Information injection-pump assembly
BOSCH
F 019 Z10 413
f019z10413
ZEXEL
106671-8680
1066718680
HINO
220204420A
220204420a
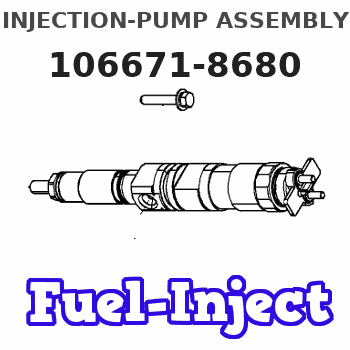
Rating:
Service parts 106671-8680 INJECTION-PUMP ASSEMBLY:
1.
_
7.
COUPLING PLATE
8.
_
9.
_
11.
Nozzle and Holder
236002191B
12.
Open Pre:MPa(Kqf/cm2)
21.6(220)
15.
NOZZLE SET
Include in #1:
106671-8680
as INJECTION-PUMP ASSEMBLY
Cross reference number
BOSCH
F 019 Z10 413
f019z10413
ZEXEL
106671-8680
1066718680
HINO
220204420A
220204420a
Zexel num
Bosch num
Firm num
Name
Calibration Data:
Adjustment conditions
Test oil
1404 Test oil ISO4113 or {SAEJ967d}
1404 Test oil ISO4113 or {SAEJ967d}
Test oil temperature
degC
40
40
45
Nozzle and nozzle holder
105780-8140
Bosch type code
EF8511/9A
Nozzle
105780-0000
Bosch type code
DN12SD12T
Nozzle holder
105780-2080
Bosch type code
EF8511/9
Opening pressure
MPa
17.2
Opening pressure
kgf/cm2
175
Injection pipe
Outer diameter - inner diameter - length (mm) mm 8-3-600
Outer diameter - inner diameter - length (mm) mm 8-3-600
Overflow valve (drive side)
134424-2120
Overflow valve opening pressure (drive side)
kPa
162
147
177
Overflow valve opening pressure (drive side)
kgf/cm2
1.65
1.5
1.8
Overflow valve (governor side)
134424-2120
Overflow valve opening pressure (governor side)
kPa
162
147
177
Overflow valve opening pressure (governor side)
kgf/cm2
1.65
1.5
1.8
Tester oil delivery pressure
kPa
157
157
157
Tester oil delivery pressure
kgf/cm2
1.6
1.6
1.6
Direction of rotation (viewed from drive side)
Right R
Right R
Injection timing adjustment
Direction of rotation (viewed from drive side)
Right R
Right R
Injection order
1-4-2-6-
3-5
Pre-stroke
mm
4.1
4.04
4.1
Beginning of injection position
Drive side NO.1
Drive side NO.1
Difference between angles 1
Cal 1-4 deg. 60 59.75 60.25
Cal 1-4 deg. 60 59.75 60.25
Difference between angles 2
Cyl.1-2 deg. 120 119.75 120.25
Cyl.1-2 deg. 120 119.75 120.25
Difference between angles 3
Cal 1-6 deg. 180 179.75 180.25
Cal 1-6 deg. 180 179.75 180.25
Difference between angles 4
Cal 1-3 deg. 240 239.75 240.25
Cal 1-3 deg. 240 239.75 240.25
Difference between angles 5
Cal 1-5 deg. 300 299.75 300.25
Cal 1-5 deg. 300 299.75 300.25
Injection quantity adjustment
Adjusting point
A
Rack position
11
Pump speed
r/min
1160
1160
1160
Average injection quantity
mm3/st.
250
245
255
Max. variation between cylinders
%
0
-2
2
Basic
*
Fixing the lever
*
Boost pressure
kPa
140
140
Boost pressure
mmHg
1050
1050
Injection quantity adjustment_02
Adjusting point
B
Rack position
3.7+-0.5
Pump speed
r/min
265
265
265
Average injection quantity
mm3/st.
11.5
8.5
14.5
Max. variation between cylinders
%
0
-15
15
Fixing the rack
*
Boost pressure
kPa
0
0
0
Boost pressure
mmHg
0
0
0
Boost compensator adjustment
Pump speed
r/min
500
500
500
Rack position
R1-4.1
Boost pressure
kPa
10.7
8
13.4
Boost pressure
mmHg
80
60
100
Boost compensator adjustment_02
Pump speed
r/min
500
500
500
Rack position
R1(11)
Boost pressure
kPa
127
127
127
Boost pressure
mmHg
950
950
950
Timer adjustment
Pump speed
r/min
900--
Advance angle
deg.
0
0
0
Remarks
Start
Start
Timer adjustment_02
Pump speed
r/min
850
Advance angle
deg.
0.3
Timer adjustment_03
Pump speed
r/min
1100
Advance angle
deg.
1
0.7
1.3
Remarks
Finish
Finish
Test data Ex:
Governor adjustment
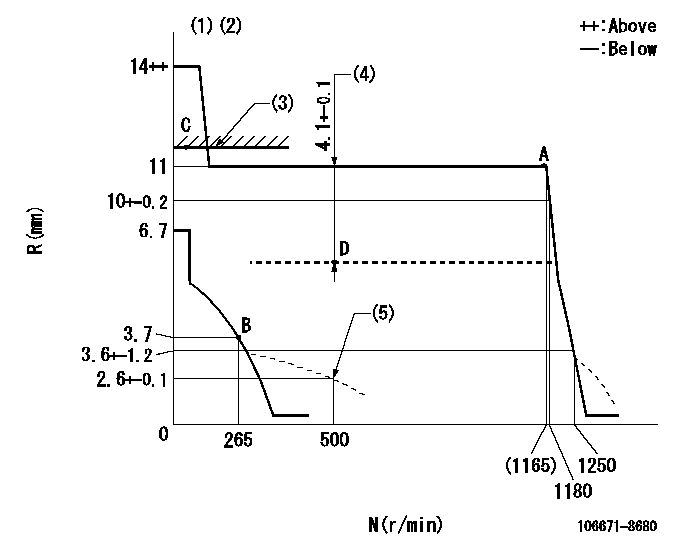
N:Pump speed
R:Rack position (mm)
(1)Target notch: K
(2)Tolerance for racks not indicated: +-0.05mm.
(3)Boost compensator excessive fuel lever at operation: L1 (at 0 boost pressure)
(4)Boost compensator stroke (at N = N1)
(5)Damper spring setting
----------
K=7 L1=R1+0.2mm N1=500r/min
----------
----------
K=7 L1=R1+0.2mm N1=500r/min
----------
Speed control lever angle
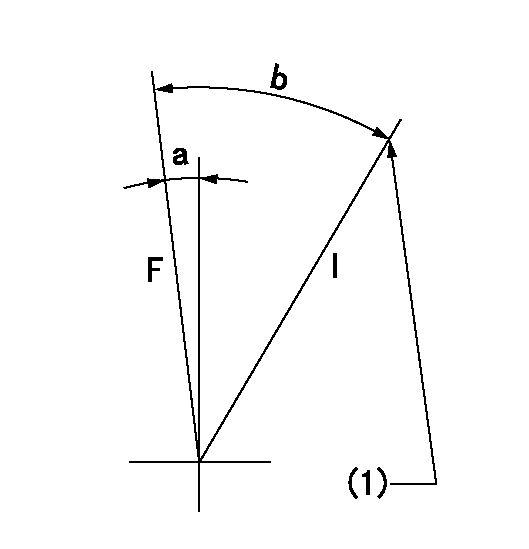
F:Full speed
I:Idle
(1)Stopper bolt setting
----------
----------
a=4deg+-5deg b=32deg+-5deg
----------
----------
a=4deg+-5deg b=32deg+-5deg
Stop lever angle

N:Pump normal
S:Stop the pump.
(1)Rack position aa or less, pump speed bb
----------
aa=3.2mm bb=0r/min
----------
a=27.5deg+-5deg b=53deg+-5deg
----------
aa=3.2mm bb=0r/min
----------
a=27.5deg+-5deg b=53deg+-5deg
0000001101
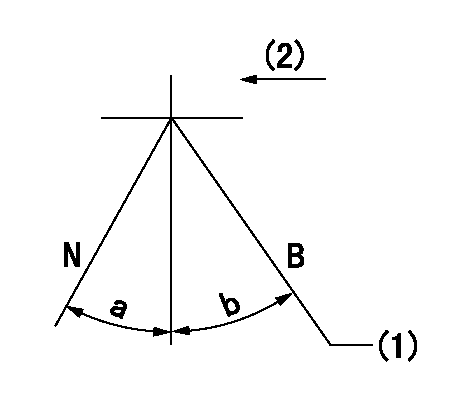
N:Normal
B:When boosted
(1)Rack position = aa
(2)Drive side
----------
aa=R1+0.2mm
----------
a=(15deg) b=(15deg)
----------
aa=R1+0.2mm
----------
a=(15deg) b=(15deg)
Timing setting
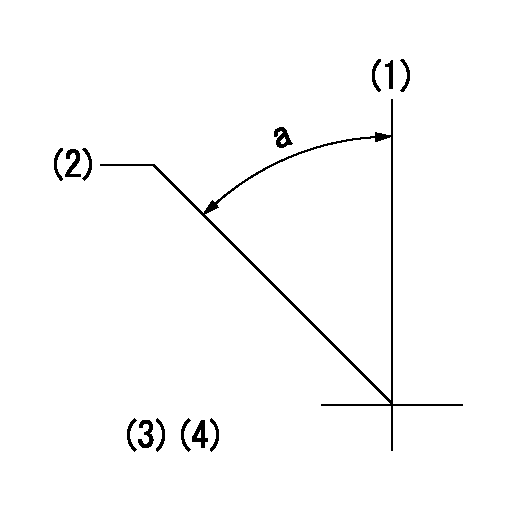
(1)Pump vertical direction
(2)Coupling's key groove position at No 1 cylinder's beginning of injection
(3)-
(4)-
----------
----------
a=(50deg)
----------
----------
a=(50deg)
Information:
Indicator Readings
If, the indicator reading a positive (+), the tip of the indicator moved into the indicator and minus (-) means that the tip of the indicator moved out of the dial indicator.When comparing two positive (+) indicator readings, the larger numerical reading is more than the smaller numerical reading. However, when comparing two minus (-) indicator readings, the larger numerical reading is less than the smaller numerical reading. In both cases, the indicator reading becomes less as the tip of the indicator moves out of the dial indicator.The Total Indicator Reading (TIR) is the total amount of movement of the indicator needle. The TIR is always a positive value even though one or both of the readings are negative. For example: If the indicator reading varied from -10 to +5, the TIR was 15. If the indicator reading is varied from -5 to - 15, the TIR was 10.Laser Tool Alignment Procedure
Note: Refer to the laser alignment tool user manual instructions for additional information regarding operation of the tool.To do laser tool alignment, perform the following steps:
Mount the transducer to the outer coupling element.
Attach the reflector to the generator hub.
Enter the required dimensions into the laser alignment tool. Examples of possible dimensions required include the following:
Transducer to reflector
Transducer to coupling centerline
Coupling diameter
Rotations Per Minute (RPM)
Transducer to front feet
Front feet to rear feet
Turn the laser ON, adjust the laser beam to the center of the reflector dust cap. Once the laser beam is centered, remove the dust cap.
Rotate the drive line one complete revolution.
Record the results displayed on the laser alignment tool. Compare the readings to the acceptable values listed in the "Generator Set Alignment Data Sheet".
Adjust the generator as needed to obtain the correct alignment. Shims may be installed or removed to achieve the correct vertical alignment. Use the horizontal adjustment screws to make horizontal adjustments.
Once the alignment is within the specifications, torque the generator mounting bolts to the proper specifications.
Perform a soft foot check. Refer to "Soft Foot Check Procedure".Soft Foot Check Procedure
Note: The soft foot check can be completed with the laser alignment tool if the tool has this function.
Ensure that all jacking screws are loose
Mount a dial indicator from the base assembly to the top of the generator mounting foot to be measured.
Preload the dial indicator to a minimum of one revolution or 2 mm (0.08 inch). Once the correct preload is set, zero the dial indicator.
Loosen the mounting bolt at the location that is being measured. Measure and record the vertical deflection of the generator mounting foot at this location as close to the mounting bolt as possible. Only loosen one bolt at a time.
The maximum deflection of the mounting foot is 0.076 mm (0.003 inch). If the indicator reading is greater than this amount, add shims to eliminate the soft foot condition. Torque the mounting bolt before moving to the next mounting foot to be measured for soft foot.
Repeat the procedure on the remaining generator mounting feet.
Perform the final torque of the
If, the indicator reading a positive (+), the tip of the indicator moved into the indicator and minus (-) means that the tip of the indicator moved out of the dial indicator.When comparing two positive (+) indicator readings, the larger numerical reading is more than the smaller numerical reading. However, when comparing two minus (-) indicator readings, the larger numerical reading is less than the smaller numerical reading. In both cases, the indicator reading becomes less as the tip of the indicator moves out of the dial indicator.The Total Indicator Reading (TIR) is the total amount of movement of the indicator needle. The TIR is always a positive value even though one or both of the readings are negative. For example: If the indicator reading varied from -10 to +5, the TIR was 15. If the indicator reading is varied from -5 to - 15, the TIR was 10.Laser Tool Alignment Procedure
Note: Refer to the laser alignment tool user manual instructions for additional information regarding operation of the tool.To do laser tool alignment, perform the following steps:
Mount the transducer to the outer coupling element.
Attach the reflector to the generator hub.
Enter the required dimensions into the laser alignment tool. Examples of possible dimensions required include the following:
Transducer to reflector
Transducer to coupling centerline
Coupling diameter
Rotations Per Minute (RPM)
Transducer to front feet
Front feet to rear feet
Turn the laser ON, adjust the laser beam to the center of the reflector dust cap. Once the laser beam is centered, remove the dust cap.
Rotate the drive line one complete revolution.
Record the results displayed on the laser alignment tool. Compare the readings to the acceptable values listed in the "Generator Set Alignment Data Sheet".
Adjust the generator as needed to obtain the correct alignment. Shims may be installed or removed to achieve the correct vertical alignment. Use the horizontal adjustment screws to make horizontal adjustments.
Once the alignment is within the specifications, torque the generator mounting bolts to the proper specifications.
Perform a soft foot check. Refer to "Soft Foot Check Procedure".Soft Foot Check Procedure
Note: The soft foot check can be completed with the laser alignment tool if the tool has this function.
Ensure that all jacking screws are loose
Mount a dial indicator from the base assembly to the top of the generator mounting foot to be measured.
Preload the dial indicator to a minimum of one revolution or 2 mm (0.08 inch). Once the correct preload is set, zero the dial indicator.
Loosen the mounting bolt at the location that is being measured. Measure and record the vertical deflection of the generator mounting foot at this location as close to the mounting bolt as possible. Only loosen one bolt at a time.
The maximum deflection of the mounting foot is 0.076 mm (0.003 inch). If the indicator reading is greater than this amount, add shims to eliminate the soft foot condition. Torque the mounting bolt before moving to the next mounting foot to be measured for soft foot.
Repeat the procedure on the remaining generator mounting feet.
Perform the final torque of the