Information injection-pump assembly
ZEXEL
106671-9630
1066719630

Rating:
Cross reference number
ZEXEL
106671-9630
1066719630
Zexel num
Bosch num
Firm num
Name
106671-9630
INJECTION-PUMP ASSEMBLY
Calibration Data:
Adjustment conditions
Test oil
1404 Test oil ISO4113 or {SAEJ967d}
1404 Test oil ISO4113 or {SAEJ967d}
Test oil temperature
degC
40
40
45
Nozzle and nozzle holder
105780-8140
Bosch type code
EF8511/9A
Nozzle
105780-0000
Bosch type code
DN12SD12T
Nozzle holder
105780-2080
Bosch type code
EF8511/9
Opening pressure
MPa
17.2
Opening pressure
kgf/cm2
175
Injection pipe
Outer diameter - inner diameter - length (mm) mm 8-3-600
Outer diameter - inner diameter - length (mm) mm 8-3-600
Overflow valve
131424-1520
Overflow valve opening pressure
kPa
157
123
191
Overflow valve opening pressure
kgf/cm2
1.6
1.25
1.95
Tester oil delivery pressure
kPa
157
157
157
Tester oil delivery pressure
kgf/cm2
1.6
1.6
1.6
Direction of rotation (viewed from drive side)
Left L
Left L
Injection timing adjustment
Direction of rotation (viewed from drive side)
Left L
Left L
Injection order
1-5-3-6-
2-4
Pre-stroke
mm
3.8
3.75
3.85
Beginning of injection position
Drive side NO.1
Drive side NO.1
Difference between angles 1
Cal 1-5 deg. 60 59.5 60.5
Cal 1-5 deg. 60 59.5 60.5
Difference between angles 2
Cal 1-3 deg. 120 119.5 120.5
Cal 1-3 deg. 120 119.5 120.5
Difference between angles 3
Cal 1-6 deg. 180 179.5 180.5
Cal 1-6 deg. 180 179.5 180.5
Difference between angles 4
Cyl.1-2 deg. 240 239.5 240.5
Cyl.1-2 deg. 240 239.5 240.5
Difference between angles 5
Cal 1-4 deg. 300 299.5 300.5
Cal 1-4 deg. 300 299.5 300.5
Injection quantity adjustment
Adjusting point
A
Rack position
10.6
Pump speed
r/min
1050
1050
1050
Average injection quantity
mm3/st.
168
166
170
Max. variation between cylinders
%
0
-3
3
Basic
*
Fixing the lever
*
Injection quantity adjustment_02
Adjusting point
C
Rack position
5.7+-0.5
Pump speed
r/min
325
325
325
Average injection quantity
mm3/st.
14
12.5
15.5
Max. variation between cylinders
%
0
-15
15
Fixing the rack
*
Timer adjustment
Pump speed
r/min
-
Advance angle
deg.
0.5
Remarks
Measure the actual speed.
Measure the actual speed.
Timer adjustment_02
Pump speed
r/min
850
Remarks
Measure the actual advance angle.
Measure the actual advance angle.
Timer adjustment_03
Pump speed
r/min
-
Advance angle
deg.
3
2.5
3.5
Remarks
Measure the actual speed, stop
Measure the actual speed, stop
Test data Ex:
Governor adjustment
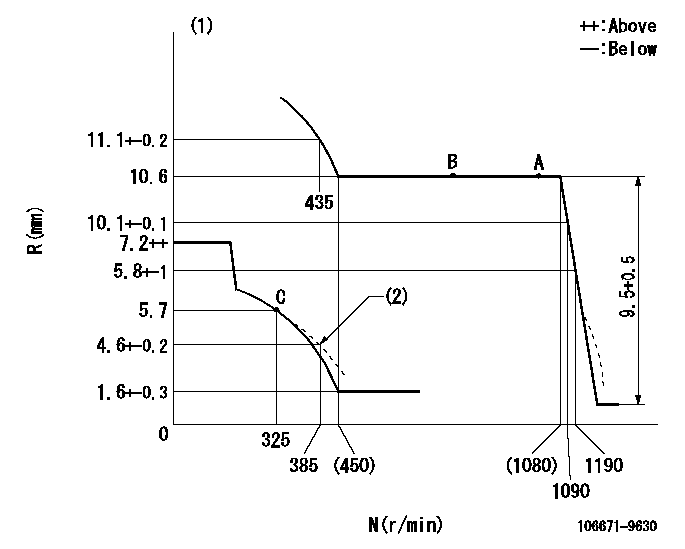
N:Pump speed
R:Rack position (mm)
(1)Tolerance for racks not indicated: +-0.05mm.
(2)Damper spring setting
----------
----------
----------
----------
Speed control lever angle

F:Full speed
----------
----------
a=(16.5deg)+-5deg
----------
----------
a=(16.5deg)+-5deg
0000000901
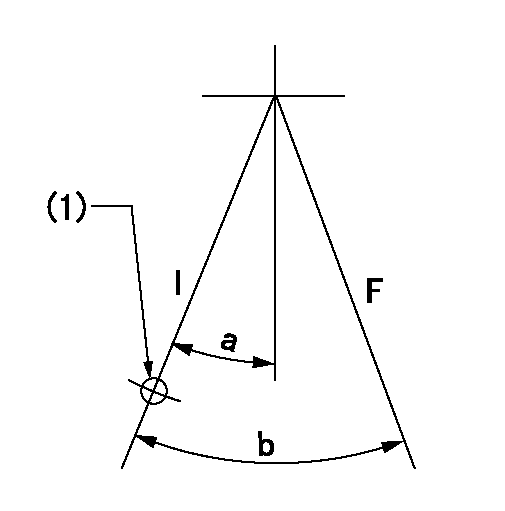
F:Full load
I:Idle
(1)Use the hole at R = aa
----------
aa=50mm
----------
a=21deg+-5deg b=33deg+-3deg
----------
aa=50mm
----------
a=21deg+-5deg b=33deg+-3deg
Stop lever angle

N:Pump normal
S:Stop the pump.
(1)Drive side
----------
----------
a=32deg+-5deg b=64deg+-5deg
----------
----------
a=32deg+-5deg b=64deg+-5deg
Timing setting

(1)Pump vertical direction
(2)Coupling's key groove position at No 1 cylinder's beginning of injection
(3)B.T.D.C.: aa
(4)-
----------
aa=20deg
----------
a=(150deg)
----------
aa=20deg
----------
a=(150deg)
Information:
Introduction
The problem that is identified below does not have a known permanent solution. Until a permanent solution is known, use the solution that is identified below.Problem
DEF heated lines can get damaged during handling or other failure modes and leak diesel exhaust fluid on Clean Emission Module (CEM) and other components.Solution
Caterpillar is aware of this problem and is recommending the following interim corrective action.
Do not operate or work on this product unless you have read and understood the instruction and warnings in the relevant Operation and Maintenance Manuals and relevant service literature. Failure to follow the instructions or heed the warnings could result in injury or death. Proper care is your responsibility.
Rework Procedure
Note: This procedure is meant for temporary repair of a DEF line to allow the machine to be safely transported to the repair shop.
Table 1
Required Parts
Part Number Part Name
473-2053 Diesel Exhaust Fluid Lines Gp (5/16th 90 degree adapter)
473-2055 Diesel Exhaust Fluid Lines Gp (5/16th straight adapter)
473-2056 Diesel Exhaust Fluid Lines Gp (3/8th 90 degree adapter)
473-2057 Diesel Exhaust Fluid Lines Gp (38th 90 Straight adapter)
Table 2
Required Tools
Part Number Part Name
1U-7648 Tube Cutter
Illustration 1 g06433660
Cut the connector end on the corrugated section with the cutter.
Illustration 2 g06433665
Cut the two wires with a tie cutter.
Illustration 3 g06433668
Use a knife or sharp blade to cut the outer sheathing off. Ensure not to cut or damage the inner fluid hose.
Illustration 4 g06433669
Install the hose clamp provided first before installing the connector. Use appropriate size (3/8th or 5/16th) and type (90 degree or straight) fitting.
Illustration 5 g06433672
Fasten the clamp until the two jaws are either in contact or about 2 to 3 mm (0.08 to 0.1 inch) apart.
The problem that is identified below does not have a known permanent solution. Until a permanent solution is known, use the solution that is identified below.Problem
DEF heated lines can get damaged during handling or other failure modes and leak diesel exhaust fluid on Clean Emission Module (CEM) and other components.Solution
Caterpillar is aware of this problem and is recommending the following interim corrective action.
Do not operate or work on this product unless you have read and understood the instruction and warnings in the relevant Operation and Maintenance Manuals and relevant service literature. Failure to follow the instructions or heed the warnings could result in injury or death. Proper care is your responsibility.
Rework Procedure
Note: This procedure is meant for temporary repair of a DEF line to allow the machine to be safely transported to the repair shop.
Table 1
Required Parts
Part Number Part Name
473-2053 Diesel Exhaust Fluid Lines Gp (5/16th 90 degree adapter)
473-2055 Diesel Exhaust Fluid Lines Gp (5/16th straight adapter)
473-2056 Diesel Exhaust Fluid Lines Gp (3/8th 90 degree adapter)
473-2057 Diesel Exhaust Fluid Lines Gp (38th 90 Straight adapter)
Table 2
Required Tools
Part Number Part Name
1U-7648 Tube Cutter
Illustration 1 g06433660
Cut the connector end on the corrugated section with the cutter.
Illustration 2 g06433665
Cut the two wires with a tie cutter.
Illustration 3 g06433668
Use a knife or sharp blade to cut the outer sheathing off. Ensure not to cut or damage the inner fluid hose.
Illustration 4 g06433669
Install the hose clamp provided first before installing the connector. Use appropriate size (3/8th or 5/16th) and type (90 degree or straight) fitting.
Illustration 5 g06433672
Fasten the clamp until the two jaws are either in contact or about 2 to 3 mm (0.08 to 0.1 inch) apart.
Have questions with 106671-9630?
Group cross 106671-9630 ZEXEL
Dpico
106671-9630
INJECTION-PUMP ASSEMBLY