Information injection-pump assembly
ZEXEL
106671-9490
1066719490
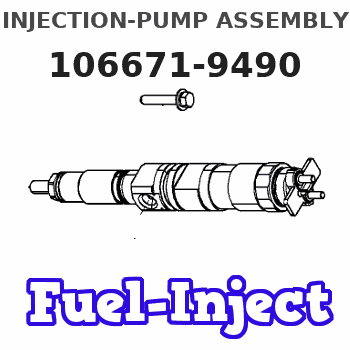
Rating:
Cross reference number
ZEXEL
106671-9490
1066719490
Zexel num
Bosch num
Firm num
Name
Calibration Data:
Adjustment conditions
Test oil
1404 Test oil ISO4113 or {SAEJ967d}
1404 Test oil ISO4113 or {SAEJ967d}
Test oil temperature
degC
40
40
45
Nozzle and nozzle holder
105780-8140
Bosch type code
EF8511/9A
Nozzle
105780-0000
Bosch type code
DN12SD12T
Nozzle holder
105780-2080
Bosch type code
EF8511/9
Opening pressure
MPa
17.2
Opening pressure
kgf/cm2
175
Injection pipe
Outer diameter - inner diameter - length (mm) mm 8-3-600
Outer diameter - inner diameter - length (mm) mm 8-3-600
Overflow valve
131424-4420
Overflow valve opening pressure
kPa
157
123
191
Overflow valve opening pressure
kgf/cm2
1.6
1.25
1.95
Tester oil delivery pressure
kPa
157
157
157
Tester oil delivery pressure
kgf/cm2
1.6
1.6
1.6
Direction of rotation (viewed from drive side)
Right R
Right R
Injection timing adjustment
Direction of rotation (viewed from drive side)
Right R
Right R
Injection order
1-5-3-6-
2-4
Pre-stroke
mm
4.7
4.65
4.75
Beginning of injection position
Governor side NO.1
Governor side NO.1
Difference between angles 1
Cal 1-5 deg. 60 59.5 60.5
Cal 1-5 deg. 60 59.5 60.5
Difference between angles 2
Cal 1-3 deg. 120 119.5 120.5
Cal 1-3 deg. 120 119.5 120.5
Difference between angles 3
Cal 1-6 deg. 180 179.5 180.5
Cal 1-6 deg. 180 179.5 180.5
Difference between angles 4
Cyl.1-2 deg. 240 239.5 240.5
Cyl.1-2 deg. 240 239.5 240.5
Difference between angles 5
Cal 1-4 deg. 300 299.5 300.5
Cal 1-4 deg. 300 299.5 300.5
Injection quantity adjustment
Adjusting point
-
Rack position
13.2
Pump speed
r/min
700
700
700
Average injection quantity
mm3/st.
121.5
118.5
124.5
Max. variation between cylinders
%
0
-2
2
Basic
*
Fixing the rack
*
Standard for adjustment of the maximum variation between cylinders
*
Injection quantity adjustment_02
Adjusting point
H
Rack position
8.5+-0.5
Pump speed
r/min
300
300
300
Average injection quantity
mm3/st.
11
9.5
12.5
Max. variation between cylinders
%
0
-15
15
Fixing the rack
*
Standard for adjustment of the maximum variation between cylinders
*
Injection quantity adjustment_03
Adjusting point
A
Rack position
R1(13.2)
Pump speed
r/min
700
700
700
Average injection quantity
mm3/st.
121.5
119.5
123.5
Basic
*
Fixing the lever
*
Injection quantity adjustment_04
Adjusting point
B
Rack position
R1+0.3
Pump speed
r/min
1100
1100
1100
Average injection quantity
mm3/st.
121.5
115.5
127.5
Fixing the lever
*
Injection quantity adjustment_05
Adjusting point
C
Rack position
R1-0.3
Pump speed
r/min
500
500
500
Average injection quantity
mm3/st.
113
107
119
Fixing the lever
*
Injection quantity adjustment_06
Adjusting point
I
Rack position
-
Pump speed
r/min
100
100
100
Average injection quantity
mm3/st.
95
85
105
Fixing the lever
*
Rack limit
*
Timer adjustment
Pump speed
r/min
(N1+50)-
-
Advance angle
deg.
0
0
0
Remarks
Start
Start
Timer adjustment_02
Pump speed
r/min
N1
Advance angle
deg.
0.5
Remarks
Measure the actual speed.
Measure the actual speed.
Timer adjustment_03
Pump speed
r/min
-
Advance angle
deg.
5.5
5
6
Remarks
Measure the actual speed, stop
Measure the actual speed, stop
Test data Ex:
Governor adjustment
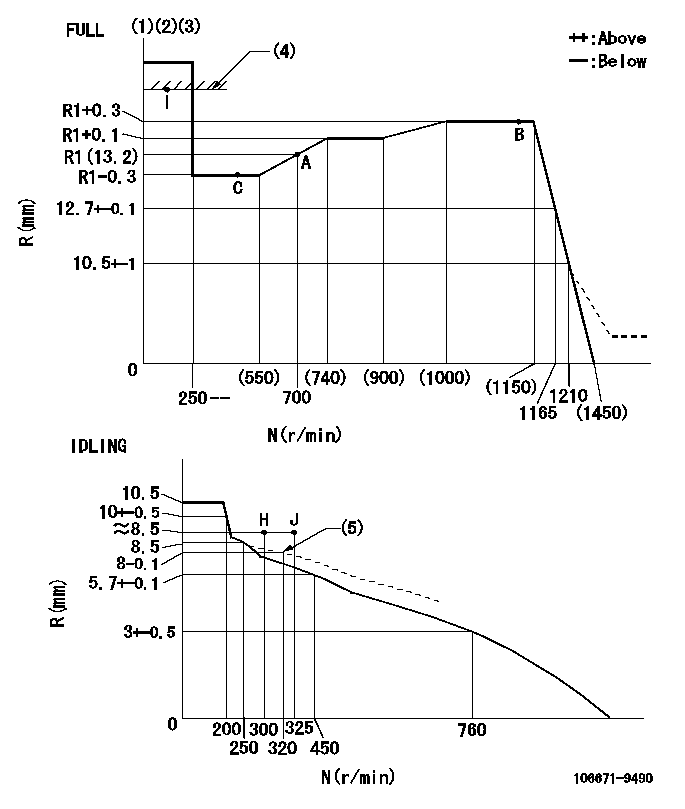
N:Pump speed
R:Rack position (mm)
(1)Torque cam stamping: T1
(2)Tolerance for racks not indicated: +-0.05mm.
(3)Microswitch adjustment unnecessary.
(4)RACK LIMIT
(5)Damper spring setting
----------
T1=AE15
----------
----------
T1=AE15
----------
Speed control lever angle
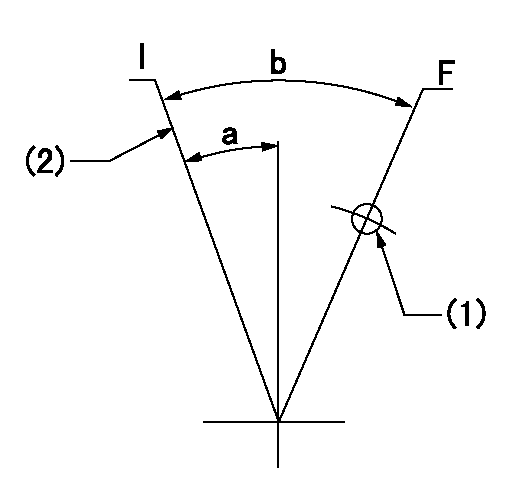
F:Full speed
I:Idle
(1)Use the hole at R = aa
(2)Stopper bolt set position 'H'
----------
aa=70mm
----------
a=14deg+-5deg b=35deg+-3deg
----------
aa=70mm
----------
a=14deg+-5deg b=35deg+-3deg
Stop lever angle

N:Pump normal
S:Stop the pump.
(1)Use the hole at R = aa
(2)Rack position bb
(3)Set the stopper screw. (After setting, apply red paint.)
----------
aa=40mm bb=1.5+-0.3mm
----------
a=20deg+-5deg b=44deg+-5deg
----------
aa=40mm bb=1.5+-0.3mm
----------
a=20deg+-5deg b=44deg+-5deg
Timing setting
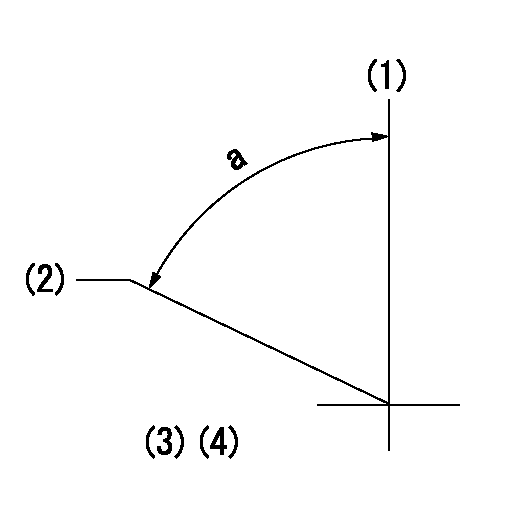
(1)Pump vertical direction
(2)Coupling's key groove position at No 1 cylinder's beginning of injection
(3)B.T.D.C.: aa
(4)-
----------
aa=10deg
----------
a=(70deg)
----------
aa=10deg
----------
a=(70deg)
Information:
Illustration 9 g06286243
Typical example
Illustration 9 shows the governor plate displaying high wear at the sleeve contact points.
Illustration 10 g06286261
Typical example
Illustration 8 shows the thrust sleeve displaying an excessive wear groove.
Illustration 11 g06286627
Typical example
Illustration 12 g06286629
Typical example
Illustration 11 and Illustration 11 show the weight thrust fingers badly worn.
Illustration 13 g06286630
Typical example
Illustration 13 shows pivot heels showing excessive wear.Fuel Quality
Illustration 14 g06286604
Typical example
Illustration 14 shows that nitrile rubber seals have cracked causing fuel leakage. The cracks in the seals are attributed to fuel attacking the rubber. Ensure that there is no particle contamination in the fuel injection pump.Unmodified Vegetable Oil or Poor Quality FAME
Illustration 15 g06286612
Typical example
Stuck metering valve causing engine overspeed. Top cover of fuel injection pump removed. Black sticky material adhering to all non-alloy surfaces, this is due to the use of unmodified vegetable oil or poor quality FAME. Refer to Illustration 15.High Water Content in Fuel
Illustration 16 g06286613
Typical example
Illustration 17 g06286615
Typical example
Illustration 16 and Illustration 17 show corrosion on component surfaces, due to high water content in fuel.Characteristics Associated with Poor Quality Fuel and Potential Issue
Table 1
Fuel Characteristics Effect Issue
FAMEs in general Causes some elastomers to soften, swell, harden, and crack. Fuel leakage.
Free methanol in FAME Corrodes aluminum and zinc. Low flash point. Corrosion on fuel injection equipment.
FAME process chemicals Potassium and sodium compound. Solid particles. Blocked nozzles.
Dissolved water in FAME Reversion of FAME to a fatty acid. Fuel filter plugging.
Free water in FAME Corrosion. Sustains bacteria. Corrosion on fuel injection equipment. Sludging.
Free glycerine, mono, and
di-glycerines in FAME Corrodes non-ferrous metals.
Sediments on moving parts and lacquering. Fuel filter clogging.
Fuel injector clogging.
Free fatty acid Corrosion of Zinc plating.
Slats of organic acids.
Organic compound formed. Corrosion on fuel injection equipment.
Fuel filter plugging.
Sediment on components
High viscosity at low temperature Generates excessive localized heat.
Higher stressed components. Fuel injection pump seizures.
Early life issues.
Poor nozzle spray.
Corrosive acids Corrodes all metallic parts. Corrosion on fuel injection equipment.
High molecular organic acids Corrosion of Zinc plating.
Slats of organic acids.
Organic compound formed. Corrosion on fuel injection equipment.
Fuel filter plugging.
Sediment on components
Polymerization products Deposits in fuel mixes Fuel filter plugging. Lacquering formation in hot areas. Recommended Procedures
Prime the fuel system to remove any air. Refer to Operation and Maintenance Manual, Fuel System - Prime for the correct procedure.Check the pressure of the fuel system. Refer to Systems Operation, Testing and Adjusting, Fuel System Pressure - Test for the correct procedure.Check the operation of the fuel injection nozzles. Refer to Systems Operation, Testing and Adjusting, Fuel Injection Nozzle - Test for the correct procedure.To inspect the fuel injection pump, refer to Special Instruction, REHS3767, Inspection of Fuel Injection Pumps on 3054C, C3.3, C4.4 (Mechanical), and C7.1 (Mechanical) Engines for the correct procedure.