Information injection-pump assembly
BOSCH
9 400 616 924
9400616924
ZEXEL
106671-7030
1066717030
MITSUBISHI
ME056462
me056462
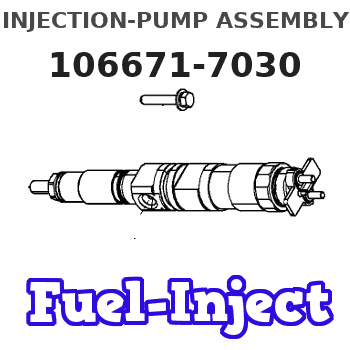
Rating:
Service parts 106671-7030 INJECTION-PUMP ASSEMBLY:
1.
_
7.
COUPLING PLATE
8.
_
9.
_
11.
Nozzle and Holder
ME056329
12.
Open Pre:MPa(Kqf/cm2)
17.7{180}/21.6{220}
15.
NOZZLE SET
Include in #1:
106671-7030
as INJECTION-PUMP ASSEMBLY
Cross reference number
BOSCH
9 400 616 924
9400616924
ZEXEL
106671-7030
1066717030
MITSUBISHI
ME056462
me056462
Zexel num
Bosch num
Firm num
Name
Calibration Data:
Adjustment conditions
Test oil
1404 Test oil ISO4113 or {SAEJ967d}
1404 Test oil ISO4113 or {SAEJ967d}
Test oil temperature
degC
40
40
45
Nozzle and nozzle holder
105780-8140
Bosch type code
EF8511/9A
Nozzle
105780-0000
Bosch type code
DN12SD12T
Nozzle holder
105780-2080
Bosch type code
EF8511/9
Opening pressure
MPa
17.2
Opening pressure
kgf/cm2
175
Injection pipe
Outer diameter - inner diameter - length (mm) mm 8-3-600
Outer diameter - inner diameter - length (mm) mm 8-3-600
Overflow valve
131424-4620
Overflow valve opening pressure
kPa
255
221
289
Overflow valve opening pressure
kgf/cm2
2.6
2.25
2.95
Tester oil delivery pressure
kPa
157
157
157
Tester oil delivery pressure
kgf/cm2
1.6
1.6
1.6
Direction of rotation (viewed from drive side)
Right R
Right R
Injection timing adjustment
Direction of rotation (viewed from drive side)
Right R
Right R
Injection order
1-5-3-6-
2-4
Pre-stroke
mm
4.8
4.75
4.85
Beginning of injection position
Governor side NO.1
Governor side NO.1
Difference between angles 1
Cal 1-5 deg. 60 59.5 60.5
Cal 1-5 deg. 60 59.5 60.5
Difference between angles 2
Cal 1-3 deg. 120 119.5 120.5
Cal 1-3 deg. 120 119.5 120.5
Difference between angles 3
Cal 1-6 deg. 180 179.5 180.5
Cal 1-6 deg. 180 179.5 180.5
Difference between angles 4
Cyl.1-2 deg. 240 239.5 240.5
Cyl.1-2 deg. 240 239.5 240.5
Difference between angles 5
Cal 1-4 deg. 300 299.5 300.5
Cal 1-4 deg. 300 299.5 300.5
Injection quantity adjustment
Adjusting point
-
Rack position
7.9
Pump speed
r/min
700
700
700
Each cylinder's injection qty
mm3/st.
104
101.4
106.6
Basic
*
Fixing the rack
*
Standard for adjustment of the maximum variation between cylinders
*
Injection quantity adjustment_02
Adjusting point
F
Rack position
5+-0.5
Pump speed
r/min
500
500
500
Each cylinder's injection qty
mm3/st.
16.5
14
19
Fixing the rack
*
Standard for adjustment of the maximum variation between cylinders
*
Injection quantity adjustment_03
Adjusting point
A
Rack position
R1(7.9)
Pump speed
r/min
700
700
700
Average injection quantity
mm3/st.
104
103
105
Basic
*
Fixing the lever
*
Injection quantity adjustment_04
Adjusting point
B
Rack position
R1(7.9)
Pump speed
r/min
1100
1100
1100
Average injection quantity
mm3/st.
118
114
122
Difference in delivery
mm3/st.
8
8
8
Fixing the lever
*
Injection quantity adjustment_05
Adjusting point
C
Rack position
5.7+-0.5
Pump speed
r/min
225
225
225
Each cylinder's injection qty
mm3/st.
16.5
14
19
Fixing the rack
*
Remarks
(check)
(check)
Injection quantity adjustment_06
Adjusting point
E
Rack position
-
Pump speed
r/min
100
100
100
Average injection quantity
mm3/st.
150
130
170
Fixing the lever
*
Timer adjustment
Pump speed
r/min
950
Advance angle
deg.
0.5
Timer adjustment_02
Pump speed
r/min
1050
Advance angle
deg.
2.2
1.7
2.7
Timer adjustment_03
Pump speed
r/min
1150
Advance angle
deg.
5.5
5
6
Remarks
Finish
Finish
Test data Ex:
Governor adjustment

N:Pump speed
R:Rack position (mm)
(1)Lever ratio: RT
(2)Target shim dimension: TH
(3)Damper spring setting: DL
(4)Excess fuel setting for starting: SXL
----------
RT=1 TH=2.6mm DL=4.5-0.2mm SXL=R1+0.2mm
----------
----------
RT=1 TH=2.6mm DL=4.5-0.2mm SXL=R1+0.2mm
----------
Speed control lever angle

F:Full speed
----------
----------
a=27deg+-5deg
----------
----------
a=27deg+-5deg
0000000901

F:Full load
I:Idle
(1)Stopper bolt setting
----------
----------
a=23deg+-3deg b=24deg+-5deg
----------
----------
a=23deg+-3deg b=24deg+-5deg
Stop lever angle

N:Pump normal
S:Stop the pump.
(1)Rack position = aa
(2)Set stopper bolt so that rack position = bb.
(3)Free (at shipping)
----------
aa=16.6mm bb=4.1-0.5mm
----------
a=35deg+-5deg b=61.5deg+7deg-5deg c=(6deg)
----------
aa=16.6mm bb=4.1-0.5mm
----------
a=35deg+-5deg b=61.5deg+7deg-5deg c=(6deg)
0000001501 MICRO SWITCH
Adjustment of the micro-switch
Adjust the bolt to obtain the following lever position when the micro-switch is ON.
(1)Speed N1
(2)Rack position Ra
----------
N1=325+-5r/min Ra=5.4mm
----------
----------
N1=325+-5r/min Ra=5.4mm
----------
Timing setting

(1)Pump vertical direction
(2)Coupling's key groove position at No 1 cylinder's beginning of injection
(3)-
(4)-
----------
----------
a=(7deg)
----------
----------
a=(7deg)
Information:
Version C of the ADEM II controller (ECM) has a primary data link for use with the CCM. This data link is called the CAT Data Link. The Module Identifier (MID) of this controller is a fixed value. Each controller on the CAT Data Link must have a unique MID. The CCM can only be connected to one Version C ECM on the CAT Data Link.
Version D of the ADEM II controller (ECM) also has a primary data link for use with the CCM. The value of the MID for the primary data link is fixed. Version D also has a secondary data link for use with the CCM. The Secondary CAT Data Link has a programmable MID. A maximum of eight different values is available for generator set applications. A maximum of three different values is available for marine applications.
EMCP II (basic model) has a primary data link for use with the CCM. This data link is called the CAT Data Link. The CAT Data Link has a programmable MID. A maximum of eight different values may be used for the MID.
EMCP II+ has the same primary data link as EMCP II (CAT Data Link) with a programmable value for the MID. The EMCP II+ also has a secondary data link for use with the CCM. The CCM Data Link has a programmable value for the MID. The CAT Data Link and the CCM Data Link have eight MID values.
The Secondary CAT Data Link and the CCM Data Link can be treated in the same manner on the 3500B Version D and the EMCP II+ applications.
There is a maximum of one CCM per data link.
There is a maximum of one CCM per engine.The previous descriptions govern the connections between the devices and the CCM. When an ADEM II controller and an EMCP II or EMCP II+ controller are connected, the CAT Data Link is always used for the connections. All subsequent connections to the CCM (ADEM II Version D or EMCP II+) are made by using the secondary data link. The following examples will illustrate some valid CCM connections with multiple electronic controllers. These examples are only a representation of most possible valid connections or combinations.
Illustration 1 g00649118
MUI Generator sets with EMCP II (Basic Model)
Illustration 2 g00649133
MUI Generator sets with EMCP II+
Illustration 3 g00649182
3500B EUI Generator set (Version C ECM)
Illustration 4 g00649184
3500 B EUI Generator sets (Version D ECM)
Illustration 5 g00649192
3500B EUI Generator sets (Version C and D ECM's)For the application that is shown in Illustration 5, only one Version C ECM is allowed.
Illustration 6 g00649200
3500B EUI Generator set (Version C ECM) with EMCP II (Basic Model)
Illustration 7 g00649317
EMCP II Basic and 3500B EUI Generator set (Version D ECM)One CCM is required for each engine with Version D ECM.
Illustration 8 g00649214
3500B EUI Generator sets (Version C ECM) with EMCP II+
Illustration 9 g00649236
3500B EUI Generator sets (Version D ECM) with EMCP II+
Illustration 10 g00649243
3500B EUI Generator sets (Version D ECM) with EMCP II+A maximum of four generator sets can be connected in the application that is shown in