Information injection-pump assembly
BOSCH
9 400 612 042
9400612042
ZEXEL
106671-9960
1066719960

Rating:
Service parts 106671-9960 INJECTION-PUMP ASSEMBLY:
1.
_
7.
COUPLING PLATE
8.
_
9.
_
10.
NOZZLE AND HOLDER ASSY
11.
Nozzle and Holder
12.
Open Pre:MPa(Kqf/cm2)
13.
NOZZLE-HOLDER
14.
NOZZLE
15.
NOZZLE SET
Include in #1:
106671-9960
as INJECTION-PUMP ASSEMBLY
Cross reference number
BOSCH
9 400 612 042
9400612042
ZEXEL
106671-9960
1066719960
Zexel num
Bosch num
Firm num
Name
Calibration Data:
Adjustment conditions
Test oil
1404 Test oil ISO4113 or {SAEJ967d}
1404 Test oil ISO4113 or {SAEJ967d}
Test oil temperature
degC
40
40
45
Nozzle and nozzle holder
105780-8250
Bosch type code
1 688 901 101
Nozzle
105780-0120
Bosch type code
1 688 901 990
Nozzle holder
105780-2190
Opening pressure
MPa
20.7
Opening pressure
kgf/cm2
211
Injection pipe
Outer diameter - inner diameter - length (mm) mm 8-3-600
Outer diameter - inner diameter - length (mm) mm 8-3-600
Overflow valve
134424-4120
Overflow valve opening pressure
kPa
255
221
289
Overflow valve opening pressure
kgf/cm2
2.6
2.25
2.95
Tester oil delivery pressure
kPa
255
255
255
Tester oil delivery pressure
kgf/cm2
2.6
2.6
2.6
Direction of rotation (viewed from drive side)
Right R
Right R
Injection timing adjustment
Direction of rotation (viewed from drive side)
Right R
Right R
Injection order
1-5-3-6-
2-4
Pre-stroke
mm
3.9
3.85
3.95
Beginning of injection position
Drive side NO.1
Drive side NO.1
Difference between angles 1
Cal 1-5 deg. 60 59.5 60.5
Cal 1-5 deg. 60 59.5 60.5
Difference between angles 2
Cal 1-3 deg. 120 119.5 120.5
Cal 1-3 deg. 120 119.5 120.5
Difference between angles 3
Cal 1-6 deg. 180 179.5 180.5
Cal 1-6 deg. 180 179.5 180.5
Difference between angles 4
Cyl.1-2 deg. 240 239.5 240.5
Cyl.1-2 deg. 240 239.5 240.5
Difference between angles 5
Cal 1-4 deg. 300 299.5 300.5
Cal 1-4 deg. 300 299.5 300.5
Injection quantity adjustment
Adjusting point
-
Rack position
13.4
Pump speed
r/min
1100
1100
1100
Average injection quantity
mm3/st.
136
134
138
Max. variation between cylinders
%
0
-2
2
Basic
*
Fixing the rack
*
Standard for adjustment of the maximum variation between cylinders
*
Injection quantity adjustment_02
Adjusting point
Z
Rack position
8+-0.5
Pump speed
r/min
440
440
440
Average injection quantity
mm3/st.
16
14.5
17.5
Max. variation between cylinders
%
0
-15
15
Fixing the rack
*
Standard for adjustment of the maximum variation between cylinders
*
Injection quantity adjustment_03
Adjusting point
A
Rack position
R1(13.4)
Pump speed
r/min
1100
1100
1100
Average injection quantity
mm3/st.
136
134
138
Basic
*
Fixing the lever
*
Boost pressure
kPa
32
32
Boost pressure
mmHg
240
240
Injection quantity adjustment_04
Adjusting point
B
Rack position
R1-1.5
Pump speed
r/min
600
600
600
Average injection quantity
mm3/st.
132
122
142
Fixing the lever
*
Boost pressure
kPa
32
32
Boost pressure
mmHg
240
240
Boost compensator adjustment
Pump speed
r/min
500
500
500
Rack position
R2-1.3
Boost pressure
kPa
6.7
5.4
8
Boost pressure
mmHg
50
40
60
Boost compensator adjustment_02
Pump speed
r/min
500
500
500
Rack position
R2(R1-1.
5)
Boost pressure
kPa
18.7
18.7
18.7
Boost pressure
mmHg
140
140
140
Timer adjustment
Pump speed
r/min
750--
Advance angle
deg.
0
0
0
Remarks
Start
Start
Timer adjustment_02
Pump speed
r/min
700
Advance angle
deg.
0.5
Timer adjustment_03
Pump speed
r/min
930
Advance angle
deg.
4
3.5
4.5
Remarks
Finish
Finish
Test data Ex:
Governor adjustment
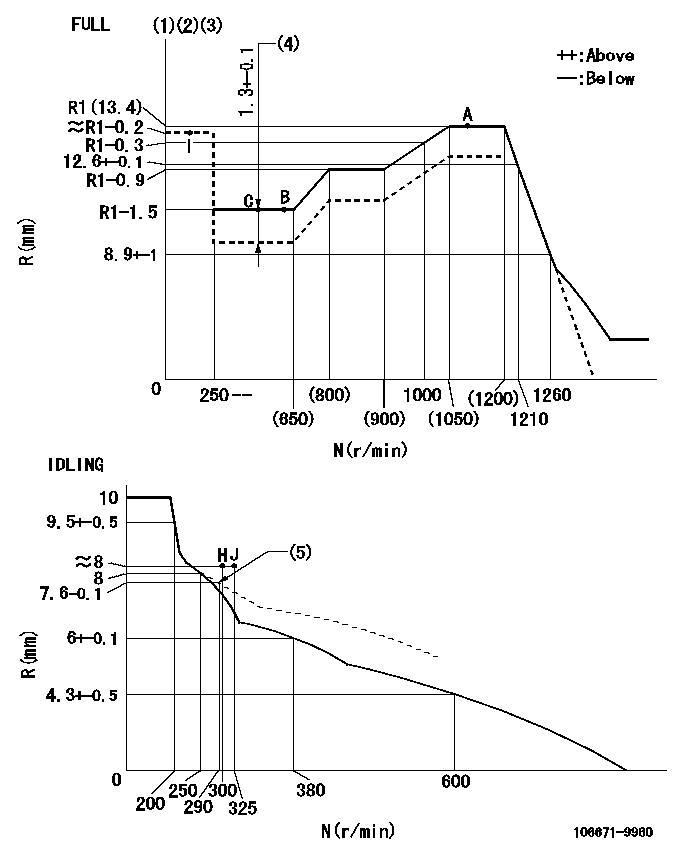
N:Pump speed
R:Rack position (mm)
(1)Torque cam stamping: T1
(2)Tolerance for racks not indicated: +-0.05mm.
(3)Microswitch adjustment unnecessary.
(4)Boost compensator stroke
(5)Damper spring setting
----------
T1=AG74
----------
----------
T1=AG74
----------
Speed control lever angle
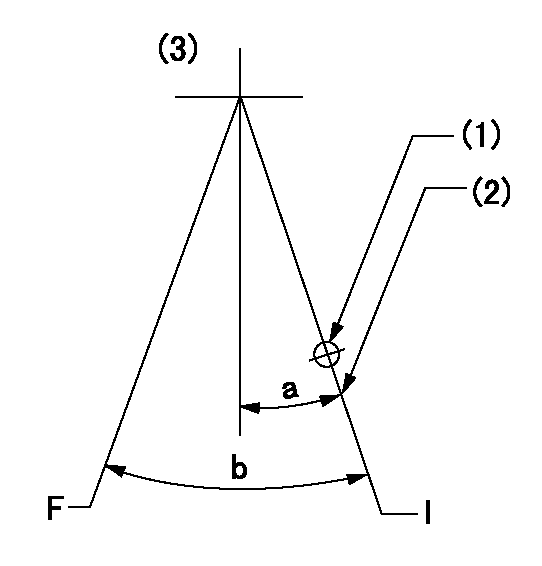
F:Full speed
I:Idle
(1)Use the hole at R = aa
(2)Stopper bolt set position 'H'
(3)Viewed from feed pump side.
----------
aa=70mm
----------
a=14deg+-5deg b=40.5deg+-3deg
----------
aa=70mm
----------
a=14deg+-5deg b=40.5deg+-3deg
Stop lever angle
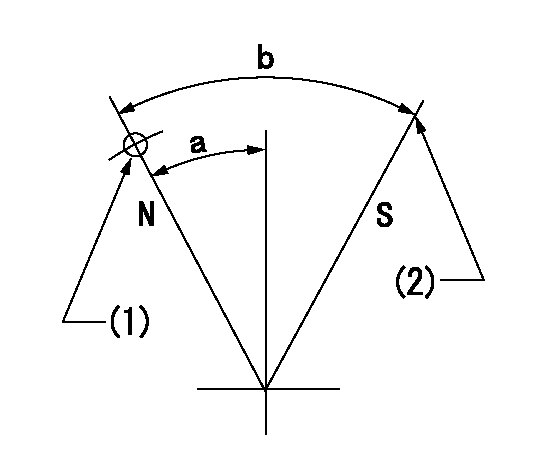
N:Pump normal
S:Stop the pump.
(1)Use the hole at R = aa
(2)At pump speed bb and rack position cc, set the stopper bolt.
----------
aa=40mm bb=0r/min cc=1.5+-0.3mm
----------
a=20deg+-5deg b=44deg+-5deg
----------
aa=40mm bb=0r/min cc=1.5+-0.3mm
----------
a=20deg+-5deg b=44deg+-5deg
Timing setting
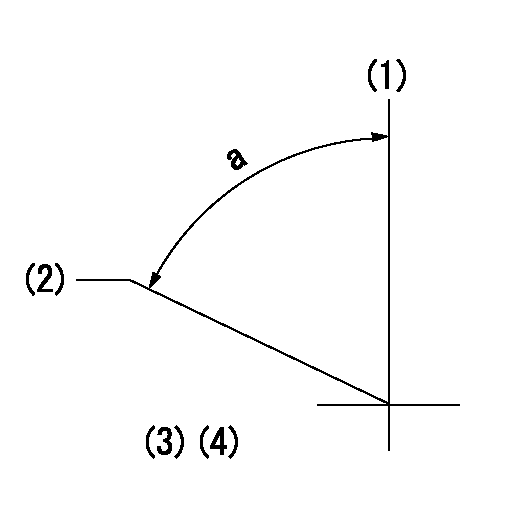
(1)Pump vertical direction
(2)Coupling's key groove position for the No. 6 cylinder's beginning of injection
(3)-
(4)-
----------
----------
a=(50deg)
----------
----------
a=(50deg)
Information:
Table 1
Revision Summary of Changes
01 Updated Illustration 1
02 Updated effectivity Introduction
The problem that is identified below does not have a known permanent solution. Until a permanent solution is known, use the solution that is identified below.Problem
Inadequate battery negative bonding to engine block causing incorrect diagnostic codes/tripping in the units that are disconnected from the engine-mounted charging alternator.Solution
Do not operate or work on this product unless you have read and understood the instruction and warnings in the relevant Operation and Maintenance Manuals and relevant service literature. Failure to follow the instructions or heed the warnings could result in injury or death. Proper care is your responsibility.
Illustration 1 g06575359
Generator set isolated DC supply system
(1) Electronic subsystem 1
(2) Electronic subsystem 2
(3) Electronic subsystem 3
(4) Generator set subsystem loads
(5) Engine ECM
(6) Starter
(7) Electronics power buss
(8) Electronics single point ground
(9) 12AWG (4 Sq.mm) bonding jumper (multi strand) wire
(10) Battery disconnect switch
(11) Customer ground connection
(12) Battery
(13) Battery charger
(14) Customer scopeNote: The red color connections in Illustration 1 are to be connected at customer site. Connections should be made after the battery disconnect switch (10).Caterpillar is aware of the problem, and is recommending the following interim solution.Install a 12AWG (4 Sq.mm) bonding jumper (multi strand) wire (9) connecting all electrical sensor grounding points (8) at the power distribution box to the customer ground connection (11). Refer to Illustration 1.Reference: Refer to Special Instruction, REHS4634, "Grounding Design Guide for Electric Power Generation Products".