Information injection-pump assembly
ZEXEL
106671-7280
1066717280
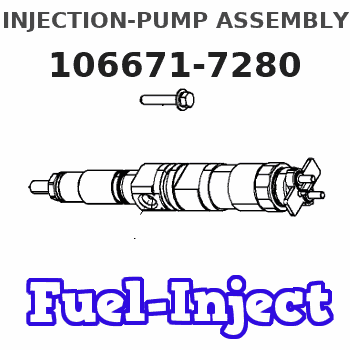
Rating:
Service parts 106671-7280 INJECTION-PUMP ASSEMBLY:
1.
_
7.
COUPLING PLATE
8.
_
9.
_
11.
Nozzle and Holder
ME056357
12.
Open Pre:MPa(Kqf/cm2)
17.7{180}/21.6{220}
15.
NOZZLE SET
Include in #1:
106671-7280
as INJECTION-PUMP ASSEMBLY
Cross reference number
ZEXEL
106671-7280
1066717280
Zexel num
Bosch num
Firm num
Name
Calibration Data:
Adjustment conditions
Test oil
1404 Test oil ISO4113 or {SAEJ967d}
1404 Test oil ISO4113 or {SAEJ967d}
Test oil temperature
degC
40
40
45
Nozzle and nozzle holder
105780-8140
Bosch type code
EF8511/9A
Nozzle
105780-0000
Bosch type code
DN12SD12T
Nozzle holder
105780-2080
Bosch type code
EF8511/9
Opening pressure
MPa
17.2
Opening pressure
kgf/cm2
175
Injection pipe
Outer diameter - inner diameter - length (mm) mm 8-3-600
Outer diameter - inner diameter - length (mm) mm 8-3-600
Overflow valve
131424-4620
Overflow valve opening pressure
kPa
255
221
289
Overflow valve opening pressure
kgf/cm2
2.6
2.25
2.95
Tester oil delivery pressure
kPa
157
157
157
Tester oil delivery pressure
kgf/cm2
1.6
1.6
1.6
Direction of rotation (viewed from drive side)
Right R
Right R
Injection timing adjustment
Direction of rotation (viewed from drive side)
Right R
Right R
Injection order
1-5-3-6-
2-4
Pre-stroke
mm
4.8
4.75
4.85
Beginning of injection position
Governor side NO.1
Governor side NO.1
Difference between angles 1
Cal 1-5 deg. 60 59.5 60.5
Cal 1-5 deg. 60 59.5 60.5
Difference between angles 2
Cal 1-3 deg. 120 119.5 120.5
Cal 1-3 deg. 120 119.5 120.5
Difference between angles 3
Cal 1-6 deg. 180 179.5 180.5
Cal 1-6 deg. 180 179.5 180.5
Difference between angles 4
Cyl.1-2 deg. 240 239.5 240.5
Cyl.1-2 deg. 240 239.5 240.5
Difference between angles 5
Cal 1-4 deg. 300 299.5 300.5
Cal 1-4 deg. 300 299.5 300.5
Injection quantity adjustment
Adjusting point
-
Rack position
9.4
Pump speed
r/min
700
700
700
Each cylinder's injection qty
mm3/st.
144
140.5
147.5
Basic
*
Fixing the rack
*
Standard for adjustment of the maximum variation between cylinders
*
Injection quantity adjustment_02
Adjusting point
F
Rack position
5+-0.5
Pump speed
r/min
500
500
500
Each cylinder's injection qty
mm3/st.
16.5
14
19
Fixing the rack
*
Standard for adjustment of the maximum variation between cylinders
*
Injection quantity adjustment_03
Adjusting point
A
Rack position
R1(9.4)
Pump speed
r/min
700
700
700
Average injection quantity
mm3/st.
144
143
145
Basic
*
Fixing the lever
*
Boost pressure
kPa
48.7
48.7
Boost pressure
mmHg
365
365
Injection quantity adjustment_04
Adjusting point
B
Rack position
R1(9.4)
Pump speed
r/min
1100
1100
1100
Average injection quantity
mm3/st.
152.8
149.6
156
Difference in delivery
mm3/st.
6.4
6.4
6.4
Fixing the lever
*
Boost pressure
kPa
48.7
48.7
Boost pressure
mmHg
365
365
Injection quantity adjustment_05
Adjusting point
D
Rack position
9.3
Pump speed
r/min
500
500
500
Average injection quantity
mm3/st.
139.5
135.5
143.5
Fixing the lever
*
Boost pressure
kPa
32.7
32.7
32.7
Boost pressure
mmHg
245
245
245
Injection quantity adjustment_06
Adjusting point
C
Rack position
5.7+-0.5
Pump speed
r/min
225
225
225
Each cylinder's injection qty
mm3/st.
16.5
14
19
Fixing the rack
*
Boost pressure
kPa
0
0
0
Boost pressure
mmHg
0
0
0
Remarks
(check)
(check)
Injection quantity adjustment_07
Adjusting point
E
Rack position
-
Pump speed
r/min
100
100
100
Average injection quantity
mm3/st.
125
105
145
Fixing the lever
*
Boost pressure
kPa
0
0
0
Boost pressure
mmHg
0
0
0
Boost compensator adjustment
Pump speed
r/min
600
600
600
Rack position
7.9
Boost pressure
kPa
6
6
6
Boost pressure
mmHg
45
45
45
Boost compensator adjustment_02
Pump speed
r/min
600
600
600
Rack position
8.6
Boost pressure
kPa
19.3
12.6
26
Boost pressure
mmHg
145
95
195
Boost compensator adjustment_03
Pump speed
r/min
600
600
600
Rack position
9.3
Boost pressure
kPa
32.7
31.4
34
Boost pressure
mmHg
245
235
255
Boost compensator adjustment_04
Pump speed
r/min
600
600
600
Rack position
R1(9.4)
Boost pressure
kPa
35.3
35.3
35.3
Boost pressure
mmHg
265
265
265
Test data Ex:
Governor adjustment
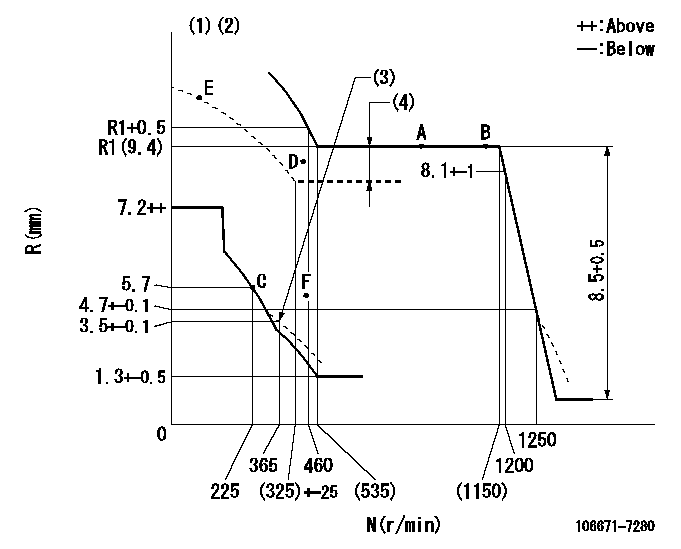
N:Pump speed
R:Rack position (mm)
(1)Tolerance for racks not indicated: +-0.05mm.
(2)Boost compensator cancel stroke: BSL
(3)Damper spring setting
(4)Boost compensator stroke: BCL
----------
BSL=2.2mm BCL=1.5+-0.1mm
----------
----------
BSL=2.2mm BCL=1.5+-0.1mm
----------
Timer adjustment

(1)Adjusting range
(2)Step response time
(N): Speed of the pump
(L): Load
(theta) Advance angle
(Srd1) Step response time 1
(Srd2) Step response time 2
1. Adjusting conditions for the variable timer
(1)Adjust the clearance between the pickup and the protrusion to L.
----------
L=1-0.2mm N2=800r/min C2=(8.8deg) t1=2.5--sec. t2=2.5--sec.
----------
N1=750++r/min P1=0kPa(0kgf/cm2) P2=392kPa(4kgf/cm2) C1=8.8+-0.3deg R01=0/4load R02=4/4load
----------
L=1-0.2mm N2=800r/min C2=(8.8deg) t1=2.5--sec. t2=2.5--sec.
----------
N1=750++r/min P1=0kPa(0kgf/cm2) P2=392kPa(4kgf/cm2) C1=8.8+-0.3deg R01=0/4load R02=4/4load
Speed control lever angle

F:Full speed
----------
----------
a=18deg+-5deg
----------
----------
a=18deg+-5deg
0000000901

F:Full load
I:Idle
(1)Stopper bolt setting
----------
----------
a=28deg+-5deg b=30deg+-3deg
----------
----------
a=28deg+-5deg b=30deg+-3deg
Stop lever angle

N:Engine manufacturer's normal use
S:Stop the pump.
(1)Rack position = aa
(2)Stopper bolt setting
(3)Rack position bb
(4)Free (at shipping)
----------
aa=4.1-0.5mm bb=13.3mm
----------
a=26deg+-5deg b=(38deg) c=0deg+7deg-5deg
----------
aa=4.1-0.5mm bb=13.3mm
----------
a=26deg+-5deg b=(38deg) c=0deg+7deg-5deg
0000001501 RACK SENSOR

V1:Supply voltage
V2f:Full side output voltage
V2i:Idle side output voltage
(A) Black
(B) Yellow
(C) Red
(D) Trimmer
(E): Shaft
(F) Nut
(G) Load lever
1. Load sensor adjustment
(1)Connect as shown in the above diagram and apply supply voltage V1.
(2)Hold the load lever (G) against the full side.
(3)Turn the shaft so that the voltage between (A) and (B) is V2.
(4)Hold the load lever (G) against the idle side.
(5)Adjust (D) so that the voltage between (A) and (B) is V2i.
(6)Repeat the above adjustments.
(7)Tighten the nut (F) at the point satisfying the standards.
(8)Hold the load lever against the full side stopper and the idle side stopper.
(9)At this time, confirm that the full side output voltage is V2f and the idle side output voltage is V2i.
----------
V1= 5+-0.02V V2f=0.15+0.03V V2i=2.35-0.03V
----------
----------
V1= 5+-0.02V V2f=0.15+0.03V V2i=2.35-0.03V
----------
0000001601 MICRO SWITCH
Adjustment of the micro-switch
Adjust the bolt to obtain the following lever position when the micro-switch is ON.
(1)Speed N1
(2)Rack position Ra
----------
N1=325r/min Ra=5.4+-0.1mm
----------
----------
N1=325r/min Ra=5.4+-0.1mm
----------
Timing setting

(1)Pump vertical direction
(2)Coupling's key groove position at No 1 cylinder's beginning of injection
(3)-
(4)-
----------
----------
a=(7deg)
----------
----------
a=(7deg)
Information:
- Generator Monitoring SystemI/O - Input/OutputMMS - Marine Monitoring SystemMMS II - Marine Monitoring System IIPLC - Programmable Logic ControllerThe 203-7811 Engine Monitoring Control Group is the service replacement for the 146-3117 Monitoring Control and the 162-1662 Monitoring Control that are used in MMS. The 203-7811 Engine Monitoring Control Group uses Wonderware as the "Graphic Display Application".The 203-7810 Engine Monitoring Control Group is the optional monitor that is used in the MMS II and the GMS. The 203-7810 Engine Monitoring Control Group uses the RSView as the "Graphic Display Application".When these engine monitoring control groups are used as service replacements in the field, use the procedure that follows to register the software to the user. This procedure can be done when the engine monitoring control group is connected to the PLC. This procedure can also be done when the engine monitoring control group is not connected to the PLC.
Connect a keyboard that is compatible with the PS/2 style of connector. Connect electrical power to the monitor.
Turn on the power.
When you are prompted, accept the license agreement. Press the "Next" button.
Enter the Microsoft Windows NT product identification number. This number is located on the right side of the computer. Press "Next".
When the message indicates that the system could not complete the login, select "OK".
Input "Administrator" for the login username. Input "3600" for the login password.
After a successful login as "Administrator", do one of the items that follow:
Restart the computer.
Close all of the programs and use a different login username.
When the message indicates that the system could not complete the login, select "OK".
Input "Operator" for the login username. Input "password" for the login password.
After a successful login as "Operator", one of the items that follow will occur:
If a 203-7811 Engine Monitoring Control Group is used, the Wonderware I/O Server and the Window Viewer will be started.
If a 203-7810 Engine Monitoring Control Group is used, the RSView Runtime will be started.
Remove the keyboard. The setup is complete.In applications that use Wonderware or RSView, the engine monitoring control group must be connected to the PLC in order for the data to be displayed.After a successful login to the "Operator" account, the computer will automatically start and the computer will start the application in the "Operator" account. The automatic start-up can be bypassed by doing the operations that follow:
Attach a keyboard.
Hold the "shift" key in the down position while the start-up of the computer is initiated.
Connect a keyboard that is compatible with the PS/2 style of connector. Connect electrical power to the monitor.
Turn on the power.
When you are prompted, accept the license agreement. Press the "Next" button.
Enter the Microsoft Windows NT product identification number. This number is located on the right side of the computer. Press "Next".
When the message indicates that the system could not complete the login, select "OK".
Input "Administrator" for the login username. Input "3600" for the login password.
After a successful login as "Administrator", do one of the items that follow:
Restart the computer.
Close all of the programs and use a different login username.
When the message indicates that the system could not complete the login, select "OK".
Input "Operator" for the login username. Input "password" for the login password.
After a successful login as "Operator", one of the items that follow will occur:
If a 203-7811 Engine Monitoring Control Group is used, the Wonderware I/O Server and the Window Viewer will be started.
If a 203-7810 Engine Monitoring Control Group is used, the RSView Runtime will be started.
Remove the keyboard. The setup is complete.In applications that use Wonderware or RSView, the engine monitoring control group must be connected to the PLC in order for the data to be displayed.After a successful login to the "Operator" account, the computer will automatically start and the computer will start the application in the "Operator" account. The automatic start-up can be bypassed by doing the operations that follow:
Attach a keyboard.
Hold the "shift" key in the down position while the start-up of the computer is initiated.