Information injection-pump assembly
BOSCH
F 019 Z20 073
f019z20073
ZEXEL
106671-9112
1066719112
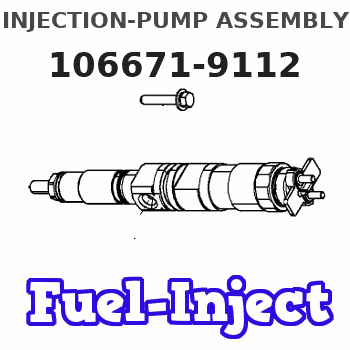
Rating:
Service parts 106671-9112 INJECTION-PUMP ASSEMBLY:
1.
_
7.
COUPLING PLATE
8.
_
9.
_
11.
Nozzle and Holder
12.
Open Pre:MPa(Kqf/cm2)
17.7{180}/21.6{220}
15.
NOZZLE SET
Include in #1:
106671-9112
as INJECTION-PUMP ASSEMBLY
Cross reference number
BOSCH
F 019 Z20 073
f019z20073
ZEXEL
106671-9112
1066719112
Zexel num
Bosch num
Firm num
Name
106671-9112
F 019 Z20 073
DPICO
INJECTION-PUMP ASSEMBLY
Q Q
Q Q
Calibration Data:
Adjustment conditions
Test oil
1404 Test oil ISO4113 or {SAEJ967d}
1404 Test oil ISO4113 or {SAEJ967d}
Test oil temperature
degC
40
40
45
Nozzle and nozzle holder
105780-8140
Bosch type code
EF8511/9A
Nozzle
105780-0000
Bosch type code
DN12SD12T
Nozzle holder
105780-2080
Bosch type code
EF8511/9
Opening pressure
MPa
17.2
Opening pressure
kgf/cm2
175
Injection pipe
Outer diameter - inner diameter - length (mm) mm 8-3-600
Outer diameter - inner diameter - length (mm) mm 8-3-600
Overflow valve
131424-4420
Overflow valve opening pressure
kPa
157
123
191
Overflow valve opening pressure
kgf/cm2
1.6
1.25
1.95
Tester oil delivery pressure
kPa
157
157
157
Tester oil delivery pressure
kgf/cm2
1.6
1.6
1.6
Direction of rotation (viewed from drive side)
Right R
Right R
Injection timing adjustment
Direction of rotation (viewed from drive side)
Right R
Right R
Injection order
1-5-3-6-
2-4
Pre-stroke
mm
4.4
4.35
4.45
Beginning of injection position
Governor side NO.1
Governor side NO.1
Difference between angles 1
Cal 1-5 deg. 60 59.5 60.5
Cal 1-5 deg. 60 59.5 60.5
Difference between angles 2
Cal 1-3 deg. 120 119.5 120.5
Cal 1-3 deg. 120 119.5 120.5
Difference between angles 3
Cal 1-6 deg. 180 179.5 180.5
Cal 1-6 deg. 180 179.5 180.5
Difference between angles 4
Cyl.1-2 deg. 240 239.5 240.5
Cyl.1-2 deg. 240 239.5 240.5
Difference between angles 5
Cal 1-4 deg. 300 299.5 300.5
Cal 1-4 deg. 300 299.5 300.5
Injection quantity adjustment
Adjusting point
-
Rack position
13.1
Pump speed
r/min
700
700
700
Each cylinder's injection qty
mm3/st.
175
170.6
179.4
Basic
*
Fixing the rack
*
Boost pressure
kPa
0
0
0
Boost pressure
mmHg
0
0
0
Standard for adjustment of the maximum variation between cylinders
*
Injection quantity adjustment_02
Adjusting point
C
Rack position
7.1+-0.5
Pump speed
r/min
225
225
225
Each cylinder's injection qty
mm3/st.
30
25.6
34.4
Fixing the rack
*
Boost pressure
kPa
0
0
0
Boost pressure
mmHg
0
0
0
Standard for adjustment of the maximum variation between cylinders
*
Injection quantity adjustment_03
Adjusting point
A
Rack position
R1(13.1)
Pump speed
r/min
700
700
700
Average injection quantity
mm3/st.
175
173
177
Basic
*
Fixing the lever
*
Boost pressure
kPa
104
104
Boost pressure
mmHg
780
780
Injection quantity adjustment_04
Adjusting point
E
Rack position
-
Pump speed
r/min
100
100
100
Average injection quantity
mm3/st.
120
80
160
Fixing the lever
*
Boost pressure
kPa
0
0
0
Boost pressure
mmHg
0
0
0
Boost compensator adjustment
Pump speed
r/min
600
600
600
Rack position
R2(R1-3.
1)
Boost pressure
kPa
3.3
3.3
6.6
Boost pressure
mmHg
25
25
50
Boost compensator adjustment_02
Pump speed
r/min
600
600
600
Rack position
R1(13.1)
Boost pressure
kPa
90.6
90.6
90.6
Boost pressure
mmHg
680
680
680
Timer adjustment
Pump speed
r/min
750--
Advance angle
deg.
0
0
0
Load
4/4
Remarks
Beginning of advance.
Beginning of advance.
Timer adjustment_02
Pump speed
r/min
250--
Advance angle
deg.
1.5
1
2
Load
0/4
Remarks
Start
Start
Timer adjustment_03
Pump speed
r/min
500--
Advance angle
deg.
0
0
0
Load
4/4
Timer adjustment_04
Pump speed
r/min
700
Advance angle
deg.
0.5
Load
4/4
Timer adjustment_05
Pump speed
r/min
1100
Advance angle
deg.
2.5
2
3
Load
4/4
Remarks
Finish
Finish
Test data Ex:
Governor adjustment
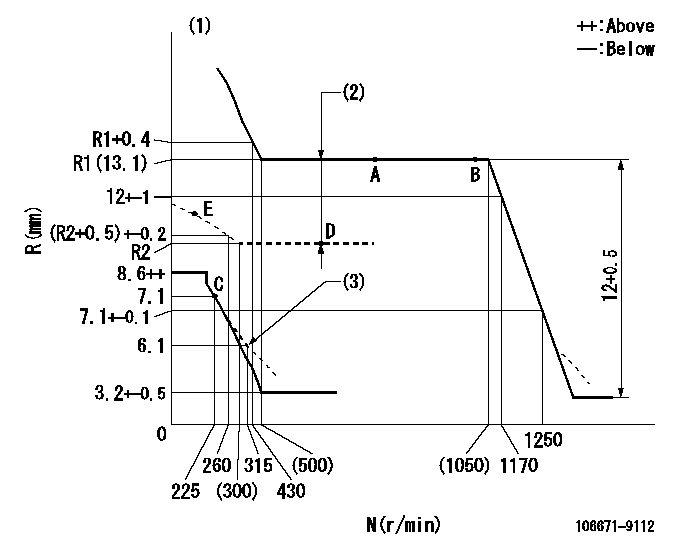
N:Pump speed
R:Rack position (mm)
(1)Tolerance for racks not indicated: +-0.05mm.
(2)Boost compensator stroke: BCL
(3)Damper spring setting
----------
BCL=3.1+-0.1mm
----------
----------
BCL=3.1+-0.1mm
----------
Speed control lever angle

F:Full speed
----------
----------
a=(18deg)+-5deg
----------
----------
a=(18deg)+-5deg
0000000901

F:Full load
I:Idle
(1)Stopper bolt setting
----------
----------
a=18deg+-5deg b=37deg+-3deg
----------
----------
a=18deg+-5deg b=37deg+-3deg
Stop lever angle
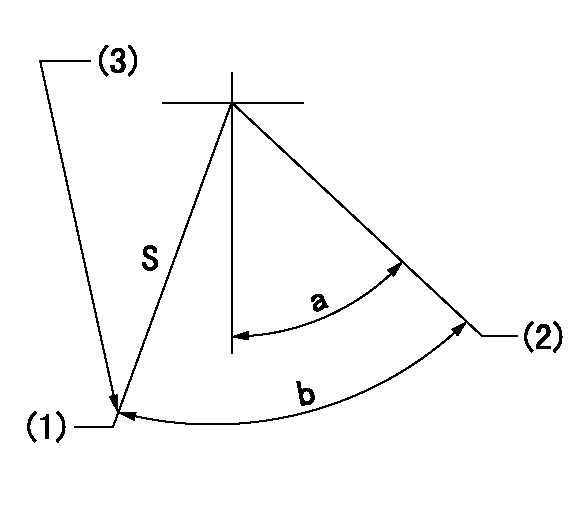
S:Stop the pump.
(1)Rack position = aa
(2)Lever free and normal position
(3)Stopper bolt setting
----------
aa=3.5-0.5mm
----------
a=38deg+-5deg b=38deg+7deg-5deg
----------
aa=3.5-0.5mm
----------
a=38deg+-5deg b=38deg+7deg-5deg
0000001501 MICRO SWITCH
Adjustment of the micro-switch
Adjust the bolt to obtain the following lever position when the micro-switch is ON.
(1)Speed N1
(2)Rack position Ra
----------
N1=325r/min Ra=6.8+-0.1mm
----------
----------
N1=325r/min Ra=6.8+-0.1mm
----------
Timing setting

(1)Pump vertical direction
(2)Coupling's key groove position at No 1 cylinder's beginning of injection
(3)B.T.D.C.: aa
(4)-
----------
aa=14deg
----------
a=(6deg)
----------
aa=14deg
----------
a=(6deg)
Information:
3-Cylinder Diesel Theory and Operation
The KDW 1003 diesel engine has an indirect injection (IDI) fuel delivery system. The fuel injectors are a unit style injector located in the cylinder head and actuated by the camshaft.As the camshaft turns, the adjustable pushrod forces the high-pressure plunger into the injector. The unit injector is then pressurized to 14,000 to 15000 kPa (2030 to 2175 psi) before injection. This process is known as popping pressure. The injection even will take place between 11° and 13° (BTDC) before the piston reaches top dead center.Refer to the engine emissions tag on the engine or the service manual for proper injection timing specifications. Refer to the service manual for the injection timing tool and procedures.The unit injectors are supplied low-pressure fuel from the electric fuel pump in the fuel tank to the injection lines coming through a grommet in the cylinder head. This pressure is between 60 to 70 kPa (8.7 to 10 psi). Fuel supply is hose A and fuel return is hose BCommon Specifications
Compression ratio: 22.8 to 1
Compression: new engine cold 2760 to 3100 kPa (400 to 450 psi) or old engine at 2415 to 2760 kPa (350 to 400 psi)
Compression minimum: 1725 kPa (250 psi) (below this pressure, cylinder misfire will occur)
Compression readingtaken through the glow plug hole, 563-4356 Test Kit
Firing order: 1 - 3 - 2
Supply fuel pressure: 60 to 70 kPa (8.7 to 10 psi)
Popping pressure: 14,000 to 15000 kPa (2030 to 2175 psi)
Thermostat open temperature: 78 to 82 °C (172.4 to 179.6 °F)
Thermostat fully open: 95 °C (203 °F)
Coolant fan on at 100.5 °C (213 °F) and off at 95 °C (203 °F)
Engine oil capacity: approximately 2.8 L (3 qt)
Engine oil (recommended): 5W-50 Synthetic
Engine oil pressure switch minimum opening pressure 30 kPa (4.35 psi) (on valve cover) normally close switch
Engine oil pressure at 120 °C (248 °F): 108 kPa (15.6 psi) at idle speed (800 to 900 rpm)Glow Plug and Thermistor
The KDW 1003 engine uses glow plug temperature sensor, or a thermistor, to adjust glow plug on time. The glow plugs are in the cylinder head precombustion chamber and heat up to 816 °C (1500 °F) to assist with starting the engine. The sensor is in the thermostat housing. As the coolant temperature rises, the sensor resistance goes down.The glow plug controller/relay is a plug-in device above the battery. The glow plug controller/relay applies 12 volts DC to the glow plugs in the precombustion chambers to aid in cold starting. Heating time is determined by the ECT thermistor signal and will vary from 0 seconds (warm engine) to approximately 30 seconds (cold engine).
Illustration 1 g06469140
(1) Black wire
(2) Brown wire
(3) Red/Orange wire
(4) Violet/White wire
(5) Orange wire
(6) Pink wire
(7) White/Blue wireUse the following procedure to test the glow plug relay. You will need a multimeter for the procedure.Note: The test should take 15 to 35 minutes.
Using an appropriate multimeter, select DC volts and connect the black test lead to the black wire (1) and the red test lead to the red/orange
The KDW 1003 diesel engine has an indirect injection (IDI) fuel delivery system. The fuel injectors are a unit style injector located in the cylinder head and actuated by the camshaft.As the camshaft turns, the adjustable pushrod forces the high-pressure plunger into the injector. The unit injector is then pressurized to 14,000 to 15000 kPa (2030 to 2175 psi) before injection. This process is known as popping pressure. The injection even will take place between 11° and 13° (BTDC) before the piston reaches top dead center.Refer to the engine emissions tag on the engine or the service manual for proper injection timing specifications. Refer to the service manual for the injection timing tool and procedures.The unit injectors are supplied low-pressure fuel from the electric fuel pump in the fuel tank to the injection lines coming through a grommet in the cylinder head. This pressure is between 60 to 70 kPa (8.7 to 10 psi). Fuel supply is hose A and fuel return is hose BCommon Specifications
Compression ratio: 22.8 to 1
Compression: new engine cold 2760 to 3100 kPa (400 to 450 psi) or old engine at 2415 to 2760 kPa (350 to 400 psi)
Compression minimum: 1725 kPa (250 psi) (below this pressure, cylinder misfire will occur)
Compression readingtaken through the glow plug hole, 563-4356 Test Kit
Firing order: 1 - 3 - 2
Supply fuel pressure: 60 to 70 kPa (8.7 to 10 psi)
Popping pressure: 14,000 to 15000 kPa (2030 to 2175 psi)
Thermostat open temperature: 78 to 82 °C (172.4 to 179.6 °F)
Thermostat fully open: 95 °C (203 °F)
Coolant fan on at 100.5 °C (213 °F) and off at 95 °C (203 °F)
Engine oil capacity: approximately 2.8 L (3 qt)
Engine oil (recommended): 5W-50 Synthetic
Engine oil pressure switch minimum opening pressure 30 kPa (4.35 psi) (on valve cover) normally close switch
Engine oil pressure at 120 °C (248 °F): 108 kPa (15.6 psi) at idle speed (800 to 900 rpm)Glow Plug and Thermistor
The KDW 1003 engine uses glow plug temperature sensor, or a thermistor, to adjust glow plug on time. The glow plugs are in the cylinder head precombustion chamber and heat up to 816 °C (1500 °F) to assist with starting the engine. The sensor is in the thermostat housing. As the coolant temperature rises, the sensor resistance goes down.The glow plug controller/relay is a plug-in device above the battery. The glow plug controller/relay applies 12 volts DC to the glow plugs in the precombustion chambers to aid in cold starting. Heating time is determined by the ECT thermistor signal and will vary from 0 seconds (warm engine) to approximately 30 seconds (cold engine).
Illustration 1 g06469140
(1) Black wire
(2) Brown wire
(3) Red/Orange wire
(4) Violet/White wire
(5) Orange wire
(6) Pink wire
(7) White/Blue wireUse the following procedure to test the glow plug relay. You will need a multimeter for the procedure.Note: The test should take 15 to 35 minutes.
Using an appropriate multimeter, select DC volts and connect the black test lead to the black wire (1) and the red test lead to the red/orange
Have questions with 106671-9112?
Group cross 106671-9112 ZEXEL
Daewoo
Dpico
Hyundai
Dpico
106671-9112
F 019 Z20 073
INJECTION-PUMP ASSEMBLY
Q
Q