Information injection-pump assembly
BOSCH
9 400 617 078
9400617078
ZEXEL
106672-3282
1066723282
HINO
220005222A
220005222a
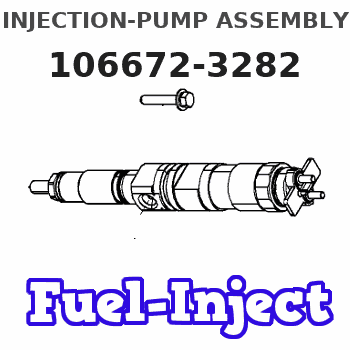
Rating:
Cross reference number
BOSCH
9 400 617 078
9400617078
ZEXEL
106672-3282
1066723282
HINO
220005222A
220005222a
Zexel num
Bosch num
Firm num
Name
106672-3282
9 400 617 078
220005222A HINO
INJECTION-PUMP ASSEMBLY
EP1 K
EP1 K
106672-3282
9 400 617 078
S220005222A HINO
INJECTION-PUMP ASSEMBLY
EP1 A K
EP1 A K
Calibration Data:
Adjustment conditions
Test oil
1404 Test oil ISO4113 or {SAEJ967d}
1404 Test oil ISO4113 or {SAEJ967d}
Test oil temperature
degC
40
40
45
Nozzle and nozzle holder
105780-8140
Bosch type code
EF8511/9A
Nozzle
105780-0000
Bosch type code
DN12SD12T
Nozzle holder
105780-2080
Bosch type code
EF8511/9
Opening pressure
MPa
17.2
Opening pressure
kgf/cm2
175
Injection pipe
Outer diameter - inner diameter - length (mm) mm 8-3-600
Outer diameter - inner diameter - length (mm) mm 8-3-600
Overflow valve (drive side)
134424-1420
Overflow valve opening pressure (drive side)
kPa
162
147
177
Overflow valve opening pressure (drive side)
kgf/cm2
1.65
1.5
1.8
Overflow valve (governor side)
134424-1720
Overflow valve opening pressure (governor side)
kPa
162
147
177
Overflow valve opening pressure (governor side)
kgf/cm2
1.65
1.5
1.8
Tester oil delivery pressure
kPa
157
157
157
Tester oil delivery pressure
kgf/cm2
1.6
1.6
1.6
Direction of rotation (viewed from drive side)
Right R
Right R
Injection timing adjustment
Direction of rotation (viewed from drive side)
Right R
Right R
Injection order
1-4-2-6-
3-5
Pre-stroke
mm
4.5
4.44
4.5
Beginning of injection position
Drive side NO.1
Drive side NO.1
Difference between angles 1
Cal 1-4 deg. 60 59.75 60.25
Cal 1-4 deg. 60 59.75 60.25
Difference between angles 2
Cyl.1-2 deg. 120 119.75 120.25
Cyl.1-2 deg. 120 119.75 120.25
Difference between angles 3
Cal 1-6 deg. 180 179.75 180.25
Cal 1-6 deg. 180 179.75 180.25
Difference between angles 4
Cal 1-3 deg. 240 239.75 240.25
Cal 1-3 deg. 240 239.75 240.25
Difference between angles 5
Cal 1-5 deg. 300 299.75 300.25
Cal 1-5 deg. 300 299.75 300.25
Injection quantity adjustment
Adjusting point
A
Rack position
8.4
Pump speed
r/min
700
700
700
Average injection quantity
mm3/st.
146.7
144.7
148.7
Max. variation between cylinders
%
0
-2
2
Basic
*
Fixing the lever
*
Boost pressure
kPa
32
32
Boost pressure
mmHg
240
240
Injection quantity adjustment_02
Adjusting point
C
Rack position
8.2
Pump speed
r/min
1075
1075
1075
Average injection quantity
mm3/st.
141.1
135.1
147.1
Max. variation between cylinders
%
0
-5
5
Fixing the lever
*
Boost pressure
kPa
32
32
Boost pressure
mmHg
240
240
Injection quantity adjustment_03
Adjusting point
D
Rack position
7.7
Pump speed
r/min
1200
1200
1200
Average injection quantity
mm3/st.
131
126
136
Max. variation between cylinders
%
0
-5
5
Fixing the lever
*
Boost pressure
kPa
32
32
Boost pressure
mmHg
240
240
Injection quantity adjustment_04
Adjusting point
E
Rack position
9.8+-0.5
Pump speed
r/min
300
300
300
Average injection quantity
mm3/st.
180.6
177.6
183.6
Fixing the lever
*
Boost pressure
kPa
32
32
Boost pressure
mmHg
240
240
Injection quantity adjustment_05
Adjusting point
G
Rack position
6.3
Pump speed
r/min
400
400
400
Average injection quantity
mm3/st.
72.9
70.9
74.9
Fixing the lever
*
Boost pressure
kPa
0
0
0
Boost pressure
mmHg
0
0
0
Injection quantity adjustment_06
Adjusting point
H
Rack position
-
Pump speed
r/min
100
100
100
Average injection quantity
mm3/st.
110
110
Fixing the lever
*
Boost pressure
kPa
0
0
0
Boost pressure
mmHg
0
0
0
Injection quantity adjustment_07
Adjusting point
I
Rack position
4.6+-0.5
Pump speed
r/min
225
225
225
Average injection quantity
mm3/st.
8.4
5.4
11.4
Max. variation between cylinders
%
0
-15
15
Fixing the rack
*
Boost pressure
kPa
0
0
0
Boost pressure
mmHg
0
0
0
Boost compensator adjustment
Pump speed
r/min
700
700
700
Rack position
6.3
Boost pressure
kPa
3.3
3.3
5.3
Boost pressure
mmHg
25
25
40
Boost compensator adjustment_02
Pump speed
r/min
700
700
700
Rack position
8.4
Boost pressure
kPa
18.7
18.7
18.7
Boost pressure
mmHg
140
140
140
Test data Ex:
Governor adjustment

N:Pump speed
R:Rack position (mm)
(1)RACK LIMIT
(2)Set idle at delivery
(3)Damper spring setting: DL
(4)Rack difference between N = N1 and N = N2
----------
DL=4.4-0.2mm N1=1075r/min N2=700r/min
----------
----------
DL=4.4-0.2mm N1=1075r/min N2=700r/min
----------
Speed control lever angle

F:Full speed
----------
----------
a=6deg+-5deg
----------
----------
a=6deg+-5deg
0000000901

F:Full load
I:Idle
(1)Set point I
(2)At delivery
----------
----------
a=25deg+-5deg b=39deg+-3deg c=41.5deg+-5deg
----------
----------
a=25deg+-5deg b=39deg+-3deg c=41.5deg+-5deg
Stop lever angle

N:Engine manufacturer's normal use
S:Stop the pump.
(1)Rack position = aa
(2)Rack position bb
(3)Free (at delivery)
(4)Set the stopper bolt (apply red paint).
----------
aa=12mm bb=2.5-0.5mm
----------
a=40deg+-5deg b=30deg+-5deg c=(50deg)
----------
aa=12mm bb=2.5-0.5mm
----------
a=40deg+-5deg b=30deg+-5deg c=(50deg)
0000001501 RACK SENSOR

R:Rack position (mm)
V:Voltage (V)
After installing the rack sensor, confirm the output value (VR).
----------
N1=700r/min Ra=8.4mm VR=1.7+-0.01V
----------
----------
N1=700r/min Ra=8.4mm VR=1.7+-0.01V
----------
0000001601 Q ADJUSTMENT PIPING

Tester fuel pipe A
(B) branch piping
Fuel inlet C
(D) Overflow valve
Piping at standard injection quantity adjustment
1. Because the pump gallery is divided into two, be careful of the fuel piping at adjustment.
----------
----------
----------
----------
Timing setting

(1)Pump vertical direction
(2)Coupling's key groove position at No 1 cylinder's beginning of injection
(3)-
(4)-
----------
----------
a=(0deg)
----------
----------
a=(0deg)
Information:
3-164D, 3-179D, 4-219D, 4-239D, 4-239T, 6-329D, 6-359D, Or 6-359T Engine
Removal
Fig. 1-Oil Cooler LinesDisconnect coolant lines (1, Fig. 1).Remove oil filter (2).
Fig. 2-Oil Cooler NippleUnscrew oil cooler nipple (Fig. 2) and lift oil cooler off of cylinder block.Remove four sided packing from bottom of oil cooler.Repair
Pressure check the coolant side of the oil cooler using 15 psi (103 kPa) (1 bar) maximum air pressure.Remove oil cooler bypass valve by driving it out the bottom of the oil cooler from the top side.
Fig. 3-Oil Cooler Bypass Valve and SpringInspect bypass valve and spring (Fig. 3) for damage and replace as necessary.Installation
Fig. 4-Four Sided PackingInstall new four sided packing (Fig. 4) on bottom of oil cooler.Position oil cooler on engine and install oil cooler nipple.
Fig. 5-Oil Cooler NippleOil cooler nipple torque (Fig. 5) ... 20 to 25 lb-ft(27 to 34 N m) (3.0 to 3.5 kg-m)Connect coolant hoses to oil cooler and install new oil filter (Group 0407).4-276D, 4-276T, 6-414D Or 6414T Engine
Removal
Fig. 6-Oil Cooler Assembly RemovalDisconnect coolant lines (1, Fig. 6) and remove oil filter (2).Remove oil cooler assembly attaching cap screws (3).Remove oil filter housing (4) from oil cooler.Repair
Remove top and bottom covers.
Fig. 7-Remove Oil CoolerUsing a suitable driver, drive oil cooler out of housing from bottom side (Fig. 7).
Fig. 8-Remove Oil Cooler Relief ValveDrive oil cooler bypass valve out the bottom from the top using a pin punch against the top of the valve (Fig. 8).
Fig. 9-Oil CoolerInspect oil cooler for damage or build-up of foreign material and clean as needed.The oil cooler can be pressure checked with a maximum of 50 psi (345 kPa) (3 bar) air pressure.
Fig. 10-Oil Cooler Bypass Valve Spring LengthCheck oil cooler bypass valve spring length:Valve spring length (Fig. 10) ... 1.91 inch(48.5 mm)when compressed with ... 29.5 to 37.5 lb(131 to 167 N)
Fig. 11-Remove O-RingsRemove O-rings from housing at bottom of oil cooler bore.Remove all gasket residue from parts.Installation
Fig. 12-Install Oil Cooler Relief ValvePosition oil cooler relief valve spring (1, Fig. 12), valve (2), and valve seat (3) in bore in bottom of housing (4).
Fig. 13-Drive Oil Cooler Relief Valve SeatUsing a suitable driver (Fig. 13), drive the valve seat into the housing until the seat bottoms.
Fig. 14-O-Ring InstallationInstall new O-rings in housing at bottom of oil cooler bore, black O-ring in upper groove (A, Fig. 14) and red O-ring in lower groove (B).Using new gasket, install oil cooler in housing from top side, being careful not to shear O-rings.Using new gaskets, install top and bottom covers and oil filter housing.Position oil cooler assembly on engine and install cap screws.Connect oil cooler coolant lines and install a new oil filter.
Removal
Fig. 1-Oil Cooler LinesDisconnect coolant lines (1, Fig. 1).Remove oil filter (2).
Fig. 2-Oil Cooler NippleUnscrew oil cooler nipple (Fig. 2) and lift oil cooler off of cylinder block.Remove four sided packing from bottom of oil cooler.Repair
Pressure check the coolant side of the oil cooler using 15 psi (103 kPa) (1 bar) maximum air pressure.Remove oil cooler bypass valve by driving it out the bottom of the oil cooler from the top side.
Fig. 3-Oil Cooler Bypass Valve and SpringInspect bypass valve and spring (Fig. 3) for damage and replace as necessary.Installation
Fig. 4-Four Sided PackingInstall new four sided packing (Fig. 4) on bottom of oil cooler.Position oil cooler on engine and install oil cooler nipple.
Fig. 5-Oil Cooler NippleOil cooler nipple torque (Fig. 5) ... 20 to 25 lb-ft(27 to 34 N m) (3.0 to 3.5 kg-m)Connect coolant hoses to oil cooler and install new oil filter (Group 0407).4-276D, 4-276T, 6-414D Or 6414T Engine
Removal
Fig. 6-Oil Cooler Assembly RemovalDisconnect coolant lines (1, Fig. 6) and remove oil filter (2).Remove oil cooler assembly attaching cap screws (3).Remove oil filter housing (4) from oil cooler.Repair
Remove top and bottom covers.
Fig. 7-Remove Oil CoolerUsing a suitable driver, drive oil cooler out of housing from bottom side (Fig. 7).
Fig. 8-Remove Oil Cooler Relief ValveDrive oil cooler bypass valve out the bottom from the top using a pin punch against the top of the valve (Fig. 8).
Fig. 9-Oil CoolerInspect oil cooler for damage or build-up of foreign material and clean as needed.The oil cooler can be pressure checked with a maximum of 50 psi (345 kPa) (3 bar) air pressure.
Fig. 10-Oil Cooler Bypass Valve Spring LengthCheck oil cooler bypass valve spring length:Valve spring length (Fig. 10) ... 1.91 inch(48.5 mm)when compressed with ... 29.5 to 37.5 lb(131 to 167 N)
Fig. 11-Remove O-RingsRemove O-rings from housing at bottom of oil cooler bore.Remove all gasket residue from parts.Installation
Fig. 12-Install Oil Cooler Relief ValvePosition oil cooler relief valve spring (1, Fig. 12), valve (2), and valve seat (3) in bore in bottom of housing (4).
Fig. 13-Drive Oil Cooler Relief Valve SeatUsing a suitable driver (Fig. 13), drive the valve seat into the housing until the seat bottoms.
Fig. 14-O-Ring InstallationInstall new O-rings in housing at bottom of oil cooler bore, black O-ring in upper groove (A, Fig. 14) and red O-ring in lower groove (B).Using new gasket, install oil cooler in housing from top side, being careful not to shear O-rings.Using new gaskets, install top and bottom covers and oil filter housing.Position oil cooler assembly on engine and install cap screws.Connect oil cooler coolant lines and install a new oil filter.
Have questions with 106672-3282?
Group cross 106672-3282 ZEXEL
Hino
106672-3282
9 400 617 078
220005222A
INJECTION-PUMP ASSEMBLY
EP1
EP1
106672-3282
9 400 617 078
S220005222A
INJECTION-PUMP ASSEMBLY
EP1
EP1