Information injection-pump assembly
BOSCH
9 400 616 954
9400616954
ZEXEL
106671-7830
1066717830
MITSUBISHI
ME050859
me050859
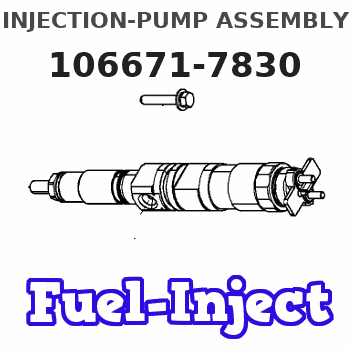
Rating:
Service parts 106671-7830 INJECTION-PUMP ASSEMBLY:
1.
_
7.
COUPLING PLATE
8.
_
9.
_
11.
Nozzle and Holder
ME059622
12.
Open Pre:MPa(Kqf/cm2)
21.6(220)
15.
NOZZLE SET
Include in #1:
106671-7830
as INJECTION-PUMP ASSEMBLY
Cross reference number
BOSCH
9 400 616 954
9400616954
ZEXEL
106671-7830
1066717830
MITSUBISHI
ME050859
me050859
Zexel num
Bosch num
Firm num
Name
Calibration Data:
Adjustment conditions
Test oil
1404 Test oil ISO4113 or {SAEJ967d}
1404 Test oil ISO4113 or {SAEJ967d}
Test oil temperature
degC
40
40
45
Nozzle and nozzle holder
105780-8140
Bosch type code
EF8511/9A
Nozzle
105780-0000
Bosch type code
DN12SD12T
Nozzle holder
105780-2080
Bosch type code
EF8511/9
Opening pressure
MPa
17.2
Opening pressure
kgf/cm2
175
Injection pipe
Outer diameter - inner diameter - length (mm) mm 8-3-600
Outer diameter - inner diameter - length (mm) mm 8-3-600
Overflow valve
131424-4620
Overflow valve opening pressure
kPa
255
221
289
Overflow valve opening pressure
kgf/cm2
2.6
2.25
2.95
Tester oil delivery pressure
kPa
157
157
157
Tester oil delivery pressure
kgf/cm2
1.6
1.6
1.6
Direction of rotation (viewed from drive side)
Right R
Right R
Injection timing adjustment
Direction of rotation (viewed from drive side)
Right R
Right R
Injection order
1-5-3-6-
2-4
Pre-stroke
mm
4.8
4.75
4.85
Beginning of injection position
Governor side NO.1
Governor side NO.1
Difference between angles 1
Cal 1-5 deg. 60 59.5 60.5
Cal 1-5 deg. 60 59.5 60.5
Difference between angles 2
Cal 1-3 deg. 120 119.5 120.5
Cal 1-3 deg. 120 119.5 120.5
Difference between angles 3
Cal 1-6 deg. 180 179.5 180.5
Cal 1-6 deg. 180 179.5 180.5
Difference between angles 4
Cyl.1-2 deg. 240 239.5 240.5
Cyl.1-2 deg. 240 239.5 240.5
Difference between angles 5
Cal 1-4 deg. 300 299.5 300.5
Cal 1-4 deg. 300 299.5 300.5
Injection quantity adjustment
Adjusting point
A
Rack position
11.4
Pump speed
r/min
1050
1050
1050
Average injection quantity
mm3/st.
126.6
123.6
129.6
Max. variation between cylinders
%
0
-3
3
Basic
*
Fixing the lever
*
Injection quantity adjustment_02
Adjusting point
B
Rack position
4.8+-0.5
Pump speed
r/min
500
500
500
Average injection quantity
mm3/st.
9.4
6.8
12
Max. variation between cylinders
%
0
-15
15
Fixing the rack
*
Injection quantity adjustment_03
Adjusting point
D
Rack position
5.1+-0.5
Pump speed
r/min
425
425
425
Average injection quantity
mm3/st.
9.8
7.2
12.4
Fixing the rack
*
Remarks
(check)
(check)
Timer adjustment
Pump speed
r/min
1200
Advance angle
deg.
0.5
Timer adjustment_02
Pump speed
r/min
-
Advance angle
deg.
2
2
2
Remarks
Measure the actual speed, stop
Measure the actual speed, stop
Test data Ex:
Governor adjustment
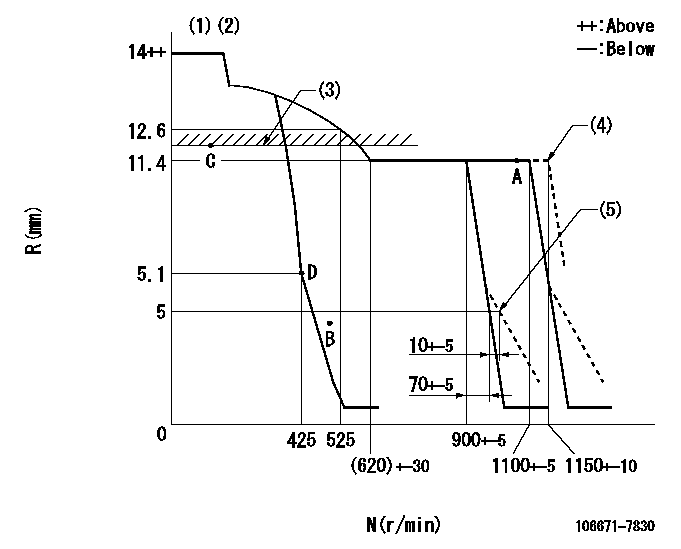
N:Pump speed
R:Rack position (mm)
(1)Target notch: K
(2)Torque spring does not operate.
(3)RACK LIMIT: RAL
(4)Setting at shipping
(5)Set idle sub-spring
----------
K=6 RAL=12+0.2mm
----------
----------
K=6 RAL=12+0.2mm
----------
Speed control lever angle

F:Full speed
I:Idle
(1)Stopper bolt setting
(2)At shipping
(3)Set the pump speed at aa
(4)Set the pump speed at bb.
----------
aa=900r/min bb=1100r/min
----------
a=27deg+-5deg b=(2deg) c=7deg+-5deg d=7deg+-5deg
----------
aa=900r/min bb=1100r/min
----------
a=27deg+-5deg b=(2deg) c=7deg+-5deg d=7deg+-5deg
Stop lever angle

N:Pump normal
S:Stop the pump.
----------
----------
a=19deg+-5deg b=53deg+-5deg
----------
----------
a=19deg+-5deg b=53deg+-5deg
Timing setting

(1)Pump vertical direction
(2)Coupling's key groove position at No 1 cylinder's beginning of injection
(3)-
(4)-
----------
----------
a=(7deg)
----------
----------
a=(7deg)
Information:
Introduction
Injector height setting is extremely important during the engine assembly process. The recommended intervals that are specified in the Operation and Maintenance Manual must be followed.Problem
An issue has been identified with the correct injector height settings. Check the injector height. Bottoming of the fuel injector rocker arm may be caused by the injector height being to high or low. Bottoming of the fuel injector can create a crack at the nose of the fuel injector rocker arm through the first and second threads of the adjusting screw hole. Once the crack has started it can result in the breaking of the fuel injector rocker arm at the nose. Breaking of the fuel injector rocker arm will result in an immediate poor engine performance.Solution
Performing the recommended inspection of the fuel injector rocker arm at the specified intervals in the operation and maintenance manual is important. Inspect the height
Injector height setting is extremely important during the engine assembly process. The recommended intervals that are specified in the Operation and Maintenance Manual must be followed.Problem
An issue has been identified with the correct injector height settings. Check the injector height. Bottoming of the fuel injector rocker arm may be caused by the injector height being to high or low. Bottoming of the fuel injector can create a crack at the nose of the fuel injector rocker arm through the first and second threads of the adjusting screw hole. Once the crack has started it can result in the breaking of the fuel injector rocker arm at the nose. Breaking of the fuel injector rocker arm will result in an immediate poor engine performance.Solution
Performing the recommended inspection of the fuel injector rocker arm at the specified intervals in the operation and maintenance manual is important. Inspect the height