Information injection-pump assembly
ZEXEL
106671-6360
1066716360
ISUZU
1156032460
1156032460
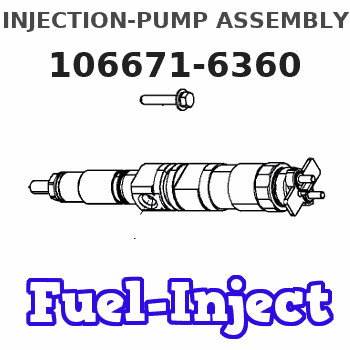
Rating:
Service parts 106671-6360 INJECTION-PUMP ASSEMBLY:
1.
_
7.
COUPLING PLATE
8.
_
9.
_
11.
Nozzle and Holder
1-15300-332-0
12.
Open Pre:MPa(Kqf/cm2)
17.7{180}/22.1{225}
15.
NOZZLE SET
Include in #1:
106671-6360
as INJECTION-PUMP ASSEMBLY
Cross reference number
ZEXEL
106671-6360
1066716360
ISUZU
1156032460
1156032460
Zexel num
Bosch num
Firm num
Name
Calibration Data:
Adjustment conditions
Test oil
1404 Test oil ISO4113 or {SAEJ967d}
1404 Test oil ISO4113 or {SAEJ967d}
Test oil temperature
degC
40
40
45
Nozzle and nozzle holder
105780-8140
Bosch type code
EF8511/9A
Nozzle
105780-0000
Bosch type code
DN12SD12T
Nozzle holder
105780-2080
Bosch type code
EF8511/9
Opening pressure
MPa
17.2
Opening pressure
kgf/cm2
175
Injection pipe
Outer diameter - inner diameter - length (mm) mm 8-3-600
Outer diameter - inner diameter - length (mm) mm 8-3-600
Overflow valve
131424-8620
Overflow valve opening pressure
kPa
206
172
240
Overflow valve opening pressure
kgf/cm2
2.1
1.75
2.45
Tester oil delivery pressure
kPa
157
157
157
Tester oil delivery pressure
kgf/cm2
1.6
1.6
1.6
Direction of rotation (viewed from drive side)
Left L
Left L
Injection timing adjustment
Direction of rotation (viewed from drive side)
Left L
Left L
Injection order
1-5-3-6-
2-4
Pre-stroke
mm
4.5
4.47
4.53
Beginning of injection position
Governor side NO.1
Governor side NO.1
Difference between angles 1
Cal 1-5 deg. 60 59.75 60.25
Cal 1-5 deg. 60 59.75 60.25
Difference between angles 2
Cal 1-3 deg. 120 119.75 120.25
Cal 1-3 deg. 120 119.75 120.25
Difference between angles 3
Cal 1-6 deg. 180 179.75 180.25
Cal 1-6 deg. 180 179.75 180.25
Difference between angles 4
Cyl.1-2 deg. 240 239.75 240.25
Cyl.1-2 deg. 240 239.75 240.25
Difference between angles 5
Cal 1-4 deg. 300 299.75 300.25
Cal 1-4 deg. 300 299.75 300.25
Injection quantity adjustment
Adjusting point
-
Rack position
11.3
Pump speed
r/min
700
700
700
Average injection quantity
mm3/st.
149
147
151
Max. variation between cylinders
%
0
-3
3
Basic
*
Fixing the rack
*
Standard for adjustment of the maximum variation between cylinders
*
Injection quantity adjustment_02
Adjusting point
H
Rack position
6.4+-0.5
Pump speed
r/min
290
290
290
Average injection quantity
mm3/st.
10
6.8
13.2
Max. variation between cylinders
%
0
-13
13
Fixing the rack
*
Standard for adjustment of the maximum variation between cylinders
*
Injection quantity adjustment_03
Adjusting point
A
Rack position
R1(11.3)
Pump speed
r/min
700
700
700
Average injection quantity
mm3/st.
149
147
151
Basic
*
Fixing the lever
*
Boost pressure
kPa
60
60
Boost pressure
mmHg
450
450
Injection quantity adjustment_04
Adjusting point
B
Rack position
R1+0.65
Pump speed
r/min
1100
1100
1100
Average injection quantity
mm3/st.
161
155
167
Fixing the lever
*
Boost pressure
kPa
60
60
Boost pressure
mmHg
450
450
Boost compensator adjustment
Pump speed
r/min
500
500
500
Rack position
R2-1.75
Boost pressure
kPa
4
4
6.7
Boost pressure
mmHg
30
30
50
Boost compensator adjustment_02
Pump speed
r/min
500
500
500
Rack position
R2(R1-0.
45)
Boost pressure
kPa
46.7
46.7
46.7
Boost pressure
mmHg
350
350
350
Timer adjustment
Pump speed
r/min
850--
Advance angle
deg.
0
0
0
Remarks
Start
Start
Timer adjustment_02
Pump speed
r/min
800
Advance angle
deg.
0.5
Timer adjustment_03
Pump speed
r/min
875
Advance angle
deg.
1
0.5
1.5
Remarks
Finish
Finish
Test data Ex:
Governor adjustment
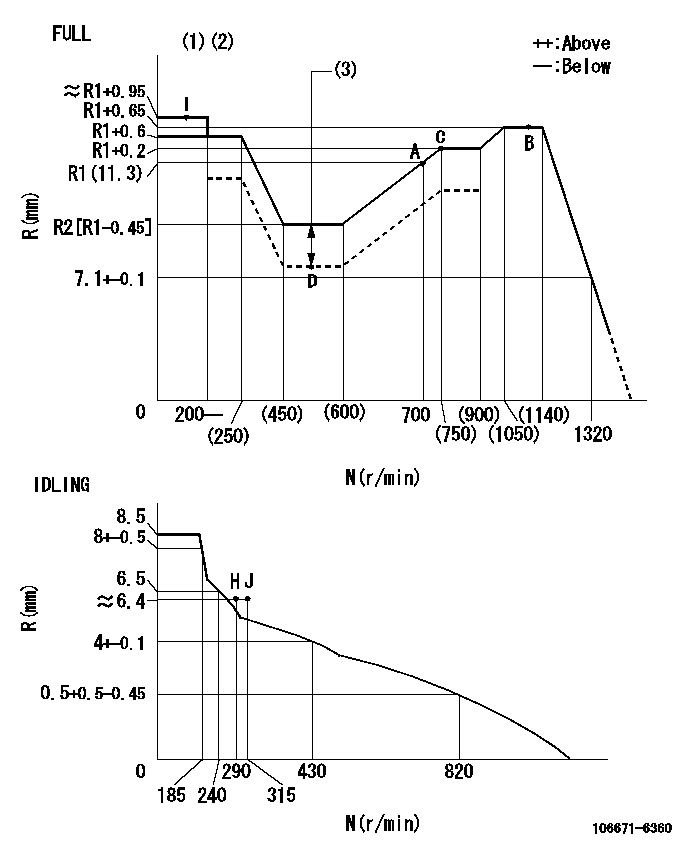
N:Pump speed
R:Rack position (mm)
(1)Torque cam stamping: T1
(2)Tolerance for racks not indicated: +-0.05mm.
(3)Boost compensator stroke: BCL
----------
T1=AE45 BCL=1.75+-0.1mm
----------
----------
T1=AE45 BCL=1.75+-0.1mm
----------
Speed control lever angle
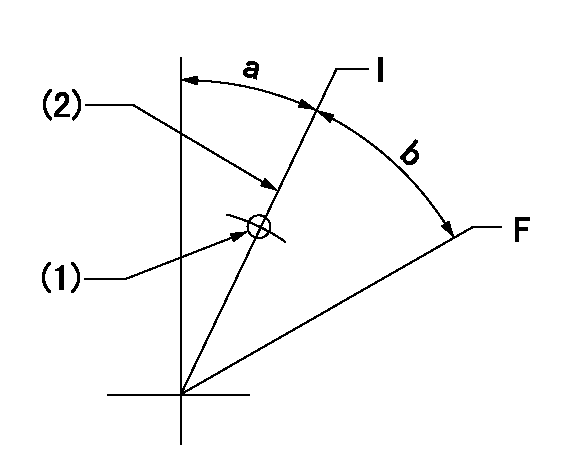
F:Full speed
I:Idle
(1)Use the pin at R = aa
(2)Stopper bolt set position 'H'
----------
aa=35mm
----------
a=27deg+-5deg b=32.5deg+-3deg
----------
aa=35mm
----------
a=27deg+-5deg b=32.5deg+-3deg
Stop lever angle
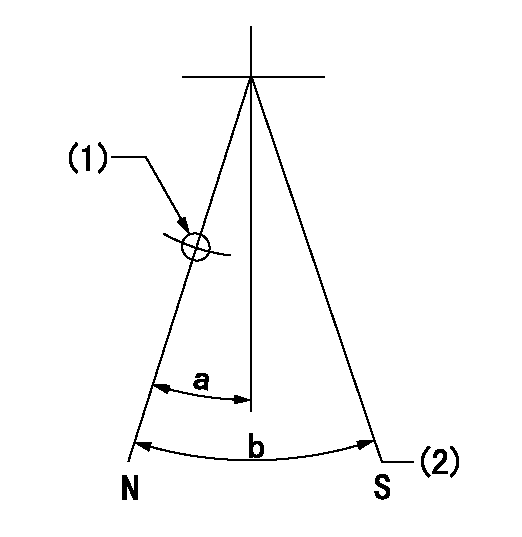
N:Pump normal
S:Stop the pump.
(1)Use the pin at R = aa
(2)Set the stopper bolt so that speed = bb and rack position = cc. (Confirm non-injection.)
----------
aa=40mm bb=0r/min cc=1.5+-0.3mm
----------
a=22deg+-5deg b=41deg+-5deg
----------
aa=40mm bb=0r/min cc=1.5+-0.3mm
----------
a=22deg+-5deg b=41deg+-5deg
Timing setting
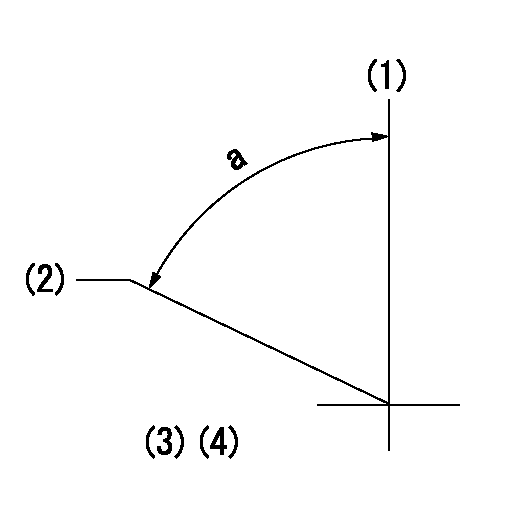
(1)Pump vertical direction
(2)Position of timer's threaded hole at the No. 1 cylinder's beginning of injection
(3)B.T.D.C.: aa
(4)-
----------
aa=14deg
----------
a=(50deg)
----------
aa=14deg
----------
a=(50deg)
Information:
Illustration 39 g00367353
Set the drive speed to "Col 4". Place a straight edge across the opening in the shutdown rod and the shutdown rod nut (F). Use a 7/16 inch open end wrench in order to turn the shutdown rod nut (F) counterclockwise until the governor begins to shut down. Once the governor begins to shut down, turn the nut clockwise one full turn.Adjustment Of The Shutdown Device
Note: The electric shutdown device and the pressure shutdown device should be checked prior to the installation, after the installation, and at 1000 hour intervals thereafter.
Failure to test, inspect and maintain these items could result in faulty operation and possible severe engine damage if an emergency shutdown situation occurs.
The electric shutdown is either an Energize-To-Shutoff (ETS) or an Energize-To-Run (ETR). Identify the type of shutdown device in your governor, and make a note of the type of shutdown device.
Visually inspect the pressure shutdown components for signs of burrs, nicks, scoring and/or wear. Repair the components if evidence of a problem exists. Inspect the pressure shutdown gasket. Determine if the gasket is reusable. If necessary, replace the gasket.
Illustration 40 g00367319
(F) Shutdown Rod Nut. (J) Shutdown Rod. (II) Solenoid. (JJ) Jam Nut. (KK) Set Screw. (LL) Shutdown Plunger. (MM) Solenoid Plunger. (NN) Pivot Pin. (PP) Shutdown Lever.
Visually inspect the electric shutdown device and determine if there is any component wear. If the shutdown is an ETS version, pay particular attention to the connection of the shutdown solenoid's plunger and the shutdown lever's link pin.If there is evidence of wear, replace the solenoid. Inspect the gasket on the electric shutdown. Determine if the gasket is reusable. If necessary, replace the gasket.Check the size of spacer on the solenoid plunger in the electric shutdown. Refer to the Service Magazine Article November 19,, "Field Replacement of Spacer to Correct Possible Sticking in Woodward 3161 Governor Electric Shutoff Group".Adjustment Of The Electric Shutdown Solenoid
Energize-To-Shutoff (ETS)
Place the housing of the electric shutdown in a vise. Use copper jaws or shop towels in order to protect the sides of the aluminum die cast housing. Do NOT excessively tighten the vise.Loosen the jam nut (JJ) that holds the solenoid in the electric shutdown's housing. Remove the solenoid coil (II) in order to expose the shutdown plunger (MM) .Note: Loctite 222 is used on the threads of the solenoid coil during manufacturing. In addition, the jam nut is tightened to a torque of 75 N m (55.5 lb ft).
Carefully clean any dirt, metal filings or metal chips from the solenoid plunger and from the cavity in the solenoid coil. Turn the jam nut on the solenoid coil so that the nut will not interfere with the adjustment of the solenoid coil. Reinstall the solenoid coil in the electric shutdown's housing by turning the coil four times.
Hold the housing and the gasket on a