Information injection-pump assembly
BOSCH
9 400 616 961
9400616961
ZEXEL
106671-7910
1066717910
MITSUBISHI
ME050868
me050868

Rating:
Service parts 106671-7910 INJECTION-PUMP ASSEMBLY:
1.
_
7.
COUPLING PLATE
8.
_
9.
_
11.
Nozzle and Holder
ME059740
12.
Open Pre:MPa(Kqf/cm2)
21.6(220)
15.
NOZZLE SET
Include in #1:
106671-7910
as INJECTION-PUMP ASSEMBLY
Cross reference number
BOSCH
9 400 616 961
9400616961
ZEXEL
106671-7910
1066717910
MITSUBISHI
ME050868
me050868
Zexel num
Bosch num
Firm num
Name
106671-7910
9 400 616 961
ME050868 MITSUBISHI
INJECTION-PUMP ASSEMBLY
6D22TC * K
6D22TC * K
Calibration Data:
Adjustment conditions
Test oil
1404 Test oil ISO4113 or {SAEJ967d}
1404 Test oil ISO4113 or {SAEJ967d}
Test oil temperature
degC
40
40
45
Nozzle and nozzle holder
105780-8140
Bosch type code
EF8511/9A
Nozzle
105780-0000
Bosch type code
DN12SD12T
Nozzle holder
105780-2080
Bosch type code
EF8511/9
Opening pressure
MPa
17.2
Opening pressure
kgf/cm2
175
Injection pipe
Outer diameter - inner diameter - length (mm) mm 8-3-600
Outer diameter - inner diameter - length (mm) mm 8-3-600
Overflow valve
131424-4620
Overflow valve opening pressure
kPa
255
221
289
Overflow valve opening pressure
kgf/cm2
2.6
2.25
2.95
Tester oil delivery pressure
kPa
157
157
157
Tester oil delivery pressure
kgf/cm2
1.6
1.6
1.6
Direction of rotation (viewed from drive side)
Right R
Right R
Injection timing adjustment
Direction of rotation (viewed from drive side)
Right R
Right R
Injection order
1-5-3-6-
2-4
Pre-stroke
mm
4.8
4.75
4.85
Beginning of injection position
Governor side NO.1
Governor side NO.1
Difference between angles 1
Cal 1-5 deg. 60 59.5 60.5
Cal 1-5 deg. 60 59.5 60.5
Difference between angles 2
Cal 1-3 deg. 120 119.5 120.5
Cal 1-3 deg. 120 119.5 120.5
Difference between angles 3
Cal 1-6 deg. 180 179.5 180.5
Cal 1-6 deg. 180 179.5 180.5
Difference between angles 4
Cyl.1-2 deg. 240 239.5 240.5
Cyl.1-2 deg. 240 239.5 240.5
Difference between angles 5
Cal 1-4 deg. 300 299.5 300.5
Cal 1-4 deg. 300 299.5 300.5
Injection quantity adjustment
Adjusting point
A
Rack position
11.4
Pump speed
r/min
750
750
750
Average injection quantity
mm3/st.
154.7
151.7
157.7
Max. variation between cylinders
%
0
-3
3
Basic
*
Fixing the lever
*
Injection quantity adjustment_02
Adjusting point
B
Rack position
10.8
Pump speed
r/min
750
750
750
Average injection quantity
mm3/st.
137.9
134.9
140.9
Fixing the lever
*
Injection quantity adjustment_03
Adjusting point
C
Rack position
6.3+-0.5
Pump speed
r/min
300
300
300
Average injection quantity
mm3/st.
11.2
8.6
13.8
Fixing the rack
*
Remarks
(check)
(check)
Injection quantity adjustment_04
Adjusting point
D
Rack position
5.5+-0.5
Pump speed
r/min
500
500
500
Average injection quantity
mm3/st.
10.2
7.6
12.8
Max. variation between cylinders
%
0
-15
15
Fixing the rack
*
Timer adjustment
Pump speed
r/min
900++
Advance angle
deg.
0
0
0
Remarks
Do not advance until starting N = 900.
Do not advance until starting N = 900.
Timer adjustment_02
Pump speed
r/min
900
Advance angle
deg.
0.5
Timer adjustment_03
Pump speed
r/min
-
Advance angle
deg.
1.5
1.5
1.5
Remarks
Measure the actual speed, stop
Measure the actual speed, stop
Test data Ex:
Governor adjustment
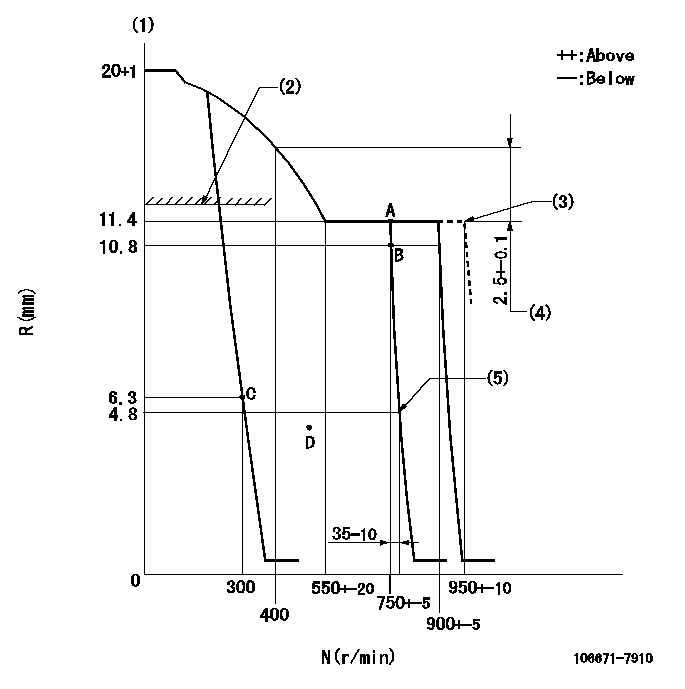
N:Pump speed
R:Rack position (mm)
(1)Target notch: K
(2)RACK LIMIT: RAL
(3)At shipping
(4)Rack difference between N = N1 and N = N2
(5)Idle sub spring setting: L1.
----------
K=6 RAL=11.7+0.2mm N1=750r/min N2=400r/min L1=4.3+-0.1mm
----------
----------
K=6 RAL=11.7+0.2mm N1=750r/min N2=400r/min L1=4.3+-0.1mm
----------
Speed control lever angle

F:Full speed
I:Idle
(1)Stopper bolt setting
(2)At shipping
(3)Pump speed = aa
(4)Pump speed = bb
----------
aa=750r/min bb=900r/min
----------
a=(25deg)+-5deg b=(2deg) c=(0deg)+-5dg d=(7deg)+-5dg
----------
aa=750r/min bb=900r/min
----------
a=(25deg)+-5deg b=(2deg) c=(0deg)+-5dg d=(7deg)+-5dg
Stop lever angle

N:Pump normal
S:Stop the pump.
----------
----------
a=19deg+-5deg b=53deg+-5deg
----------
----------
a=19deg+-5deg b=53deg+-5deg
Timing setting

(1)Pump vertical direction
(2)Coupling's key groove position at No 1 cylinder's beginning of injection
(3)-
(4)-
----------
----------
a=(7deg)
----------
----------
a=(7deg)
Information:
Introduction
Procedure to prevent injector Plunger Spring failure due to inadequate fuel system priming.
The low-pressure fuel system must be primed after injector replacement or other repair to the low-pressure fuel system circuit which may allow air to enter the system.
Inadequate priming can result in air being present in the low-pressure fuel system and inside the injectors.
Attempting to start the engine without adequate priming may result in an early hour failure of the injector plunger spring.
Follow the procedure below to prevent injector failure due to inadequate priming.
DO NOT START THE ENGINE WITHOUT PRIMING THE FUEL SYSTEM
Illustration 1 g03735591
Damaged plunger spring due to improper fuel system primingFuel System Priming Procedure:
Disconnect the injector harness at the valve cover.
Use the hand primer to fill the fuel system. Pump until the hand primer becomes too hard to depress by hand.
Crank the engine 3 times for 15 seconds each. Reapply the hand primer after each cranking cycle.
Once the hand primer remains hard to depress after the 15 second crank, reconnect the injector harness and start the engine.
Clear any related fault codes (ET) that were logged while cranking the engine with the injector harness disconnected.
Illustration 2 g03736011
Procedure to prevent injector Plunger Spring failure due to inadequate fuel system priming.
The low-pressure fuel system must be primed after injector replacement or other repair to the low-pressure fuel system circuit which may allow air to enter the system.
Inadequate priming can result in air being present in the low-pressure fuel system and inside the injectors.
Attempting to start the engine without adequate priming may result in an early hour failure of the injector plunger spring.
Follow the procedure below to prevent injector failure due to inadequate priming.
DO NOT START THE ENGINE WITHOUT PRIMING THE FUEL SYSTEM
Illustration 1 g03735591
Damaged plunger spring due to improper fuel system primingFuel System Priming Procedure:
Disconnect the injector harness at the valve cover.
Use the hand primer to fill the fuel system. Pump until the hand primer becomes too hard to depress by hand.
Crank the engine 3 times for 15 seconds each. Reapply the hand primer after each cranking cycle.
Once the hand primer remains hard to depress after the 15 second crank, reconnect the injector harness and start the engine.
Clear any related fault codes (ET) that were logged while cranking the engine with the injector harness disconnected.
Illustration 2 g03736011
Have questions with 106671-7910?
Group cross 106671-7910 ZEXEL
Mitsubishi
106671-7910
9 400 616 961
ME050868
INJECTION-PUMP ASSEMBLY
6D22TC
6D22TC