Information injection-pump assembly
ZEXEL
106671-9820
1066719820
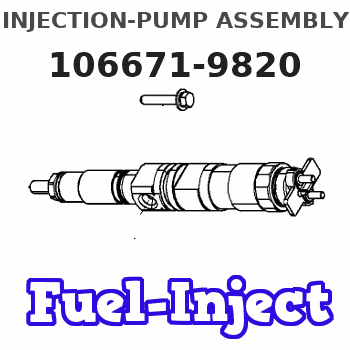
Rating:
Service parts 106671-9820 INJECTION-PUMP ASSEMBLY:
1.
_
7.
COUPLING PLATE
8.
_
9.
_
10.
NOZZLE AND HOLDER ASSY
11.
Nozzle and Holder
12.
Open Pre:MPa(Kqf/cm2)
13.
NOZZLE-HOLDER
14.
NOZZLE
15.
NOZZLE SET
Include in #1:
106671-9820
as INJECTION-PUMP ASSEMBLY
Cross reference number
ZEXEL
106671-9820
1066719820
Zexel num
Bosch num
Firm num
Name
106671-9820
DPICO
INJECTION-PUMP ASSEMBLY
6D22 * Q
6D22 * Q
Calibration Data:
Adjustment conditions
Test oil
1404 Test oil ISO4113 or {SAEJ967d}
1404 Test oil ISO4113 or {SAEJ967d}
Test oil temperature
degC
40
40
45
Nozzle and nozzle holder
105780-8250
Bosch type code
1 688 901 101
Nozzle
105780-0120
Bosch type code
1 688 901 990
Nozzle holder
105780-2190
Opening pressure
MPa
20.7
Opening pressure
kgf/cm2
211
Injection pipe
Outer diameter - inner diameter - length (mm) mm 8-3-600
Outer diameter - inner diameter - length (mm) mm 8-3-600
Overflow valve
131425-0220
Overflow valve opening pressure
kPa
157
157
157
Overflow valve opening pressure
kgf/cm2
1.6
1.6
1.6
Tester oil delivery pressure
kPa
255
255
255
Tester oil delivery pressure
kgf/cm2
2.6
2.6
2.6
Direction of rotation (viewed from drive side)
Right R
Right R
Injection timing adjustment
Direction of rotation (viewed from drive side)
Right R
Right R
Injection order
1-5-3-6-
2-4
Pre-stroke
mm
3.9
3.85
3.95
Beginning of injection position
Governor side NO.1
Governor side NO.1
Difference between angles 1
Cal 1-5 deg. 60 59.5 60.5
Cal 1-5 deg. 60 59.5 60.5
Difference between angles 2
Cal 1-3 deg. 120 119.5 120.5
Cal 1-3 deg. 120 119.5 120.5
Difference between angles 3
Cal 1-6 deg. 180 179.5 180.5
Cal 1-6 deg. 180 179.5 180.5
Difference between angles 4
Cyl.1-2 deg. 240 239.5 240.5
Cyl.1-2 deg. 240 239.5 240.5
Difference between angles 5
Cal 1-4 deg. 300 299.5 300.5
Cal 1-4 deg. 300 299.5 300.5
Injection quantity adjustment
Adjusting point
-
Rack position
12.3
Pump speed
r/min
700
700
700
Each cylinder's injection qty
mm3/st.
129
125.8
132.2
Basic
*
Fixing the rack
*
Standard for adjustment of the maximum variation between cylinders
*
Injection quantity adjustment_02
Adjusting point
Z
Rack position
8+-0.5
Pump speed
r/min
570
570
570
Each cylinder's injection qty
mm3/st.
15
13
17
Fixing the rack
*
Standard for adjustment of the maximum variation between cylinders
*
Injection quantity adjustment_03
Adjusting point
A
Rack position
R1(12.3)
Pump speed
r/min
700
700
700
Average injection quantity
mm3/st.
129
128
130
Basic
*
Fixing the lever
*
Timer adjustment
Pump speed
r/min
750--
Advance angle
deg.
0
0
0
Remarks
Start
Start
Timer adjustment_02
Pump speed
r/min
-
Advance angle
deg.
1.5
1
2
Remarks
Measure the actual speed.
Measure the actual speed.
Timer adjustment_03
Pump speed
r/min
-
Advance angle
deg.
0
0
0
Remarks
Measure the actual speed.
Measure the actual speed.
Timer adjustment_04
Pump speed
r/min
700
Advance angle
deg.
0.5
Timer adjustment_05
Pump speed
r/min
1100
Advance angle
deg.
3.5
3
4
Timer adjustment_06
Pump speed
r/min
-
Advance angle
deg.
4
3.5
4.5
Remarks
Measure the actual speed, stop
Measure the actual speed, stop
Test data Ex:
Governor adjustment
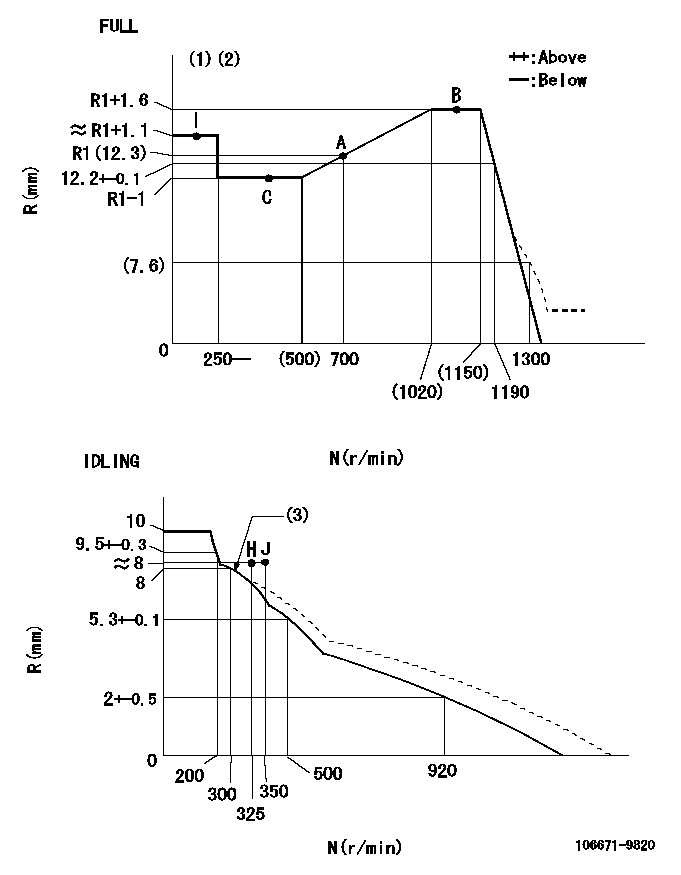
N:Pump speed
R:Rack position (mm)
(1)Torque cam stamping: T1
(2)Tolerance for racks not indicated: +-0.05mm.
(3)Damper spring setting: DL
----------
T1=AG11 DL=7.9-0.2mm
----------
----------
T1=AG11 DL=7.9-0.2mm
----------
Speed control lever angle
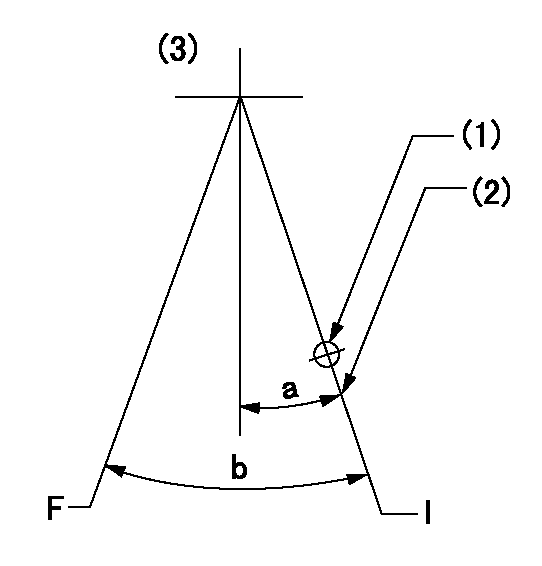
F:Full speed
I:Idle
(1)Use the hole at R = aa
(2)Stopper bolt setting
(3)Viewed from feed pump side.
----------
aa=37.5mm
----------
a=0deg+-5deg b=(33deg)+-3deg
----------
aa=37.5mm
----------
a=0deg+-5deg b=(33deg)+-3deg
Stop lever angle

N:Pump normal
S:Stop the pump.
(1)Use the hole at R = aa
(2)Set the stopper bolt so that speed = bb and rack position = cc. (Confirm non-injection.)
----------
aa=45mm bb=1100r/min cc=3.5+-0.3mm
----------
a=29.5deg+-5deg b=40deg+-5deg
----------
aa=45mm bb=1100r/min cc=3.5+-0.3mm
----------
a=29.5deg+-5deg b=40deg+-5deg
0000001501 MICRO SWITCH
Adjustment of the micro-switch
Adjust the bolt to obtain the following lever position when the micro-switch is ON.
(1)Speed N1
(2)Rack position Ra
----------
N1=475r/min Ra=7.6+-0.1mm
----------
----------
N1=475r/min Ra=7.6+-0.1mm
----------
Timing setting

(1)Pump vertical direction
(2)Coupling's key groove position at No 1 cylinder's beginning of injection
(3)B.T.D.C.: aa
(4)-
----------
aa=11deg
----------
a=(5deg)
----------
aa=11deg
----------
a=(5deg)
Information:
Illustration 3 g06519715
DOC brackets
Illustration 4 g06519717
DOC
Connect the welding ground cable directly to the DOC brackets or the DOC that will be welded. Place the ground cable as close as possible to the weld. This location will reduce the possibility of welding current damage bearings, hydraulic components, electrical components, and ground straps.Note: If electrical components are used as a ground for the welder, current flow from the welder could severely damage the component. Current flow from the welder could also severely damage electrical components that are located between the welder ground and the weld.
Illustration 5 g06519270
Weld blanket
Illustration 6 g06519272
Use a weld blanket draped over the engine to protect the engine from weld splatter. Likely need 2 or 3 blankets to cover between DOCs and the entire engine from splatter.
Illustration 7 g06519274
Illustration 8 g06519277
(1) 536-5400 Plate
Clean the top surface in the two locations where plates (1) will be welded in place with either a wire wheel or a flap disk.Note: Failure to clean the weld area could result in poor weld quality.
Illustration 9 g06519323
(D1) 6 2 mm (0.236 0.079 inch)
Illustration 10 g06519297
(D1) 6 2 mm (0.236 0.079 inch)
(D2) 43 3 mm (1.693 0.118 inch)
Illustration 11 g06519348
(D2) 43 3 mm (1.693 0.118 inch)
Set the plates on the top side of the housing and line up perpendicular to the front face. Position the plates to dimension (D1) from the front edge of the top plate.
Position the plates to dimension (D2) from the far edge of the rounded plate. There is a chamfer and fillet weld that will make measurements less precise. Use a tape measure to position.Note: Etching marks may also be present on the top of the unit and can be used for further positional guidance.
Illustration 12 g06519373
(W1) Tack weld
With the plates in place, add tack welds (W1) to the plates shown in Illustration 12. Use 308L weld wire.
Illustration 13 g06519408
(W2) 50 to 100 mm (1.969 to 3.937 inch)
Skip fillet weld (W2) down the side of each plate and then weld at the ends of each plates. Use 308L weld wire.
Illustration 14 g06519430
Finished product
Verify the weld quality and look for the following:
Cracks
Porosity
Inclusions
Convexity/Excess Weld Material
Concavity/Under Fill
Excess Penetration
Lack of Penetration
Fillet Weld - Undersize
Lack of Fusion
Undercut
Toe Radius
Overlap
Poor Restarts/Tie-ins
Cleaning/Grinding
Spatter/Arc Strike/Wire Stub
Illustration 15 g06519435
Mark the new plates with "THIS SIDE UP".Note: Make sure that the text is visible and stands out on the DOC.
Have questions with 106671-9820?
Group cross 106671-9820 ZEXEL
Dpico
106671-9820
INJECTION-PUMP ASSEMBLY
6D22
6D22