do not touch the heat sink on the generator regulator when the generator is running. It is electrically "hot".24. Do not work on electrically "hot" equipment.25. Always disconnect the engine starter circuit when working on the generator.26. Hot engine oil can cause burns when drained. Allow the oil to cool below 140°F or provide protection when draining the hot oil.27. Never remove a plug to check pressure with the engine running. Shut down the engine and assure there is no pressure before removing plug.28. When starting an engine after repair, make provisions for shutting off air supply in case there is an overspeed on start up.29. Never look into an open cylinder port and turn over
Have questions with 106672-9860?
Group cross 106672-9860 ZEXEL
Komatsu
Komatsu
Niigata-Urawa
Niigata-Urawa
Niigata-Urawa
Niigata-Tekkou
Komatsu
106672-9860
INJECTION-PUMP ASSEMBLY