Information injection-pump assembly
ZEXEL
106671-7610
1066717610
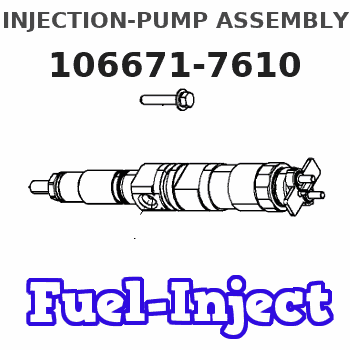
Rating:
Cross reference number
ZEXEL
106671-7610
1066717610
Zexel num
Bosch num
Firm num
Name
Calibration Data:
Adjustment conditions
Test oil
1404 Test oil ISO4113 or {SAEJ967d}
1404 Test oil ISO4113 or {SAEJ967d}
Test oil temperature
degC
40
40
45
Nozzle and nozzle holder
105780-8140
Bosch type code
EF8511/9A
Nozzle
105780-0000
Bosch type code
DN12SD12T
Nozzle holder
105780-2080
Bosch type code
EF8511/9
Opening pressure
MPa
17.2
Opening pressure
kgf/cm2
175
Injection pipe
Outer diameter - inner diameter - length (mm) mm 8-3-600
Outer diameter - inner diameter - length (mm) mm 8-3-600
Overflow valve
131424-4620
Overflow valve opening pressure
kPa
255
221
289
Overflow valve opening pressure
kgf/cm2
2.6
2.25
2.95
Tester oil delivery pressure
kPa
157
157
157
Tester oil delivery pressure
kgf/cm2
1.6
1.6
1.6
Direction of rotation (viewed from drive side)
Right R
Right R
Injection timing adjustment
Direction of rotation (viewed from drive side)
Right R
Right R
Injection order
1-5-3-6-
2-4
Pre-stroke
mm
4.8
4.75
4.85
Beginning of injection position
Governor side NO.1
Governor side NO.1
Difference between angles 1
Cal 1-5 deg. 60 59.5 60.5
Cal 1-5 deg. 60 59.5 60.5
Difference between angles 2
Cal 1-3 deg. 120 119.5 120.5
Cal 1-3 deg. 120 119.5 120.5
Difference between angles 3
Cal 1-6 deg. 180 179.5 180.5
Cal 1-6 deg. 180 179.5 180.5
Difference between angles 4
Cyl.1-2 deg. 240 239.5 240.5
Cyl.1-2 deg. 240 239.5 240.5
Difference between angles 5
Cal 1-4 deg. 300 299.5 300.5
Cal 1-4 deg. 300 299.5 300.5
Injection quantity adjustment
Adjusting point
-
Rack position
9.4
Pump speed
r/min
700
700
700
Each cylinder's injection qty
mm3/st.
144
140.5
147.5
Basic
*
Fixing the rack
*
Standard for adjustment of the maximum variation between cylinders
*
Injection quantity adjustment_02
Adjusting point
F
Rack position
5+-0.5
Pump speed
r/min
500
500
500
Each cylinder's injection qty
mm3/st.
16.5
14
19
Fixing the rack
*
Standard for adjustment of the maximum variation between cylinders
*
Injection quantity adjustment_03
Adjusting point
A
Rack position
R1(9.4)
Pump speed
r/min
700
700
700
Average injection quantity
mm3/st.
144
143
145
Basic
*
Fixing the lever
*
Boost pressure
kPa
28
28
Boost pressure
mmHg
210
210
Injection quantity adjustment_04
Adjusting point
B
Rack position
9.65+-0.
5
Pump speed
r/min
1100
1100
1100
Average injection quantity
mm3/st.
161
159
163
Fixing the lever
*
Boost pressure
kPa
28
28
Boost pressure
mmHg
210
210
Injection quantity adjustment_05
Adjusting point
C
Rack position
5.7+-0.5
Pump speed
r/min
225
225
225
Each cylinder's injection qty
mm3/st.
16.5
14
19
Fixing the rack
*
Boost pressure
kPa
0
0
0
Boost pressure
mmHg
0
0
0
Remarks
(check)
(check)
Injection quantity adjustment_06
Adjusting point
D
Rack position
-
Pump speed
r/min
100
100
100
Average injection quantity
mm3/st.
115
75
155
Fixing the lever
*
Boost pressure
kPa
0
0
0
Boost pressure
mmHg
0
0
0
Injection quantity adjustment_07
Adjusting point
G
Rack position
9.9+-0.5
Pump speed
r/min
500
500
500
Average injection quantity
mm3/st.
153
151
155
Fixing the lever
*
Boost pressure
kPa
28
28
Boost pressure
mmHg
210
210
Boost compensator adjustment
Pump speed
r/min
600
600
600
Rack position
8.2
Boost pressure
kPa
4
4
4
Boost pressure
mmHg
30
30
30
Boost compensator adjustment_02
Pump speed
r/min
600
600
600
Rack position
8.7
Boost pressure
kPa
8
6.7
9.3
Boost pressure
mmHg
60
50
70
Boost compensator adjustment_03
Pump speed
r/min
600
600
600
Rack position
R1(9.4)
Boost pressure
kPa
14.7
14.7
14.7
Boost pressure
mmHg
110
110
110
Test data Ex:
Governor adjustment
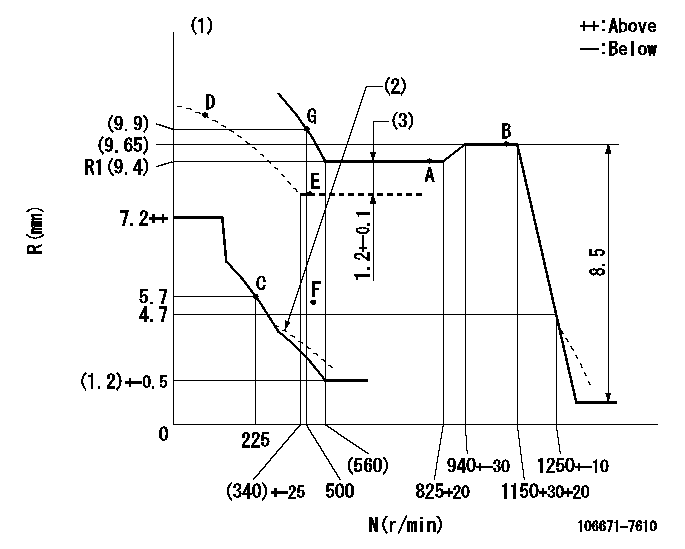
N:Pump speed
R:Rack position (mm)
(1)Boost compensator cancel stroke: BSL
(2)Damper spring setting: DL
(3)Boost compensator stroke
----------
BSL=1.6mm DL=4.5-0.2mm
----------
----------
BSL=1.6mm DL=4.5-0.2mm
----------
Timer adjustment

(1)Adjusting range
(2)Step response time
(N): Speed of the pump
(L): Load
(theta) Advance angle
(Srd1) Step response time 1
(Srd2) Step response time 2
1. Adjusting conditions for the variable timer
(1)Adjust the clearance between the pickup and the protrusion to L.
----------
L=1-0.2mm N2=800r/min C2=(8.8deg) t1=2.5--sec. t2=2.5--sec.
----------
N1=750++r/min P1=0kPa(0kgf/cm2) P2=392kPa(4kgf/cm2) C1=8.8+-0.3deg R01=0/4load R02=4/4load
----------
L=1-0.2mm N2=800r/min C2=(8.8deg) t1=2.5--sec. t2=2.5--sec.
----------
N1=750++r/min P1=0kPa(0kgf/cm2) P2=392kPa(4kgf/cm2) C1=8.8+-0.3deg R01=0/4load R02=4/4load
Speed control lever angle

F:Full speed
----------
----------
a=16.5deg+-5deg
----------
----------
a=16.5deg+-5deg
0000000901

F:Full load
I:Idle
(1)Stopper bolt setting
----------
----------
a=28deg+-5deg b=(30deg)+-3deg
----------
----------
a=28deg+-5deg b=(30deg)+-3deg
Stop lever angle

N:Engine manufacturer's normal use
S:Stop the pump.
(1)Rack position = aa
(2)Stopper bolt setting
(3)Rack position bb
(4)Free (at shipping)
----------
aa=4.1-0.5mm bb=13.3mm
----------
a=26deg+-5deg b=(38deg) c=0deg+7deg-5deg
----------
aa=4.1-0.5mm bb=13.3mm
----------
a=26deg+-5deg b=(38deg) c=0deg+7deg-5deg
0000001501 RACK SENSOR

V1:Supply voltage
V2f:Full side output voltage
V2i:Idle side output voltage
(A) Black
(B) Yellow
(C) Red
(D) Trimmer
(E): Shaft
(F) Nut
(G) Load lever
1. Load sensor adjustment
(1)Connect as shown in the above diagram and apply supply voltage V1.
(2)Hold the load lever (G) against the full side.
(3)Turn the shaft so that the voltage between (A) and (B) is V2.
(4)Hold the load lever (G) against the idle side.
(5)Adjust (D) so that the voltage between (A) and (B) is V2i.
(6)Repeat the above adjustments.
(7)Tighten the nut (F) at the point satisfying the standards.
(8)Hold the load lever against the full side stopper and the idle side stopper.
(9)At this time, confirm that the full side output voltage is V2f and the idle side output voltage is V2i.
----------
V1= 5+-0.02V V2f=0.15+0.03V V2i=2.35-0.03V
----------
----------
V1= 5+-0.02V V2f=0.15+0.03V V2i=2.35-0.03V
----------
0000001601 MICRO SWITCH
Adjustment of the micro-switch
Adjust the bolt to obtain the following lever position when the micro-switch is ON.
(1)Speed N1
(2)Rack position Ra
----------
N1=325+-5r/min Ra=5.4mm
----------
----------
N1=325+-5r/min Ra=5.4mm
----------
Timing setting

(1)Pump vertical direction
(2)Coupling's key groove position at No 1 cylinder's beginning of injection
(3)-
(4)-
----------
----------
a=(7deg)
----------
----------
a=(7deg)
Information:
Remove the smaller hex nut (15.88 mm) (10) from the new 396-0380 Coupling along with ferrule (11) and ferrule (12). Orient the parts as shown in Illustration 3. Loosely install the parts onto the existing half of the 396-0380 Coupling on the engine. Refer to Illustration 4. Do not tighten the nut at this time.Note: Failure to orient the ferrules as shown in Illustration 3 will result in leakage and the need to replace the parts.
Illustration 5 g06054145
(14) 485-1630 Hose As
Push the quick-connect end of hose (14) onto the fuel pump drain line tube. An audible click should be heard and the fuel line should stay attached when gently pulled.
Illustration 6 g06054154
(14) 485-1630 Hose As
(15) 5P-9085 Clip
Place two new clips (15) onto hose (14) as shown in Illustration 6.
Illustration 7 g06054168
(14) 485-1630 Hose As
(16) 6V-8455 Bolt
(17) 8T-4121 Hard Washer
Illustration 8 g06054107
Lift the tube end of hose (14) and place the hose into the connector nut as shown in Illustration 8. Hand-tighten the nut, only.
Loosely secure the two clips with new bolts (16) and washers (17).
Illustration 9 g06054123
Mark the tube connector nut at the 6 o'clock position.
Illustration 10 g06054127
While holding the lower fitting stationary with another wrench and pushing the tube downward, tighten the nut one and one-quarter revolutions until the mark is at the 9 o'clock position. Refer to Illustrations 8,9, and 10.
Once the fitting is tightened, tighten bolts (16) securing the two clips (Illustration 7). Tighten the vertically mounted bolt first, then tighten the horizontally mounted bolt. Tighten each bolt to 25 2 N m (18.5 1.5 lb ft).
Reuse the existing hardware and reinstall the secondary fuel filter base. Tighten the bolts to 45 5 N m (33 4 lb ft). Hold the filter base vertical while tightening the bolts.
Illustration 11 g06054224
(18) Banjo bolt
(19) Spigot
(20) Front port
(21) Rear port
(22) 485-1627 Hose As
(25) 228-6046 Connector
(26) 228-7100 O-Ring Seal
Remove banjo bolt (18) and spigot (19). Retain one of the washers. Replace the banjo bolt with the new 8T-4191 Bolt and the retained washer. Tighten the bolt to 22 2 N m (16 1.5 lb ft).
Illustration 12 g06054327
Hose release orientation
(22) 485-1627 Hose As
Install hose (22) on the pump. It is important to note that the plastic release must be rotated so the flat is aligned with the body of the pump. Refer to Illustration 12.
Install connector (25) and O-Ring (26) at rear port (21). Tighten the connector to 30 2 N m (22 1.5 lb ft).
Install the new 228-7089 O-Ring Seal onto the connector. Then, install the other end of hose (22) to the connector. Holding the hose angle at approximately 5 degrees clockwise from vertical down, tighten the hose to 30 2 N m (22 1.5 lb ft).
Install a new 228-7100 O-Ring Seal onto the 8T-7487 Connector and install at front port (20). Tighten the connector to 30 2 N m (22 1.5 lb ft).
Install the new 228-7088 O-Ring Seal on the 8T-7487 Connector.
Illustration 13 g06054360
Connect braided hose (3) to