Information injection-pump assembly
BOSCH
9 400 617 077
9400617077
ZEXEL
106672-3272
1066723272
HINO
220005212A
220005212a
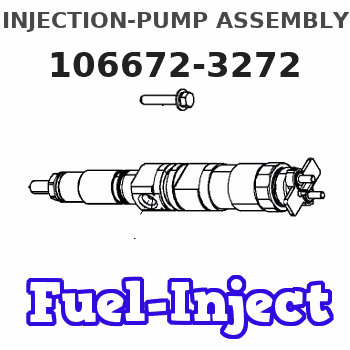
Rating:
Service parts 106672-3272 INJECTION-PUMP ASSEMBLY:
1.
_
5.
AUTOM. ADVANCE MECHANIS
7.
COUPLING PLATE
8.
_
9.
_
11.
Nozzle and Holder
236001642A
12.
Open Pre:MPa(Kqf/cm2)
16.7(170)/23.5(240)
15.
NOZZLE SET
Include in #1:
106672-3272
as INJECTION-PUMP ASSEMBLY
Cross reference number
BOSCH
9 400 617 077
9400617077
ZEXEL
106672-3272
1066723272
HINO
220005212A
220005212a
Zexel num
Bosch num
Firm num
Name
106672-3272
9 400 617 077
220005212A HINO
INJECTION-PUMP ASSEMBLY
EP1 A * K 14CA PE6P,6PD PE
EP1 A * K 14CA PE6P,6PD PE
Calibration Data:
Adjustment conditions
Test oil
1404 Test oil ISO4113 or {SAEJ967d}
1404 Test oil ISO4113 or {SAEJ967d}
Test oil temperature
degC
40
40
45
Nozzle and nozzle holder
105780-8140
Bosch type code
EF8511/9A
Nozzle
105780-0000
Bosch type code
DN12SD12T
Nozzle holder
105780-2080
Bosch type code
EF8511/9
Opening pressure
MPa
17.2
Opening pressure
kgf/cm2
175
Injection pipe
Outer diameter - inner diameter - length (mm) mm 8-3-600
Outer diameter - inner diameter - length (mm) mm 8-3-600
Overflow valve (drive side)
134424-1420
Overflow valve opening pressure (drive side)
kPa
162
147
177
Overflow valve opening pressure (drive side)
kgf/cm2
1.65
1.5
1.8
Overflow valve (governor side)
134424-1720
Overflow valve opening pressure (governor side)
kPa
162
147
177
Overflow valve opening pressure (governor side)
kgf/cm2
1.65
1.5
1.8
Tester oil delivery pressure
kPa
157
157
157
Tester oil delivery pressure
kgf/cm2
1.6
1.6
1.6
Direction of rotation (viewed from drive side)
Right R
Right R
Injection timing adjustment
Direction of rotation (viewed from drive side)
Right R
Right R
Injection order
1-4-2-6-
3-5
Pre-stroke
mm
4.5
4.44
4.5
Beginning of injection position
Drive side NO.1
Drive side NO.1
Difference between angles 1
Cal 1-4 deg. 60 59.75 60.25
Cal 1-4 deg. 60 59.75 60.25
Difference between angles 2
Cyl.1-2 deg. 120 119.75 120.25
Cyl.1-2 deg. 120 119.75 120.25
Difference between angles 3
Cal 1-6 deg. 180 179.75 180.25
Cal 1-6 deg. 180 179.75 180.25
Difference between angles 4
Cal 1-3 deg. 240 239.75 240.25
Cal 1-3 deg. 240 239.75 240.25
Difference between angles 5
Cal 1-5 deg. 300 299.75 300.25
Cal 1-5 deg. 300 299.75 300.25
Injection quantity adjustment
Adjusting point
A
Rack position
8.4
Pump speed
r/min
700
700
700
Average injection quantity
mm3/st.
146.7
144.7
148.7
Max. variation between cylinders
%
0
-2
2
Basic
*
Fixing the lever
*
Boost pressure
kPa
32
32
Boost pressure
mmHg
240
240
Injection quantity adjustment_02
Adjusting point
C
Rack position
8.2
Pump speed
r/min
1075
1075
1075
Average injection quantity
mm3/st.
141.1
135.1
147.1
Max. variation between cylinders
%
0
-5
5
Fixing the lever
*
Boost pressure
kPa
32
32
Boost pressure
mmHg
240
240
Injection quantity adjustment_03
Adjusting point
D
Rack position
7.7
Pump speed
r/min
1200
1200
1200
Average injection quantity
mm3/st.
131
126
136
Max. variation between cylinders
%
0
-5
5
Fixing the lever
*
Boost pressure
kPa
32
32
Boost pressure
mmHg
240
240
Injection quantity adjustment_04
Adjusting point
E
Rack position
9.8+-0.5
Pump speed
r/min
300
300
300
Average injection quantity
mm3/st.
180.6
177.6
183.6
Fixing the lever
*
Boost pressure
kPa
32
32
Boost pressure
mmHg
240
240
Injection quantity adjustment_05
Adjusting point
G
Rack position
6.3
Pump speed
r/min
400
400
400
Average injection quantity
mm3/st.
72.9
70.9
74.9
Fixing the lever
*
Boost pressure
kPa
0
0
0
Boost pressure
mmHg
0
0
0
Injection quantity adjustment_06
Adjusting point
H
Rack position
-
Pump speed
r/min
100
100
100
Average injection quantity
mm3/st.
110
110
Fixing the lever
*
Boost pressure
kPa
0
0
0
Boost pressure
mmHg
0
0
0
Injection quantity adjustment_07
Adjusting point
I
Rack position
4.6+-0.5
Pump speed
r/min
225
225
225
Average injection quantity
mm3/st.
8.4
5.4
11.4
Max. variation between cylinders
%
0
-15
15
Fixing the rack
*
Boost pressure
kPa
0
0
0
Boost pressure
mmHg
0
0
0
Boost compensator adjustment
Pump speed
r/min
700
700
700
Rack position
6.3
Boost pressure
kPa
3.3
3.3
5.3
Boost pressure
mmHg
25
25
40
Boost compensator adjustment_02
Pump speed
r/min
700
700
700
Rack position
8.4
Boost pressure
kPa
18.7
18.7
18.7
Boost pressure
mmHg
140
140
140
Test data Ex:
Governor adjustment

N:Pump speed
R:Rack position (mm)
(1)Lever ratio: RT
(2)Target shim dimension: TH
(3)RACK LIMIT
(4)Set idle at delivery
(5)Damper spring setting: DL
(6)Rack difference between N = N1 and N = N2
----------
RT=0.8 TH=1.7mm DL=4.4-0.2mm N1=1075r/min N2=700r/min
----------
----------
RT=0.8 TH=1.7mm DL=4.4-0.2mm N1=1075r/min N2=700r/min
----------
Speed control lever angle

F:Full speed
----------
----------
a=6deg+-5deg
----------
----------
a=6deg+-5deg
0000000901

F:Full load
I:Idle
(1)Set point I
(2)At delivery
----------
----------
a=25deg+-5deg b=39deg+-3deg c=41.5deg+-5deg
----------
----------
a=25deg+-5deg b=39deg+-3deg c=41.5deg+-5deg
Stop lever angle

N:Pump normal
S:Stop the pump.
----------
----------
a=40deg+-5deg b=50deg+-5deg
----------
----------
a=40deg+-5deg b=50deg+-5deg
0000001501 RACK SENSOR

R:Rack position (mm)
V:Voltage (V)
After installing the rack sensor, confirm the output value (VR).
----------
N1=700r/min Ra=8.4mm VR=1.7+-0.01V
----------
----------
N1=700r/min Ra=8.4mm VR=1.7+-0.01V
----------
0000001601 Q ADJUSTMENT PIPING

Tester fuel pipe A
(B) branch piping
Fuel inlet C
(D) Overflow valve
Piping at standard injection quantity adjustment
1. Because the pump gallery is divided into two, be careful of the fuel piping at adjustment.
----------
----------
----------
----------
Timing setting

(1)Pump vertical direction
(2)Coupling's key groove position at No 1 cylinder's beginning of injection
(3)-
(4)-
----------
----------
a=(0deg)
----------
----------
a=(0deg)
Information:
Fig. 4-Axial Bearing Movement CheckFasten dial indicator to turbine housing so that the indicator tip rests on the end of the shaft (Fig. 4).Move the shaft back and forth axially by hand. The total axial movement of the shaft should be 0.001 to 0.004 in. (0.03 to 0.10 mm). If not repair or replace unit.Repair
As each part is removed, place it in a clean protective container.Refer to Fig. 6 for part identification and relationship.
Fig. 5-Turbine Housing RemovalScribe a line on the mating surfaces of the turbine housing (1, Fig. 5) and center housing (2) to aid in alignment during reassembly.Remove the turbine housing-to-center housing cap screws (5, Fig. 5), lock plates (3), and clamps (4). Carefully remove turbine housing.
Fig. 6-Turbocharger Exploded View
Fig. 7-Removing Compressor (Impeller)Mount a suitable holding fixture (1, Fig. 7) (see Group 0499 Special Tools - Turbocharger) in a vise.Insert the turbine wheel into the fixture.Use a double universal socket to remove the compressor wheel retaining nut to avoid possible bending of the shaft.Remove the impeller (2, Fig. 7) from the shaft.
Fig. 8-Shaft and Wheel AssemblyRemove the turbine wheel and shaft assembly (3, Fig. 8) from the center housing keeping it centered until it is clear of the housing. Fig. 8 shows the turbine wheel assembly (1). The piston ring (2) can now be removed.Remove the back plate to center housing cap screw (16, Fig. 6) and lock plates (15).Carefully remove back plate by tapping with a soft mallet.
Fig. 9-Back Plate Assembly IMPORTANT: Back plate (2, Fig. 9) and the spring (1) are sold only as an assembly. The installed depth of the spring is a controlled dimension. Therefore, do not remove or replace the spring by itself. Cleaning can be done without removing the spring from the back plate.
Fig. 10-Removing Thrust Collar and Thrust WasherRemove the thrust collar (2, Fig. 10) and thrust washer (3) as shown in Fig. 10. Remove the O-ring (1) from housing and piston ring (4) from thrust collar.
Fig. 11-Retaining Ring and Bearing RemovalRemove retaining rings (2, Fig. 11) with a No. 501 Waldes Truarc Snap Ring Pliers, if snap rings are used, and bearings (1) from both sides of the center housing.Cleaning
Before cleaning, inspect parts for signs of burning, rubbing, or other damage which might not be evident after cleaning.Soak all parts in clean carbon solvent for approximately 25 minutes. After soaking use a stiff bristle brush to remove all dirt particles. Dry parts thoroughly. Normally, a light accumulation of carbon deposits will not affect turbine wheel operation.Inspection
Replace the following parts: O-ring (13, Fig. 6), lock plates (6, 15, and 21) piston rings (8 and 18), retaining rings (11), and all damaged nuts and bolts. If bearings and thrust washers show signs of nicks, scores, shellac deposits, or foreign material embedment, replace them.After cleaning, if any of the parts in the assembly show signs of rubbing, scoring, scratches, or seizure, replace them.Assembly
Be sure each part is clean before assembling. As parts are assembled, cover openings to prevent entry of dirt
Have questions with 106672-3272?
Group cross 106672-3272 ZEXEL
Hino
106672-3272
9 400 617 077
220005212A
INJECTION-PUMP ASSEMBLY
EP1
EP1