Information injection-pump assembly
BOSCH
9 400 619 805
9400619805
ZEXEL
106672-3421
1066723421
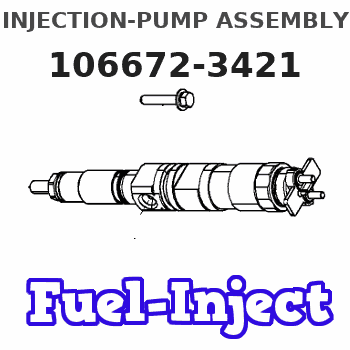
Rating:
Service parts 106672-3421 INJECTION-PUMP ASSEMBLY:
1.
_
5.
AUTOM. ADVANCE MECHANIS
7.
COUPLING PLATE
8.
_
9.
_
11.
Nozzle and Holder
236001561C
12.
Open Pre:MPa(Kqf/cm2)
21.6(220)
15.
NOZZLE SET
Include in #1:
106672-3421
as INJECTION-PUMP ASSEMBLY
Cross reference number
Zexel num
Bosch num
Firm num
Name
Information:
1. Overview of Lubrication System
Flow of oil2. Oil Pump, Relief Valve, and Oil Pressure Switch
2.1 Disassembly
Disassembly sequence and points to check on oil pump1 Oil filter2 Oil pump3 Gasket4 Oil pump cover5 Inner rotor6 Outer rotor (The inner and outer rotors form a rotor assembly)7 O-ring8 Oil pump body9 Relief valve10 Oil pressure switch KEY POINTS FOR DISASSEMBLY(1) Oil PumpRemove the oil pump (parts (3) through (8) in the above drawing) as an assembly.
Removing oil pump(2) Oil Pressure SwitchRemove the switch using the Oil Pressure Switch Socket Wrench (MD998054).
Removing oil pressure switch2.2 Inspection and Repair(1) Oil Pump(a) Using a thickness gauge, measure the clearance between the outer rotor and pump body. If the measurement exceeds the limit, replace the rotor assembly.
Unit: mm (in.)
Measuring outer rotor-to-pump body clearance(b) Using a thickness gauge, measure the clearance between the outer rotor and inner rotor. If the measurement exceeds the limit, replace the rotor assembly.
Unit: mm (in.)
Measuring outer rotor-to-inner rotor clearance(c) Using a straight edge and a thickness gauge, measure the clearance between the rotors and pump cover. If the measurement exceeds the limit, replace either the rotors or the pump body.
Unit: mm (in.)
Measuring clearance between rotors and pump over(2) Oil Pressure Switch(a) Connect a tester (set to the ohm range) between the terminal and body of the oil pressure switch. There should be continuity. If there is no continuity, the switch is faulty and should be replaced.
Inspecting oil pressure switch(b) Insert a thin rod into the oil hole in the switch body. When the rod is then pushed in gently, there should be no continuity between the switch body and terminal. If there is continuity, the switch is faulty and should be replaced.(c) Apply an air pressure of 49 kPa {0.5 kgf/cm2} (7.2 psi) to the switch through the oil hole. If there is no continuity, the switch is normal. Simultaneously, check for air leakage. Any air leakage means that the diaphragm is broken and, therefore, the switch should be replaced.
Inspecting oil pressure switch2.3 Assembly
Points to note during reassembly of oil pump KEY POINTS FOR REASSEMBLY Oil Pressure Switch(a) Install the switch using the Oil Pressure Switch Socket Wrench (MD998054).(b) Before installation, apply sealant to the threads of the switch. (Use either Hermeseal H1 or Threebond 1104).
(a) Avoid applying sealant excessively to prevent it from reaching the end of the threads.(b) Never tighten the switch to a torque exceeding specification.
Installing oil pressure switch
Flow of oil2. Oil Pump, Relief Valve, and Oil Pressure Switch
2.1 Disassembly
Disassembly sequence and points to check on oil pump1 Oil filter2 Oil pump3 Gasket4 Oil pump cover5 Inner rotor6 Outer rotor (The inner and outer rotors form a rotor assembly)7 O-ring8 Oil pump body9 Relief valve10 Oil pressure switch KEY POINTS FOR DISASSEMBLY(1) Oil PumpRemove the oil pump (parts (3) through (8) in the above drawing) as an assembly.
Removing oil pump(2) Oil Pressure SwitchRemove the switch using the Oil Pressure Switch Socket Wrench (MD998054).
Removing oil pressure switch2.2 Inspection and Repair(1) Oil Pump(a) Using a thickness gauge, measure the clearance between the outer rotor and pump body. If the measurement exceeds the limit, replace the rotor assembly.
Unit: mm (in.)
Measuring outer rotor-to-pump body clearance(b) Using a thickness gauge, measure the clearance between the outer rotor and inner rotor. If the measurement exceeds the limit, replace the rotor assembly.
Unit: mm (in.)
Measuring outer rotor-to-inner rotor clearance(c) Using a straight edge and a thickness gauge, measure the clearance between the rotors and pump cover. If the measurement exceeds the limit, replace either the rotors or the pump body.
Unit: mm (in.)
Measuring clearance between rotors and pump over(2) Oil Pressure Switch(a) Connect a tester (set to the ohm range) between the terminal and body of the oil pressure switch. There should be continuity. If there is no continuity, the switch is faulty and should be replaced.
Inspecting oil pressure switch(b) Insert a thin rod into the oil hole in the switch body. When the rod is then pushed in gently, there should be no continuity between the switch body and terminal. If there is continuity, the switch is faulty and should be replaced.(c) Apply an air pressure of 49 kPa {0.5 kgf/cm2} (7.2 psi) to the switch through the oil hole. If there is no continuity, the switch is normal. Simultaneously, check for air leakage. Any air leakage means that the diaphragm is broken and, therefore, the switch should be replaced.
Inspecting oil pressure switch2.3 Assembly
Points to note during reassembly of oil pump KEY POINTS FOR REASSEMBLY Oil Pressure Switch(a) Install the switch using the Oil Pressure Switch Socket Wrench (MD998054).(b) Before installation, apply sealant to the threads of the switch. (Use either Hermeseal H1 or Threebond 1104).
(a) Avoid applying sealant excessively to prevent it from reaching the end of the threads.(b) Never tighten the switch to a torque exceeding specification.
Installing oil pressure switch