Information injection-pump assembly
ZEXEL
106672-2190
1066722190
MITSUBISHI-HEAV
0429050651
0429050651
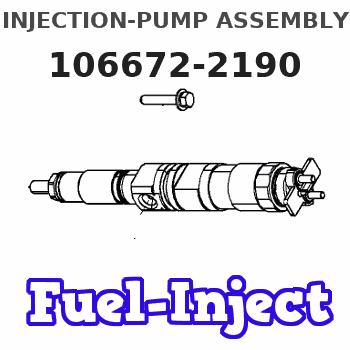
Rating:
Service parts 106672-2190 INJECTION-PUMP ASSEMBLY:
1.
_
2.
FUEL INJECTION PUMP
5.
AUTOM. ADVANCE MECHANIS
7.
COUPLING PLATE
8.
_
9.
_
11.
Nozzle and Holder
12.
Open Pre:MPa(Kqf/cm2)
29.4{300}
15.
NOZZLE SET
Include in #1:
106672-2190
as INJECTION-PUMP ASSEMBLY
Cross reference number
ZEXEL
106672-2190
1066722190
MITSUBISHI-HEAV
0429050651
0429050651
Zexel num
Bosch num
Firm num
Name
Calibration Data:
Adjustment conditions
Test oil
1404 Test oil ISO4113 or {SAEJ967d}
1404 Test oil ISO4113 or {SAEJ967d}
Test oil temperature
degC
40
40
45
Nozzle
105015-3640
Bosch type code
DLL165S288NP85
Nozzle holder
105040-2140
Opening pressure
MPa
29.4
Opening pressure
kgf/cm2
300
Injection pipe
Outer diameter - inner diameter - length (mm) mm 6-2-1130
Outer diameter - inner diameter - length (mm) mm 6-2-1130
Overflow valve
131424-1520
Overflow valve opening pressure
kPa
157
123
191
Overflow valve opening pressure
kgf/cm2
1.6
1.25
1.95
Tester oil delivery pressure
kPa
157
157
157
Tester oil delivery pressure
kgf/cm2
1.6
1.6
1.6
Direction of rotation (viewed from drive side)
Left L
Left L
Injection timing adjustment
Direction of rotation (viewed from drive side)
Left L
Left L
Injection order
1-5-3-6-
2-4
Pre-stroke
mm
3.4
3.35
3.45
Beginning of injection position
Governor side NO.1
Governor side NO.1
Difference between angles 1
Cal 1-5 deg. 60 59.5 60.5
Cal 1-5 deg. 60 59.5 60.5
Difference between angles 2
Cal 1-3 deg. 120 119.5 120.5
Cal 1-3 deg. 120 119.5 120.5
Difference between angles 3
Cal 1-6 deg. 180 179.5 180.5
Cal 1-6 deg. 180 179.5 180.5
Difference between angles 4
Cyl.1-2 deg. 240 239.5 240.5
Cyl.1-2 deg. 240 239.5 240.5
Difference between angles 5
Cal 1-4 deg. 300 299.5 300.5
Cal 1-4 deg. 300 299.5 300.5
Injection quantity adjustment
Adjusting point
A
Rack position
18
Pump speed
r/min
750
750
750
Average injection quantity
mm3/st.
330
321
339
Max. variation between cylinders
%
0
-3
3
Basic
*
Fixing the rack
*
Injection quantity adjustment_02
Adjusting point
B
Rack position
18
Pump speed
r/min
450
450
450
Average injection quantity
mm3/st.
338
328
348
Max. variation between cylinders
%
0
-5
5
Fixing the rack
*
Injection quantity adjustment_03
Adjusting point
C
Rack position
8
Pump speed
r/min
250
250
250
Average injection quantity
mm3/st.
30
27
33
Max. variation between cylinders
%
0
-10
10
Fixing the rack
*
Injection quantity adjustment_04
Adjusting point
D
Rack position
5.4
Pump speed
r/min
750
750
750
Average injection quantity
mm3/st.
30
25
35
Fixing the rack
*
Test data Ex:
Governor adjustment
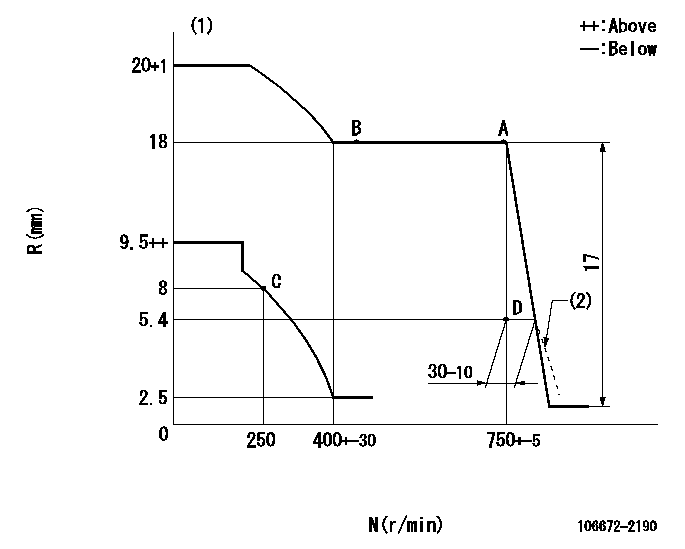
N:Pump speed
R:Rack position (mm)
(1)Target notch: K
(2)Idle sub spring setting: L1.
----------
K=7 L1=5.6-0.5mm
----------
----------
K=7 L1=5.6-0.5mm
----------
Speed control lever angle

F:Full speed
S:Stop
----------
----------
a=(23deg) b=32deg+-3deg
----------
----------
a=(23deg) b=32deg+-3deg
0000000901

F:Full load
I:Idle
S:Stop
----------
----------
a=5deg+-5deg b=31deg+-3deg c=7deg+-3deg
----------
----------
a=5deg+-5deg b=31deg+-3deg c=7deg+-3deg
Information:
To Reassemble
1. Fit oil feed connection to rocker shaft and secure with the locating screw, ensuring that the screw enters the locating hole in the shaft.2. Refit the support brackets, springs, and rocker levers in the correct order (Fig. E.4). The support brackets are interchangeable and when fitting them ensure that the securing stud/setscrew holes are to the right viewing the shaft from the front end, with each pair of rockers inclined away from each other at the valve end.3. Fit securing washer and circlip to each end of the shaft.Push Rods
Check the push rods for straightness. If any are bent, fit replacements.Valve Stem Oil Seals
Where oversize valves are fitted, always ensure that correct size valve seals or 'O' rings are used.
E3 1. Collets2. Valve Spring Cap3. Oil Deflector4. Inner Valve Spring5. Outer Valve Spring6. Valve Spring Seat7. Exhaust Valve8. Inlet ValveAll hydraulically governed engines and certain mechanically governed engines have rubber oil deflectors fitted to inlet valve stems only (see Fig. E.3). When fitting these oil deflectors, the open end should be towards the cylinder head.With the majority of mechanically governed engines, oil seals are fitted to both inlet and exhaust valves. Earlier engines had a shallow rubber oil deflector fitted to the valve stems and positioned above the conical valve spring seating collar, the open end of the deflector being fitted towards the cylinder head. Later engines have a thin valve spring seating washer and a rubber oil seal which fits over the integral valve guide protrusion. In some cases, this latter seal has a nylon insert. The later sealing arrangement, due to a change in the diameter of the valve guide protrusion, is not interchangeable with the earlier sealing arrangement.On some engines, the seals are manufactured from Viton or silicon rubber material and they have a garter spring fitted around their outer circumference.In manufacturing, some engines have a red coloured material for inlet valve seals and black for exhaust valve seals. The red seal may only be fitted over the inlet valve. It is unsuitable for exhaust valves but the black seal may be fitted to either exhaust or inlet.The 4.2482 engine has a valve stem oil seal on both inlet and exhaust valves. The seals have garter springs round the seal neck for improved oil control.To Re-Assemble the Cylinder Head
1. Lightly oil valve stems.2. Fit valve to its correct guide or bore.3. Fit valve stem oil seals.4. Locate spring seat washers, valve springs and spring caps in position.5. Compress each valve spring and fit the valve collets.
E11, Valve Cap Sealing Arrangement As from Engine No. LD-----U778518H, 'O' ring seals have been fitted in the valve spring caps under the collets. The valve spring caps have been changed which have a deeper body so that the seal can be fitted as shown in Fig. E.11. The new caps are fitted to both valves, but the seals are fitted to exhaust valves only. T4.236 engines have two 'O' rings fitted in each valve spring cap.Cylinder Head
1. Fit oil feed connection to rocker shaft and secure with the locating screw, ensuring that the screw enters the locating hole in the shaft.2. Refit the support brackets, springs, and rocker levers in the correct order (Fig. E.4). The support brackets are interchangeable and when fitting them ensure that the securing stud/setscrew holes are to the right viewing the shaft from the front end, with each pair of rockers inclined away from each other at the valve end.3. Fit securing washer and circlip to each end of the shaft.Push Rods
Check the push rods for straightness. If any are bent, fit replacements.Valve Stem Oil Seals
Where oversize valves are fitted, always ensure that correct size valve seals or 'O' rings are used.
E3 1. Collets2. Valve Spring Cap3. Oil Deflector4. Inner Valve Spring5. Outer Valve Spring6. Valve Spring Seat7. Exhaust Valve8. Inlet ValveAll hydraulically governed engines and certain mechanically governed engines have rubber oil deflectors fitted to inlet valve stems only (see Fig. E.3). When fitting these oil deflectors, the open end should be towards the cylinder head.With the majority of mechanically governed engines, oil seals are fitted to both inlet and exhaust valves. Earlier engines had a shallow rubber oil deflector fitted to the valve stems and positioned above the conical valve spring seating collar, the open end of the deflector being fitted towards the cylinder head. Later engines have a thin valve spring seating washer and a rubber oil seal which fits over the integral valve guide protrusion. In some cases, this latter seal has a nylon insert. The later sealing arrangement, due to a change in the diameter of the valve guide protrusion, is not interchangeable with the earlier sealing arrangement.On some engines, the seals are manufactured from Viton or silicon rubber material and they have a garter spring fitted around their outer circumference.In manufacturing, some engines have a red coloured material for inlet valve seals and black for exhaust valve seals. The red seal may only be fitted over the inlet valve. It is unsuitable for exhaust valves but the black seal may be fitted to either exhaust or inlet.The 4.2482 engine has a valve stem oil seal on both inlet and exhaust valves. The seals have garter springs round the seal neck for improved oil control.To Re-Assemble the Cylinder Head
1. Lightly oil valve stems.2. Fit valve to its correct guide or bore.3. Fit valve stem oil seals.4. Locate spring seat washers, valve springs and spring caps in position.5. Compress each valve spring and fit the valve collets.
E11, Valve Cap Sealing Arrangement As from Engine No. LD-----U778518H, 'O' ring seals have been fitted in the valve spring caps under the collets. The valve spring caps have been changed which have a deeper body so that the seal can be fitted as shown in Fig. E.11. The new caps are fitted to both valves, but the seals are fitted to exhaust valves only. T4.236 engines have two 'O' rings fitted in each valve spring cap.Cylinder Head