Information injection-pump assembly
BOSCH
F 01G 09U 07M
f01g09u07m
ZEXEL
106671-7870
1066717870
MITSUBISHI
ME056752
me056752

Rating:
Service parts 106671-7870 INJECTION-PUMP ASSEMBLY:
1.
_
7.
COUPLING PLATE
8.
_
9.
_
11.
Nozzle and Holder
ME056357
12.
Open Pre:MPa(Kqf/cm2)
17.7{180}/21.6{220}
15.
NOZZLE SET
Include in #1:
106671-7870
as INJECTION-PUMP ASSEMBLY
Cross reference number
BOSCH
F 01G 09U 07M
f01g09u07m
ZEXEL
106671-7870
1066717870
MITSUBISHI
ME056752
me056752
Zexel num
Bosch num
Firm num
Name
Calibration Data:
Adjustment conditions
Test oil
1404 Test oil ISO4113 or {SAEJ967d}
1404 Test oil ISO4113 or {SAEJ967d}
Test oil temperature
degC
40
40
45
Nozzle and nozzle holder
105780-8140
Bosch type code
EF8511/9A
Nozzle
105780-0000
Bosch type code
DN12SD12T
Nozzle holder
105780-2080
Bosch type code
EF8511/9
Opening pressure
MPa
17.2
Opening pressure
kgf/cm2
175
Injection pipe
Outer diameter - inner diameter - length (mm) mm 8-3-600
Outer diameter - inner diameter - length (mm) mm 8-3-600
Overflow valve
131424-4620
Overflow valve opening pressure
kPa
255
221
289
Overflow valve opening pressure
kgf/cm2
2.6
2.25
2.95
Tester oil delivery pressure
kPa
157
157
157
Tester oil delivery pressure
kgf/cm2
1.6
1.6
1.6
RED3 control unit part number
407910-2
470
RED3 rack sensor specifications
mm
15
Direction of rotation (viewed from drive side)
Right R
Right R
Injection timing adjustment
Direction of rotation (viewed from drive side)
Right R
Right R
Injection order
1-5-3-6-
2-4
Pre-stroke
mm
4.8
4.75
4.85
Beginning of injection position
Governor side NO.1
Governor side NO.1
Difference between angles 1
Cal 1-5 deg. 60 59.5 60.5
Cal 1-5 deg. 60 59.5 60.5
Difference between angles 2
Cal 1-3 deg. 120 119.5 120.5
Cal 1-3 deg. 120 119.5 120.5
Difference between angles 3
Cal 1-6 deg. 180 179.5 180.5
Cal 1-6 deg. 180 179.5 180.5
Difference between angles 4
Cyl.1-2 deg. 240 239.5 240.5
Cyl.1-2 deg. 240 239.5 240.5
Difference between angles 5
Cal 1-4 deg. 300 299.5 300.5
Cal 1-4 deg. 300 299.5 300.5
Injection quantity adjustment
Rack position
(9.3)
Vist
V
2.14
2.14
2.14
Pump speed
r/min
700
700
700
Average injection quantity
mm3/st.
138
137
139
Max. variation between cylinders
%
0
-2
2
Basic
*
Injection quantity adjustment_02
Rack position
(5.2)
Vist
V
2.96
2.86
3.06
Pump speed
r/min
500
500
500
Average injection quantity
mm3/st.
10
8
12
Max. variation between cylinders
%
0
-15
15
Test data Ex:
Governor adjustment

(1)Adjusting range
(2)Step response time
(N): Speed of the pump
(L): Load
(theta) Advance angle
(Srd1) Step response time 1
(Srd2) Step response time 2
1. Adjusting conditions for the variable timer
(1)Adjust the clearance between the pickup and the protrusion to L.
----------
L=1-0.2mm N2=800r/min C2=(8.8deg) t1=2.5--sec. t2=2.5--sec.
----------
N1=750++r/min P1=0kPa(0kgf/cm2) P2=392kPa(4kgf/cm2) C1=8.8+-0.3deg R01=0/4load R02=4/4load
----------
L=1-0.2mm N2=800r/min C2=(8.8deg) t1=2.5--sec. t2=2.5--sec.
----------
N1=750++r/min P1=0kPa(0kgf/cm2) P2=392kPa(4kgf/cm2) C1=8.8+-0.3deg R01=0/4load R02=4/4load
Speed control lever angle
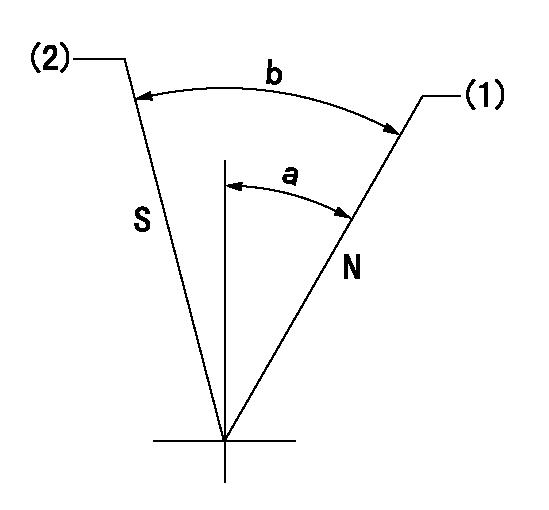
N:Pump normal
S:Stop the pump.
(1)Rack position = aa
(2)Rack position bb
----------
aa=16mm bb=1mm
----------
a=19deg+-5deg b=29deg+-5deg
----------
aa=16mm bb=1mm
----------
a=19deg+-5deg b=29deg+-5deg
0000000901

(1)Pump vertical direction
(2)Coupling's key groove position at No 1 cylinder's beginning of injection
(3)B.T.D.C.: aa
(4)-
----------
aa=9deg
----------
a=(7deg)
----------
aa=9deg
----------
a=(7deg)
Stop lever angle

(Rs) rack sensor specifications
(C/U) control unit part number
(V) Rack sensor output voltage
(R) Rack position (mm)
1. Confirming governor output characteristics (rack 15 mm, span 6 mm)
(1)When the output voltages of the rack sensor are V1 and V2, check that the rack positions R1 and R2 in the table above are satisfied.
----------
----------
----------
----------
Information:
Table 1
S O S Oil Analysis Guidelines    
Test Parameter     Guideline    
Oxidation     (1)    
Soot     (1)    
Sulfation     (1)    
Wear Metals     Trend Analysis and Cat Wear Table (1) norms    
Water     0.5% maximum    
Glycol     0%    
Fuel Dilution     Based on viscosity (1) and GC (2) fuel dilution in excess of 4%    
Viscosity "ASTM D445" measured at 100° C (212° F)     +/-3 centistokes (cSt) change from new oil viscosity.    
( 1 ) Acceptable values for these parameters are proprietary to the S O S oil analysis program.
( 2 ) Gas ChromatographConsult your Caterpillar dealer for complete information and assistance about the S O S oil analysis program.Obtaining S O S Oil Samples
Before you obtain an S O S oil sample, operate the engine until the oil is warm and the oil is well circulated. Then obtain the S O S oil sample.In order to obtain a good oil sample, do not take the oil sample from the drain stream. The drain stream method can allow a stream of dirty oil from the bottom of the compartment to contaminate the sample. Likewise, never dip an oil sample from an oil container or pour a sample from a used filter.There are two acceptable ways to obtain S O S oil samples. The following methods are listed in the order that is preferred:
Use an in-line sampling valve on the pressurized oil manifold.
Use a sampling gun (vacuum pump) that is inserted into the sump.Use of the in-line sampling valve is the preferred method. This method provides samples that are less likely to be contaminated. In order to obtain an oil sample from the engine, it may be necessary to increase the engine's speed. Normally, the oil sample is taken at low idle. If the flow rate is too low, increase engine speed to high idle in order to obtain the oil sample.
Do not use the same vacuum sampling pump for extracting oil samples that is used for extracting coolant samples.A small residue of either type sample may remain in the pump and may cause a false positive analysis for the sample being taken.Always use a separate pump for oil sampling and a separate pump for coolant sampling.Failure to do so may cause a false analysis which could lead to customer and dealer concerns.
Oil Sampling Interval
Take the oil samples as close as possible to the standard intervals. In order to receive the full value from S O S oil analysis, you must establish a consistent trend of data. In order to establish pertinent history of data, perform consistent oil samplings that are evenly spaced.
Table 2
Compartment     Engine    
Recommended Sampling Interval    
24140 kilometers (15000 miles)
(1) (2)    
Sampling Valve     Yes    
Oil Type     DEO, DEO-ULS    
Recommended Oil Change Interval     (3)    
( 1 ) Under certain conditions, the Caterpillar dealer or the Operation and Maintenance Manual may allow a longer