Information injection-pump assembly
ZEXEL
106671-9111
1066719111
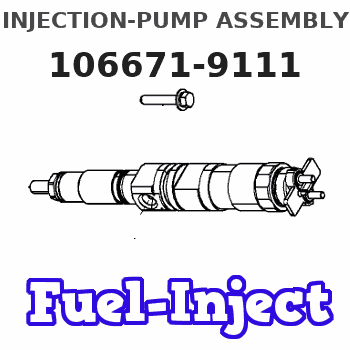
Rating:
Service parts 106671-9111 INJECTION-PUMP ASSEMBLY:
1.
_
7.
COUPLING PLATE
8.
_
9.
_
11.
Nozzle and Holder
12.
Open Pre:MPa(Kqf/cm2)
17.7{180}/21.6{220}
15.
NOZZLE SET
Include in #1:
106671-9111
as INJECTION-PUMP ASSEMBLY
Cross reference number
ZEXEL
106671-9111
1066719111
Zexel num
Bosch num
Firm num
Name
Calibration Data:
Adjustment conditions
Test oil
1404 Test oil ISO4113 or {SAEJ967d}
1404 Test oil ISO4113 or {SAEJ967d}
Test oil temperature
degC
40
40
45
Nozzle and nozzle holder
105780-8140
Bosch type code
EF8511/9A
Nozzle
105780-0000
Bosch type code
DN12SD12T
Nozzle holder
105780-2080
Bosch type code
EF8511/9
Opening pressure
MPa
17.2
Opening pressure
kgf/cm2
175
Injection pipe
Outer diameter - inner diameter - length (mm) mm 8-3-600
Outer diameter - inner diameter - length (mm) mm 8-3-600
Overflow valve
131424-4420
Overflow valve opening pressure
kPa
157
123
191
Overflow valve opening pressure
kgf/cm2
1.6
1.25
1.95
Tester oil delivery pressure
kPa
157
157
157
Tester oil delivery pressure
kgf/cm2
1.6
1.6
1.6
Direction of rotation (viewed from drive side)
Right R
Right R
Injection timing adjustment
Direction of rotation (viewed from drive side)
Right R
Right R
Injection order
1-5-3-6-
2-4
Pre-stroke
mm
4.4
4.35
4.45
Beginning of injection position
Governor side NO.1
Governor side NO.1
Difference between angles 1
Cal 1-5 deg. 60 59.5 60.5
Cal 1-5 deg. 60 59.5 60.5
Difference between angles 2
Cal 1-3 deg. 120 119.5 120.5
Cal 1-3 deg. 120 119.5 120.5
Difference between angles 3
Cal 1-6 deg. 180 179.5 180.5
Cal 1-6 deg. 180 179.5 180.5
Difference between angles 4
Cyl.1-2 deg. 240 239.5 240.5
Cyl.1-2 deg. 240 239.5 240.5
Difference between angles 5
Cal 1-4 deg. 300 299.5 300.5
Cal 1-4 deg. 300 299.5 300.5
Injection quantity adjustment
Adjusting point
-
Rack position
13.1
Pump speed
r/min
700
700
700
Each cylinder's injection qty
mm3/st.
175
170.6
179.4
Basic
*
Fixing the rack
*
Standard for adjustment of the maximum variation between cylinders
*
Injection quantity adjustment_02
Adjusting point
C
Rack position
7.1+-0.5
Pump speed
r/min
225
225
225
Each cylinder's injection qty
mm3/st.
30
25.6
34.4
Fixing the rack
*
Standard for adjustment of the maximum variation between cylinders
*
Injection quantity adjustment_03
Adjusting point
A
Rack position
R1(13.1)
Pump speed
r/min
700
700
700
Average injection quantity
mm3/st.
175
173
177
Basic
*
Fixing the lever
*
Boost pressure
kPa
104
104
Boost pressure
mmHg
780
780
Injection quantity adjustment_04
Adjusting point
E
Rack position
-
Pump speed
r/min
100
100
100
Average injection quantity
mm3/st.
120
80
160
Fixing the lever
*
Boost pressure
kPa
0
0
0
Boost pressure
mmHg
0
0
0
Boost compensator adjustment
Pump speed
r/min
600
600
600
Rack position
R2(R1-3.
1)
Boost pressure
kPa
3.3
3.3
6.6
Boost pressure
mmHg
25
25
50
Boost compensator adjustment_02
Pump speed
r/min
600
600
600
Rack position
R1(13.1)
Boost pressure
kPa
90.6
90.6
90.6
Boost pressure
mmHg
680
680
680
Timer adjustment
Pump speed
r/min
750--
Advance angle
deg.
0
0
0
Load
4/4
Remarks
Beginning of advance.
Beginning of advance.
Timer adjustment_02
Pump speed
r/min
250++
Advance angle
deg.
1.5
1
2
Load
0/4
Remarks
Start
Start
Timer adjustment_03
Pump speed
r/min
500--
Advance angle
deg.
0
0
0
Load
4/4
Timer adjustment_04
Pump speed
r/min
700
Advance angle
deg.
0.5
Load
4/4
Timer adjustment_05
Pump speed
r/min
1100
Advance angle
deg.
2.5
2
3
Load
4/4
Remarks
Finish
Finish
Test data Ex:
Governor adjustment
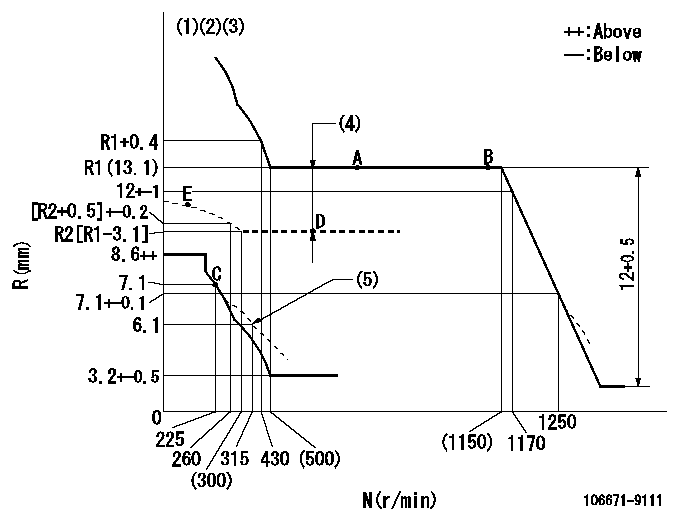
N:Pump speed
R:Rack position (mm)
(1)Lever ratio: RT
(2)Target shim dimension: TH
(3)Tolerance for racks not indicated: +-0.05mm.
(4)Boost compensator stroke: BCL
(5)Damper spring setting
----------
RT=1 TH=2.7mm BCL=3.1+-0.1mm
----------
----------
RT=1 TH=2.7mm BCL=3.1+-0.1mm
----------
Speed control lever angle

F:Full speed
----------
----------
a=(18deg)+-5deg
----------
----------
a=(18deg)+-5deg
0000000901

F:Full load
I:Idle
(1)Stopper bolt setting
----------
----------
a=28deg+-5deg b=37deg+-3deg
----------
----------
a=28deg+-5deg b=37deg+-3deg
Stop lever angle
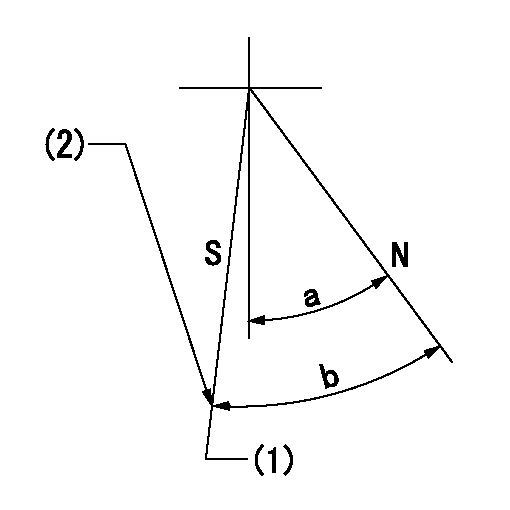
N:Pump normal
S:Stop the pump.
(1)Rack position = aa
(2)Stopper bolt setting
----------
aa=3.5-0.5mm
----------
a=38deg+-5deg b=38deg+7deg-5deg
----------
aa=3.5-0.5mm
----------
a=38deg+-5deg b=38deg+7deg-5deg
0000001501 MICRO SWITCH
Adjustment of the micro-switch
Adjust the bolt to obtain the following lever position when the micro-switch is ON.
(1)Speed N1
(2)Rack position Ra
----------
N1=325r/min Ra=6.8+-0.1mm
----------
----------
N1=325r/min Ra=6.8+-0.1mm
----------
Timing setting

(1)Pump vertical direction
(2)Coupling's key groove position at No 1 cylinder's beginning of injection
(3)B.T.D.C.: aa
(4)-
----------
aa=14deg
----------
a=(6deg)
----------
aa=14deg
----------
a=(6deg)
Information:
Personal injury or death can result from improper maintenance procedures. To avoid injury or death, follow the procedures exactly as stated below.
Before servicing/performing maintenance on the machine, electrical power must be physically disconnected; battery plugs must be disconnected from the batteries, or the trailing cable must be unplugged, and warning tags and padlocks shall be applied by a certified electrician. Certified electricians shall perform or direct any electrical work, including any energized testing, repair work in controllers, motors, or other approved compartments, and shall insure that all compartments are properly closed and inspected prior to re-energization. All applicable lock out and tag out procedures must be followed.
Do not operate the machine if any guards or covers are missing or inadequately secured. Personnel could be seriously injured or machine damage may occur.
Observe the safe working load limits of all lifting and blocking devices and keep a safe distance from suspended/blocked loads. Personnel may be seriously injured or killed by falling loads.
Required Parts
Table 2
Required Parts
Item Qty Part Number Part Name
1 1 574-7991 Film Field Rework Procedure
Illustration 1 g06471195
DEF injector hose connector contacting the clearance hole
Visually inspect the DEF injector clearance hole for evidence of rub and wear for the DEF injector hose connector.
Illustration 2 g06480781
Clearance hole before grinding
Illustration 3 g06471198
Detail of area A
(D1) 12.1 mm (0.48 inch)
(D2) 75 mm (2.9 inch)
(D3) 50 mm (1.96 inch)
Illustration 4 g06471200
(D4) 50 mm (1.96 inch)
(D5) 12.6 mm (0.49 inch)
(D6) 11.7 mm (0.46 inch)
(D7) 75 mm (2.9 inch)
(D8) Radius is 35 mm (1.4 inch)
If evidence of contact is found, remove the hose connector from the DEF injector. Use die-grinder to increase size of the clearance hole from outside of the machine. Refer to the dimensions that are provided in Illustration 3 and Illustration 4.Note: To prevent unexpected lowering of the lift arms, use a lift arm safety brace to lock the lift arms in raised position. Refer to Operation and Maintenance Manual , SEBU9084 , "Loader Lift Arm Brace Operation".
Illustration 5 g06471201
DEF hose reconnected to outer connector
After the clearance hole is increased, connect the hose connector for DEF to the outer connector on the DEF injector. Verify the clearance between the frame and the DEF hose connector.
Illustration 6 g06471202
Increased clearance hole
Rotate hose connector towards front of machine. Refer to Illustration 6 for proper orientation. The increased hole is large enough to provide clearance for the hose connector.
Illustration 7 g06471206
(1) 574-7991 Film
Paint any bare metal to prevent rust and cover the clearance hole with film (1).