Information injection-pump assembly
ZEXEL
106671-9150
1066719150
MITSUBISHI-HEAV
3626552120
3626552120
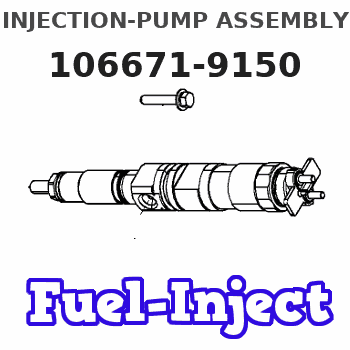
Rating:
Service parts 106671-9150 INJECTION-PUMP ASSEMBLY:
1.
_
7.
COUPLING PLATE
8.
_
9.
_
11.
Nozzle and Holder
36261-33010
12.
Open Pre:MPa(Kqf/cm2)
21.6{220}
15.
NOZZLE SET
Include in #1:
106671-9150
as INJECTION-PUMP ASSEMBLY
Cross reference number
ZEXEL
106671-9150
1066719150
MITSUBISHI-HEAV
3626552120
3626552120
Zexel num
Bosch num
Firm num
Name
Calibration Data:
Adjustment conditions
Test oil
1404 Test oil ISO4113 or {SAEJ967d}
1404 Test oil ISO4113 or {SAEJ967d}
Test oil temperature
degC
40
40
45
Nozzle and nozzle holder
105780-8140
Bosch type code
EF8511/9A
Nozzle
105780-0000
Bosch type code
DN12SD12T
Nozzle holder
105780-2080
Bosch type code
EF8511/9
Opening pressure
MPa
17.2
Opening pressure
kgf/cm2
175
Injection pipe
Outer diameter - inner diameter - length (mm) mm 8-3-600
Outer diameter - inner diameter - length (mm) mm 8-3-600
Overflow valve
131424-7420
Overflow valve opening pressure
kPa
255
221
289
Overflow valve opening pressure
kgf/cm2
2.6
2.25
2.95
Tester oil delivery pressure
kPa
157
157
157
Tester oil delivery pressure
kgf/cm2
1.6
1.6
1.6
Direction of rotation (viewed from drive side)
Right R
Right R
Injection timing adjustment
Direction of rotation (viewed from drive side)
Right R
Right R
Injection order
1-5-3-6-
2-4
Pre-stroke
mm
3.9
3.85
3.95
Beginning of injection position
Governor side NO.1
Governor side NO.1
Difference between angles 1
Cal 1-5 deg. 60 59.5 60.5
Cal 1-5 deg. 60 59.5 60.5
Difference between angles 2
Cal 1-3 deg. 120 119.5 120.5
Cal 1-3 deg. 120 119.5 120.5
Difference between angles 3
Cal 1-6 deg. 180 179.5 180.5
Cal 1-6 deg. 180 179.5 180.5
Difference between angles 4
Cyl.1-2 deg. 240 239.5 240.5
Cyl.1-2 deg. 240 239.5 240.5
Difference between angles 5
Cal 1-4 deg. 300 299.5 300.5
Cal 1-4 deg. 300 299.5 300.5
Injection quantity adjustment
Adjusting point
A
Rack position
16
Pump speed
r/min
900
900
900
Average injection quantity
mm3/st.
204
197
211
Max. variation between cylinders
%
0
-3
3
Basic
*
Fixing the lever
*
Boost pressure
kPa
120
120
Boost pressure
mmHg
900
900
Injection quantity adjustment_02
Adjusting point
D
Rack position
5.8+-0.5
Pump speed
r/min
450
450
450
Average injection quantity
mm3/st.
24.5
21.5
27.5
Max. variation between cylinders
%
0
-10
10
Fixing the rack
*
Boost pressure
kPa
0
0
0
Boost pressure
mmHg
0
0
0
Injection quantity adjustment_03
Adjusting point
E
Rack position
-
Pump speed
r/min
100
100
100
Average injection quantity
mm3/st.
315
315
335
Fixing the lever
*
Boost pressure
kPa
0
0
0
Boost pressure
mmHg
0
0
0
Rack limit
*
Boost compensator adjustment
Pump speed
r/min
500
500
500
Rack position
R1-1
Boost pressure
kPa
66.6
66.6
66.6
Boost pressure
mmHg
500
500
500
Boost compensator adjustment_02
Pump speed
r/min
500
500
500
Rack position
R1(16.8)
Boost pressure
kPa
107
100.3
113.7
Boost pressure
mmHg
800
750
850
Timer adjustment
Pump speed
r/min
470--
Advance angle
deg.
0
0
0
Remarks
Start
Start
Timer adjustment_02
Pump speed
r/min
420
Advance angle
deg.
0.5
Timer adjustment_03
Pump speed
r/min
740
Advance angle
deg.
4
3.5
4.5
Remarks
Finish
Finish
Test data Ex:
Governor adjustment
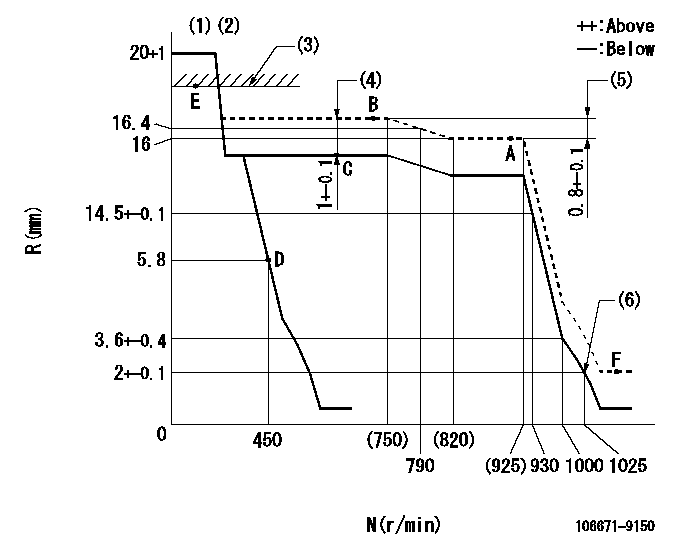
N:Pump speed
R:Rack position (mm)
(1)Target notch: K
(2)Tolerance for racks not indicated: +-0.05mm.
(3)RACK LIMIT
(4)Boost compensator stroke
(5)Rack difference between N = N1 and N = N2
(6)Set idle sub-spring
----------
K=6 N1=900r/min N2=700r/min
----------
----------
K=6 N1=900r/min N2=700r/min
----------
Speed control lever angle
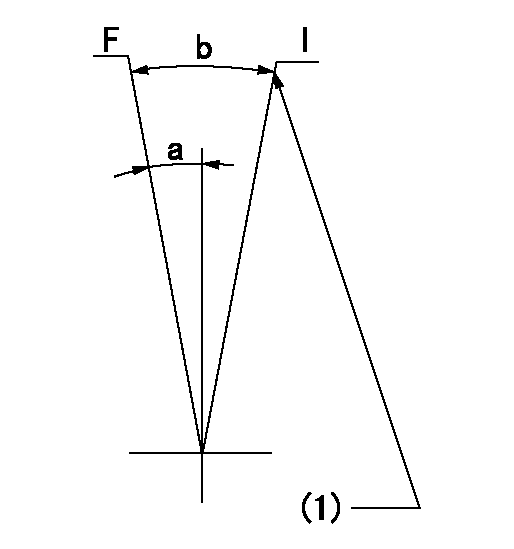
F:Full speed
I:Idle
(1)Stopper bolt setting
----------
----------
a=3deg+-5deg b=20deg+-5deg
----------
----------
a=3deg+-5deg b=20deg+-5deg
Stop lever angle

N:Pump normal
S:Stop the pump.
(1)Pump speed aa and rack position bb (to be sealed at delivery)
----------
aa=0r/min bb=1-0.2mm
----------
a=35deg+-5deg b=70deg+-5deg
----------
aa=0r/min bb=1-0.2mm
----------
a=35deg+-5deg b=70deg+-5deg
Timing setting

(1)Pump vertical direction
(2)Coupling's key groove position at No 1 cylinder's beginning of injection
(3)-
(4)-
----------
----------
a=(90deg)
----------
----------
a=(90deg)
Information:
Location of Components
Illustration 1 g06494607
Typical example
(A) DEF tank breather
(B) Heater relay
(C) DEF fast fill tank-mounted valve
(D) Plug heater
(E) Heated supply line
(F) DEF fast fill receiver
(G) DEF tank
Illustration 2 g06494608
(C) DEF fast fill tank-mounted valveThe ground level DEF fill system works much like the ground level fast fuel system. DEF fast fill tank-mounted valve (C) is mounted in DEF tank (G). Fast fill tank-mounted valve (C) has a piston that is normally closed with a spring.
Illustration 3 g06516649
(H) O-Ring seal
(J) Flow In
(K) Flow Out
(L) Back cavityNote: O-Ring seal (H) allows small amount of fluid flow.Note: The main flow through the valve is not shown.Note: During normal flow conditions there is no pressure built up in back cavity (L). Back cavity (L) is essentially "open to atmosphere".When filling, the DEF flow opens the piston, past the diverter shield and a portion flows through an orifice in the piston into the float area.
Illustration 4 g06516652
(L) Back cavity
(M) Rolling diaphragm
(N) O-Ring seal
(P) Drain holeNote: O-Ring seal (N) prevents any flow from back cavity (L).Note: Once the float rises, the pressure in back cavity (L) equals the pressure pushing the front of rolling diaphragm (M). Since the area behind rolling diaphragm (M) is greater than the area in front, along with the spring force, diaphragm (M) is held shut.When the tank level causes the float to rise high enough, the orifice is blocked, causing increased pressure on the piston until valve (C) closes. The increased pressure in the fill line then causes the nozzle attached to the receiver to shut off.The nozzle shuts off when the nozzle sees 172 to 200 kPa (25 to 29 psi) resistance. If pressure is not great enough from the source pump/supply at nozzle, there is not enough pressure built up in line between valve and nozzle to trigger nozzle shut off and DEF exits the breather-overfill.Targeted flow for the DEF supply pump should be 45 L/min (12 US gpm). Excessive flow can lead to premature shut-off of DEF nozzle.DEF tank valve (C), supply line (E), and DEF fast fill receiver (F) are electrically heated based on ambient temperature, battery, and alternator loads controlled through heater relay (B). For heated DEF hose repair kit, refer to Service Magazine, M0103829, "Repair Kits for Quick Connect Diesel Exhaust Fluid (DEF) Line Fittings Are Now Available for Certain Cat® Machine Engines".Note: If receiver (F) and supply line (E) on machine are drained for storage, the system must be refilled via the ground fill connection. The system is refilled to ensure that plug heater (D) in receiver (F) remains submerged in DEF fluid during the heating operation.
Plug heater (D) probe must be submerged at least 80% in DEF fluid to prevent overheating that could lead to plug heater (D) failing.
Illustration 1 g06494607
Typical example
(A) DEF tank breather
(B) Heater relay
(C) DEF fast fill tank-mounted valve
(D) Plug heater
(E) Heated supply line
(F) DEF fast fill receiver
(G) DEF tank
Illustration 2 g06494608
(C) DEF fast fill tank-mounted valveThe ground level DEF fill system works much like the ground level fast fuel system. DEF fast fill tank-mounted valve (C) is mounted in DEF tank (G). Fast fill tank-mounted valve (C) has a piston that is normally closed with a spring.
Illustration 3 g06516649
(H) O-Ring seal
(J) Flow In
(K) Flow Out
(L) Back cavityNote: O-Ring seal (H) allows small amount of fluid flow.Note: The main flow through the valve is not shown.Note: During normal flow conditions there is no pressure built up in back cavity (L). Back cavity (L) is essentially "open to atmosphere".When filling, the DEF flow opens the piston, past the diverter shield and a portion flows through an orifice in the piston into the float area.
Illustration 4 g06516652
(L) Back cavity
(M) Rolling diaphragm
(N) O-Ring seal
(P) Drain holeNote: O-Ring seal (N) prevents any flow from back cavity (L).Note: Once the float rises, the pressure in back cavity (L) equals the pressure pushing the front of rolling diaphragm (M). Since the area behind rolling diaphragm (M) is greater than the area in front, along with the spring force, diaphragm (M) is held shut.When the tank level causes the float to rise high enough, the orifice is blocked, causing increased pressure on the piston until valve (C) closes. The increased pressure in the fill line then causes the nozzle attached to the receiver to shut off.The nozzle shuts off when the nozzle sees 172 to 200 kPa (25 to 29 psi) resistance. If pressure is not great enough from the source pump/supply at nozzle, there is not enough pressure built up in line between valve and nozzle to trigger nozzle shut off and DEF exits the breather-overfill.Targeted flow for the DEF supply pump should be 45 L/min (12 US gpm). Excessive flow can lead to premature shut-off of DEF nozzle.DEF tank valve (C), supply line (E), and DEF fast fill receiver (F) are electrically heated based on ambient temperature, battery, and alternator loads controlled through heater relay (B). For heated DEF hose repair kit, refer to Service Magazine, M0103829, "Repair Kits for Quick Connect Diesel Exhaust Fluid (DEF) Line Fittings Are Now Available for Certain Cat® Machine Engines".Note: If receiver (F) and supply line (E) on machine are drained for storage, the system must be refilled via the ground fill connection. The system is refilled to ensure that plug heater (D) in receiver (F) remains submerged in DEF fluid during the heating operation.
Plug heater (D) probe must be submerged at least 80% in DEF fluid to prevent overheating that could lead to plug heater (D) failing.