Information injection-pump assembly
ZEXEL
106672-3390
1066723390
HINO
220203020A
220203020a
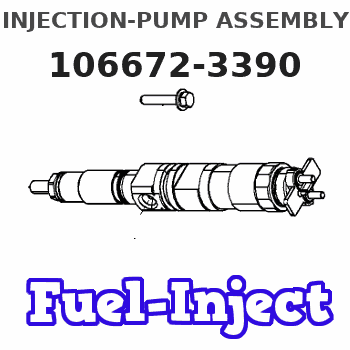
Rating:
Cross reference number
ZEXEL
106672-3390
1066723390
HINO
220203020A
220203020a
Zexel num
Bosch num
Firm num
Name
Calibration Data:
Adjustment conditions
Test oil
1404 Test oil ISO4113 or {SAEJ967d}
1404 Test oil ISO4113 or {SAEJ967d}
Test oil temperature
degC
40
40
45
Nozzle and nozzle holder
105780-8140
Bosch type code
EF8511/9A
Nozzle
105780-0000
Bosch type code
DN12SD12T
Nozzle holder
105780-2080
Bosch type code
EF8511/9
Opening pressure
MPa
17.2
Opening pressure
kgf/cm2
175
Injection pipe
Outer diameter - inner diameter - length (mm) mm 8-3-600
Outer diameter - inner diameter - length (mm) mm 8-3-600
Overflow valve
134424-1420
Overflow valve opening pressure
kPa
162
147
177
Overflow valve opening pressure
kgf/cm2
1.65
1.5
1.8
Tester oil delivery pressure
kPa
157
157
157
Tester oil delivery pressure
kgf/cm2
1.6
1.6
1.6
Direction of rotation (viewed from drive side)
Right R
Right R
Injection timing adjustment
Direction of rotation (viewed from drive side)
Right R
Right R
Injection order
1-4-2-6-
3-5
Pre-stroke
mm
4.5
4.4
4.5
Beginning of injection position
Drive side NO.1
Drive side NO.1
Difference between angles 1
Cal 1-4 deg. 60 59.5 60.5
Cal 1-4 deg. 60 59.5 60.5
Difference between angles 2
Cyl.1-2 deg. 120 119.5 120.5
Cyl.1-2 deg. 120 119.5 120.5
Difference between angles 3
Cal 1-6 deg. 180 179.5 180.5
Cal 1-6 deg. 180 179.5 180.5
Difference between angles 4
Cal 1-3 deg. 240 239.5 240.5
Cal 1-3 deg. 240 239.5 240.5
Difference between angles 5
Cal 1-5 deg. 300 299.5 300.5
Cal 1-5 deg. 300 299.5 300.5
Injection quantity adjustment
Adjusting point
B
Rack position
7.3
Pump speed
r/min
650
650
650
Average injection quantity
mm3/st.
100.2
98.2
102.2
Max. variation between cylinders
%
0
-2
2
Basic
*
Fixing the lever
*
Injection quantity adjustment_02
Adjusting point
C
Rack position
4.9+-0.5
Pump speed
r/min
440
440
440
Average injection quantity
mm3/st.
10.2
7.2
13.2
Max. variation between cylinders
%
0
-15
15
Fixing the rack
*
Injection quantity adjustment_03
Adjusting point
D
Rack position
-
Pump speed
r/min
100
100
100
Average injection quantity
mm3/st.
134
129
139
Fixing the lever
*
Rack limit
*
Test data Ex:
Governor adjustment
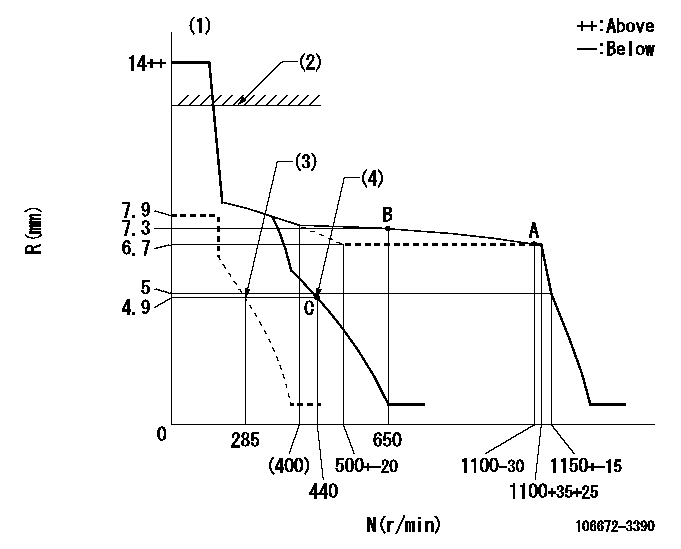
N:Pump speed
R:Rack position (mm)
(1)Target notch: K
(2)RACK LIMIT
(3)Set idle sub-spring
(4)Main spring setting
----------
K=13
----------
----------
K=13
----------
Speed control lever angle

F:Full speed
I:Idle
(1)Stopper bolt setting
----------
----------
a=(13deg)+-5deg b=(26deg)+-5deg
----------
----------
a=(13deg)+-5deg b=(26deg)+-5deg
Stop lever angle
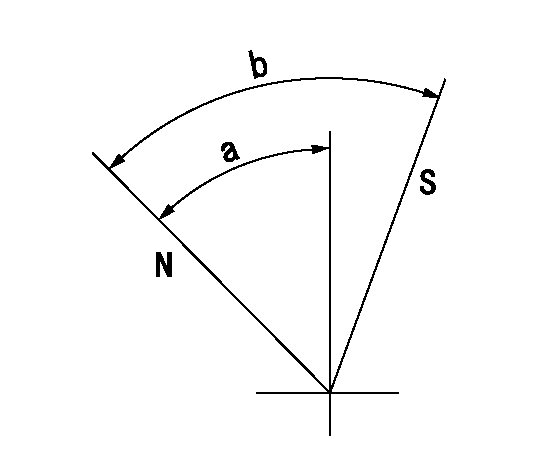
N:Pump normal
S:Stop the pump.
----------
----------
a=53deg+-5deg b=53deg+-5deg
----------
----------
a=53deg+-5deg b=53deg+-5deg
Timing setting
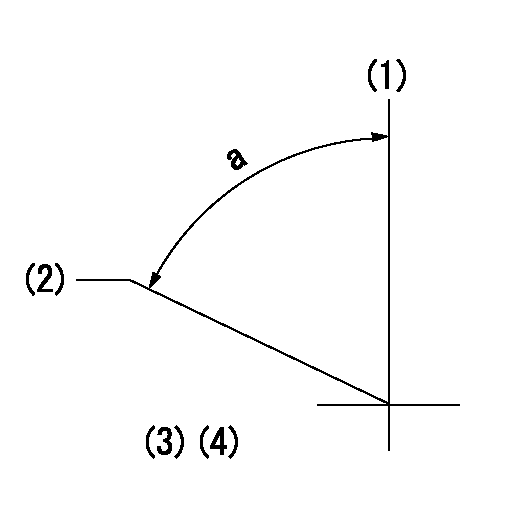
(1)Pump vertical direction
(2)Coupling's key groove position at No 1 cylinder's beginning of injection
(3)-
(4)-
----------
----------
a=(50deg)
----------
----------
a=(50deg)
Information:
1. Overview
1.1 External Views 1.2 Engine Model and Engine Serial Number(1) The engine model code is embossed next to the injection pump on the right-hand side of the cylinder block.
Engine model and total displacement(2) The engine serial number is shown by a label attached to the top of the rocker cover. It is also stamped on the injection pump mounting surface of the cylinder block.(3) The engine serial number is stamped as shown below:
Location of engine serial number label1.3 Engine Model and Application Codes(1) The engine model code is designated as shown below.* Engine model and classification * Model code 2. Specifications
2.1 Major Specifications 3. Points to Note for Disassembly and Reassembly
This service manual contains recommended service procedures for your Mitsubishi diesel engine. It also contains information on special tools and basic safety precautions. Since hazards exist in many places, the safety precautions in this manual should not be considered exhaustive. It is your responsibility to exercise common sense and to pay attention to safety at all times.Always perform service operations in accordance with this manual. When performing disassembly and reassembly operations, also observe the general instructions given below.3.1 Disassembly(1) Use only the correct tools and instruments.(2) Use an overhaul stand or work bench if necessary, and make ready a surface where removed parts can be arranged. Remove parts in the specified disassembly sequence.(3) Arrange disassembled parts neatly to avoid losing them.(4) Pay attention to alignment and position marks. If necessary, make your own marks to facilitate reassembly.(5) Carefully check parts for abnormalities when removing or cleaning them. Abnormalities may be harder to see after parts have been removed or cleaned.(6) Strive to ensure safety at all times. It is particularly important to make sure that items being disassembled are properly balanced and to pay attention to safety when moving heavy items. Use jacks and chain blocks when necessary.3.2 Reassembly(1) Wash all engine parts (except oil seals, O-rings, and rubber seals) in cleaning solvent and dry them with compressed air.(2) Use only the correct tools and instruments.(3) Use only high-quality oils and greases of the specified types. Be sure to apply a coat of oil, grease, or sealant wherever specified.(4) Use a torque wrench to achieve all specified tightening torques.(5) As a general rule, all gaskets and seals must be replaced with new ones. Apply adhesive where required, and be careful not to apply too much.
1.1 External Views 1.2 Engine Model and Engine Serial Number(1) The engine model code is embossed next to the injection pump on the right-hand side of the cylinder block.
Engine model and total displacement(2) The engine serial number is shown by a label attached to the top of the rocker cover. It is also stamped on the injection pump mounting surface of the cylinder block.(3) The engine serial number is stamped as shown below:
Location of engine serial number label1.3 Engine Model and Application Codes(1) The engine model code is designated as shown below.* Engine model and classification * Model code 2. Specifications
2.1 Major Specifications 3. Points to Note for Disassembly and Reassembly
This service manual contains recommended service procedures for your Mitsubishi diesel engine. It also contains information on special tools and basic safety precautions. Since hazards exist in many places, the safety precautions in this manual should not be considered exhaustive. It is your responsibility to exercise common sense and to pay attention to safety at all times.Always perform service operations in accordance with this manual. When performing disassembly and reassembly operations, also observe the general instructions given below.3.1 Disassembly(1) Use only the correct tools and instruments.(2) Use an overhaul stand or work bench if necessary, and make ready a surface where removed parts can be arranged. Remove parts in the specified disassembly sequence.(3) Arrange disassembled parts neatly to avoid losing them.(4) Pay attention to alignment and position marks. If necessary, make your own marks to facilitate reassembly.(5) Carefully check parts for abnormalities when removing or cleaning them. Abnormalities may be harder to see after parts have been removed or cleaned.(6) Strive to ensure safety at all times. It is particularly important to make sure that items being disassembled are properly balanced and to pay attention to safety when moving heavy items. Use jacks and chain blocks when necessary.3.2 Reassembly(1) Wash all engine parts (except oil seals, O-rings, and rubber seals) in cleaning solvent and dry them with compressed air.(2) Use only the correct tools and instruments.(3) Use only high-quality oils and greases of the specified types. Be sure to apply a coat of oil, grease, or sealant wherever specified.(4) Use a torque wrench to achieve all specified tightening torques.(5) As a general rule, all gaskets and seals must be replaced with new ones. Apply adhesive where required, and be careful not to apply too much.