Information injection-pump assembly
BOSCH
F 019 Z10 869
f019z10869
ZEXEL
106672-3581
1066723581
HINO
220006921A
220006921a
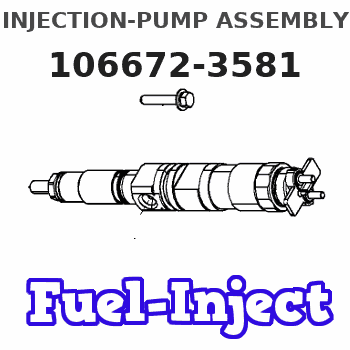
Rating:
Service parts 106672-3581 INJECTION-PUMP ASSEMBLY:
1.
_
5.
AUTOM. ADVANCE MECHANIS
9.
_
11.
Nozzle and Holder
236002260A
12.
Open Pre:MPa(Kqf/cm2)
16.7(170)/23.5(240)
14.
NOZZLE
Include in #1:
106672-3581
as INJECTION-PUMP ASSEMBLY
Cross reference number
BOSCH
F 019 Z10 869
f019z10869
ZEXEL
106672-3581
1066723581
HINO
220006921A
220006921a
Zexel num
Bosch num
Firm num
Name
Calibration Data:
Adjustment conditions
Test oil
1404 Test oil ISO4113 or {SAEJ967d}
1404 Test oil ISO4113 or {SAEJ967d}
Test oil temperature
degC
40
40
45
Nozzle and nozzle holder
105780-8140
Bosch type code
EF8511/9A
Nozzle
105780-0000
Bosch type code
DN12SD12T
Nozzle holder
105780-2080
Bosch type code
EF8511/9
Opening pressure
MPa
17.2
Opening pressure
kgf/cm2
175
Injection pipe
Outer diameter - inner diameter - length (mm) mm 8-3-600
Outer diameter - inner diameter - length (mm) mm 8-3-600
Overflow valve
134424-1420
Overflow valve opening pressure
kPa
162
147
177
Overflow valve opening pressure
kgf/cm2
1.65
1.5
1.8
Tester oil delivery pressure
kPa
157
157
157
Tester oil delivery pressure
kgf/cm2
1.6
1.6
1.6
PS/ACT control unit part no.
407980-2
24*
Digi switch no.
31
Direction of rotation (viewed from drive side)
Left L
Left L
Injection timing adjustment
Direction of rotation (viewed from drive side)
Left L
Left L
Injection order
1-4-2-6-
3-5
Pre-stroke
mm
6.4
6.37
6.43
Beginning of injection position
Drive side NO.1
Drive side NO.1
Difference between angles 1
Cal 1-4 deg. 60 59.75 60.25
Cal 1-4 deg. 60 59.75 60.25
Difference between angles 2
Cyl.1-2 deg. 120 119.75 120.25
Cyl.1-2 deg. 120 119.75 120.25
Difference between angles 3
Cal 1-6 deg. 180 179.75 180.25
Cal 1-6 deg. 180 179.75 180.25
Difference between angles 4
Cal 1-3 deg. 240 239.75 240.25
Cal 1-3 deg. 240 239.75 240.25
Difference between angles 5
Cal 1-5 deg. 300 299.75 300.25
Cal 1-5 deg. 300 299.75 300.25
Injection quantity adjustment
Adjusting point
A
Rack position
10.9
Pump speed
r/min
650
650
650
Average injection quantity
mm3/st.
199.2
197.2
201.2
Max. variation between cylinders
%
0
-2
2
Basic
*
Fixing the lever
*
Boost pressure
kPa
44
44
Boost pressure
mmHg
330
330
PS407980-224*
V
V1+0.05+
-0.01
PS407980-224*
mm
6.3+-0.0
3
Remarks
Refer to items regarding the pre-stroke actuator
Refer to items regarding the pre-stroke actuator
Injection quantity adjustment_02
Adjusting point
B
Rack position
11.15
Pump speed
r/min
1000
1000
1000
Average injection quantity
mm3/st.
214.9
208.9
220.9
Max. variation between cylinders
%
0
-5
5
Fixing the lever
*
Boost pressure
kPa
44
44
Boost pressure
mmHg
330
330
PS407980-224*
V
V1+0.05+
-0.01
PS407980-224*
mm
6.3+-0.0
3
Injection quantity adjustment_03
Adjusting point
F
Rack position
-
Pump speed
r/min
100
100
100
Average injection quantity
mm3/st.
215.3
210.3
220.3
Fixing the lever
*
Boost pressure
kPa
44
44
Boost pressure
mmHg
330
330
Rack limit
*
PS407980-224*
V
V1+0.05+
-0.01
PS407980-224*
mm
6.3+-0.0
3
Injection quantity adjustment_04
Adjusting point
G
Rack position
4.9+-0.5
Pump speed
r/min
225
225
225
Average injection quantity
mm3/st.
10
7
13
Max. variation between cylinders
%
0
-15
15
Fixing the rack
*
Boost pressure
kPa
0
0
0
Boost pressure
mmHg
0
0
0
PS407980-224*
V
V1+0.05+
-0.01
PS407980-224*
mm
6.3+-0.0
3
Boost compensator adjustment
Pump speed
r/min
500
500
500
Rack position
8.7
Boost pressure
kPa
3.3
3.3
5.3
Boost pressure
mmHg
25
25
40
Boost compensator adjustment_02
Pump speed
r/min
500
500
500
Rack position
10.65
Boost pressure
kPa
30.7
30.7
30.7
Boost pressure
mmHg
230
230
230
0000001601
Pre-stroke
mm
6.4
6.37
6.43
Remarks
When the timing sleeve is pushed up
When the timing sleeve is pushed up
_02
Connector angle
deg.
8.5
8.45
8.55
Remarks
When the eccentric pin is tightened
When the eccentric pin is tightened
_03
Supply voltage
V
24
23.5
24.5
Ambient temperature
degC
23
18
28
Pre-stroke
mm
4
3.95
4.05
Output voltage
V
2.45
2.44
2.46
Adjustment
*
_04
Supply voltage
V
24
23.5
24.5
Ambient temperature
degC
23
18
28
Pre-stroke
mm
6.4
6.37
6.43
Output voltage
V
1.2
1
1.4
Confirmation
*
Remarks
Output voltage V1
Output voltage V1
_05
Supply voltage
V
24
23.5
24.5
Ambient temperature
degC
23
18
28
Pre-stroke
mm
3.4
Output voltage
V
3
2.98
3
Confirmation
*
_06
Supply voltage
V
24
23.5
24.5
Ambient temperature
degC
23
18
28
Output voltage
V
3.05
3.05
Confirmation of operating range
*
Test data Ex:
Governor adjustment
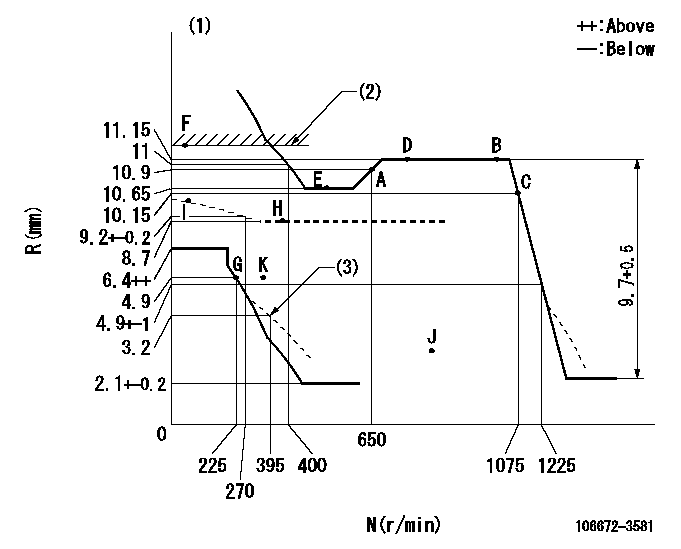
N:Pump speed
R:Rack position (mm)
(1)Tolerance for racks not indicated: +-0.05mm.
(2)RACK LIMIT
(3)Damper spring setting
----------
----------
----------
----------
Speed control lever angle

F:Full speed
----------
----------
a=15.5deg+-5deg
----------
----------
a=15.5deg+-5deg
0000000901

F:Full load
I:Idle
(1)Stopper bolt setting
----------
----------
a=25deg+-5deg b=31.5deg+-3deg
----------
----------
a=25deg+-5deg b=31.5deg+-3deg
Stop lever angle
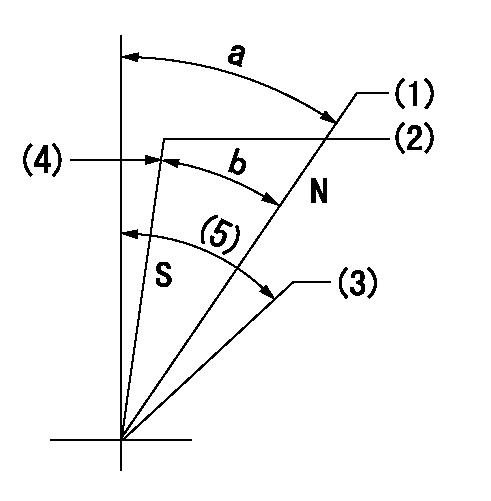
N:Engine manufacturer's normal use
S:Stop the pump.
(1)Rack position = aa
(2)Rack position bb
(3)Free (at delivery)
(4)Set the stopper bolt (apply red paint).
(5)(Actual measurement)
----------
aa=12.9mm bb=2.4-0.5mm
----------
a=44deg+-5deg b=35deg+-5deg
----------
aa=12.9mm bb=2.4-0.5mm
----------
a=44deg+-5deg b=35deg+-5deg
0000001301

(1)Pump vertical direction
(2)Coupling's key groove position at No 1 cylinder's beginning of injection
(3)Pre-stroke: aa
(4)-
----------
aa=6.4+-0.03mm
----------
a=(0deg)
----------
aa=6.4+-0.03mm
----------
a=(0deg)
0000002201 RACK SENSOR

(VR) measurement voltage
(I) Part number of the control unit
(G) Apply red paint.
(H): End surface of the pump
1. Rack limit adjustment
(1)Mount the joint (B).
(2)Select the shim (D) so that the rack limit's rack position is obtained at that time.
(3)Install the rod (E) to the block (C).
The distance between the pump end face and the rod (E) at rack limit must be L.
2. Rack sensor adjustment (-0020)
(1)Screw in the bobbin (A) until it contacts the joint (B).
(2)Fix the speed control lever at the full side.
(3)Set at speed N.
(4)Adjust the depth that the bobbin (A) is screwed in so that the control unit's rack sensor output voltage is VR+-0.01 (V), then tighten the nut (F). (If equipped with a boost compensator, perform with boost pressure applied.)
(5)Adjust the bobbin (A) so that the rack sensor's output voltage is VR+-0.01.
(6)Apply G at two places.
Connecting part between the joint (B) and the nut (F)
Connecting part between the joint (B) and the end surface of the pump (H)
----------
L=38-0.2mm N=850r/min Ra=(11.15)mm
----------
----------
L=38-0.2mm N=850r/min Ra=(11.15)mm
----------
0000002301 GOVERNOR TORQUE CONTROL

Dr:Torque control stroke
(A): Without torque control spring capsule
1. Adjustment procedures
(1)Procedure is the same as that for the RFD (former type), except that the positive torque control stroke must be determined at the full lever setting.
2. Procedures for adjustment
(1)Remove the torque control spring capsule.
(2)Operate the pump at approximately N1. (End of idling spring operation < N1.)
(3)Tilt the lever to the full side.
(4)Set so that R = RF.
(5)Increase the speed by pushing in the screw (attached to the bracket on the rear of the tension lever) through the adjusting window.
(6)Adjust so that the torque control stroke Dr1 can be obtained.
(7)Align N2 and N3 with the torque control spring capsule.
3. Final confirmation
(1)After final confirmation, temporarily set the load lever to N = N1, R = idling position.
(2)From this condition, increase speed to N = N4.
(3)Confirm that positive torque control stroke is Dr2.
----------
N1=500r/min N2=- N3=- N4=1000r/min RF=10.65mm Dr1=0.5mm Dr2=0+0.3mm
----------
----------
N1=500r/min N2=- N3=- N4=1000r/min RF=10.65mm Dr1=0.5mm Dr2=0+0.3mm
----------
Information:
This Program can only be administered after a failure occurs. The decision whether to apply the Program is made by the dealer. When reporting the repair, use "PS5560" as the Part Number and "7755" as the Group Number. Use "96" as the Warranty Claim Description Code and use "Z" as the SIMS Description Code.
Termination Date
December 19, 1999Problem
The connection plate from the fuel injection pump lever may wear prematurely causing the return spring to disconnect on certain 312 Excavators. When the return spring disconnects, the fuel injection pump will no longer operate properly.
Affected Product
Model & Identification Number
312 (6BL112-1827)
CIPI Product (05A10771, 10798, 11808)
Parts Needed
1 - 5C2890 Nut1 - 8C3111 Rod End1 - 8T4971 Bolt1 - 9X8256 Washer1 - 1643187 PlateAction Required
See the attached Rework Procedures.
Service Claim Allowances
This is a 1-hour job.
Parts Disposition
Handle the parts in accordance with your Warranty Bulletin on warranty parts handling.
Attach.(1-Rework Procedure)Rework Procedure
1. Disconnect return spring from 1190312 Plate.2. Remove the ball-joint from extremity of the governor cable, and replace it by 8C3111 Rod End.3. Remove 1190312 Plate, 9X8256 Washer and 8T4134 Nut. Keep 9X8256 Washer to be reused.4. To connect new 1643187 Plate together with injection pump lever and 8C3111 Cable Rod End, use 8T4971 Bolt, (2) 9X8256 Washers and 5C2890 Nut. See Illustration 1.5. Reconnect the return spring to 1643187 Plate.6. Perform an auto calibration through controller Service Mode, and readjust if necessary the cable tension, according to Hydraulics and Electronics "Testing & Adjusting" manual.
Illustration 1
Termination Date
December 19, 1999Problem
The connection plate from the fuel injection pump lever may wear prematurely causing the return spring to disconnect on certain 312 Excavators. When the return spring disconnects, the fuel injection pump will no longer operate properly.
Affected Product
Model & Identification Number
312 (6BL112-1827)
CIPI Product (05A10771, 10798, 11808)
Parts Needed
1 - 5C2890 Nut1 - 8C3111 Rod End1 - 8T4971 Bolt1 - 9X8256 Washer1 - 1643187 PlateAction Required
See the attached Rework Procedures.
Service Claim Allowances
This is a 1-hour job.
Parts Disposition
Handle the parts in accordance with your Warranty Bulletin on warranty parts handling.
Attach.(1-Rework Procedure)Rework Procedure
1. Disconnect return spring from 1190312 Plate.2. Remove the ball-joint from extremity of the governor cable, and replace it by 8C3111 Rod End.3. Remove 1190312 Plate, 9X8256 Washer and 8T4134 Nut. Keep 9X8256 Washer to be reused.4. To connect new 1643187 Plate together with injection pump lever and 8C3111 Cable Rod End, use 8T4971 Bolt, (2) 9X8256 Washers and 5C2890 Nut. See Illustration 1.5. Reconnect the return spring to 1643187 Plate.6. Perform an auto calibration through controller Service Mode, and readjust if necessary the cable tension, according to Hydraulics and Electronics "Testing & Adjusting" manual.
Illustration 1