Information injection-pump assembly
ZEXEL
106671-7270
1066717270
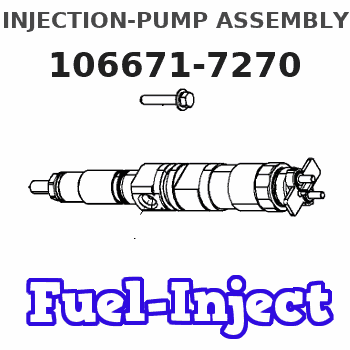
Rating:
Cross reference number
ZEXEL
106671-7270
1066717270
Zexel num
Bosch num
Firm num
Name
Calibration Data:
Adjustment conditions
Test oil
1404 Test oil ISO4113 or {SAEJ967d}
1404 Test oil ISO4113 or {SAEJ967d}
Test oil temperature
degC
40
40
45
Nozzle and nozzle holder
105780-8140
Bosch type code
EF8511/9A
Nozzle
105780-0000
Bosch type code
DN12SD12T
Nozzle holder
105780-2080
Bosch type code
EF8511/9
Opening pressure
MPa
17.2
Opening pressure
kgf/cm2
175
Injection pipe
Outer diameter - inner diameter - length (mm) mm 8-3-600
Outer diameter - inner diameter - length (mm) mm 8-3-600
Overflow valve
131424-4620
Overflow valve opening pressure
kPa
255
221
289
Overflow valve opening pressure
kgf/cm2
2.6
2.25
2.95
Tester oil delivery pressure
kPa
157
157
157
Tester oil delivery pressure
kgf/cm2
1.6
1.6
1.6
Direction of rotation (viewed from drive side)
Right R
Right R
Injection timing adjustment
Direction of rotation (viewed from drive side)
Right R
Right R
Injection order
1-5-3-6-
2-4
Pre-stroke
mm
4.8
4.75
4.85
Beginning of injection position
Governor side NO.1
Governor side NO.1
Difference between angles 1
Cal 1-5 deg. 60 59.5 60.5
Cal 1-5 deg. 60 59.5 60.5
Difference between angles 2
Cal 1-3 deg. 120 119.5 120.5
Cal 1-3 deg. 120 119.5 120.5
Difference between angles 3
Cal 1-6 deg. 180 179.5 180.5
Cal 1-6 deg. 180 179.5 180.5
Difference between angles 4
Cyl.1-2 deg. 240 239.5 240.5
Cyl.1-2 deg. 240 239.5 240.5
Difference between angles 5
Cal 1-4 deg. 300 299.5 300.5
Cal 1-4 deg. 300 299.5 300.5
Injection quantity adjustment
Adjusting point
-
Rack position
9.4
Pump speed
r/min
700
700
700
Each cylinder's injection qty
mm3/st.
144
140.5
147.5
Basic
*
Fixing the rack
*
Standard for adjustment of the maximum variation between cylinders
*
Injection quantity adjustment_02
Adjusting point
F
Rack position
5+-0.5
Pump speed
r/min
500
500
500
Each cylinder's injection qty
mm3/st.
16.5
14
19
Fixing the rack
*
Standard for adjustment of the maximum variation between cylinders
*
Injection quantity adjustment_03
Adjusting point
A
Rack position
R1(9.4)
Pump speed
r/min
700
700
700
Average injection quantity
mm3/st.
144
143
145
Basic
*
Fixing the lever
*
Boost pressure
kPa
48.7
48.7
Boost pressure
mmHg
365
365
Injection quantity adjustment_04
Adjusting point
B
Rack position
R1(9.4)
Pump speed
r/min
1100
1100
1100
Average injection quantity
mm3/st.
152.8
149.6
156
Difference in delivery
mm3/st.
6.4
6.4
6.4
Fixing the lever
*
Boost pressure
kPa
48.7
48.7
Boost pressure
mmHg
365
365
Injection quantity adjustment_05
Adjusting point
D
Rack position
9.3
Pump speed
r/min
500
500
500
Average injection quantity
mm3/st.
139.5
135.5
143.5
Fixing the lever
*
Boost pressure
kPa
32.7
32.7
32.7
Boost pressure
mmHg
245
245
245
Injection quantity adjustment_06
Adjusting point
C
Rack position
5.7+-0.5
Pump speed
r/min
300
300
300
Each cylinder's injection qty
mm3/st.
16.5
14
19
Fixing the rack
*
Boost pressure
kPa
0
0
0
Boost pressure
mmHg
0
0
0
Remarks
(check)
(check)
Injection quantity adjustment_07
Adjusting point
E
Rack position
-
Pump speed
r/min
100
100
100
Average injection quantity
mm3/st.
115
95
135
Fixing the lever
*
Boost pressure
kPa
0
0
0
Boost pressure
mmHg
0
0
0
Boost compensator adjustment
Pump speed
r/min
600
600
600
Rack position
7.9
Boost pressure
kPa
6
6
6
Boost pressure
mmHg
45
45
45
Boost compensator adjustment_02
Pump speed
r/min
600
600
600
Rack position
8.6
Boost pressure
kPa
19.3
12.6
26
Boost pressure
mmHg
145
95
195
Boost compensator adjustment_03
Pump speed
r/min
600
600
600
Rack position
9.3
Boost pressure
kPa
32.7
31.4
34
Boost pressure
mmHg
245
235
255
Boost compensator adjustment_04
Pump speed
r/min
600
600
600
Rack position
R1(9.4)
Boost pressure
kPa
35.3
35.3
35.3
Boost pressure
mmHg
265
265
265
Timer adjustment
Pump speed
r/min
450--
Advance angle
deg.
0
0
0
Remarks
Start
Start
Timer adjustment_02
Pump speed
r/min
400
Advance angle
deg.
0.5
Timer adjustment_03
Pump speed
r/min
800
Advance angle
deg.
3
2.5
3.5
Remarks
Finish
Finish
Test data Ex:
Governor adjustment
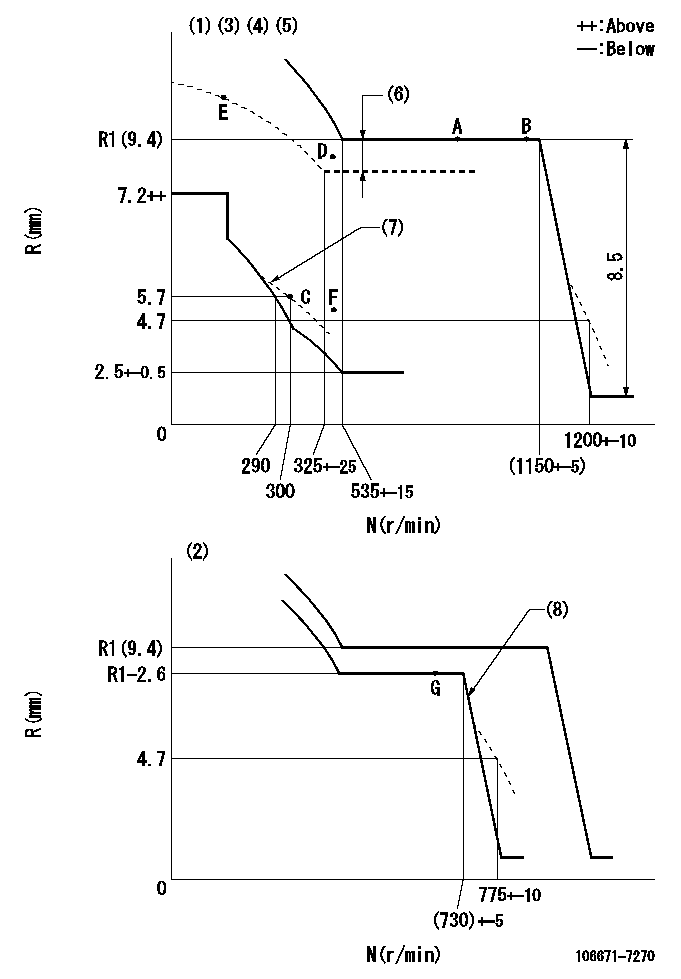
N:Pump speed
R:Rack position (mm)
(1)Adjust with speed control lever at full position (minimum-maximum speed specification)
(2)Adjust with the load control lever in the full position (variable speed specification).
(3)Lever ratio: RT
(4)Target shim dimension: TH
(5)Boost compensator cancel stroke: BSL
(6)Boost compensator stroke: BCL
(7)Damper spring setting: DL
(8)When air cylinder is operating.
----------
RT=1 TH=2.5mm BSL=2.2mm BCL=1.5+-0.1mm DL=6.2-0.2mm
----------
----------
RT=1 TH=2.5mm BSL=2.2mm BCL=1.5+-0.1mm DL=6.2-0.2mm
----------
Speed control lever angle
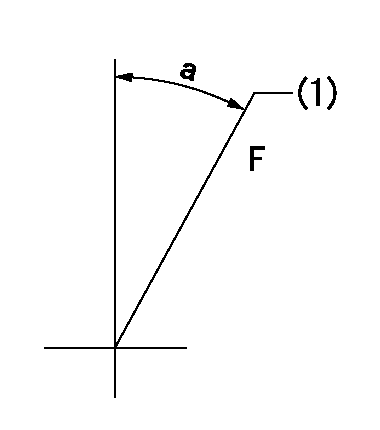
F:Full speed
(1)Pump speed = aa
----------
aa=1150r/min
----------
a=(17deg)+-5deg
----------
aa=1150r/min
----------
a=(17deg)+-5deg
0000000901
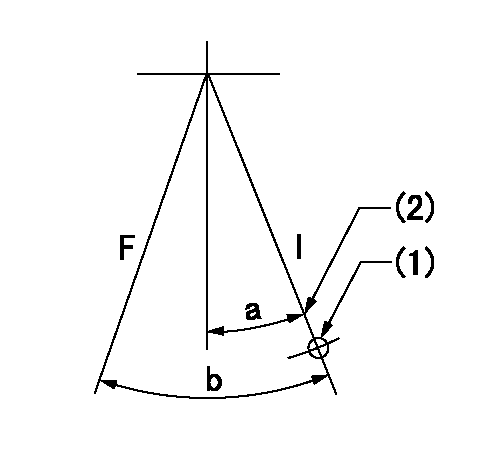
F:Full load
I:Idle
(1)Use the hole at R = aa
(2)Stopper bolt setting
----------
aa=51mm
----------
a=25deg+-5deg b=26.5deg+-3deg
----------
aa=51mm
----------
a=25deg+-5deg b=26.5deg+-3deg
Stop lever angle

N:Engine manufacturer's normal use
S:Stop the pump.
(1)Rack position = aa
(2)Stopper bolt setting
(3)Rack position bb
(4)Free (at shipping)
----------
aa=4.1-0.5mm bb=13.3mm
----------
a=45deg+5deg-7deg b=26deg+-5deg c=(83deg)
----------
aa=4.1-0.5mm bb=13.3mm
----------
a=45deg+5deg-7deg b=26deg+-5deg c=(83deg)
0000001501 MICRO SWITCH
Adjustment of the micro-switch
Adjust the bolt to obtain the following lever position when the micro-switch is ON.
(1)Speed N1
(2)Rack position Ra
----------
N1=400+-5r/min Ra=5.4mm
----------
----------
N1=400+-5r/min Ra=5.4mm
----------
0000001601 2-STAGE CHANGEOVER DEVICE

RFD governor 2 stage changeover mechanism adjustment outline
(A) Bolt
(B) bolt
(c) Nut
(D) Return spring
(E) Bolt
(F) Bolt
(G) Screw
(H) Bolt
(I) Load lever
(J) Speed lever
(K) Air cylinder
(M Air inlet
Figure 1 is only for reference. Lever shape, etc, may vary.
1. Minimum-maximum speed specification adjustment (when running)
(a) Without applying air to the air cylinder, loosen bolts (A) and (B).
(1)High speed return L setting
(a) In the speed range Nf~Nf - 300r/min, adjust using the speed adjusting bolt to determine the temporary beginning of high speed control speed.
(b) Determine the rack position in the vicinity of Rf using the full load lever.
(c) Increase speed and confirm return distance L.
(d) Adjust using the tension lever bolt to obtain L.
(2)Setting full load rack position Rf
(a) Move the load control lever to the full side.
(b) Adjust the full load adjusting bolt so that Rf can be obtained, then fix.
(3)Setting the beginning of high speed operation Nf
(a) Adjust using bolt (E) so that Nf can be obtained, and then fix.
(4)Idle control setting (Re, Ni, Rc)
(a) Set the speed at Ns + 200r/min and move the load control lever to the idle side.
(b) Fix the lever in the position where Re can be obtained.
(c) Next, decrease speed to Ni and screw in the idle spring.
(d) Adjust to obtain rack position Ri.
(e) Increase the speed and after confirming that the rack position is Re at Ns, set the speed at 0.
(f) Confirm protrusion position Rc at idle.
(5)Damper spring adjustment
(a) Increase speed and set the speed at the rack position Rd - 0.1 mm
(b) Set using the damper spring so that the rack position Rd can be obtained.
(c) When Rd is not specified, Rd = Ri - 0.5 mm.
(6)High speed droop confirmation
(a) Return the load control lever to the full load lever position.
(b) Increase the speed and confirm that Rf can be obtained at Nf r/min.
(c) Confirm that speed is Nh at rack position Rh.
2. Variable speed specification adjustment (at operation)
(a) Remove return spring (D).
(b) Apply air pressure of 245~294 kPa {2.5~3 kg/cm2} to the air cylinder.
(c) Perform the following adjustment in this condition.
(1)Setting full load rack position Rf'
(a) Pull the load lever to the idle side.
(b) Obtain rack position Rf' using the nut (C). (Pump speed is Nf'-50 r/min.)
(2)Setting full speed Nf'
(a) Adjust using bolt (B) so that Nf can be obtained, and then fix.
(3)Low speed side setting
(a) At 350r/min, set bolt (F) at beginning of governor operation position, then fix.
3. Bolt (A) adjustment
(1)Install return spring (D) and perform the adjustments below at air pressure 0.
(a) Set at speed Nf using bolt (E).
(b) Screw in bolt (A).
(c) Screw in 1 more turn from the speed lever contact position
(d) Fix bolt (A).
(e) At this time confirm that the air cylinder's shaft moves approximately 1 mm towards the governor.
4. Lever operation confirmation using the air cylinder
(1)Apply 588 kPa {6 kg/cm2} air pressure to the air cylinder.
(2)Confirm that the cylinder piston is moved 50 mm by the spring (D).
----------
----------
----------
----------
Timing setting

(1)Pump vertical direction
(2)Coupling's key groove position at No 1 cylinder's beginning of injection
(3)-
(4)-
----------
----------
a=(7deg)
----------
----------
a=(7deg)
Information:
Disconnect all electrical power from the panel before making a panel cutout. Make sure the area around the panel cutout is clear. Take precautions to prevent metal cuttings from entering any components that are already installed in the panel. Failure to follow these instructions may result in personal injury or damage to the panel components.
Environmental Considerations
Mount the monitor in a panel or in an enclosure in order to protect the internal circuitry.Provide adequate ventilation in the enclosure. Also, consider heat produced by other devices in the enclosure. The ambient temperature around the monitor must be maintained between 5 °C (41 °F) and 50 °C (122 °F). Make sure that you provide provisions for accessing the back panel and side panels of the monitor. Installing components and removing components requires access to the panels. The floppy disk drive is also accessed through the panels. Refer to Illustration 1.
Illustration 1 g00857541
Mounting ClearancesNote: The dimensions in Illustration 1 are only applicable if the monitor has adequate ventilation. Cooling methods must be used in order to lower air temperature within the enclosure.Mounting Hardware
Table 1
Item    Description    Quantity    Use For    
Self-locking nuts     #10-32     10 (8 required)     Panel or enclosure mounting    In addition to the tools that are required in order to make the cut for the panel, you will need the following tools:
Drill
9.525 mm (3/8 inch) socket
15 cm (6 inch) extension rod (minimum)
Socket driver (in/lb. torque wrench recommended)
RulerPanel Mounting
In order to install the monitor in a panel, perform the following procedure:
Cut an opening in the panel by using the dimensions that are provided. Drill eight 6.4 mm (0.25 inch) holes for the mounting studs. Refer to Installation, "Dimensions" for more information.
Make sure that the sealing gasket is properly positioned on the terminal. This gasket forms a compression seal. Do not use sealing compounds.
Place the monitor in the opening in the panel. Align the studs with the mounting holes.
Install the eight self-locking nuts. Hand tighten the self-locking nuts.
Illustration 2 g00857579
Torque Sequence
Alternately tighten the self-locking nuts with the 9.525 mm (3/8 inch) socket. Tighten the nuts until the monitor is held firmly against the panel. The amount of torque that is required increases significantly as the gasket reaches the proper compression. Tighten the nuts to a torque of 2.7 N m (24 lb in). Refer to Illustration 2 for the recommended tightening sequence.Note: Tighten the nuts to a torque of 2.7 N m (24 lb in) in order to provide a proper seal and prevent damage to the monitor.