Information injection-pump assembly
BOSCH
9 400 617 084
9400617084
ZEXEL
106672-3364
1066723364
HINO
220202795A
220202795a
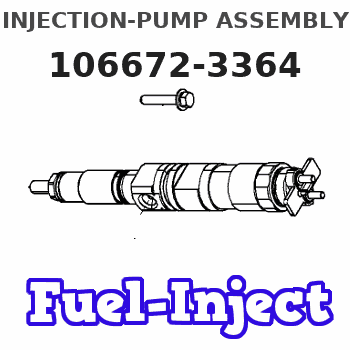
Rating:
Service parts 106672-3364 INJECTION-PUMP ASSEMBLY:
1.
_
5.
AUTOM. ADVANCE MECHANIS
7.
COUPLING PLATE
8.
_
9.
_
11.
Nozzle and Holder
23600-2030A
12.
Open Pre:MPa(Kqf/cm2)
19.6{200}
15.
NOZZLE SET
Include in #1:
106672-3364
as INJECTION-PUMP ASSEMBLY
Cross reference number
BOSCH
9 400 617 084
9400617084
ZEXEL
106672-3364
1066723364
HINO
220202795A
220202795a
Zexel num
Bosch num
Firm num
Name
106672-3364
9 400 617 084
220202795A HINO
INJECTION-PUMP ASSEMBLY
EK130-T K 14CA INJECTION PUMP ASSY PE6P,6PD PE
EK130-T K 14CA INJECTION PUMP ASSY PE6P,6PD PE
Calibration Data:
Adjustment conditions
Test oil
1404 Test oil ISO4113 or {SAEJ967d}
1404 Test oil ISO4113 or {SAEJ967d}
Test oil temperature
degC
40
40
45
Nozzle and nozzle holder
105780-8140
Bosch type code
EF8511/9A
Nozzle
105780-0000
Bosch type code
DN12SD12T
Nozzle holder
105780-2080
Bosch type code
EF8511/9
Opening pressure
MPa
17.2
Opening pressure
kgf/cm2
175
Injection pipe
Outer diameter - inner diameter - length (mm) mm 8-3-600
Outer diameter - inner diameter - length (mm) mm 8-3-600
Overflow valve
134424-0920
Overflow valve opening pressure
kPa
162
147
177
Overflow valve opening pressure
kgf/cm2
1.65
1.5
1.8
Tester oil delivery pressure
kPa
157
157
157
Tester oil delivery pressure
kgf/cm2
1.6
1.6
1.6
Direction of rotation (viewed from drive side)
Left L
Left L
Injection timing adjustment
Direction of rotation (viewed from drive side)
Left L
Left L
Injection order
1-4-2-6-
3-5
Pre-stroke
mm
3.3
3.2
3.3
Beginning of injection position
Drive side NO.1
Drive side NO.1
Difference between angles 1
Cal 1-4 deg. 60 59.5 60.5
Cal 1-4 deg. 60 59.5 60.5
Difference between angles 2
Cyl.1-2 deg. 120 119.5 120.5
Cyl.1-2 deg. 120 119.5 120.5
Difference between angles 3
Cal 1-6 deg. 180 179.5 180.5
Cal 1-6 deg. 180 179.5 180.5
Difference between angles 4
Cal 1-3 deg. 240 239.5 240.5
Cal 1-3 deg. 240 239.5 240.5
Difference between angles 5
Cal 1-5 deg. 300 299.5 300.5
Cal 1-5 deg. 300 299.5 300.5
Injection quantity adjustment
Adjusting point
A
Rack position
9.6
Pump speed
r/min
900
900
900
Average injection quantity
mm3/st.
175.3
173.3
177.3
Max. variation between cylinders
%
0
-4
4
Basic
*
Fixing the rack
*
Injection quantity adjustment_02
Adjusting point
B
Rack position
9.1
Pump speed
r/min
750
750
750
Average injection quantity
mm3/st.
167.8
161.8
173.8
Max. variation between cylinders
%
0
-4
4
Fixing the rack
*
Injection quantity adjustment_03
Adjusting point
-
Rack position
5.4+-0.5
Pump speed
r/min
360
360
360
Average injection quantity
mm3/st.
14.8
11.8
17.8
Max. variation between cylinders
%
0
-15
15
Fixing the rack
*
Remarks
Adjust only variation between cylinders; adjust governor according to governor specifications.
Adjust only variation between cylinders; adjust governor according to governor specifications.
Test data Ex:
Governor adjustment
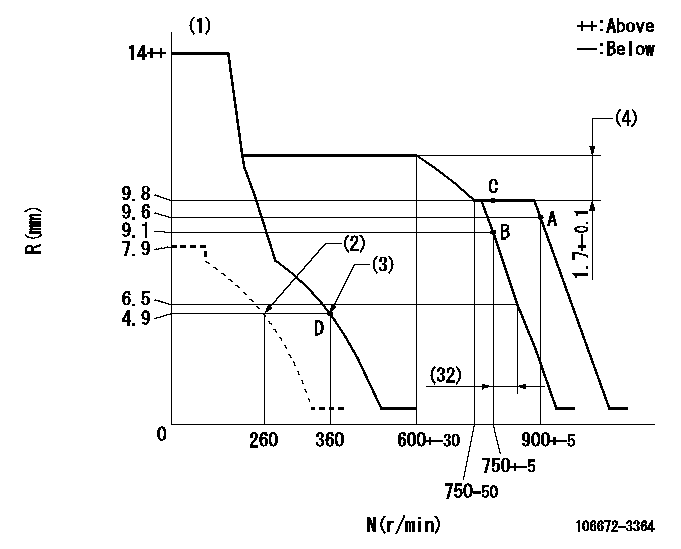
N:Pump speed
R:Rack position (mm)
(1)Notch fixed: K
(2)Set idle sub-spring
(3)Main spring setting
(4)Rack difference between N = N1 and N = N2
----------
K=6 N1=750r/min N2=550r/min
----------
----------
K=6 N1=750r/min N2=550r/min
----------
Speed control lever angle

F:Full speed
I:Idle
(1)Set the pump speed at aa. ( At delivery )
(2)Set the pump speed at bb.
(3)Stopper bolt setting
----------
aa=900r/min bb=750r/min
----------
a=(5deg)+-5deg b=(19deg)+-5deg c=(5deg)+-5deg
----------
aa=900r/min bb=750r/min
----------
a=(5deg)+-5deg b=(19deg)+-5deg c=(5deg)+-5deg
Stop lever angle

N:Pump normal
S:Stop the pump.
(1)Contacts inner stopper.
(2)Rack position = aa or less, at speed = bb
(3)Contacts outer stopper.
----------
aa=4.4mm bb=0r/min
----------
a=27deg+-5deg b=53deg+-5deg c=(11deg)
----------
aa=4.4mm bb=0r/min
----------
a=27deg+-5deg b=53deg+-5deg c=(11deg)
Timing setting

(1)Pump vertical direction
(2)Coupling's key groove position at No 1 cylinder's beginning of injection
(3)-
(4)-
----------
----------
a=(0deg)
----------
----------
a=(0deg)
Information:
GENERAL
1. Schematic
Schematic2. Specifications INSPECTION
1. Oil pumpVisually check the pump for rough rotation or other defects. Replace the pump assembly if defective.
Checking oil pump2. Oil pressure switch (1) Test for continuity between the terminal and body with an ohmmeter as shown in the illustration. No continuity is the cause for replacing the switch.
Testing oil pressure switch (1)(2) Insert a small diameter bar into the oil hole in the switch and lightly push it in to test for no continuity as shown in the illustration. Any continuity is the cause for replacing the switch.(3) Apply a pressure air of 0.5 kgf/cm2 (7 psi) [49 kPa] to the switch through the oil hole to test for no continuity. Any continuity is the cause for replacing the switch. Also, check for air leaks. Any air leak is an indication of a ruptured diaphragm. In such a case, replace the switch.
Testing oil pressure switch (2)3. Pressure relief valve (1) Check the valve seat for contact. Check the spring for damage.(2) Measure the oil pressure at which the relief valve opens (the oil pressure with the engine running at the rated rpm). If the pressure is not correct, remove the cap nut and increase or decrease the amount of shims. The engine oil pressure tap is located on the right side of the engine.
Checking pressure relief valve
1. Schematic
Schematic2. Specifications INSPECTION
1. Oil pumpVisually check the pump for rough rotation or other defects. Replace the pump assembly if defective.
Checking oil pump2. Oil pressure switch (1) Test for continuity between the terminal and body with an ohmmeter as shown in the illustration. No continuity is the cause for replacing the switch.
Testing oil pressure switch (1)(2) Insert a small diameter bar into the oil hole in the switch and lightly push it in to test for no continuity as shown in the illustration. Any continuity is the cause for replacing the switch.(3) Apply a pressure air of 0.5 kgf/cm2 (7 psi) [49 kPa] to the switch through the oil hole to test for no continuity. Any continuity is the cause for replacing the switch. Also, check for air leaks. Any air leak is an indication of a ruptured diaphragm. In such a case, replace the switch.
Testing oil pressure switch (2)3. Pressure relief valve (1) Check the valve seat for contact. Check the spring for damage.(2) Measure the oil pressure at which the relief valve opens (the oil pressure with the engine running at the rated rpm). If the pressure is not correct, remove the cap nut and increase or decrease the amount of shims. The engine oil pressure tap is located on the right side of the engine.
Checking pressure relief valve
Have questions with 106672-3364?
Group cross 106672-3364 ZEXEL
Hino
106672-3364
9 400 617 084
220202795A
INJECTION-PUMP ASSEMBLY
EK130-T
EK130-T